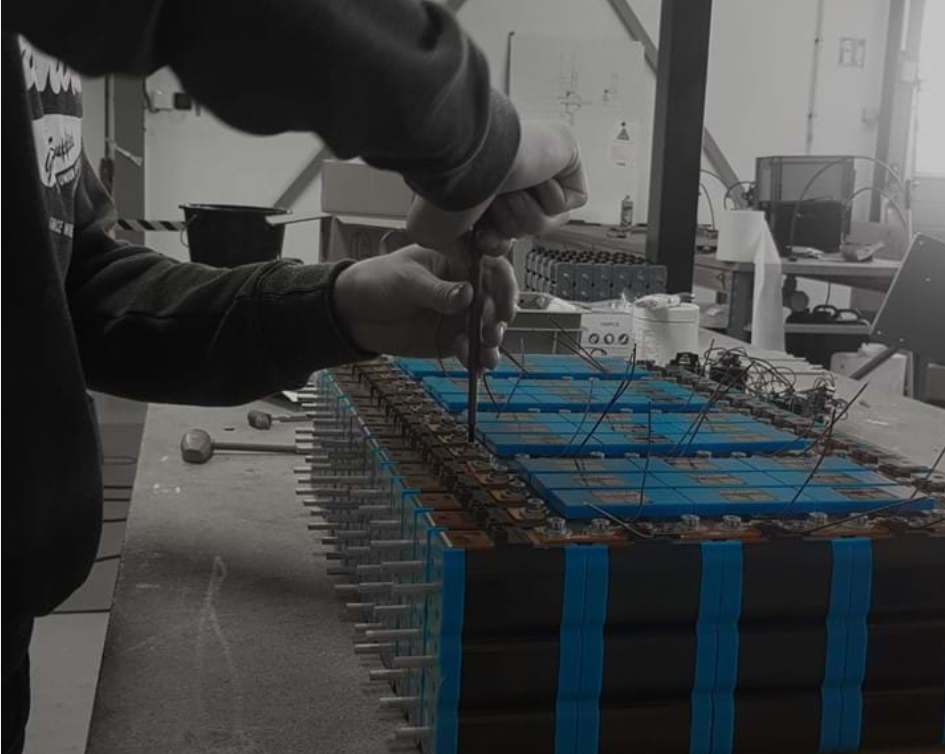
How can you draw as much power as possible out of an electric motor within twenty minutes, without setting the racing car on fire? Peter Hinten, amateur racer and co-founder of Power Battery, came into contact with electric racing through the STORM project at the Eindhoven University of Technology (TU/e). He noticed that improvements in the mechanics were needed to enable the motor to cope with a heavy battery pack.
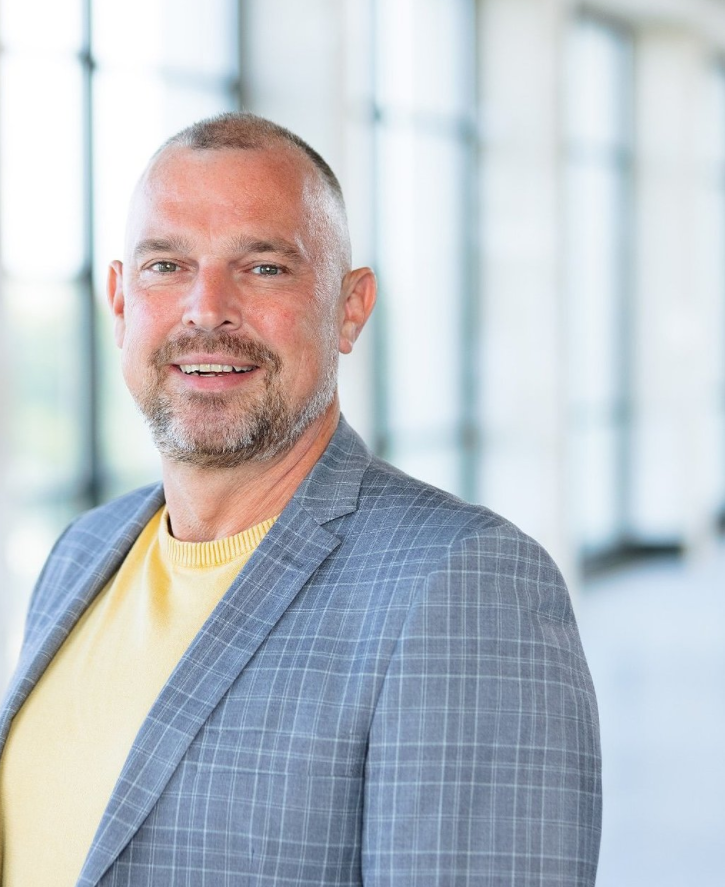
This is how Power Battery was born: a start-up from the Dutch town of Nuenen that develops battery packs for vehicles that rely on high levels of power and where space and weight are limiting factors.
โIn addition to racing cars, we also make battery packs for airplanes, speedboats and even upgraded retrofits of classic Porsches and Mercedes carsโ Jan-Hein van Twist tells us. Together with Hinten, he founded Power Battery back in 2018. The assignment was clear: Develop a small, powerful battery pack that can be used up within twenty minutes (longer than that is not necessary on a race track) without causing a fire hazard. Van Twist: โSo that is how we came up with liquid coolant for Li-Ion cells, a unique cooling system that keeps the battery packs safe, which is capable of delivering huge amounts of power and lasts longer.โ
Overheated batteries
Lithium-ion cells are the most common cells for battery packs in mobile applications because they have the best load capacity to power ratio. โIf youโre making a touring motorcycle, range is an important factor. You do not want to charge your motorcycle every twenty minutes. That requirement is dropped on the racing circuit, where range doesnโt matter, as long as riders can go full throttle for twenty minutes. During that time, as much power as possible must be available.โ
Sounds like a simple task, but the moment a battery is heavily charged, it overheats. Van Twist explains that this can cause a fire, and it also degrades the life of the battery. โThe chemical composition of the battery changes when it overheats, and the capacity decreases because of that.โ
Innovative cooling system
At Power Battery they found a solution for both the fire hazard and the reduced battery life. An aluminum pipe containing coolant runs through the battery modules which are made up of eight to twelve cells. โThat can be water, but in more extreme situations, it can also be a stronger coolant, such as glycol.โ To illustrate, a racing car requires 198 modules consisting of twelve cells to be able to race for twenty minutes.
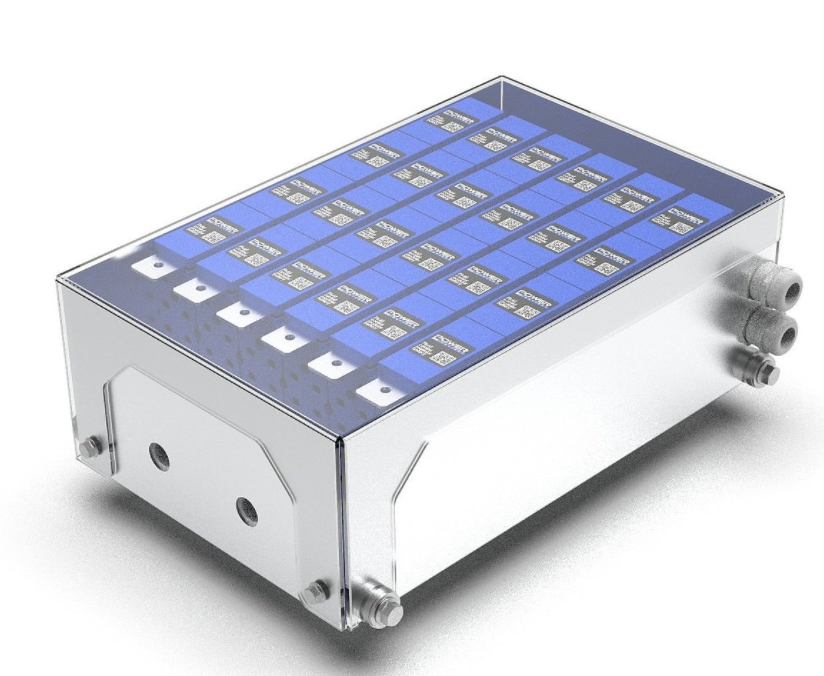
The cooling system controls the temperature of the cells. โEven when the battery is completely drained in twenty minutes, the outside of the cell does not get hotter than 55 degrees Celsius. Normally the temperature would rise to 90 degrees Celsius or higher.โ Power Battery guarantees a solid performance for a longer period of time and the battery life is also preserved. For the modules, Power Battery purchases A-grade battery cells that can handle at least 500 cycles โ that is, 250 times from 0 percent to 100 percent.
Once the race is over, the battery packs can be connected immediately to the charger. Van Twist: โThere are companies that make similar packs, but with those, you have to wait at least an hour before you can recharge the batteries. Power Battery is the only company on the market that can cool a high-grade, high-performance Li-Ion battery pack so efficiently.โ
Areas of application
Power Battery is focusing on high-end partners in the racing and leisure industry. โWe partnered up with ERA Championship. The first all-electric junior formula class in the world. Our battery pack is the
main power unit for the powertrain of the racing cars. Besides that, we also convert retrofit, classic Porsches and Mercedes cars and recreational boats.โ
Apart from the high-end industry, Power Battery also focuses on heavy duty equipment, such as cranes and port equipment. โโWe actually wanted to offer our modules to pack builders. But it turned out that there were hardly any of them, or they didnโt deliver quality that was good enough. So, we started doing that in-house. Thatโs how we ended up with heavy-duty equipment: harbor materials, cranes, shovels. Our original technology is not really interesting for that, itโs too expensive. But we did gain a lot of knowledge and expertise in building safe and high-quality battery packsโ Van Twist explains.
For that sector, Power Battery builds battery packs that are based on Lithium Iron Phosphate technology which lasts up to a minimum of three thousand cycles. The packs have the same capacity as Li-ion technology, but are two to three times larger and heavier. โIn heavy-duty equipment, unlike in the racing and leisure industries โ space and weight are less important factors. Instead, it is particularly important that the packs are inexpensive and long-lasting.
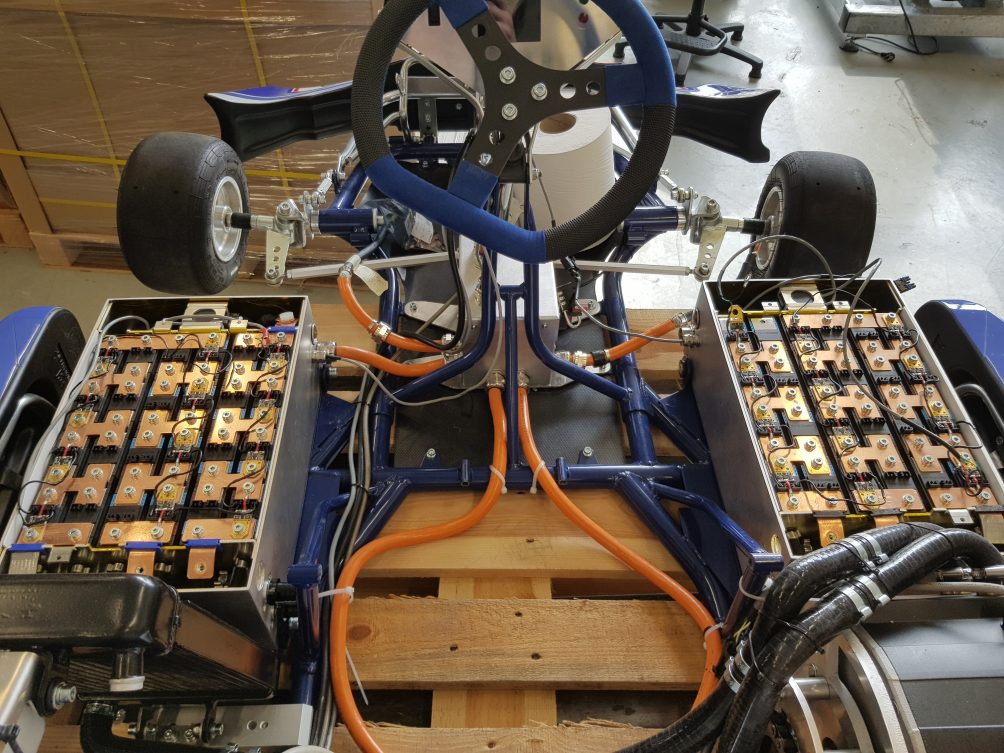
Brainport Region
The fact that Power Battery is located in the Brainport Region is very valuable to them, says Van Twist. He sees that there are plenty of initiatives coming from Brainport aimed at gaining a leading position in the European market when it comes to batteries and battery production. โFor example, there are a lot of companies that are looking into electric aircraft. That is also an area of application where Power Battery has managed to stand out. After all, flying is all about being small and powerful.โ
Power Battery frequently works together with other start-ups. โThere are more and more parties in need of clean powertrains. But because the market is relatively immature, a lot of parties are still looking for funding, both internally and externally, as well as at how the electric powertrain is put together.โ Aligning the various components in a powertrain โ controller, electric motor and a battery pack โ involves a lot of knowledge, Van Twist explains. โThe choice and tuning of different powertrain components still need to become much more readily available to a broader group of medium and small-sized companies. A lot of companies are struggling with that.โ
โThe choice and tuning of different powertrain components still need to become much more readily available to a broader group of medium and small-sized companies. A lot of companies are struggling with that.โ
Jan-Hein van Twist
The ecosystem
With the ecosystem in mind, Van Twist cites three things Power Battery would like to see. โFirst of all, more parties that understand motor-controller combinations, or are doing research on them. I envision a kind of online shop where you can find different, tried and tested and verified motor-controller combinations. It would also help if there were more electronics companies working on control units, so that the drivelines can be better aligned with each other. โWe get that knowledge from abroad at the moment.โ
Finally, Van Twist would like to see more freedom when it comes to regulations for experiments with electric flights. โA stretch of airspace where all the rules donโt have to apply and where prototypes can be tested. I see that governments from other countries do grant that freedom. Sure, the risk profile is higher, but you can gain a foothold in the market and fast-track product developments. In the Netherlands, we have all the components we need to create a strong profile for ourselves in the field of electric aviation. We, as Power Battery, would really like to contribute to that.โ
You can read more about automotive here.