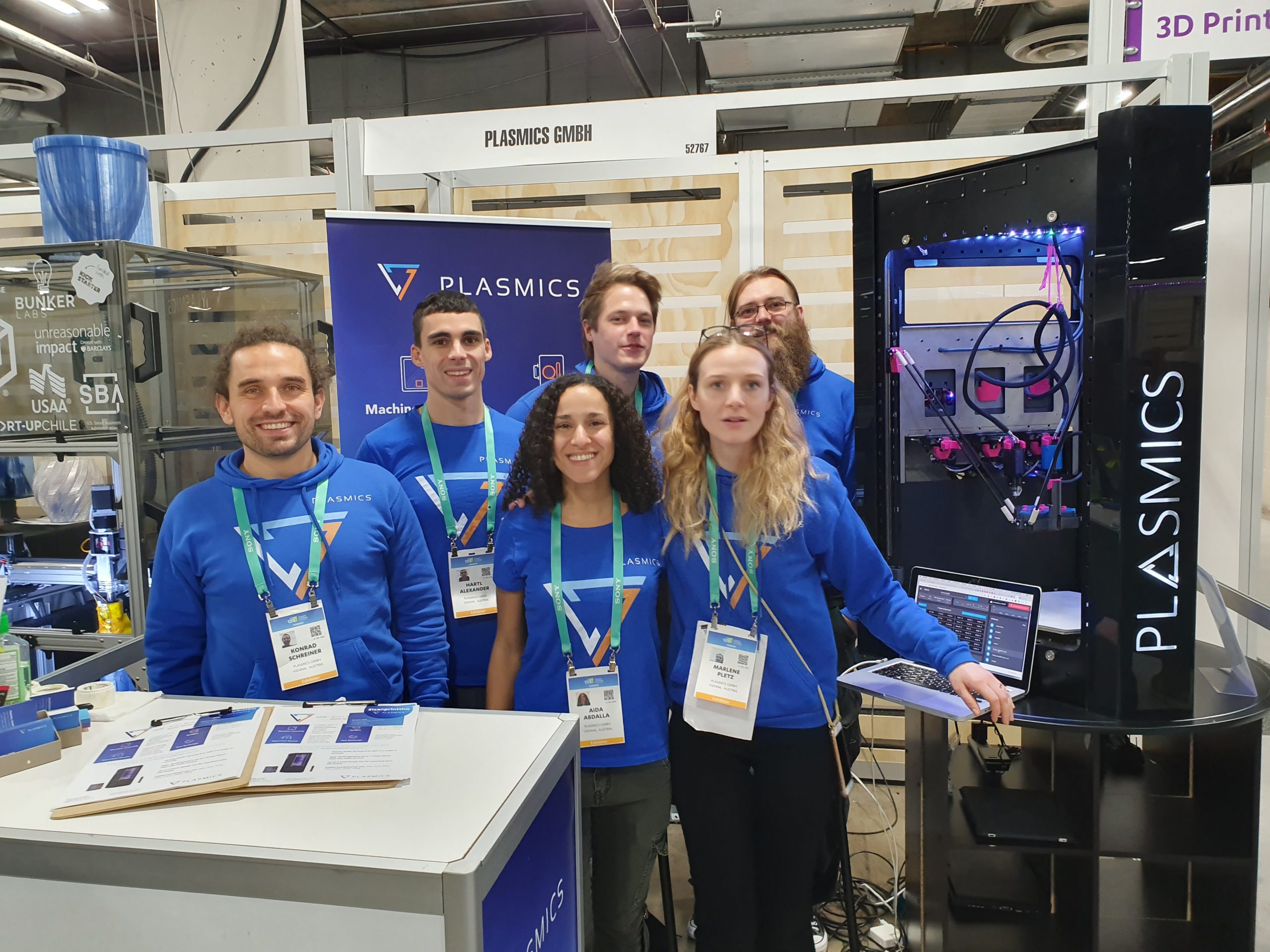
“3D printing must become very simple,” says Konrad Schreiner, the founder of Plasmics. “If it’s not user-friendly, you won’t use it.” In his 3D printing process, the entire object is printed – in one go. That means when he prints a lamp, it comes out of the printer fully wired.
Actually, Schreiner studied economics but has always had a connection to mechanical engineering. The idea for the multi-material printer came to him during his first job. He worked in a pharmaceutical production company and pharmaceutical products require special manufacturing parameters. Every product must be particle-free. That means you have to guarantee line purity from one material to the next. He adopted this principle for his 3D printing process. While other 3D printers print different materials through a single nozzle, his system has a separate nozzle for each material.
We’ve been talking for a long time about the fact that one day everyone will have a 3D printer at home – why isn’t it here yet?
3D printing is already thirty years old. At the moment there are various technologies and the hype is over. But now is the time to start pursuing commercial 3D printing processes – to bring this to the market.
Why hasn’t 3D printing caught on yet?
It’s still too expensive and the quality is still not good enough. And consumers may not yet see any need for it. They are not yet aware that they can create 3D objects themselves. Take, for example, the rubber duck made in China, which we can buy cheaply despite the effort it takes to get it here. The raw materials and the duck are manufactured in China. Then the rubber duck is packaged and transported by container ship across the sea. Here it is loaded onto trucks, taken to distribution centers and then delivered to stores. It is only so cheap because it is produced in large quantities and because it is backed up by a highly efficient delivery process.
However, sourcing from low-wage countries is at the expense of the environment. Furthermore, I doubt that you would look at the rubber duck quite the same way if you knew that it has already traveled thousands of kilometers.
Plasmics is a multi-material printer. What materials can be printed?
Plastics are the chief raw material together with alloys that already melt at low temperatures, to metals that melt at temperatures of up to 400 degrees. However, we are still in the experimental phase where metals are concerned.
And what can be printed with them?
Most objects are made of a variety of materials – and many are made of a combination of metal and plastics. In a lamp, for example, the base is made of soft rubber, the casing is made of plastic and there’s conductive metal inside. These are different types of production processes that we combine.
What was the biggest obstacle that you had to overcome?
It is not easy to find a team that works well together. I tried all kinds of things to find the right people for the right positions. If you want to succeed, you have to work together towards a common goal.
It’s also difficult to sell the idea of 3D printing. The technology is disruptive, which means you can replace a lot of manufacturing processes with it. But the existing processes work and are cheap, so it’s not easy to explain why they should be replaced. Especially given that 3D printing costs more in Europe than a rubber duck from China.
We do see a future for local manufacture. If you can manufacture everything locally, you no longer have any interest in getting things from far away. Except for craftsmanship from Taiwan, for example, which also has innate value.
What were the best moments?
That was a year ago when the first prototype worked. The first prototype that kept our promise – to investors – even though there are some challenges that still need to be mastered.
the Plasmics 3D printer (c) Plasmics
What are these challenges?
More models need to be developed that end users can print out at home. Users have little interest in designing their own models. There’s knowledge behind it that you won’t get to grips within an afternoon. So, our key to the market is first of all those people who have the expertise. For example, orthopedic surgeons, who can construct 3D models for insoles and thus turn into product designers. We offer them a sales platform for their models and the manufacturing technology. Customers should be able to simply download them, similar to an app store.
What can we expect from you in a year?
We are planning to launch no later than September 2020 at the Formnext trade fair in Frankfurt. Provided that the fair still takes place despite the COVID-19 crisis. There we will show only a part of the 3D printing process. This is the development that is most important for the multi-material printer – and which is still aimed at experts initially.
Where do you want to be with Plasmics five years from now?
The team is certainly the main challenge. Everyone is motivated and has ideas. But that means there is a danger of losing focus. That’s why we have started to stagger our timeline of products so that the pipeline for products is still guaranteed. This will apply for the next two years at least. In five years’ time, we aim to have a 3D printer for home use.
What makes your 3D printing process better than existing technology?
We are convinced that we have the better approach. When we started, there wasn’t a 3D printer with an exchange mechanism. This allows you to print different materials with one printer. Other 3D printing processes process all materials through the same nozzle. We have the right nozzle for every material. Each material develops differently under the influence of heat and during the cooling process. Materials expand and contract. A one-size-fits-all solution can’t compete.
Thank you for the interview.
Are you interested in start-ups? Read all articles from our series here!