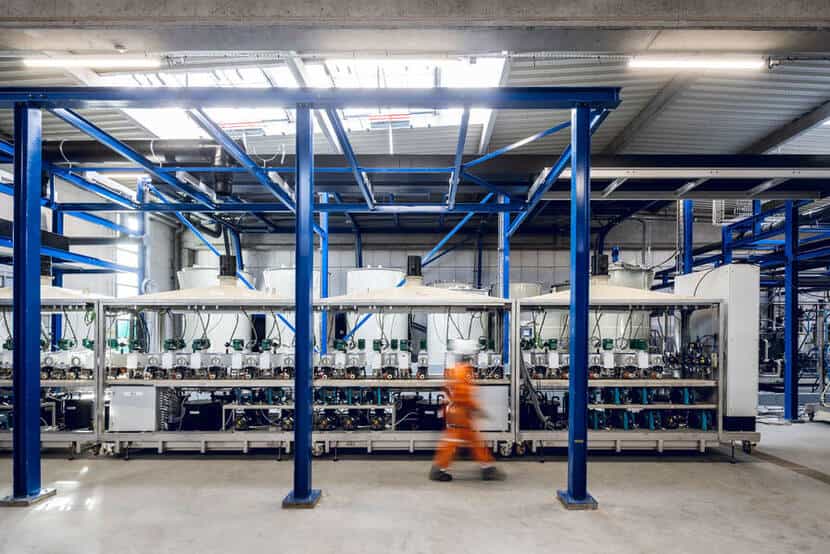
Mining group Eramet has invested 10 million euros in its R&D center in Trappes (Yvelines) to industrialize its innovative process for recovering metals from discarded batteries. The goal is to produce 250 kg of lithium and cobalt and 1,000 kg of nickel at the pilot plant. However, questions remain about the business model for the future plant in Dunkirk.
- ERAMET starts pilot plant in Trappes in preparation for larger plant in Dunkirk;
- Focus is on recovering 250 kg of lithium, 250 kg of cobalt, and 1 ton of nickel per year;
- Car manufacturers must meet European recycled metal quotas;
- There is still uncertainty about the business model.
Pink cobalt sulfate powder, green nickel sulfate pellets, and white lithium powder
Pink cobalt sulfate powder, green nickel sulfate pellets, and white lithium powder: this is what should soon come out of Eramet’s pilot plant for recycling electric vehicle batteries. The 800 m² plant, which opened on Nov. 14, is located at the mining group’s R&D center in Trappes (Yvelines), but production has not yet started there. It is a crucial step for the group, which wants to gain a foothold in the coveted market for critical metals in electric batteries. Eramet has plans for two recycling plants in Dunkirk.
Quotas for recycled material
European regulations impose quotas on car manufacturers for the use of recycled metal. Dismantling and reusing end-of-life batteries is becoming increasingly essential and inevitable. “The mine of the future is the secondary mine,” said Christel Bories, CEO of Eramet.
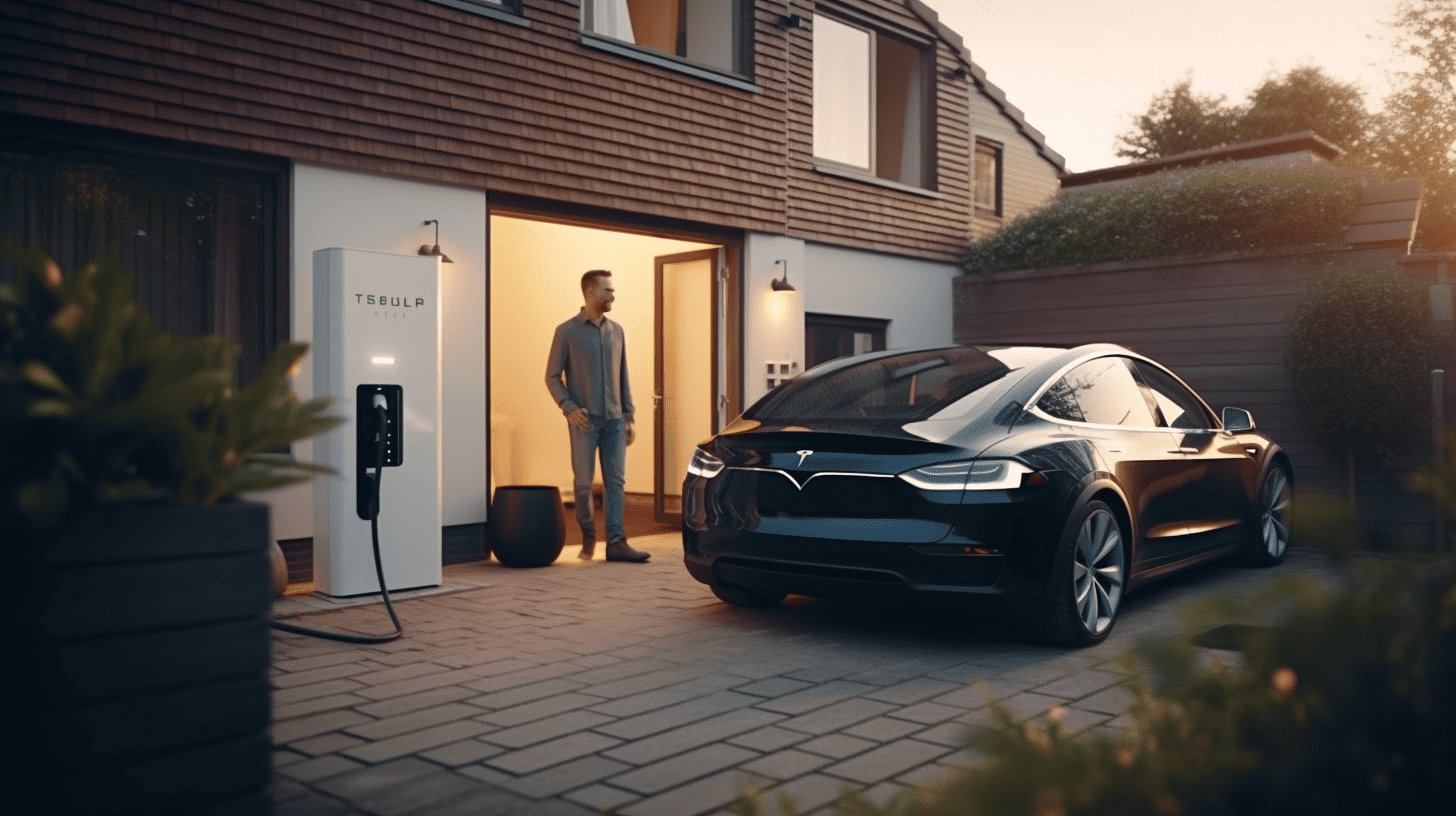
Plans for mega plant, 1,000 times bigger
Europe counts more and more recycling projects. For its part, Eramet has been working with the Suez Group on this issue since 2019. Suez is responsible for producing the black mass, the first recycling stage, where battery cells are ground into a fine black powder after removing the leading plastic, aluminum, and electric cable components.
Eramet is involved in the second part of the process: the hydrometallurgical recovery of cobalt, nickel, and lithium fused into the black mass. Their quality and purity are high enough to be reused in new batteries.
This second phase should be carried out on an industrial scale at the pilot plant in Trappes, in which ERAMET has invested 10 million euros, including two million euros in subsidies. With a capacity of 5 tons of black mass, the site is intended as a scale model of the future plant the group plans to build in Dunkirk. The pilot plant is expected to produce 250 kg of lithium, the same amount of cobalt, and one ton of nickel per year.
Battery quality
To achieve this, the black mass must first be purified and stripped of copper, aluminum and iron residues, followed by graphite. “This is where we make the difference. It is the most important stage in achieving battery quality,” emphasizes Frédéric Martin, head of the recycling project at Eramet, which has filed two patents for its process.
A business model is yet to be defined
The pilot plant will be used to validate the efficiency of the process, which should achieve a metal recovery rate of more than ninety percent. The water consumption of the future plant should also be determined. The lithium, cobalt, and nickel produced on a trial basis will be sent to car and battery manufacturers to check if it meets their expectations and to have the material obtained validated.
But there is another factor at play. Christel Bories wants to ensure that battery recycling becomes profitable. “We need to understand the business model better,” says the Eramet CEO. Talks with car manufacturers are ongoing.
The critical question is at what price manufacturers and gigafactories will sell their production scrap. Cell scrap, which accounts for ten to thirty percent of a gigafactory’s production, is likely to be the primary source of supply for the recycling plant in the first few years. However, recycling end-of-life batteries is also slow to take off.
Second plant: black mass production
The decision by the two partners, Suez and Eramet, to build a second plant in Dunkirk for black mass production, on the other hand, is likely to come sooner and is less under discussion. The project, in which Suez is expected to hold a majority stake, is much less capital-intensive. The investment should be approved in early 2024, and black liquor production would begin in 2025. The business model is also less in doubt. The plant, which is expected to employ about 100 people, will be supplied mainly by the future gigafactories in the Hauts-de-France region, which can process 200,000 batteries a year. “For safety reasons, the transportation of batteries is complex and expensive,” said Sabina Soussan, the head of Suez. Recycling close to the source is, therefore, essential.
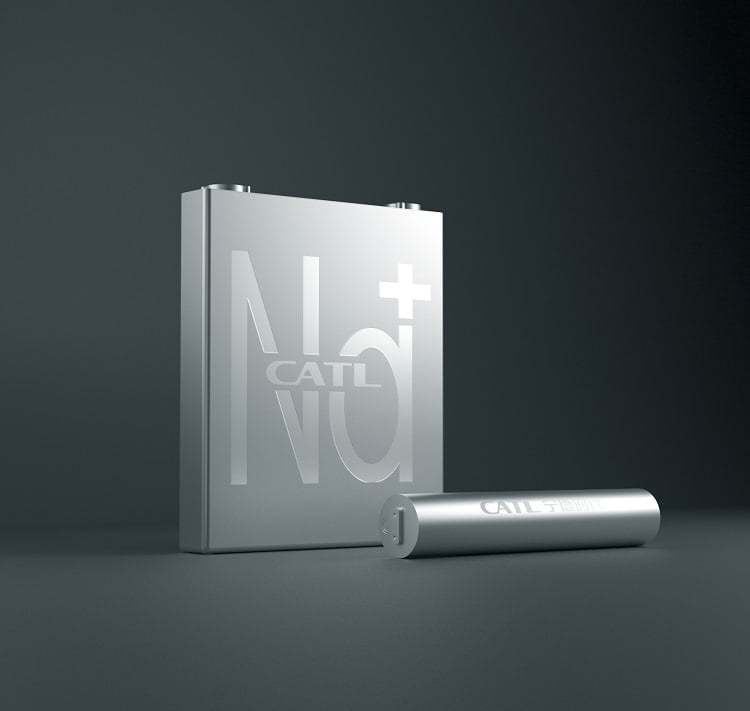