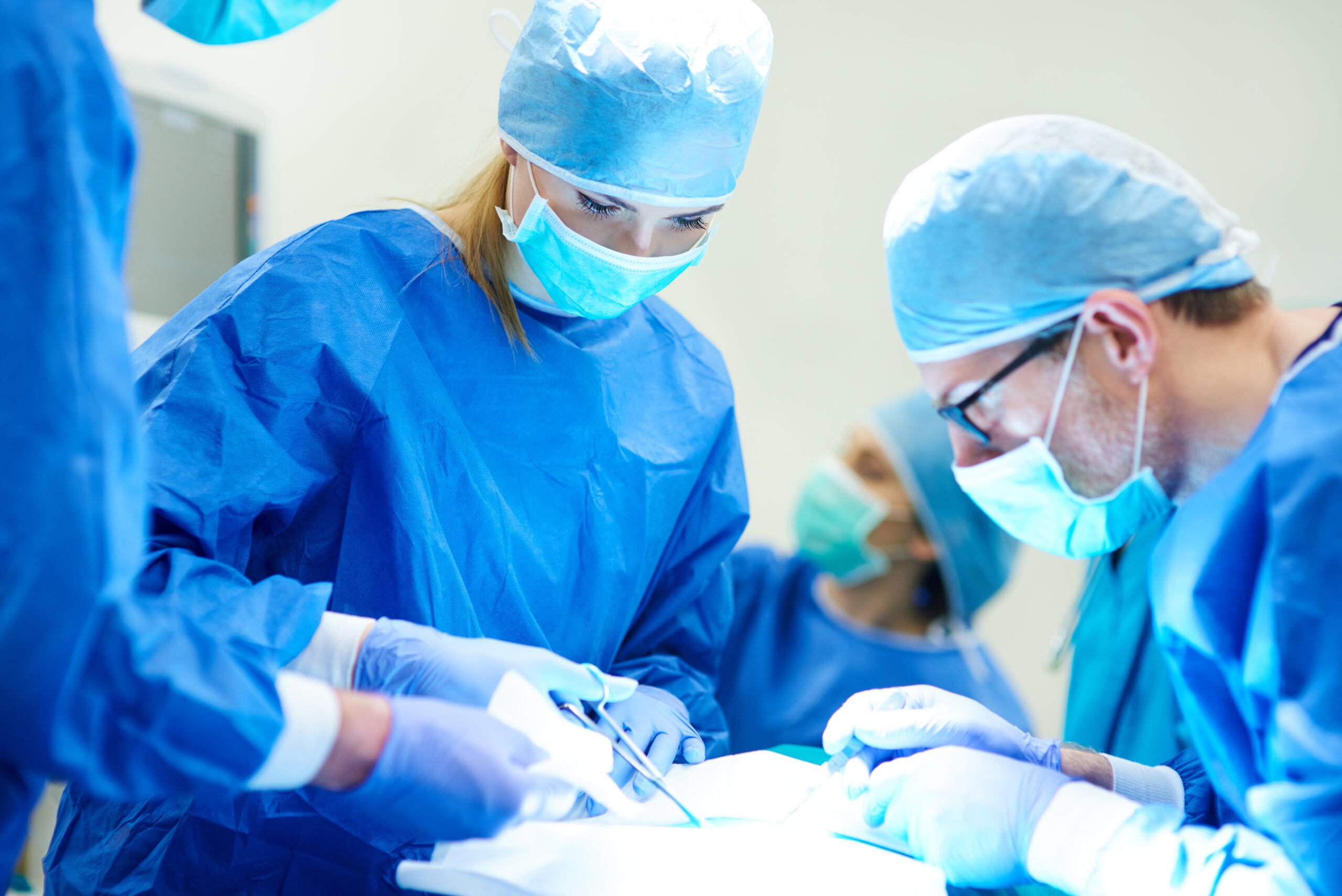
Overwhelmed by the corona pandemic and due to a severe shortage of medical supplies such as face masks, isolation gowns and anti-spatter goggles, the government and the healthcare sector purchased protective equipment from whoever was selling it. The call for sustainable home-grown products – and hence independence – was resounding. But competing with foreign prices and bringing sustainable products onto the market is quite a challenge, as Folkert Huysinga, project manager for Sustainable Innovation at Eindhoven Engine, well knows.
Jos van Mijl, owner of the textile screen printer Eco Textieldruk, mentioned earlier in this article that he had bought a machine that can produce more than a hundred medical face masks per minute. The machine has been idle for months owing to competition from abroad.
SBIR competitions
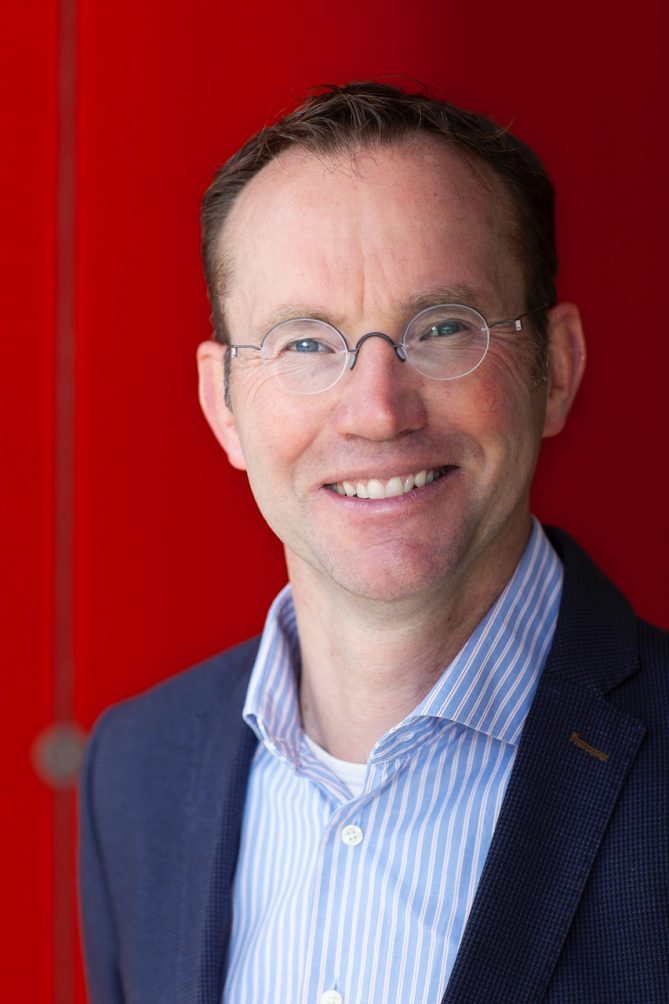
At the onset of the pandemic, Huysinga was production team leader at the Landelijk Consortium Hulpmiddelen (Dutch National Aid Consortium – LCH). He saw many initiatives like Van Mijl’s roll by. ” A lot of people and companies have invested time, money and effort since March 2020. The government has also provided help with this. It’s a shame that initiatives like this are threatening to peter out. Now is the time to move on and secure innovation in our own country for the long term.”
To follow up on initiatives such as that of Van Mijl, The Netherlands Ministry of Health, Welfare and Sport, in cooperation with the Netherlands Enterprise Agency, SBIR competitions (Small Business Innovation Research) are organised with the aim of creating new suppliers for the Dutch market for an innovative product or service.
Reusable isolation gowns and durable mouth-nose face masks
When the LCH was set up at the beginning of the pandemic, it was tasked with accelerating the procurement, distribution and manufacture of medical supplies in record time. Maarten Steinbuch, director of Eindhoven Engine, supported LCH in this endeavour. As a result of the collaboration, Huysinga, Steinbuch and Jaap Lombaers, director of Knowledge Management at the Netherlands Organisation for Applied Scientific Research (TNO), decided to enter Eindhoven Engine into two SBIR competitions: for medical nose/mouth masks and for isolation gowns.
Huysinga is the project leader and both initiatives are meanwhile in the second round. This means that the government is making money available for further research, the purchase of materials and production of the first models. “This is the last phase of funding, after which we should be able to stand on our own two feet,” says Huysinga.
Eindhoven Engine, the innovation accelerator at the Eindhoven University of Technology (TU/e) campus, is part of a consortium for both competitions. According to Huysinga, its strength lies in its cooperation with knowledge institutes, manufacturing companies, the healthcare sector and the government. “We look across the entire chain to see how things can be improved and made more sustainable. In terms of material use and in terms of production, but also in terms of waste processing, safety and wearing comfort. We cannot do this alone; the strength of Eindhoven Engine lies in the fact that we seek cooperation with specialised parties.”
Reusable ProH-I isolation gown
For the sustainable isolation gown, Eindhoven Engine started a collaboration with researchers and students from TU Eindhoven, Fontys and TNO and with Havep, a company from Brabant that is known for its manufacture of protective clothing.
The ProH I jacket is reusable and made of a stretchable PET material with an innovative membrane.
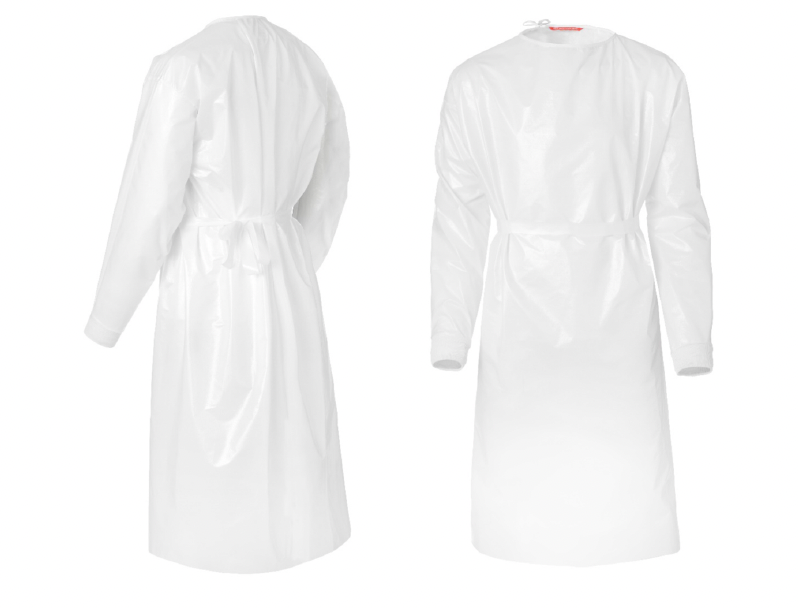
Pro-Mouth/nose masks
Eindhoven Engine, together with Sion Biotext from Limburg – a company with a wealth of experience in the production of medical nose/mouth masks – and TNO, are developing a sustainable face mask that is based on renewable and biodegradable PLA, PHA and/or starch mixtures.
The materials are produced in the Netherlands and Europe. With the introduction of the masks, Eindhoven Engine aims to save 770 tonnes of crude oil annually for the production of 150 million masks.
Competition from abroad
As is the case for Van Mijl, competition from abroad is one of the key challenges for the consortia that Eindhoven Engine is part of. ” After all, labour in China is much cheaper; we simply cannot compete with that,” says Huysinga.
Nevertheless, Huysinga has faith in realising a sustainable, Dutch production line for medical protective equipment: “No matter how low-priced the supplies from abroad are, it is not sustainable to have everything flown in from so far away. Moreover, during this crisis we have also seen that something as simple as a shortage of face masks or isolation gowns can paralyse the entire healthcare system. It is therefore very important to become less dependent. We can also see opportunities for further innovations in domestic production.”
Independence, innovation and more insight into the quality of the protection equipment are consequently major advantages for manufacturing on Dutch soil. Moreover, although hospitals buy medical equipment themselves, the government is nevertheless ultimately responsible for offering a sustainable alternative.
Automation, knowledge and expertise
Huysinga regularly sits at the table with the Ministry of Health, Welfare and Sport, the RVO, procurement organisations and hospitals. “A lot of energy is now being put into sustainable, Dutch production, through the SBIR competitions for example. The key question is still: how can we ensure that the sustainable masks that we produce here in the Netherlands are not 20% more expensive than masks from China? I think we can come a long way through a high degree of automation, knowledge and expertise, as long as all parties remain on board and have the courage to look beyond the cost price.”
In any case, Huysinga hopes that the sustainable alternatives will have a fair chance of success. It seems “dramatic” to him if later, after all the energy and time he and others have invested, he is told: we’re not going to do it, it’s too expensive. “That would be short-sighted. Everyone, the government, procurement organisations and producers, should dare to go for a long-term solution instead of a quick win.”
Huysinga describes his task as project leader for sustainable medical supplies as a “complicated challenge”. The Dutch procurement policy for medical supplies is a much-discussed topic, which means that everything Huysinga does is put under a magnifying glass. “That makes it interesting, but also very difficult.”
In March 2020, everyone, including companies, were willing to put their shoulders to the wheel all together. Now everyone is tempted to crawl back into their own corner, while we can only compete with other countries if we we start thinking in terms of Netherlands Ltd. I have seen some excellent cooperation initiatives emerge from that perspective.
Folkert Huysinga
BV Netherlands
Huysinga endorses Van Mijl’s plea for a Dutch network of medical face masks that is safe and sustainable. He is convinced that it can be done, but it will be difficult no matter how. Huysinga sees the ‘one for all and all for one’ spirit that prevailed at the start of the pandemic slowly dissipating. “In March 2020, everyone, including companies, wanted to buckle down together. But now everyone is tempted to retreat into their own little corner. Whereas we can only compete with other countries if we start thinking in terms of Netherlands Ltd. With that in mind, I have seen some excellent cooperation initiatives emerge from that perspective.. We have to think less in terms of our egos and more in terms of the interests of the ecosystem.
If the sustainable nose and mouth masks from Eindhoven Engine actually materialise, it may well be that Van Mijl will have to dust off his machine. Huysinga: “If we succeed in bringing a sustainable alternative to the market, we will also need to be able to scale it up and see which partners we can do that with.