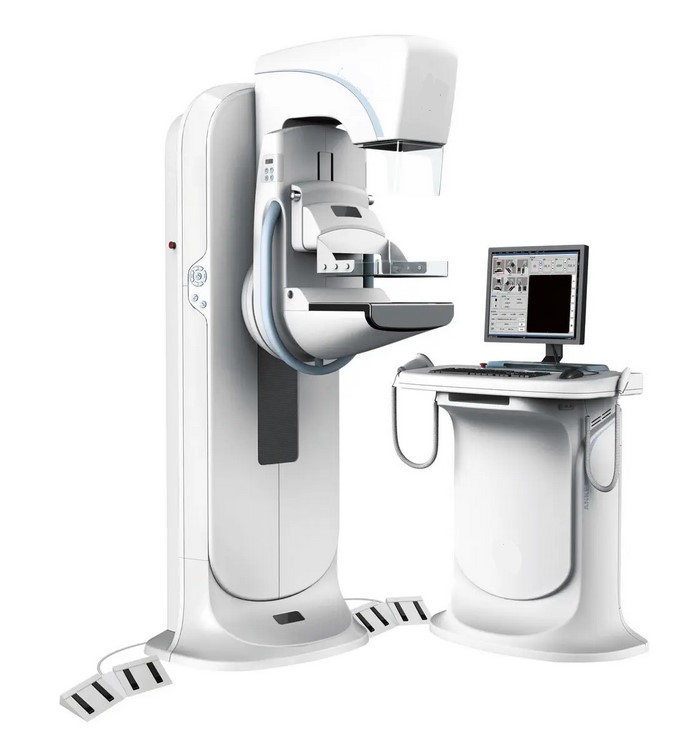
Less radiation yet sharper X-ray images. This can be achieved with a special, large CMOS sensor. Equipment with these sensors is becoming increasingly common in the treatment rooms of dentists and hospitals. We are all used to dental x-rays whereby a plate is placed in your mouth and the dentist leaves the room at the moment the picture is taken to avoid exposure to too much radiation.
Innovatieve techniek
“This is no longer necessary thanks to an innovative technique. X-rays can be taken with better resolutions and faster speeds, while considerably less radiation is needed,” says Jeroen Lotgering, director of the NXP factory in the Dutch city of Nijmegen where chips are manufactured. “The use of these chips means that the radiation required is so low that video images can be taken continuously during surgery.” Demand for this specific X-ray equipment is currently booming. The equipment is used, among others, by dentists and physicians, and also for e.g. mammograms.
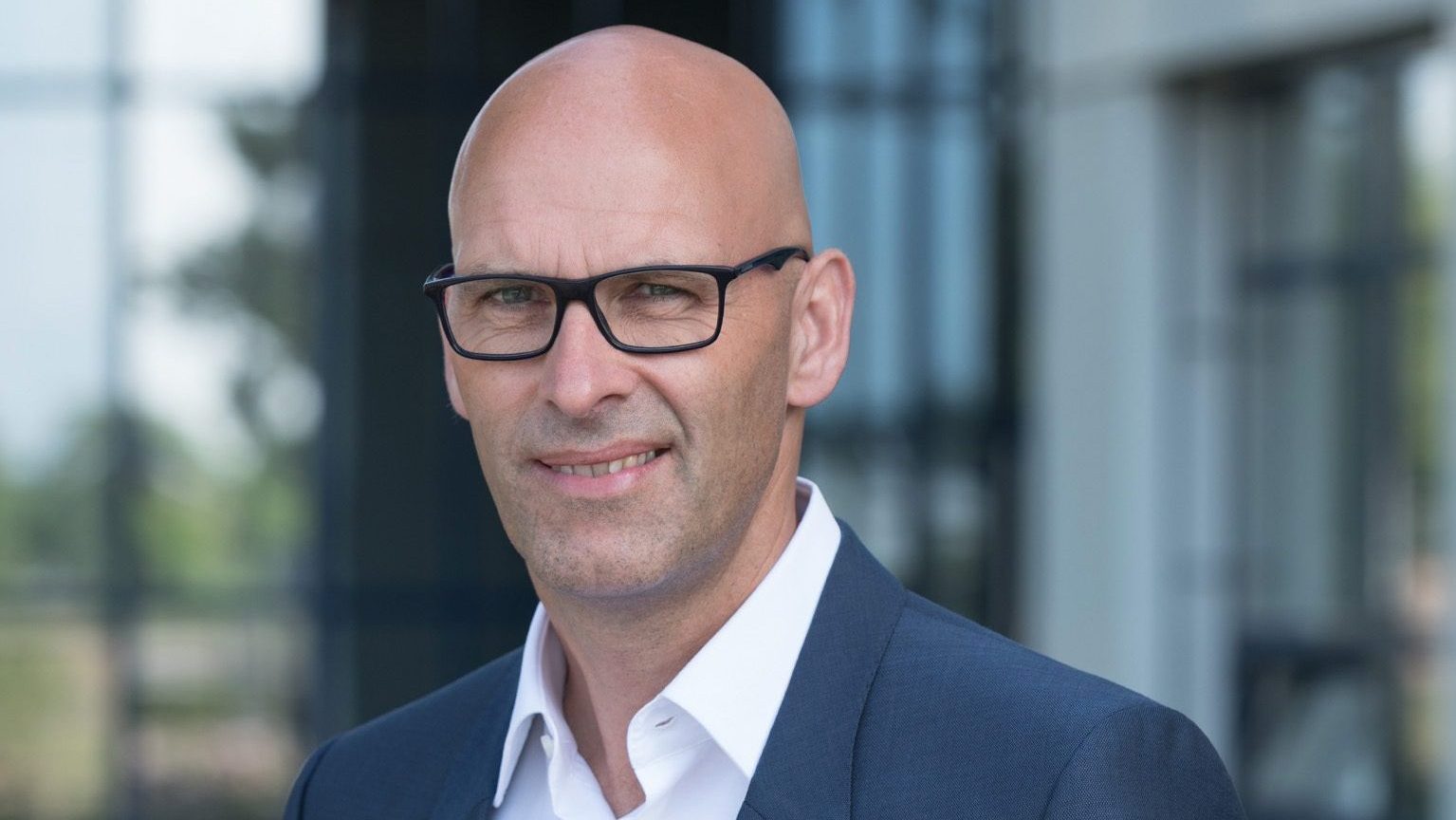
Medical world
Chips for these devices are being made at NXP. The basis for the technology is a CMOS (Complementary Metal Oxide Semiconductor) sensor. CMOS has been around for over 20 years and is used in cameras in mobile phones, among other things. However, the use of the technique in the medical world has taken much longer to develop. For X-ray imaging applications, it has the added advantage that the image sensor and the circuits that process the signal can be integrated into the same chip. Many other techniques require a separate chip for signal processing. Six chips, and accordingly, six wafers, are needed for the largest detectors.
Fragile
Typically, hundreds to as many as 80,000 chips can be made from an eight-inch wafer. However, for this X-ray machine, only one chip is taken from a wafer. “For some products, the trend is that everything is becoming smaller and smaller, but that doesn’t apply to all chips,” Lotgering says. “In this case, we need a large surface area. You can imagine that this is a very fragile product, and it is even more important that no dust or other contaminants end up on the wafer. Because then you would have to throw away a whole slab.”
15 billion chips
In NXP’s Nijmegen ICN8 factory, approximately 15 billion chips are manufactured each year. That makes it NXP’s largest factory in the world. The semiconductor manufacturer is focused on the automotive industry. The chips are used for safety systems (such as airbags and sensors), infotainment and communication between cars. In addition, NXP also caters to other sectors, with chips for medical equipment.
Influence of war
For several years now, Jeroen Lotgering had been director of the Nijmegen factory, and has been responsible for NXP’s six factories across the world since the beginning of 2022. Due to the major chip shortages, the semiconductor manufacturer is committed to delivering to its customers as much and as reliably as it possibly can. For now, the war in Ukraine has had no effect on semiconductor manufacture. “We are not dependent on Ukraine or Russia for the supply of raw materials. At the same time, it is also not yet entirely clear how everything interacts. For example, certain automobile manufacturers which buy chips from NXP are unable to continue production right now because they have to wait for other raw materials and parts.”
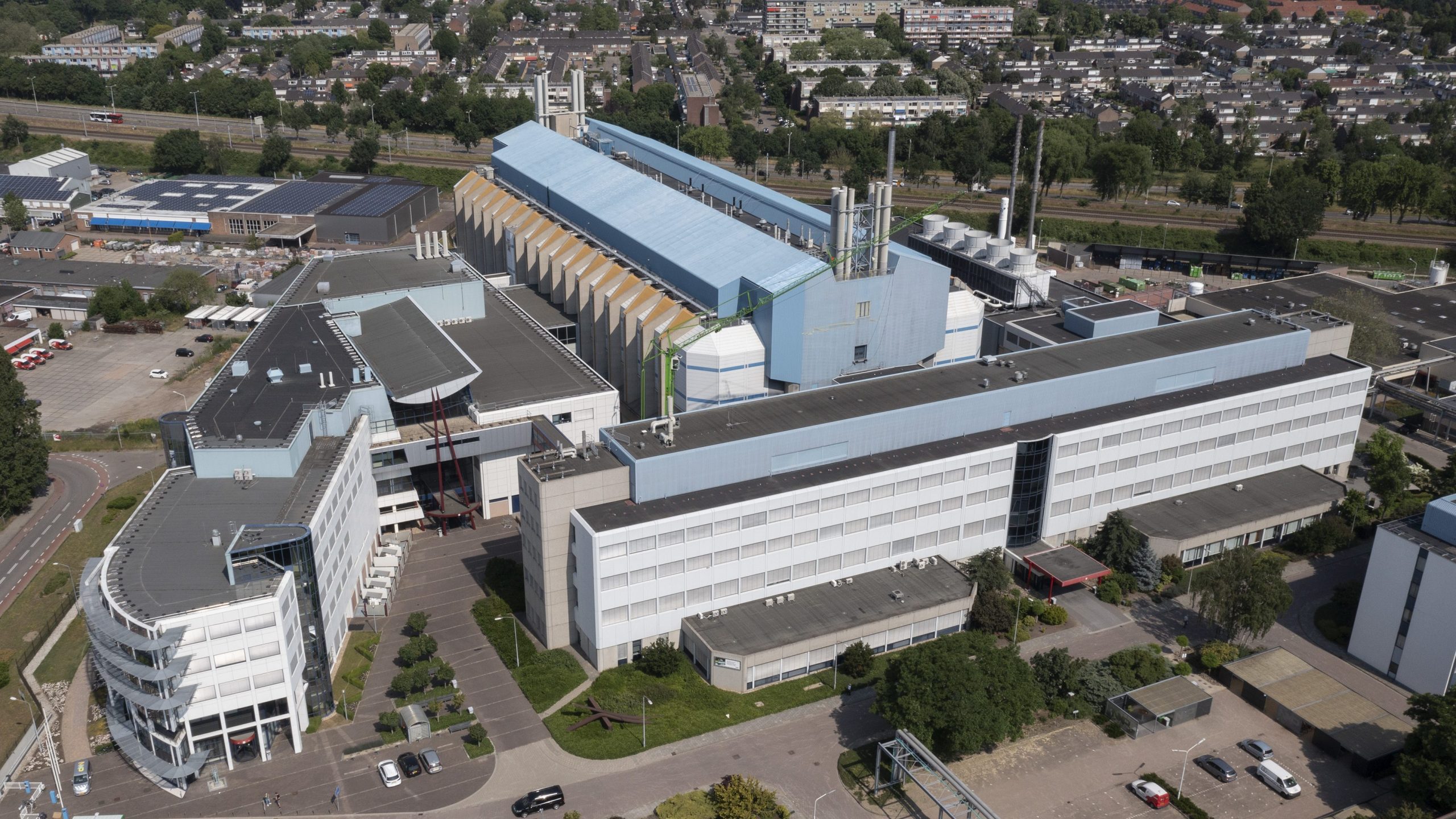
Supplies
NXP wants to continue to expand production. For one thing, the factory in Nijmegen was recently rebuilt at a cost of millions so that more chips could be manufactured. Lotgering: ” And then these will have to be shipped all over the world. You’re dependent on transport and as is the case everywhere else, the question remains as to how this will unfold over the coming period. Supply and transport remain key points of concern.”
Also interesting: NXP is working on new innovations in record year