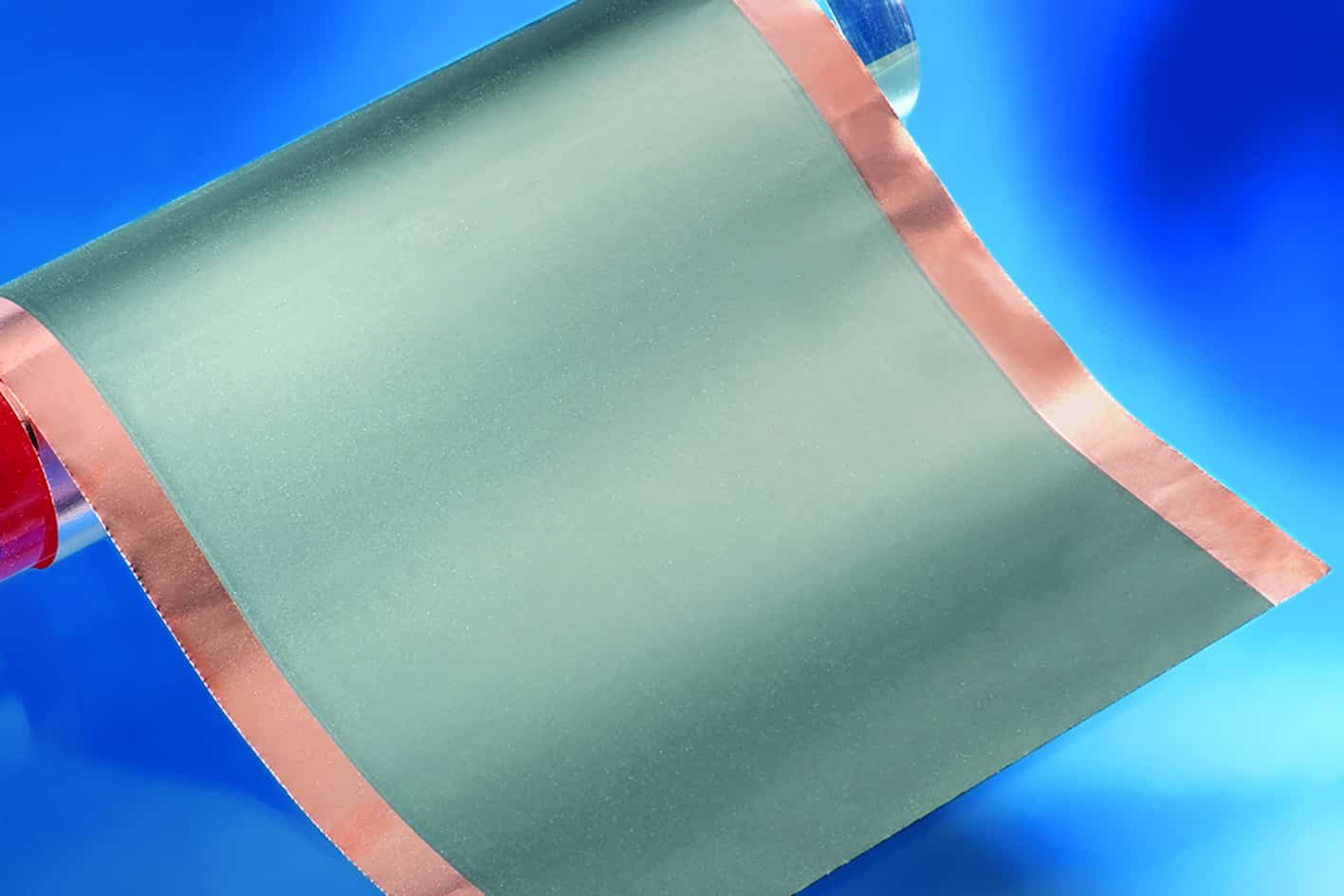
Researchers at the Fraunhofer Institute for Laser Technology (ILT) in Aachen have developed two groundbreaking laser-based manufacturing processes that boost energy efficiency in lithium-ion battery production, says Fraunhofer in a press release. This is of importance, as battery technologies are the key to the energy transition.
The new diode laser drying system reduces energy consumption by 50 percent and the space required for industrial-scale systems by 60 percent, compared to conventional methods. The second innovation is a high-power ultrashort pulse (USP) laser, which creates channels in the battery electrode, increasing power density and service lifetime. These channels serve as Li-ion highways, shortening the charging process and preventing defects, ultimately extending the battery’s lifespan. The next step is scaling up the technology from prototype to industrial production lines.
Diode laser drying: Energy-efficient and space-saving
In traditional lithium-ion battery production, copper foils coated with graphite paste are dried in gas-powered continuous furnaces at 160 to 180 degrees Celsius. These furnaces consume a large amount of energy and occupy significant space, typically measuring between 60 and 100 meters in length for industrial-scale operations.
The Fraunhofer ILT researchers have developed a diode laser system that carries out the drying process more efficiently. This laser, with a wavelength of 1 micrometer, is combined with a specially designed optical system that illuminates the electrode over a large area. As a result, the graphite particles heat up, and the liquid evaporates, reducing the energy required for drying by up to 50 percent and the space needed for an industrial-scale drying system by at least 60 percent.
Ultrashort pulse laser: Enhancing power density and service lifetime
Alongside the diode laser drying system, the Fraunhofer ILT team has improved the power density and service lifetime of lithium-ion batteries using a high-power ultrashort pulse (USP) laser with 1 millijoule of pulse energy. This laser introduces channels into the battery electrode, serving as Li-ion highways that significantly reduce the distance the ions must travel and shorten the charging process. This also prevents defects, increasing the number of potential charging cycles and ultimately extending the battery’s lifespan.
The researchers have successfully transferred the principles of this laser-based process from the laboratory to a scalable, industry-ready process that uses ultrashort pulse laser radiation in the femtosecond range to modify the electrodes. This short interaction time allows for material ablation without melting, preventing power loss in the battery.
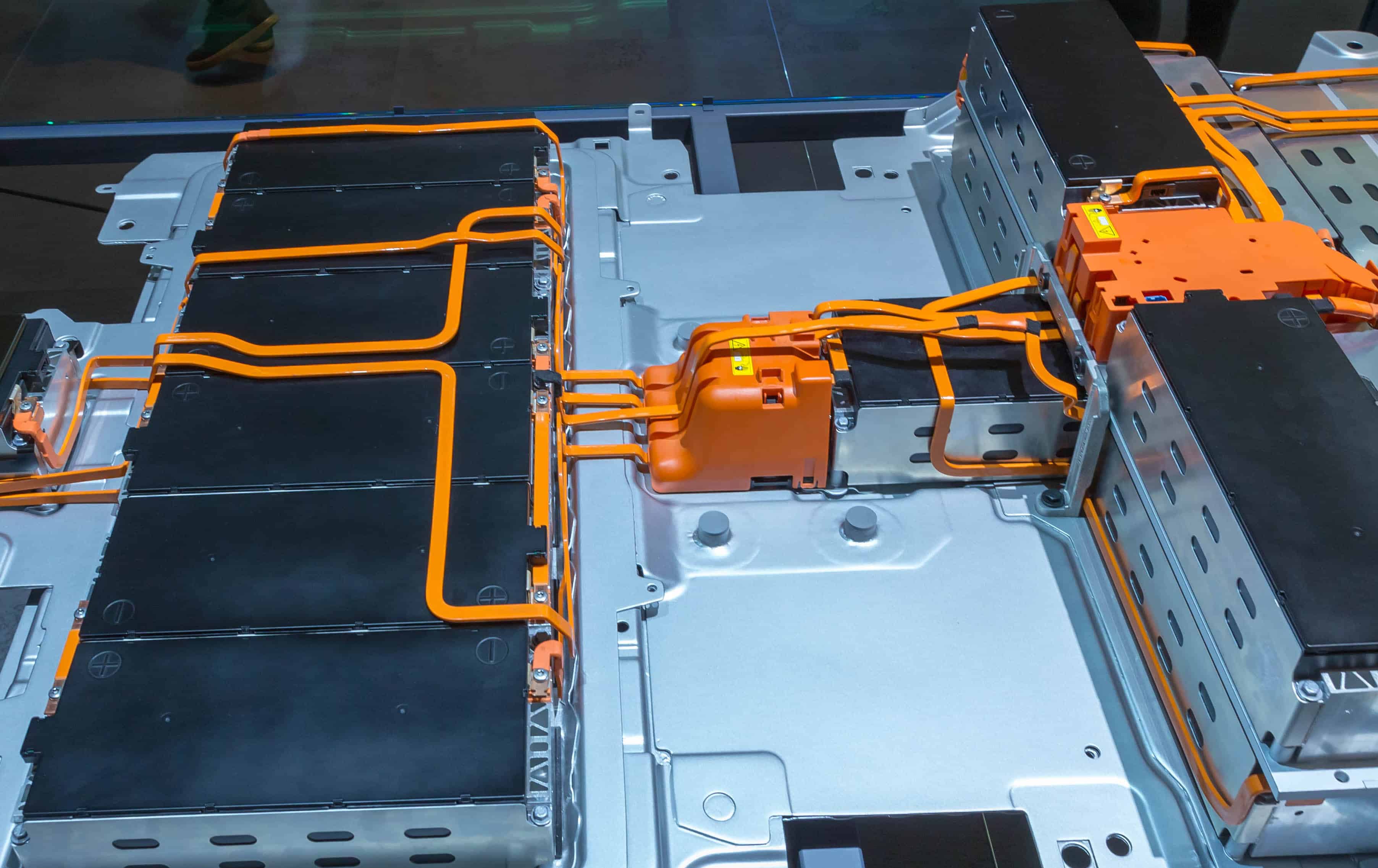
Scaling up for industrial production
One challenge the Fraunhofer team faced was adapting this process for larger areas to achieve the high throughput required for industrial production. They solved this problem by using a multi-beam arrangement for parallel process control. Four scanners, each with six beamlets, process the tape in parallel, covering a width of 250 millimeters and continuously processing the graphite layer. This multi-beam optics technology was developed and implemented in close collaboration with Pulsar Photonics GmbH, a Fraunhofer ILT spin-off founded in 2013.
The research conducted at Fraunhofer ILT shows that laser technology can be used as a digital production process to improve battery cell quality and increase sustainability during manufacturing. The next step is scaling up the technology from prototype to industrial production lines.