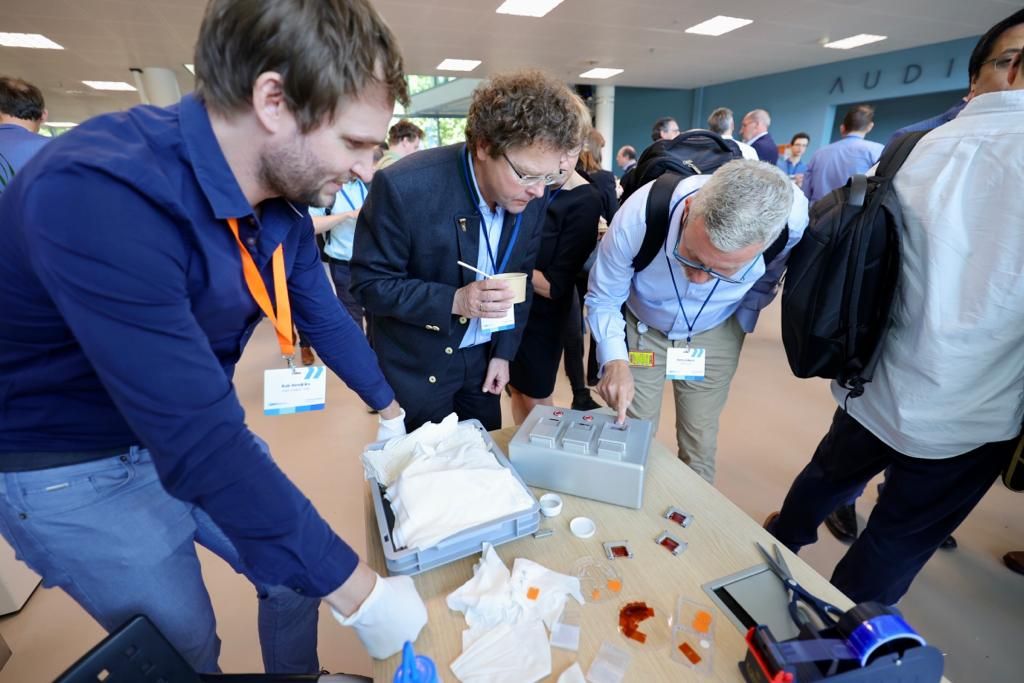
Electronics are becoming smaller but also more powerful. Their manufacturers are looking for ways to accelerate and scale up their production. Rob Hendriks is a program lead at TNO and a founder of FononTech, a spin-off company from Holst Centre that will launch soon. He has been researching impulse printing, which has the potential to be the solution that is needed. Impulse printing involves a technique that tackles challenges that manufacturers face. It allows the scalable and sustainable production of semiconductors, circuit boards, as well as different types of displays.
How FononTech was born
FononTech is the company that Rob Hendriks will be launching in the upcoming two months. Hendriks explains that he has spent his whole career in the printing industry. It all started because of his passion for developing a printer.
His journey started at the Holst Centre and eventually took him back there again. At Holst Centre, in collaboration with Fabien Bruning, he started from scratch and built a fully developed working prototype that incorporated impulse printing. “What you see here is a demonstration kit. We built it so small so that you can carry it in your suitcase and you can go everywhere with it. This is how you can demonstrate the technology and let people play around with it,” Hendriks tells.
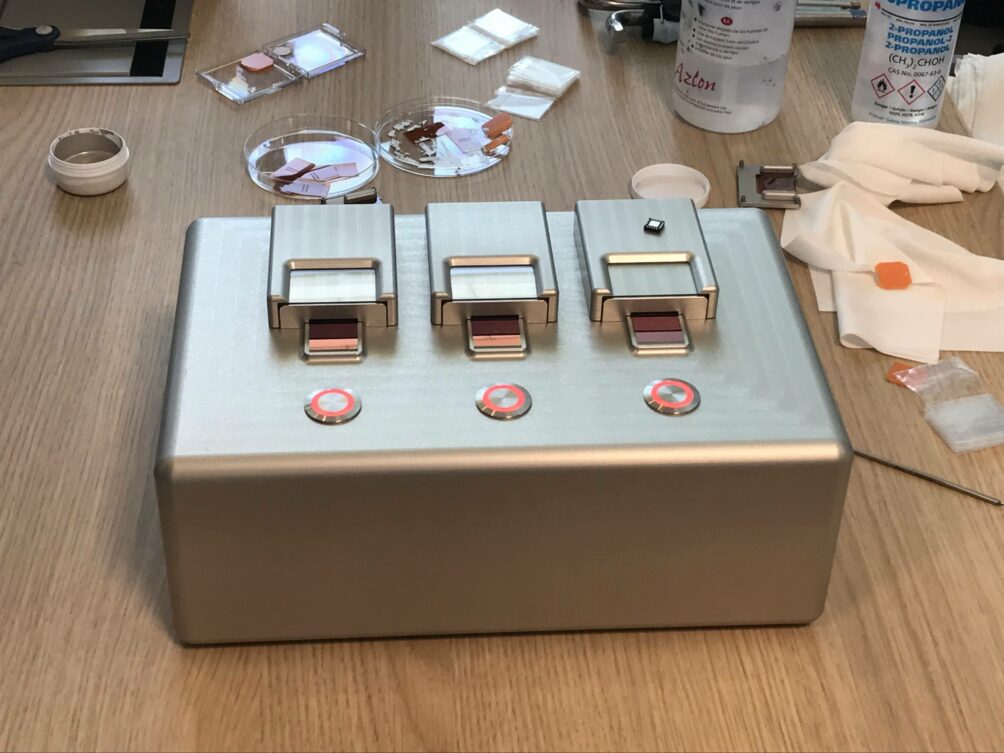
“I always wanted to develop a technology that could be industrialized,” Hendriks adds. Previously, he worked on projects but all of them got bogged down at some stage or could not be industrialized. “This technology is designed for scalability. Basically, we think we can end up being used on any electronic device,” Hendriks goes on to explain.
“We called the company FononTech because phonon is a heat particle. That’s where the names come from. All of our technologies are based on heat generation.”
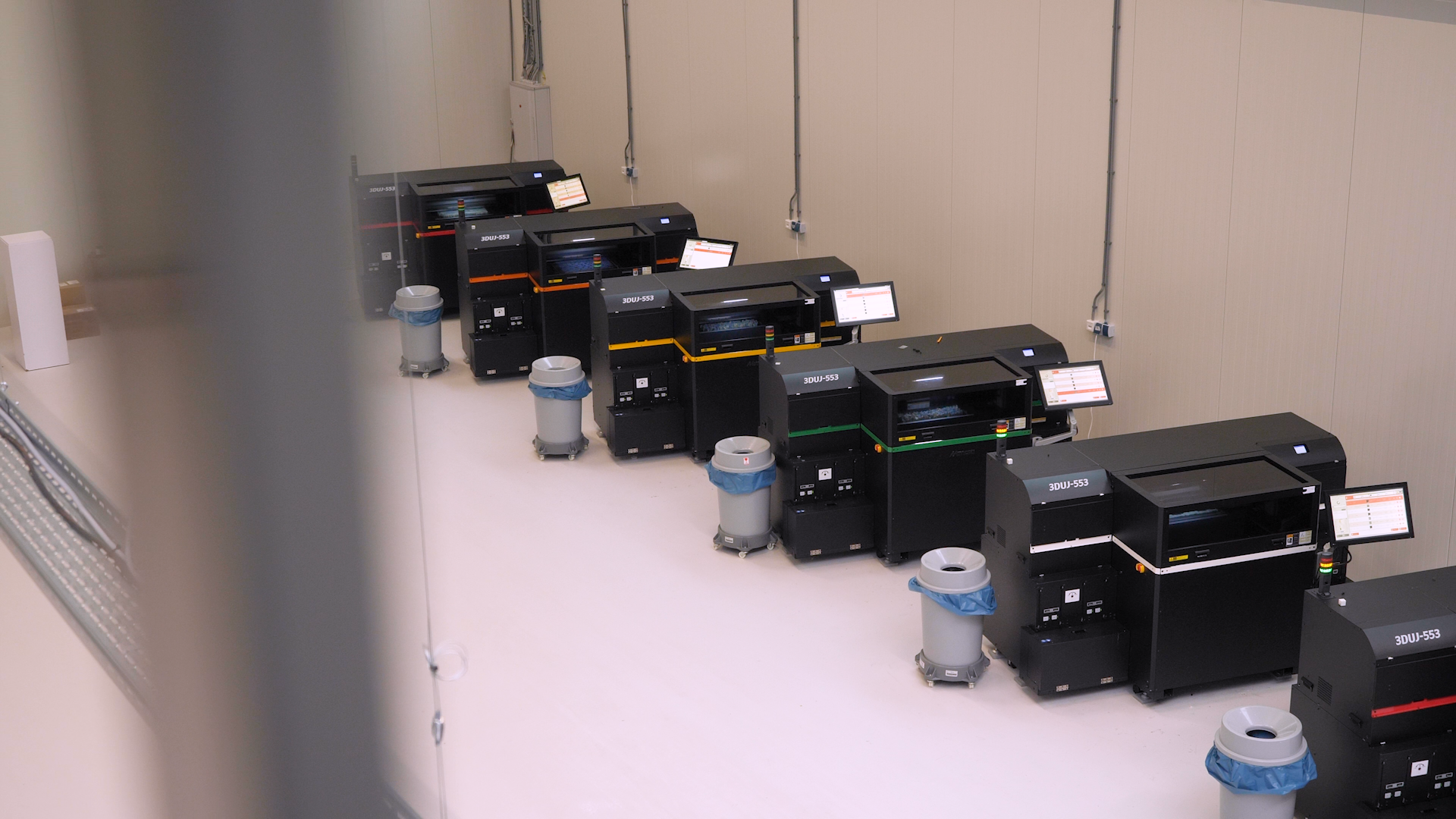
How does it work?
“The technology works by means of rapid surface heating,” Hendriks states. “We use a heater that heats up fast, so that when you put a liquid on top of it, you actually boil the solvent or the liquid.” When the solvent reaches its boiling temperature on the heater interface, rapid gas generation leads to a build-up of pressure. It pushes the ink at an incredible speed towards the surface that you want to print on. “It’s so fast that it accelerates at 1 million G-force.”
Impulse printing can print on any type of surface. “It’s incredible,” Hendriks exclaims. “In one microsecond, the ink is accelerated from zero to ten meters per second.” During the Holst Centre Innovation Day at the High Tech Campus, people could see, observe and learn more about the technology.
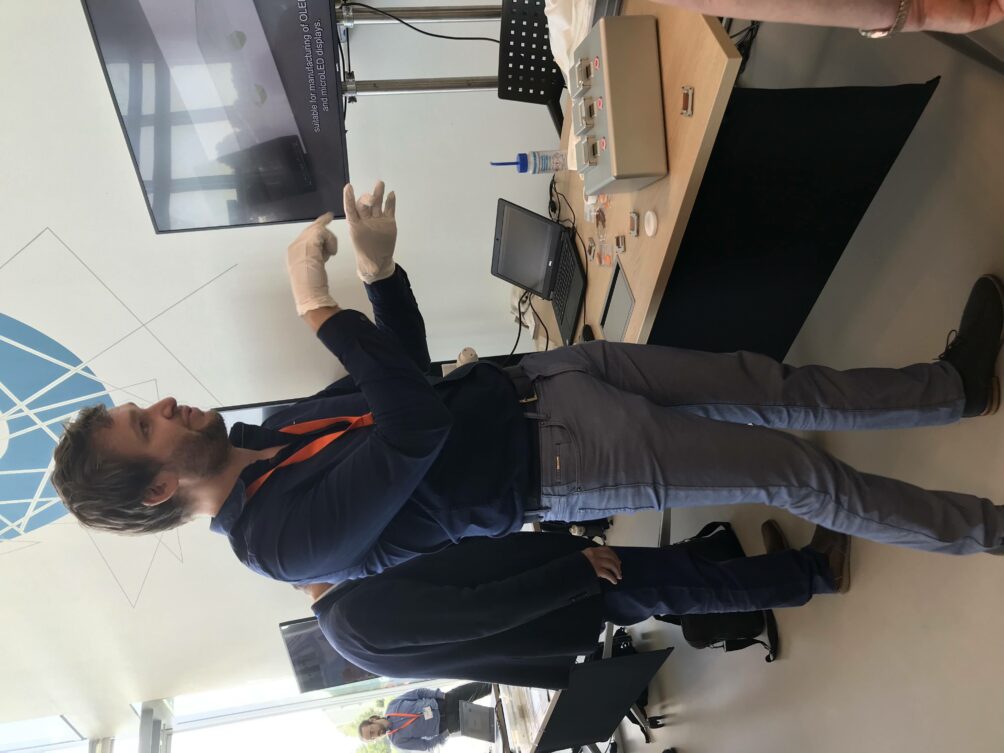
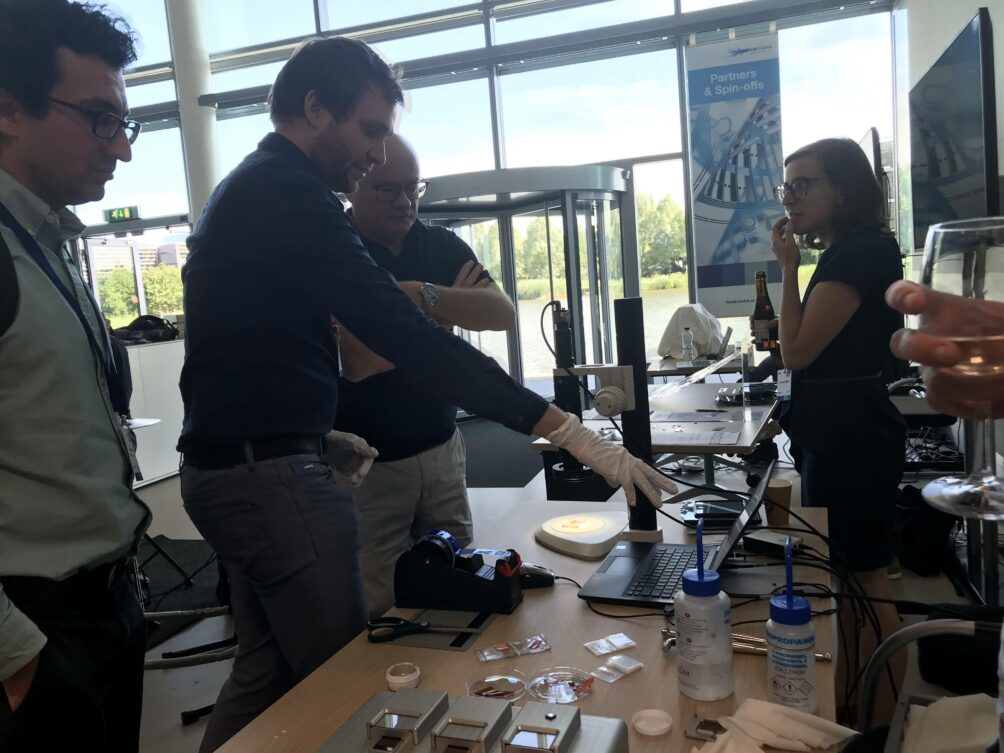
This technique addresses many manufacturing challenges. For example, it can deposit feature sizes ranging from several microns to many millimeters. The ink does not experience any shear forces, meaning that a wide variety of viscosities can be deposited. Therefore, impulse printing can print on any type of surface, and patterns can be printed over gaps or wrapped around substrates.
Industrialization
Currently, manufacturers employ techniques such as lithography or dispensing systems to create the components used for modern devices. “What the industry tries to do is to make chips smaller, more powerful and pack more of them in smaller spaces. And our technology enables this.”
“Our technology is really designed for scalability. And you will probably see it in phones, VR headsets, and smartwatches,” Hendriks says in conclusion.
Cover photo: Rob Hendriks at Holst Centre Innovation Day