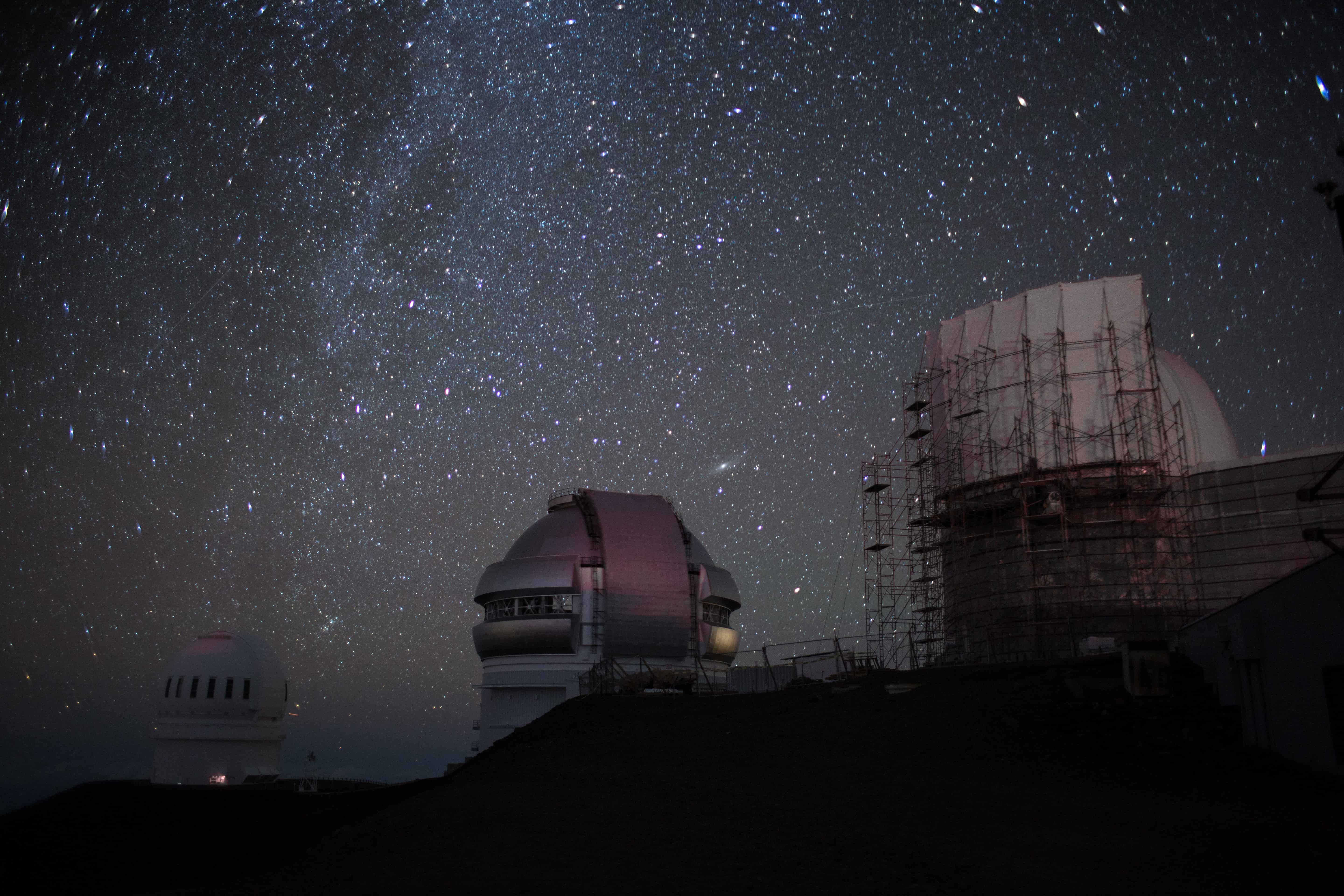
Researchers at Optica (Advancing Optics and Photonics Worldwide) have developed a new way to produce and shape large, high-quality mirrors for telescopes deployed in space. Not only are they much thinner than the ones that were previously used, they are also flexible enough to be rolled up and stored compactly inside a launch vehicle, the organisation claims in a press release.
“Launching and deploying space telescopes is a complicated and costly procedure,” said Sebastian Rabien from Max Planck Institute for Extraterrestrial Physics in Germany. “This new approach — which is very different from typical mirror production and polishing procedures — could help solve weight and packaging issues for telescope mirrors, enabling much larger, and thus more sensitive, telescopes to be placed in orbit.”
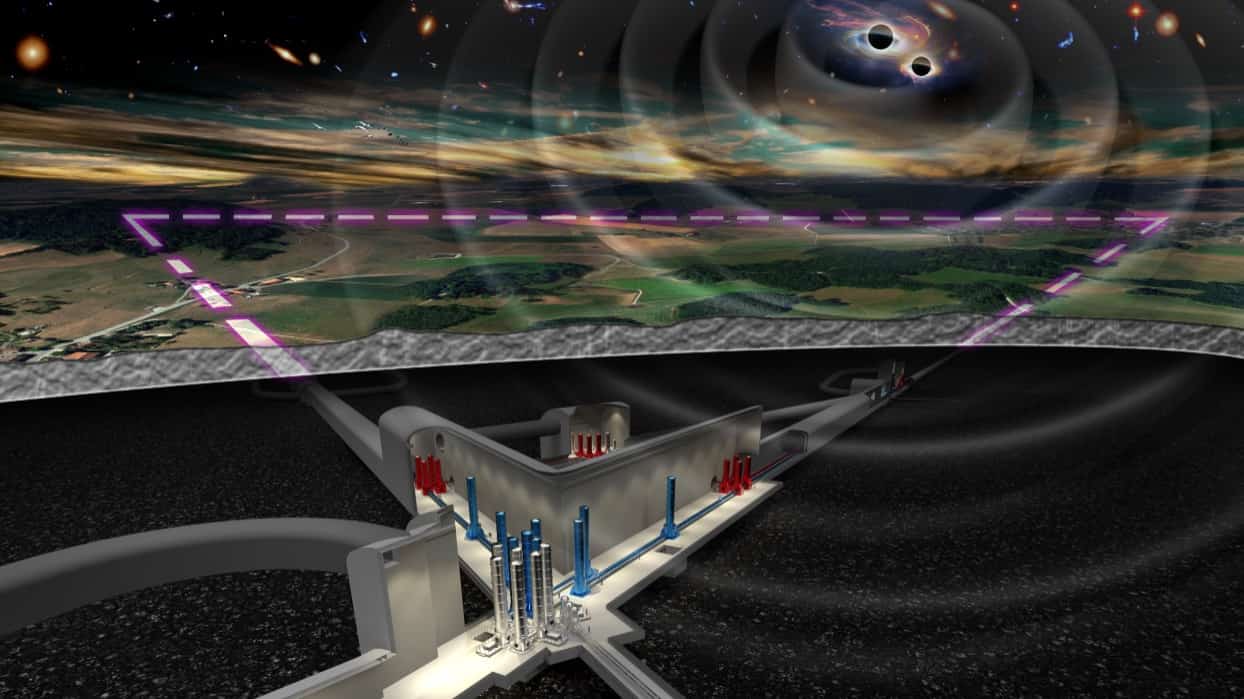
The technical side of things
Rabien reports the successful fabrication of parabolic membrane mirror prototypes up to thirty centimeters in diameter. These mirrors were created by using chemical vapor deposition to grow membrane mirrors on a rotating liquid inside a vacuum chamber. The researcher also developed a method that uses heat to adaptively correct imperfections that might occur after the mirror is unfolded.
“Although this work only demonstrated the feasibility of the methods, it lays the groundwork for larger packable mirror systems that are less expensive,” said Rabien. “It could make lightweight mirrors that are fifteen to twenty meters in diameter a reality, enabling space-based telescopes that are orders of magnitude more sensitive than ones currently deployed or being planned.”
Applying an old process in a new way
The new method was developed during the COVID-19 pandemic, which Rabien says gave him some extra time to think and try out new concepts. “In a long series of tests, we researched many liquids to find out their usability for the process, investigated how the polymer growth can be carried out homogeneously, and worked to optimize the process.”
To create the precise shape necessary for a telescope mirror, the researchers added a rotating container filled with a small amount of liquid to the inside of the vacuum chamber. The liquid forms a perfect parabolic shape onto which the polymer can grow, forming the mirror base. When the polymer is thick enough, a reflective metal layer is applied to the top via evaporation and the liquid is washed away.
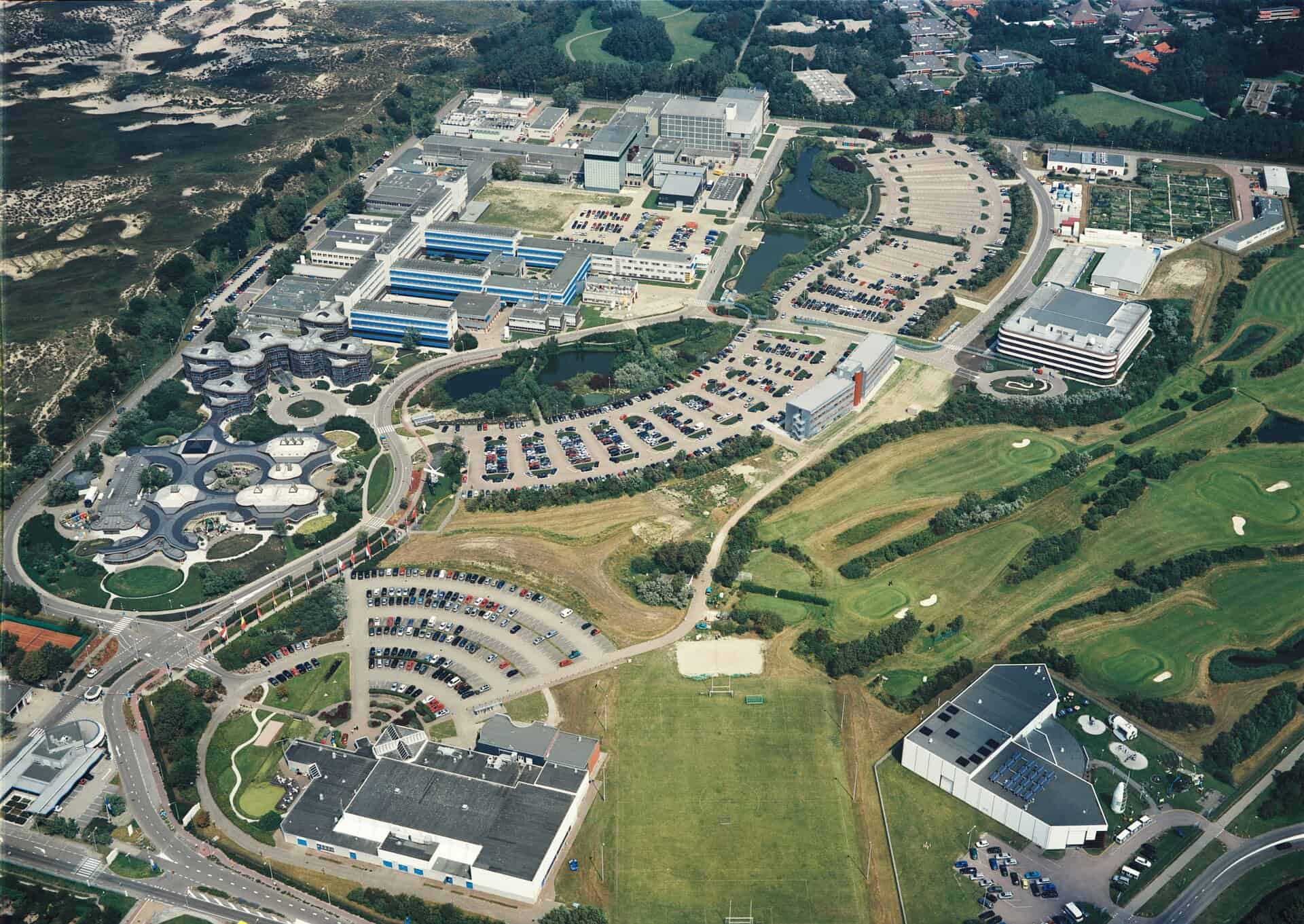
Reshaping a folded mirror
The thin and lightweight mirror created using this technique can easily be folded or rolled up during the trip to space. However, it would be nearly impossible to get it back to the perfect parabolic shape after unpacking. To reshape the membrane mirror, the researchers developed a thermal method that uses a localized temperature change created with light to enable adaptive shape control that can bring the thin membrane into the desired optical shape.
The new membrane-based mirrors could also be used in adaptive optics systems. Adaptive optics can improve the performance of optical systems by using a deformable mirror to compensate for distortion in incoming light.
Selected for you!
Innovation Origins is the European platform for innovation news. In addition to the many reports from our own editors in 15 European countries, we select the most important press releases from reliable sources. This way you can stay up to date on what is happening in the world of innovation. Are you or do you know an organization that should not be missing from our list of selected sources? Then report to our editorial team.