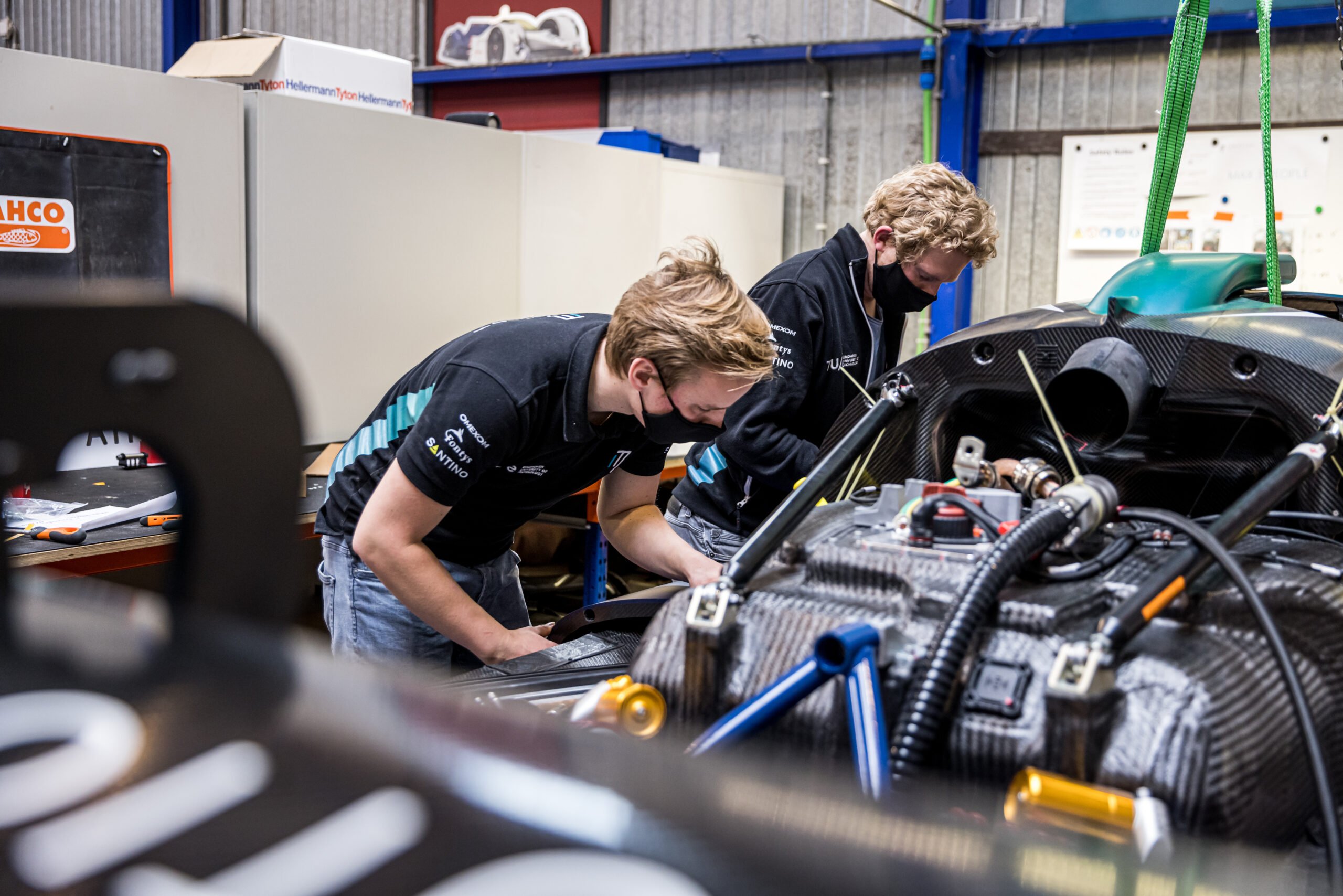
Driving around the Le Mans circuit at a speed of between 250 and 300 kilometers an hour. For twenty-four hours. But without a roaring petrol engine. Instead, with the high-pitched squeal of an electric motor. This is what the Eindhoven student team InMotion is aiming for. In 2023, they want to compete in the 24 Hour race at Le Mans with their electric Revolution.
“The high-pitched squeaking sound, is the sound of, among other things, the transmission from the motors to the wheels,” says marketing manager Luc Siecker. “That will persist and be even slightly more than in a normal electric car.”
The biggest bottleneck for a successful participation in Le Mans is the car’s charging time. The team shortened that time from 20 minutes down to 12. “Our battery pack has a capacity of 57 kilowatt hours. That’s about the same size as a Tesla Model 3, though that comparison is tricky because there are different varieties within that model. The charging time for a Tesla now is about 20 minutes on average.”
Records
The Revolution recharges 8 minutes faster. “Our ultimate goal is to be able to charge as fast as it takes to fill up a gasoline car,” says Mr. Hicks. That means charging time should go to about 2 to 4 minutes. “Then charging time will no longer be an obstacle to going electric.”
The student team has been building electric cars since 2014. Actually, initially with a team from 2012, Siecker points out. “The first car was started from a project stemming from 2009. Students then built a car that ran on bioethanol. At the time, people still thought that was the future. Eventually, that became an electric car in 2014 – because we wanted to show that an electric car can also be fast.” The fact that an electric car is also capable of being fast was already demonstrated by the team with the Fusion, a first prototype that set records at the Zandvoort (1:48:371), Zolder (1:42:641) and Assen (1:43: 059) circuits.
Unfortunately, the battery of that Formula 1-looking car ran out after three laps. Which is why the students want to get the recharging time down to as low a level as possible. In the process, several problems come to mind. For example, how do you keep the batteries cool when you charge them? That cooling and dissipation of heat makes it difficult to bring down the charging time, Siecker goes on to explain. “We hope to have reduced the charging time to 7.5 minutes by the end of 2021.”
Sealed box
The students bought a chassis in order to craft their dream car and then built it to their own taste. In a racing car, the driver sits in a monocoque that protects him. Siecker: “Normally, the engine is suspended behind the monocoque. That really gives structure to a racing car. Our car doesn’t have a big engine, but a big battery pack instead.” Together with the manufacturer of the monocoque, Ginetta, the students developed a box that forms part of the chassis. It houses the battery modules. “That box is completely sealed. We can even put it underwater if in the extreme and exceptional case something might go wrong.”
Because the weight distribution is different, the rear has to be a bit stiffer, Siecker continues. “That’s why we developed a frame behind the monocoque: the tubular frame. The rear of a normal racing car is largely the engine. In our car, this is the tubular frame on which the rear suspension is mounted.”
The blue and black Revolution is, for the student team, the future projection of what the ultimate endurance car looks like. Made specifically to race for a long time on the Le Mans circuit. An expensive car, Siecker adds. “If the car crashed because of one of your mistakes, you wouldn’t want to have it on your conscience.” Hence, only professional drivers are allowed to drive the car. “They also give us good feedback in turn, because they have experience testing racing cars.”
Once in a lifetime
Not only students from the Dutch Eindhoven University of Technology (TU/e) are working on the racing monster for Le Mans. Students from Fontys University of Applied Sciences, for instance, are also working on it. Among them is Noor Rens, a Human Resource Management student. With her non-technical background, she is more concerned about the “soft side” of the team. Most students in the team follow a technical study such as mechanical engineering, engineering physics or automotive. “We are all really different. We complement each other. I can apply everything I learn in practice. Analyzing a CV, for example, to recruit people for next year’s team.”
And for Siecker, it is a once in a lifetime experience to work with InMotion. He put his Psychology and Technology studies on hold for a year to do this. “What makes it unique is that you are putting a cool technology in an awesome car with no one else but students. I get goosebumps every time I see it assembled.”
Siecker is hoping to present the Revolution to the world at the end of this month.
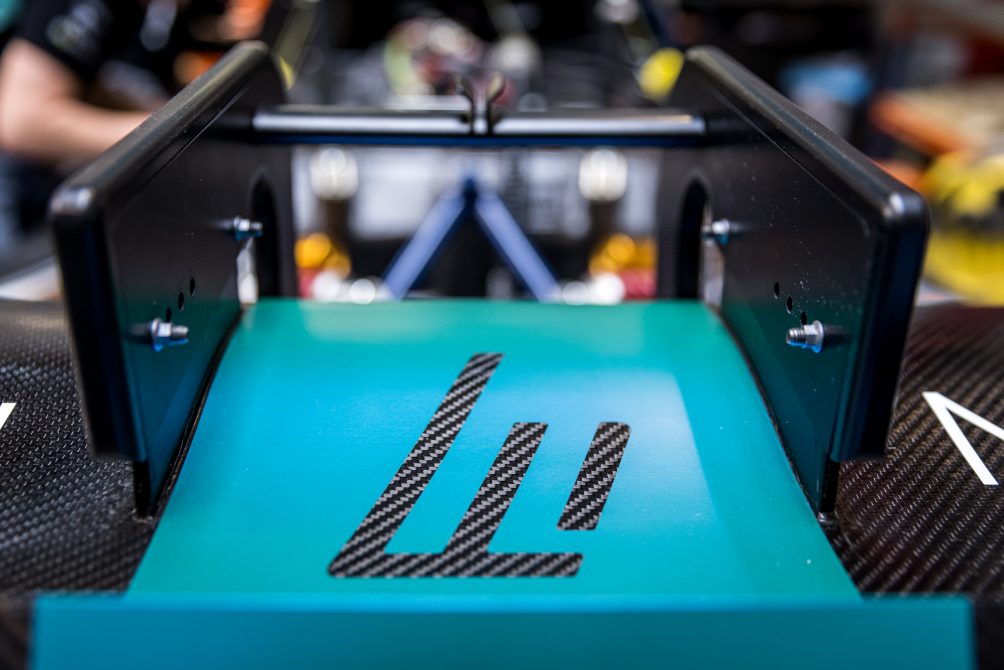