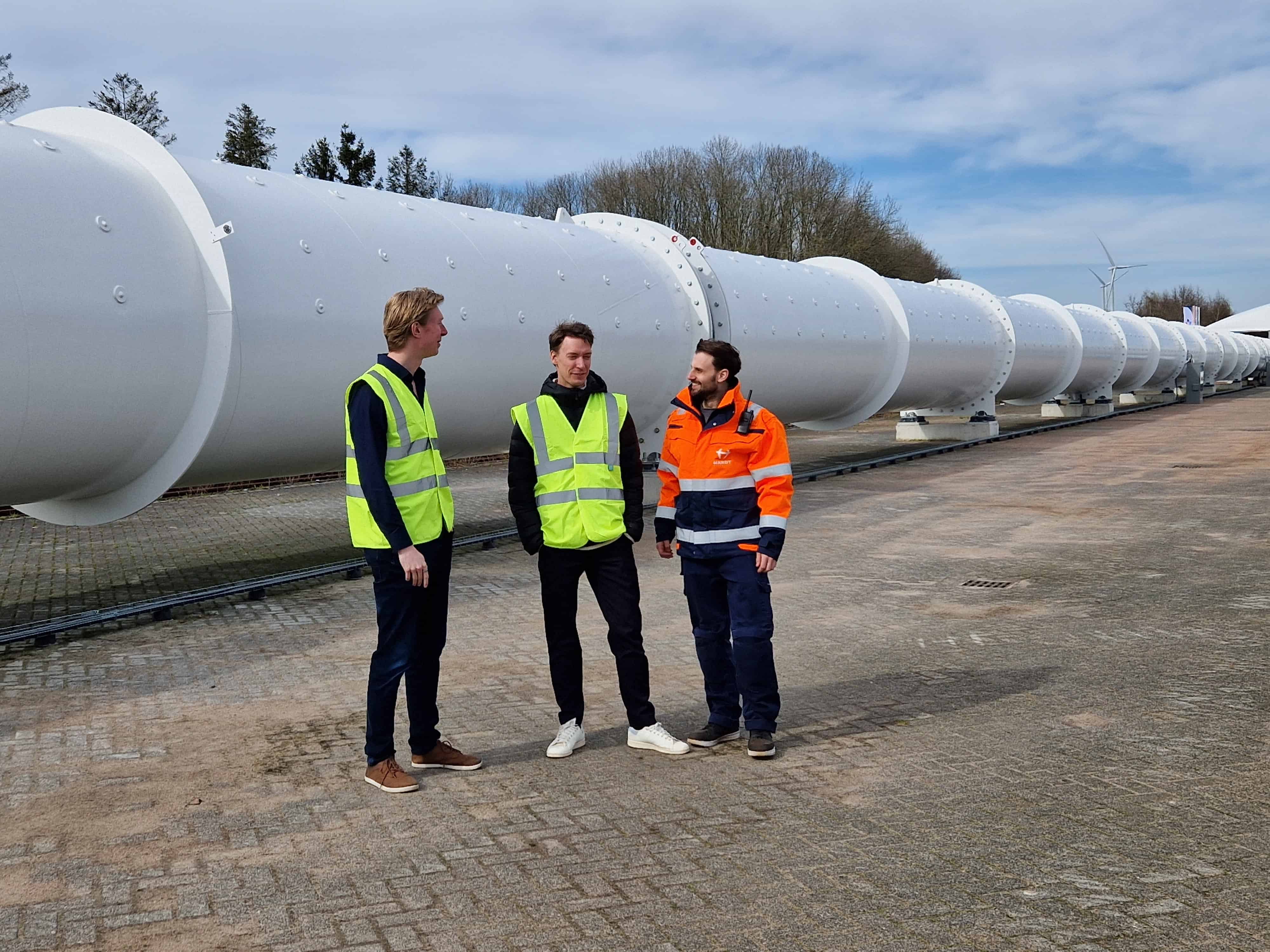
To a passenger arriving by train to Veendam—a town in the province of Groningen, the Netherlands—spotting a few hundred meters long white pipe that stretches parallel to the railway might not mean much. The outskirts of the town feature windmills and processing plants, so this might just be another processing pipe. Well, the pipe might actually be the way to get to Veendam in twenty years.
Why this is important:
With the opening of the European Hyperloop Center, the Netherlands puts itself at the forefront of the research on hyperloop, a future mode of transportation.
The pipe is part of the European Hyperloop Center (EHC), a newly built hyperloop test facility. It is a hotspot for testing and validating hyperloop-related technologies, comprising a test track, a workshop area, and a knowledge center. Construction started in September last year, with the symbolic placement of the first bit of pipe. Now that the tube construction is complete, tests can start. “The facility is open to any company to test and validate their innovations,” underlines Sascha Lamme, director of the EHC and co-founder of Hardt Hyperloop.
The Dutch Hardt Hyperloop is one of the European companies at the forefront of hyperloop developments. The company, headquartered in Rotterdam, worked on creating the new testing facility. In fact, the EHC is a public-private initiative by Hardt Hyperloop, the Province of Groningen, the City of Groningen, and the Municipality of Veendam. Hardt is part of the Hyperloop Development Program, which comprises European companies and institutions and was funded by the Dutch Government and the European Commission.
How does the Hyperloop work?
Simply put, the hyperloop mobility system consists of a train in a vacuum tube that can travel at up to 1000 km/h speeds. Traveling from Amsterdam to Budapest would take four hours and twenty minutes— as compared to the over 19 hours needed by train today. Instead of wagons, there are pressurized pods, which levitate on tracks using special magnets. By removing air, the vehicles don’t have to push it away to counteract the drag force, and by eliminating friction, pods can move more freely, reaching faster speeds. If there is no force to thwart drag, less energy is needed to make the pods move. The Hyperloop is fully electric, thus with no tailpipe emissions.
The longest test pipe in Europe
Located on HUSA Logistics’ terrain, the white pipe stretches 420 meters along the railway track, where today’s trains start to slow down before arriving at the nearby station. As we approach the facility, Marinus van der Meijs, co-founder and technology and engineering director of Hardt Hyperloop, opens the white tube. Shortly after, the LED lights are turned on, illuminating the cavity as far as the eye can see.
In a way, the tube structure is simple. The pipe, made of steel, is a couple of meters wide. Differently from a train, the levitation tracks are on the pipe’s top sides. Right next to them stretches a bar code. This identifies where the pod is, with the infrastructure and pods that always communicate with the control room.
The EHC pipe is the longest hyperloop testing facility in Europe. With this track length, Hardt expects to run its pod to a top speed of up to 100 km/h, much slower than the hyperloop promises and current trains offer. “In China, there is a couple of kilometers long test pipe, where pods got a 700 km/h top speed,” clarifies Tim Houter, co-founder of Hardt Hyperloop.
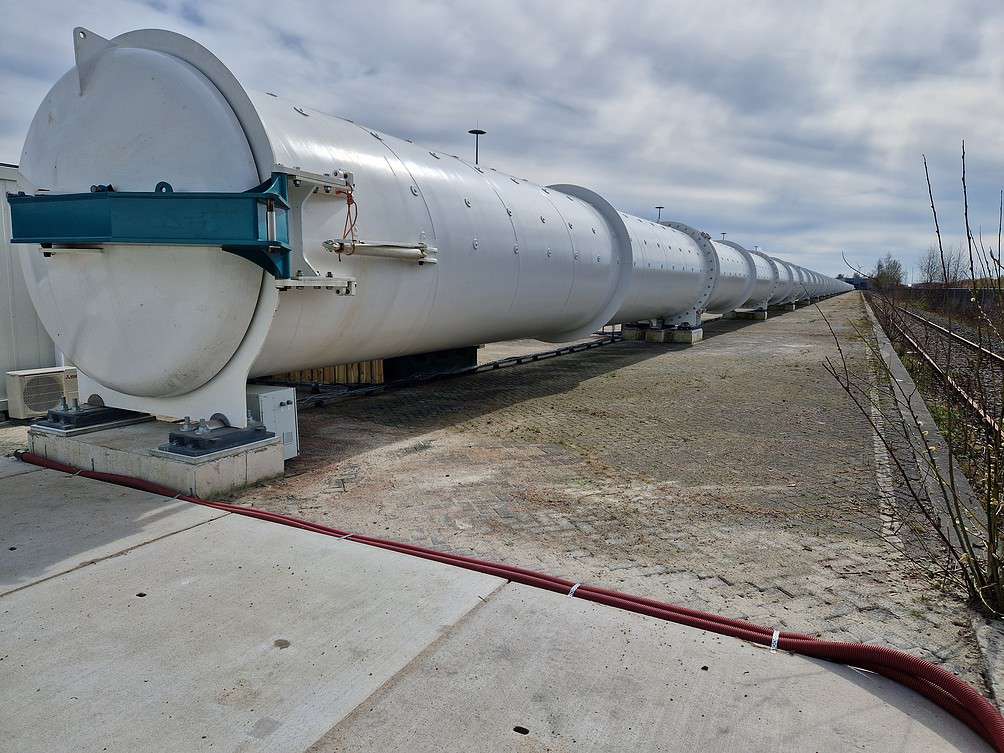
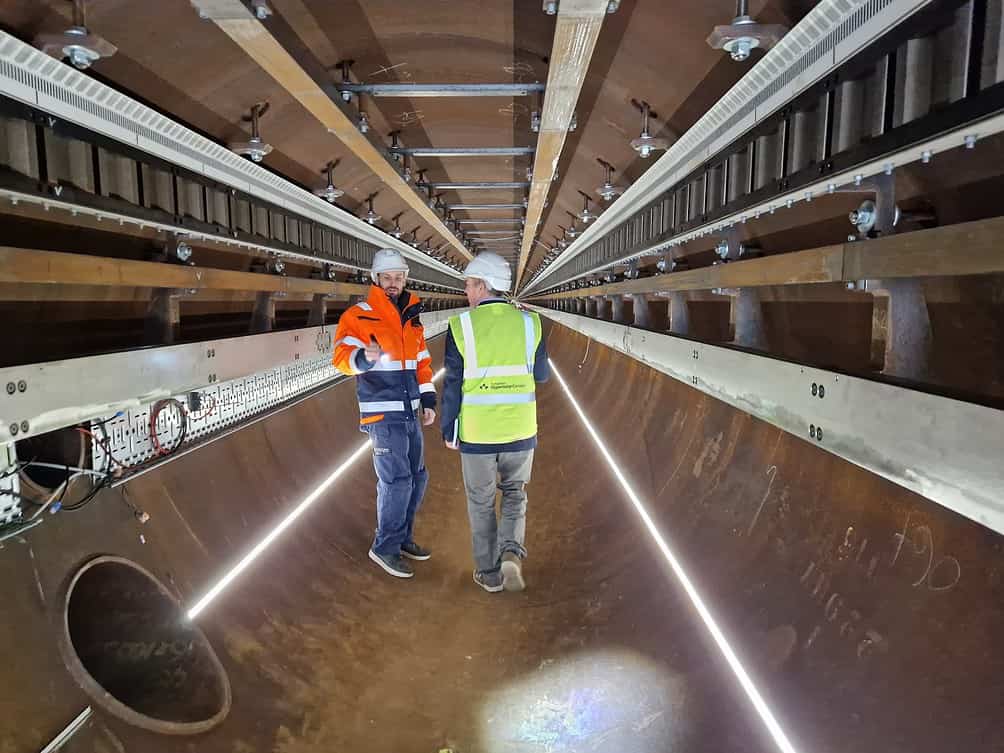
Lane switch
Walking inside the echoey tube, tracks start to split, and the tunnel divides into two parts. This is a full lane switch, an essential element that will help companies validate the technology. Simply put, the tube bifurcates, allowing pods to go to the left or to the right. Despite the high speeds hyperloop pods plan to reach, switching is designed to be as smooth as possible. “The lane switch is designed to happen gradually, even at such elevated speeds. Differently from rail tracks, there are no moving components,” explains Van der Meijs while walking inside the pipe.
Hyperloop pods will travel in convoys. Unlike train wagons, they will be detached from each other, meaning that every pod can take a different route. Van der Meijs compares it to a highway junction, with vehicles that can take whatever exit they need to. When switching, pods run for a short stretch on one side only, concentrating levitation on the side where the vehicle is turning.
Complementary to the pipe is the vacuum system. In a small container next to the tube is a vacuum pump, which literally draws the air out of the pipe to keep the vacuum. The pipe design allows the tube to remain sealed so that once air is removed, no other gets in. Lamme explains that an established hyperloop system would need one such pump every couple of kilometers— although much depends on the pump’s power and on the air condition. In case of an emergency, the pump can bring air into the system in a few seconds.
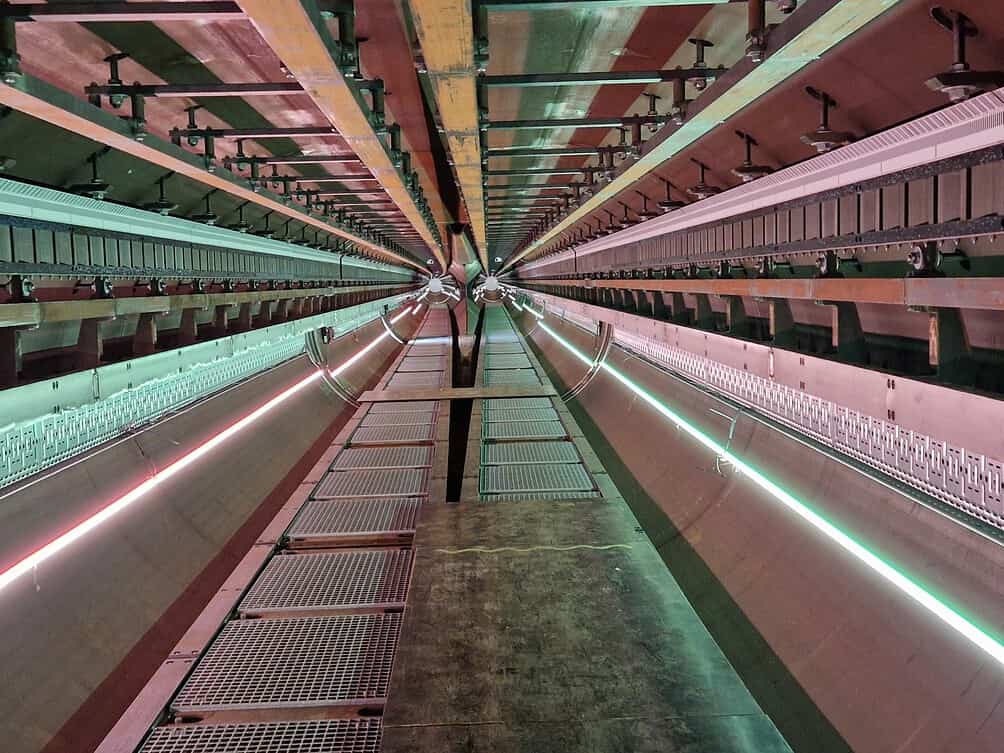
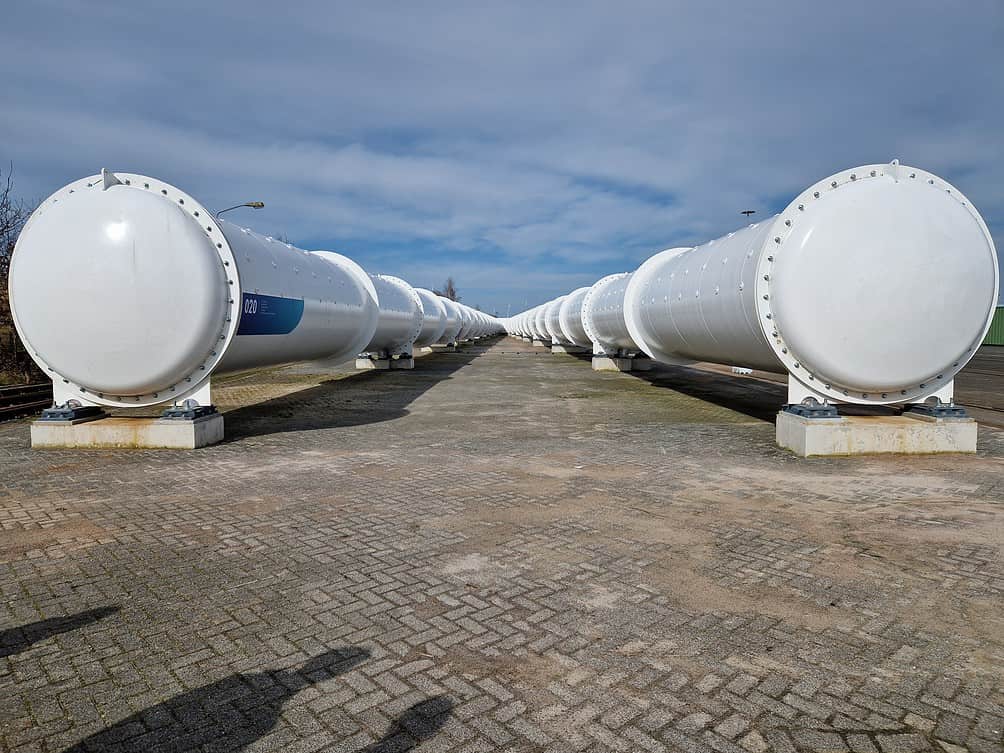
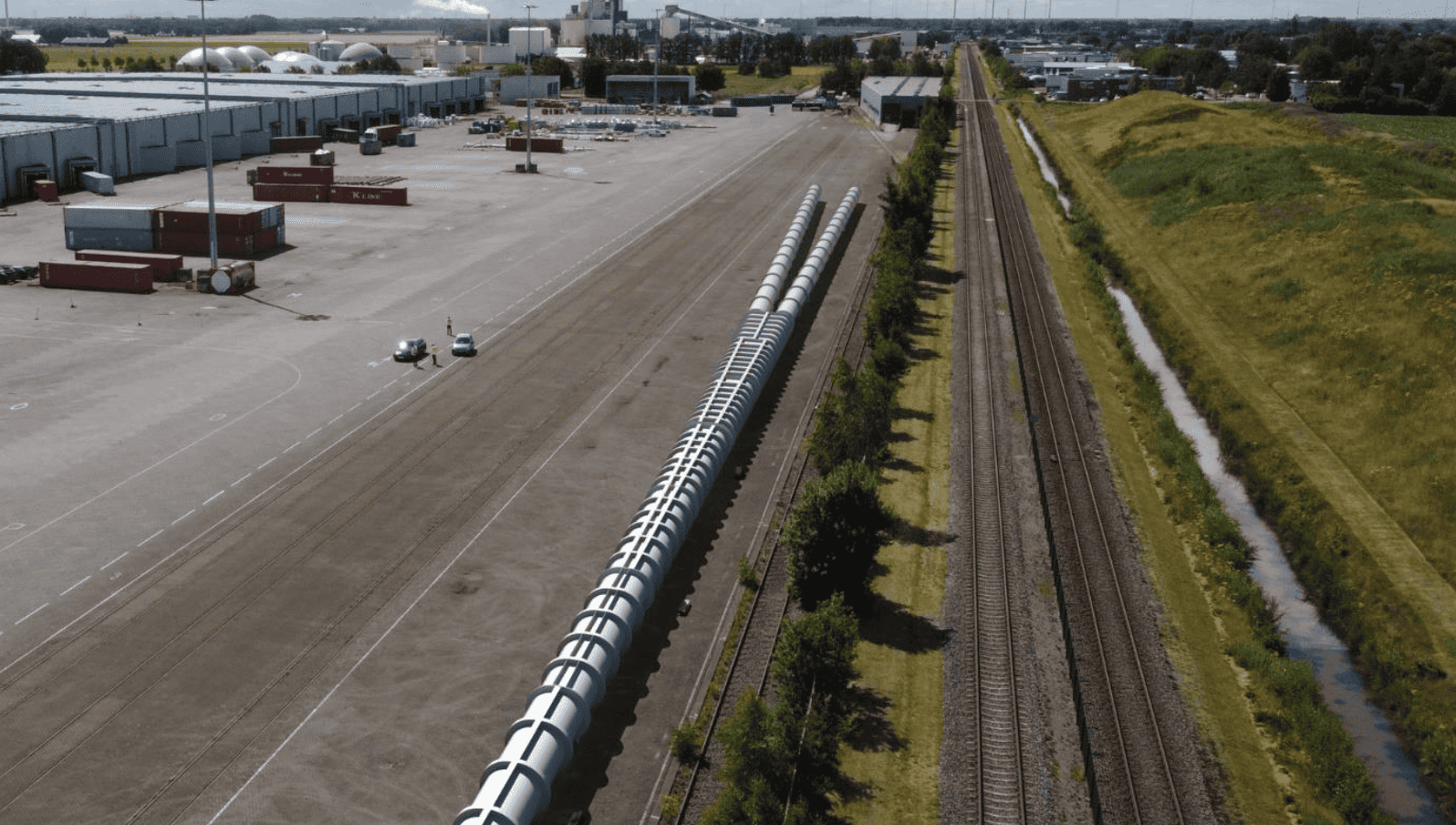
The road ahead
Hyperloop is not the only potential technology to disrupt rail transport. Magnetic levitation, which is used in some rail tracks in Asia, is another example. In Europe, Nevomo is also working on adapting maglev to existing railway tracks. “Adapting magnetic levitation on already existing tracks undoubtedly increases trains’ speed. However, all the advantages of running in a vacuum are missed. Trains wouldn’t get to hyperloop speeds anyway, and there is still the problem of magnetic drag to be managed,” says Lamme.
Costs are yet another concern for the development of the hyperloop. According to Hardt, hyperloop costs are lower than high-speed rail (HSR). A 2018 report by the European Court of Auditors found that, on average, a kilometer of HSR costs €25 million.
As the first tests kicked off, Hardt aims to have its first route by 2030. In addition to the tests on the track, the company will work on passenger experience with the University of Groningen. Reducing the discomfort caused by the high speeds is one of the critical points to address. Plenty of work to do, and the EHC will surely be instrumental. As we leave the testing terrain, the light blue Arriva trains keep passing on the nearby tracks as if scrutinizing that pipe that hopes to replace them in the future.
In the main picture from left to right: Tim Houter, Sasha Lamme, and Marinus van der Meijs