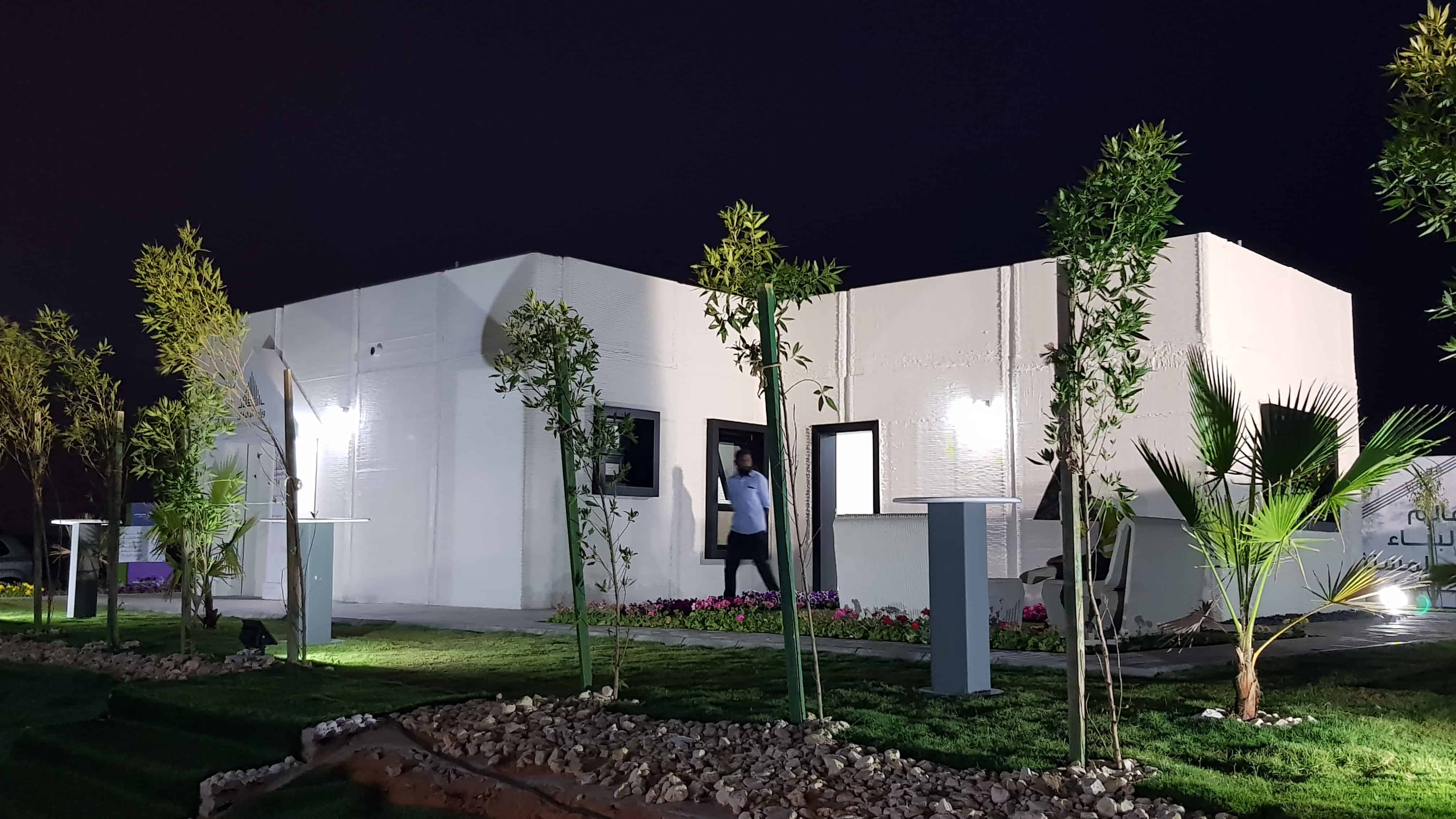
Nowadays, you must wait months or even years for a newly built home. The construction process does not always proceed as efficiently as it should, materials are lost due to mistakes and the choices are limited. Meanwhile, the housing shortage is worsening and there is a structural shortage of skilled workers. This poses a major social problem, for which a solution is not readily available. This is why the Dutch government is coming up with partial solutions by adjusting its policies. For example, by making amendments to the objection procedure for new construction projects, so that construction can start more quickly. However, more is needed: a major and structural change in the way we build and especially in the way we think about construction.
One promising innovation involves 3D printers. A concrete printer can quickly, accurately, and with minimal waste lay down the structure of a house. This way, the construction process can be automated โ at least in part. This saves time, money, and labor.
The game changer
โAutomation in construction can be instrumental in providing a structural solution to todayโs problems. 3D printing is a game changer. Construction will then become more of a process like you also see in the automotive industry,โ states Branko ล avija, associate professor at the Delft University of Technology (TU Delft). He is a member of a research group that focuses on materials for 3D printing in construction. ล avija: โFor instance, houses in the future could roll โ at least in part โ off the assembly line.โ
An assembly line for houses may sound a long way off. But scale-up CyBe is already working on this idea. The company would like to open its factory to fabricate houses. In the factory, a house would go from station to station, becoming more and more complete as it goes along. A 3D printer makes the walls, foundation, and floors, and then it also assembles insulation, plumbing, and all the other parts. This is how it can be transported to the construction site as a whole ready-made package. The complete process takes five days. After five days, every day a house rolls off the assembly line.
The company also sells its robots to universities and companies around the world. โOur customers print all over the world. They make homes, as well as artificial reefs (to grow more corals at the bottom of the sea, ed.), outdoor furniture, and other items. In addition, the robots are also used in research at universities,โ says Pleun Zant, marketing officer at CyBe.
Modular homes
In addition to modular construction, CyBe develops and sells five other printer models. One of these is a gantry printer, which can quickly and easily create modules that can be used to build modular homes. โ The dimensions of the modules are designed to be easily transportable,โ Zant says. The modules come from the factory fully complete, even the walls are plastered and the kitchen and bathroom are installed. โWe do as much as possible from a regulated, factory setup. At the construction site, the modules are set down and joined up (this can be done both horizontally and vertically, ed.). Itโs basically a plug-and-play principle.โ
Aside from the speed of construction, factory conditions also ensure a smaller margin of error, reduced transportation costs, and less waste. โWith a 3D printer, the process is more optimized which means materials are used more efficiently. Due to the optimal setup, the printer uses fewer materials than traditional construction methods, and therefore less is also thrown away,โ ล avija points out.
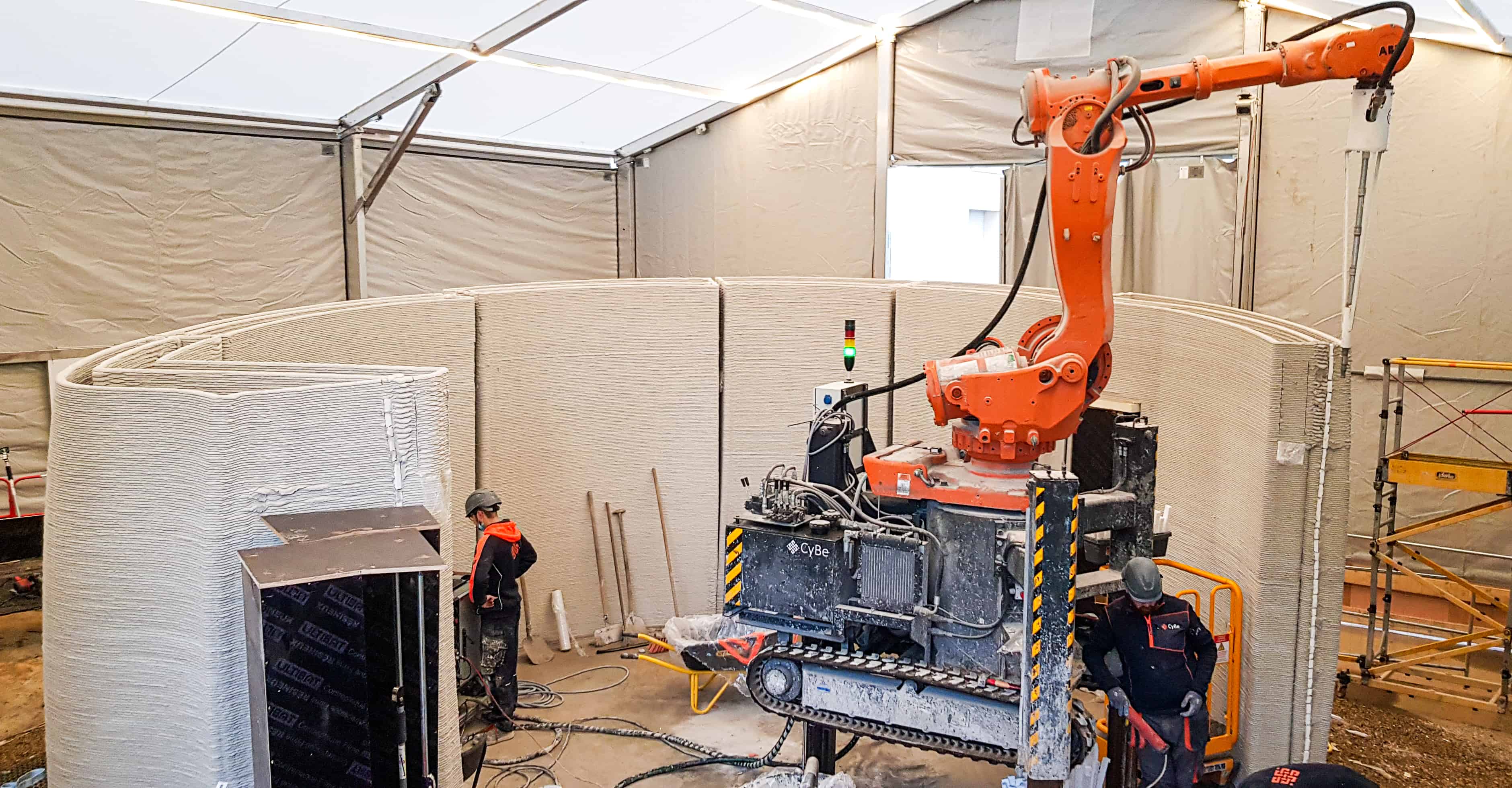
Making materials more sustainable
What he still sees are several opportunities to make materials more sustainable in the future, such as the concrete the printer works with. After all, concrete in itself is not an environmentally friendly material. โWhen it comes to concrete, the biggest polluter is cement. We have to figure out a way to use less cement or completely replace the cement with another type of material,โ ล avija explains. Researchers in his group has already been working on this for years. One possibility is to make use of a residual product from the steel industry. โI hope we get to work together with other sectors more. After all, the waste from one sector can, in turn, be a raw material for another.โ
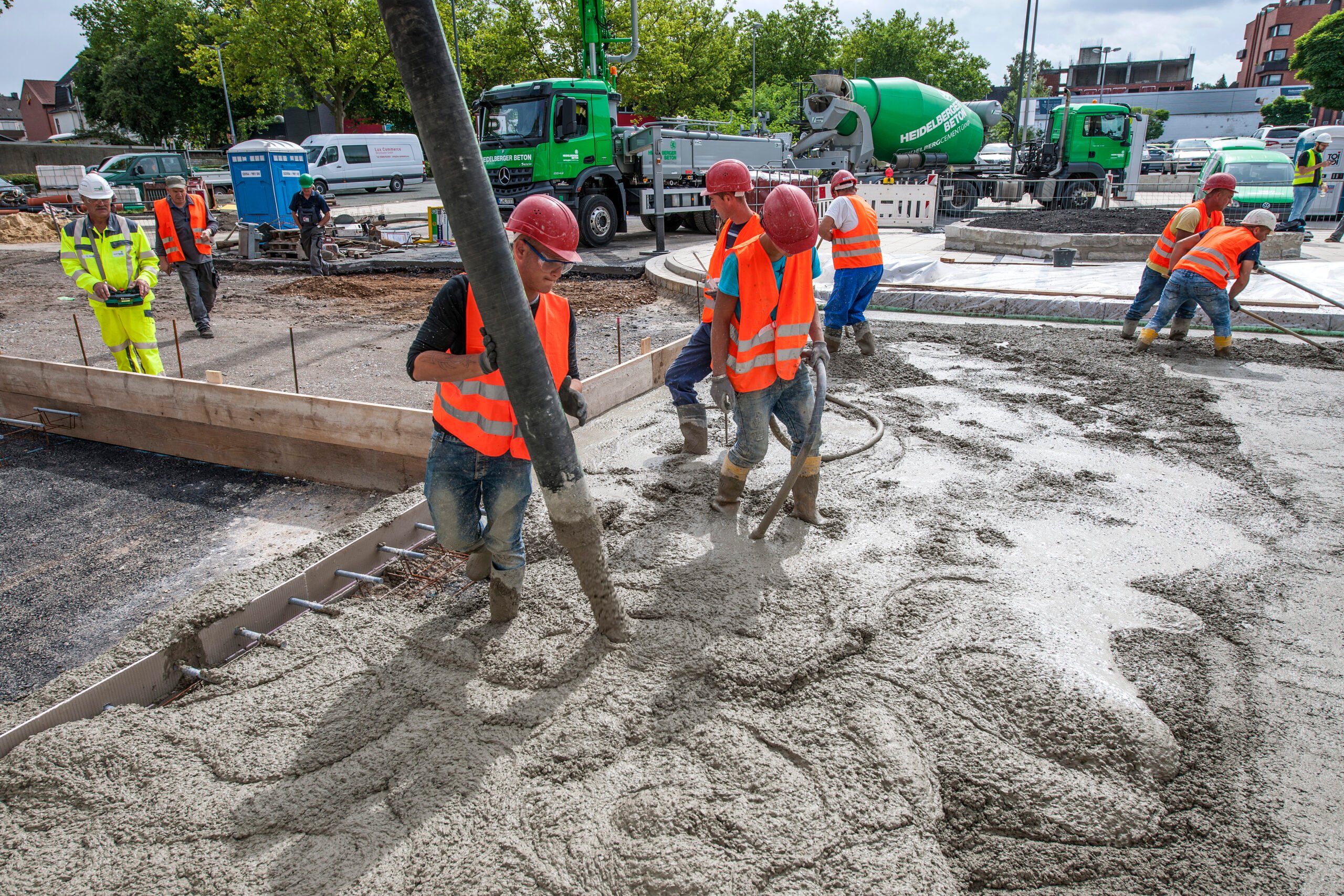
Still, ล avija does not necessarily view concrete as a bad option. โAfter all, concrete is quite durable compared to other materials. It is strong, cheap, widely available, and lasts a very long time. If we find a more environmentally friendly material that is not as strong, we will probably have to replace it more often. In the end, thatโs not sustainable either. I think we can and should replace concrete in some cases, but we should always take a good look at which material best suits a particular situation.โ He envisions, for example, a modular system that can be taken apart so that certain parts can be repurposed in other projects.
Crucial role for start-ups
The implementation of such a modular system involves changing not only the materials in the construction industry but also the mindset. This is a difficult feat. โInnovations entail a lot of risks. That makes it less appealing for established companies as well as to start working with them,โ ล avija explains. Thatโs why these kinds of developments often stem from universities. Scientists tend to focus primarily on technological innovation. However, to also make it economically interesting, the researcher sees an important role for start-ups. โA large number of start-ups have been developing 3D printers for construction for several years now. They often start with a subsidy from the government but reach a stage where they have to become profitable themselves. Now that thatโs starting to take shape, the risk for large companies is diminishing and they want to look at this innovation too.โ
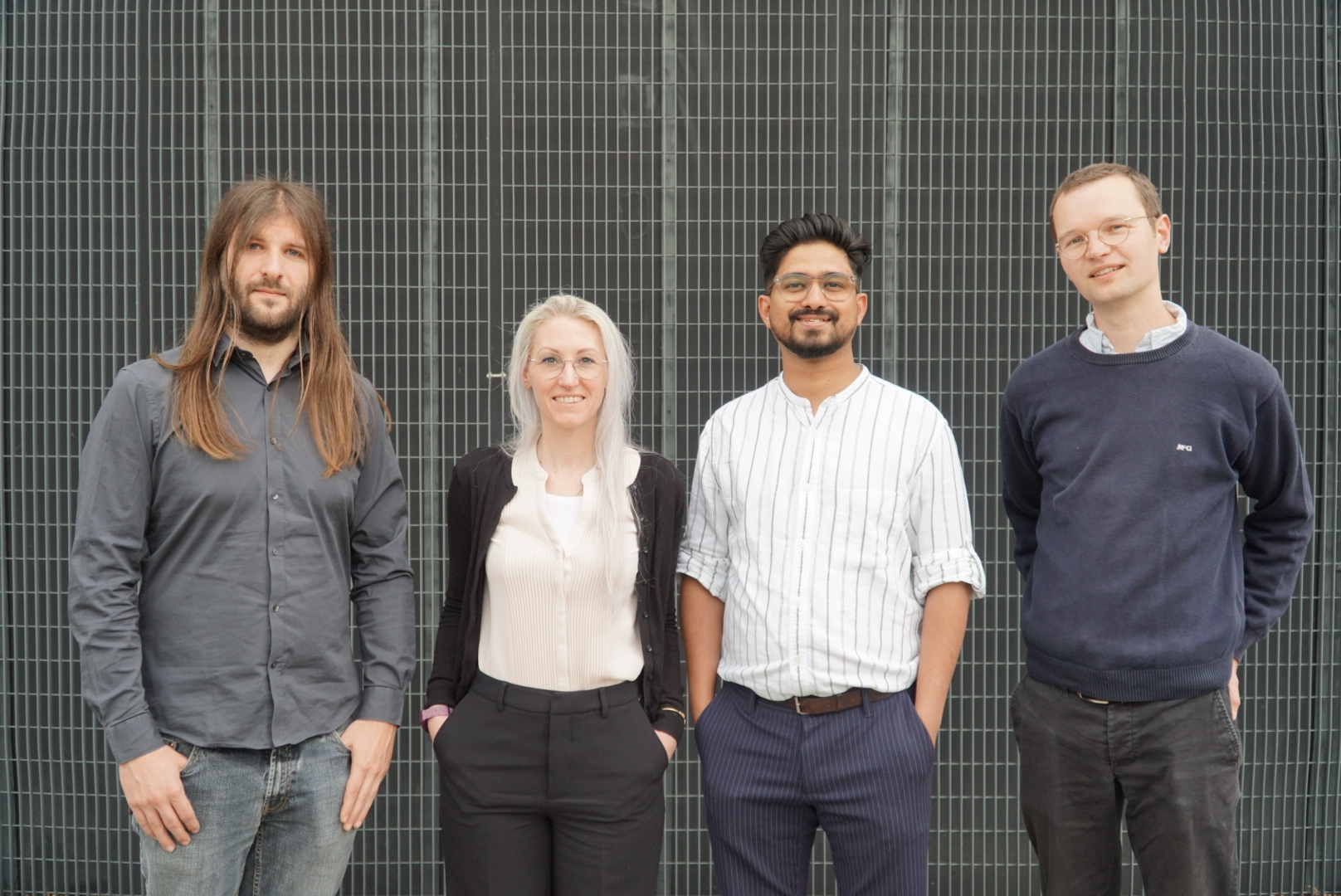
Bridging the knowledge gap
Apart from the willingness to invest, CyBe has also noticed a major knowledge gap between start-ups and reputable construction companies. The start-up is trying to bridge the gap with its learning platform. On this platform, customers can find such things as software and models to quickly get to work with the 3D printer. Besides construction companies, CyBe also has several universities as partners. Zant: โIn return, we gain new knowledge and insights through the universities, which we can then pass on to construction companies.โ
ล avija also sees increased cooperation with industry from within universities. โ3D printing in construction is a technology that is relatively easy to apply. That means that cooperation with industry early on is crucial to be able to make an impact,โ he states. Thatโs why the researcher is in contact with several start-ups, including CyBe. They are looking at opportunities to do projects together, for example for masterโs students. This benefits both the research and the actual application of innovation.
He also considers the cooperation between universities, including in the 4TU.Built Environment, is extremely important. This is a partnership between the four Dutch technical universities in the areas of scientific research and valorization in construction. โWe have already taken on several projects under the auspices of 4TUBuilt Environment. Each university does research on a different part of 3D concrete printing. For example, ล avija collaborates with the Department of the Built Environment at Eindhoven University of Technology (TU/e). From TU Delft, he focuses mainly on materials for 3D printing in construction. In Eindhoven, lecturer Rob Wolfs and professor and dean Theo Salet, among others, are working on the development of the 3D printer itself. โThatโs how we complement each other so well and make progressโ, he said.
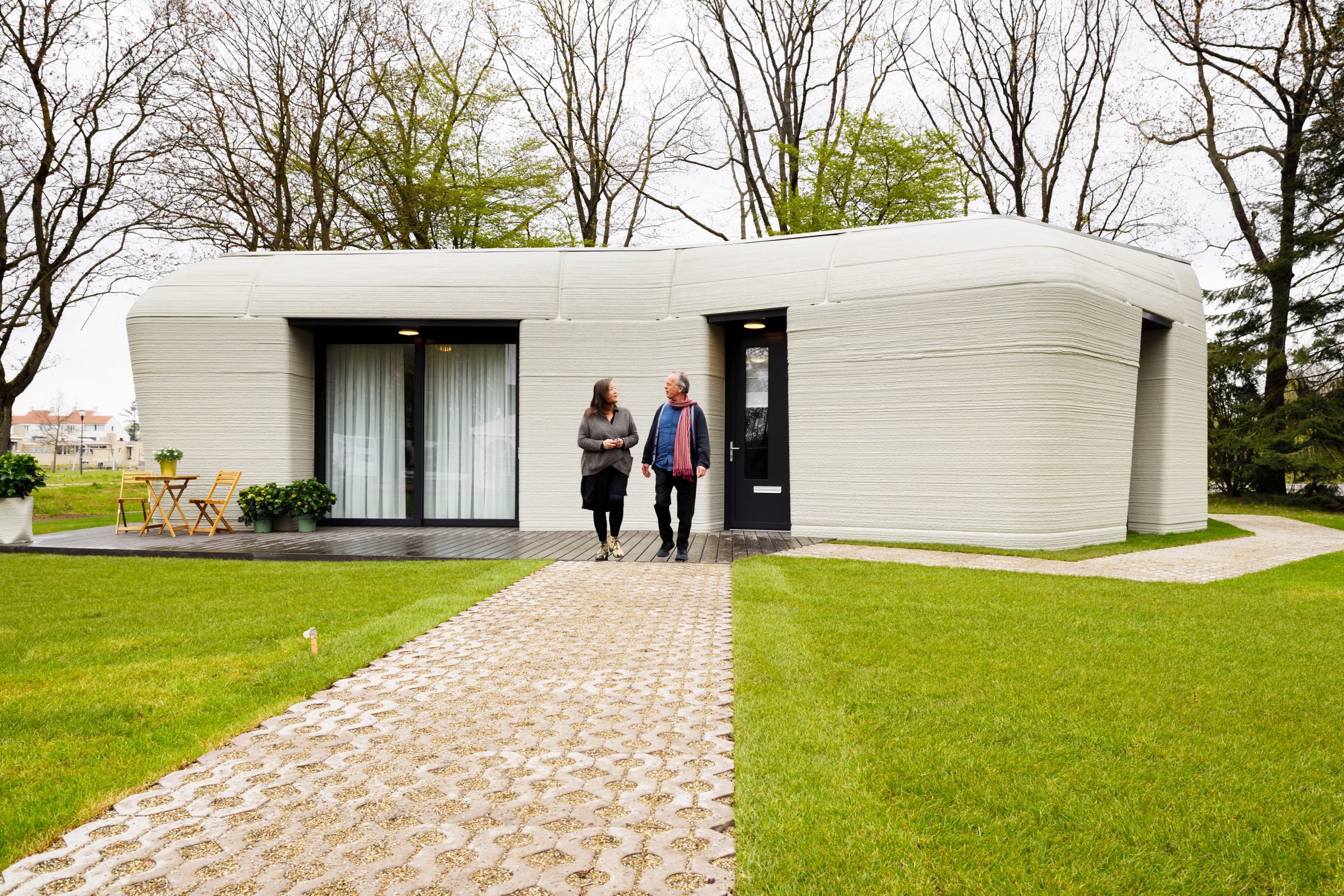
Obstacles
While the development of 3D printing in construction is advancing rapidly, there are still several obstacles to overcome. Concrete often has steel reinforcements for extra strength. At present, it is not yet possible to integrate that reinforcement into the printing process. The structures that have already been printed, such as a bike bridge in the Dutch town of Gemert in Brabant, were later manually reinforced. ล avija: โIdeally, you want to combine all parts and operations into a single automated process. This is not yet technically possible. Therefore, this new technology is no better than current construction methods. We still have some steps to take over the coming period to make it more compatible with the needs of the industry. If we can do that, then this technology can make a great impact in a range of fields.โ
The researcher is expecting that in the next few years, it may become possible to fabricate an automated structure. For example, think of a staircase or a bridge. A house, he notes, is even more complicated. โThen you also have to deal with plumbing and electricity. These are especially difficult to automate. But it would be nice if this can one day be done because we also have far too few electricians and plumbers.โ Zant adds: โIn our company, the plumbing and electrical fittings are also still installed manually in the houses at the moment. But this is all done in the factory. Thatโs already improving efficiency.โ
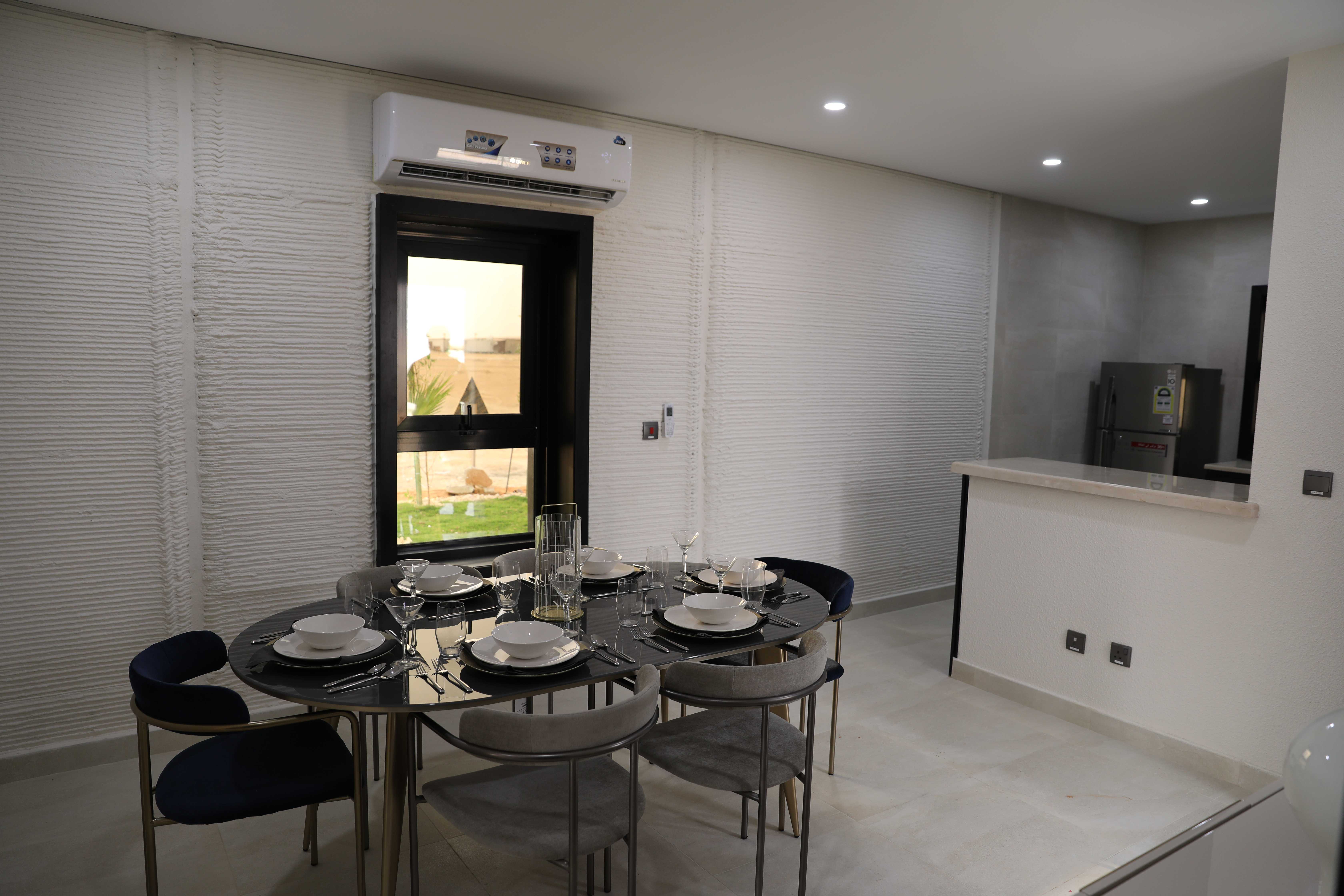
Choosing what you want
Both agree that the shape and construction freedom that a 3D printer offers consumers is the most important and appreciable part. A door in a different place, or extra electrical outlets are then no longer all that complicated. That can simply be configured in the model that the printer will create. Zant: โWe are currently working on an apartment complex where we made a bike rack and a flower box embedded in the wall. Also, one of our customers in New Zealand is making a 3D-printed water storage unit under a house.โ
A great deal of research is still needed to make improvements, but 3D concrete printing appears to be the bright future for science, industry, and the consumer alike. Zant: โIn any case, the possibilities are endless.โ