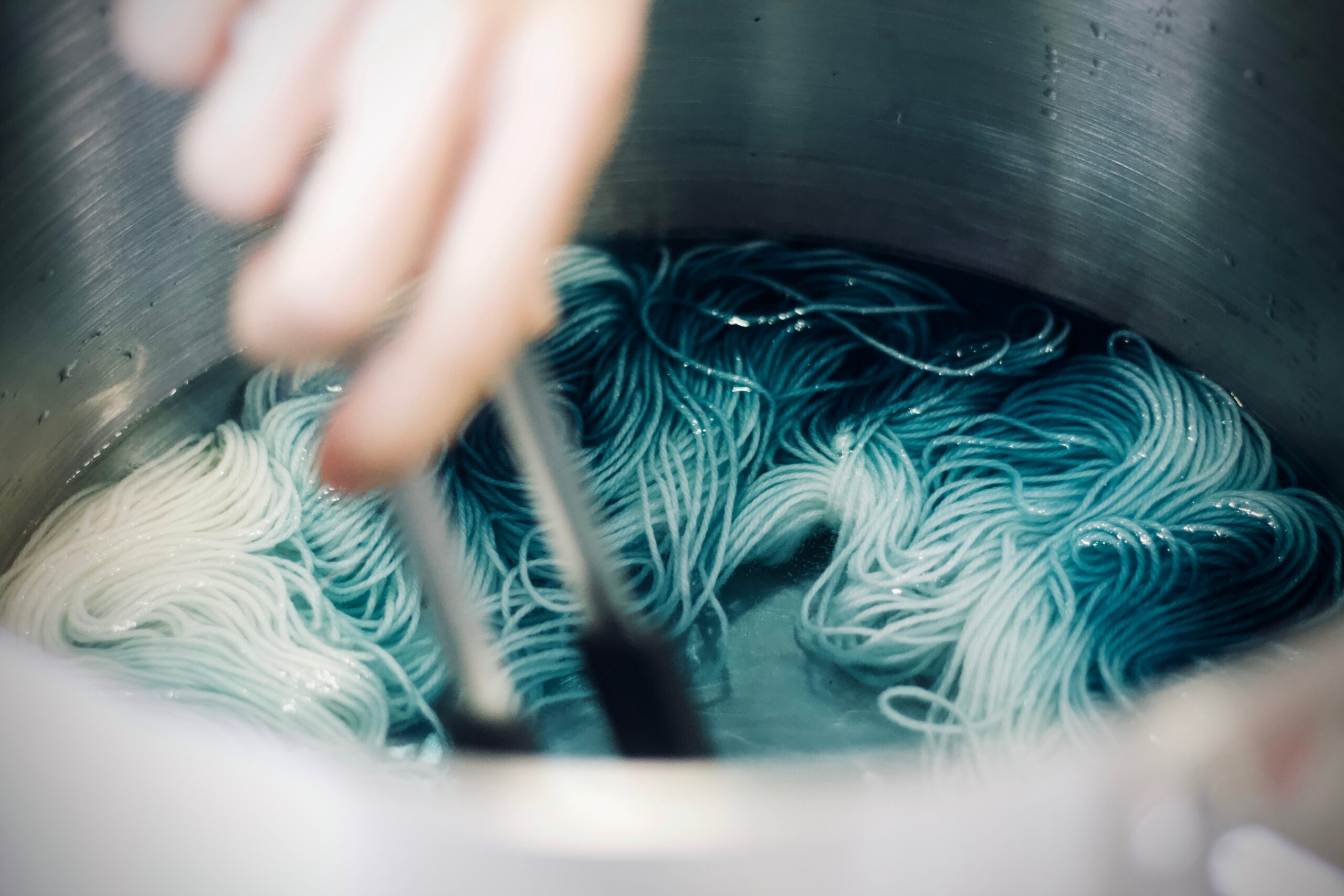
Textile dyes still contain harmful chemicals for which no efficient, sustainable alternative has yet been found. Black pigments from waste materials could form part of the solution.
Synthetic textile dyes are often derived from non-renewable petrochemical compounds. If not processed correctly, they further contribute to water pollution. The development of sustainable textile dyes has made great strides recently, but there are still many hazardous chemicals in use that are listed on the ZDHC’s RSL and mRSL lists. This is because no similarly performing, less harmful alternative has yet been found.
Zero Discharge of Hazardous Chemicals (ZDHC) is an international coalition of companies and organizations working together to eliminate hazardous chemicals from the textile industry.
Why black?
Black is one of the colors most commonly used to dye clothing. At the same time, black is also one of the most harmful textile dyes to humans and the environment. This is because black is not actually a color, but must be mixed together from several complementary pigments such as blue, orange, or yellow. In addition, there are many manufacturing processes for black, increasing the likelihood that questionable ingredients creep in. Textiles dyed in Europe have been subject to the EU’s REACH chemicals regulation since 2007, which requires registration of the substances used. For textiles imported into the EU, however, there is still a lack of transparency.
Also interesting: Truly sustainable cotton that is water-repellent, fluorescent and super magnetic
Waste materials are a solution
To find a sustainable solution compatible with people and the environment, Fashion for Good is launching the Black Pigment pilot project. The research consortium includes three innovators and international partners from the fashion industry: the French Kering Group, the American PVH Corp. and the Danish Bestseller Group. Together, they aim to develop black pigments from waste materials that are suitable for spin-dyeing two types of fibers: man-made cellulosic fibers (MMC) and yarns made from recycled polyester (rPET). Black pigments are a special form of carbon, consisting of very small particles with high opacity. If extracted from waste materials such as industrial carbon, algae and wood, they could replace synthetic textile dyes. They could also enable more sustainable textile production with less carbon pollution.
High opacity
The high opacity of black pigments is relevant in that it is often not present in synthetic textile dyes. Synthetic fibers in particular have a low tendency to combine with dyes. Experts speak of color affinity.
In conventional processes, halogen compounds or heavy metals are used to achieve high color affinity. In the case of black, for example, this is lead. But heavy metals are toxic and pollute the groundwater in the countries of production. They also endanger the health of textile workers who are exposed to them in high concentrations.
The three innovators – Graviky Labs, Living Ink and Nature Coatings – are from the U.S. and bring different technologies to the table:
Graviky Labs produces dyes from carbon emissions sequestered from the atmosphere.
Living Ink makes black pigments from algae that are bio-based and with a negative carbon footprint.
Nature Coatings transforms wood waste from certified sources into high-performing black pigments in a circular manufacturing process that produces almost no emissions of CO2 or other greenhouse gases.
Wastewater-free dyeing
The pilot project focuses on spin dyeing, whereby the color is added to the polymer blend before it is spun. No wastewater is produced in the process. As a result, spin dyeing is considered to be a resource and environmentally-friendly production process for synthetic textiles. Due to its high opacity, the color quality is also better than with synthetic textile dyes.
But the technologies of the three innovators have so far only been used for textile printing. To adapt the formulations to spin dyeing, the three innovators are supported by Fashion for Good industry partners Birla Cellulose and Paradise Textiles. Paradise Textiles is the Alpine Group’s materials research and innovation center and contributes its experience to the application of advanced total manufacturing processes for sustainable and high-performance fabrics. Birla Cellulose contributes its technical know-how to the production of spin-dyed MMC fibers.
Free of hazardous substances
The composition of these new dyes is water-based and they contain no substances from the Restricted Substances List (RSL). This relates to the end product and lists substances or groups of substances that may only be detectable to a limited extent or not at all in the end product. The RSL must be complied with in order to reduce the toxicological exposure of humans and the environment to chemicals.
At the same time, the pigments meet one of the most important criteria for textile dyes: they are colorfast. This is an aspect where other sustainable textile dyes often fail. This means that the black pigments do not fade in the sun or turn brown or bronze at either high or low concentrations. Added bonus: The pigments are suitable for a wide range of applications, including screen printing, rotary printing, coatings, paints, resin casting and the dyeing of wood.
Performance
The first MMC fibers and rPet yarns spin-dyed with black pigments will emerge from the first phase of the pilot project. This means that the performance, colorfastness, wearability and effect of all solutions can be evaluated as early as mid-2022. Next, the yarns and fibers from the most promising formulations will be processed into fabrics and tested in larger production runs.
To evaluate the research and development results, the fibers and yarns dyed with black pigments will be compared to standard synthetic dyes currently used in the industry. Color affinity, colorfastness, light fastness and tensile strength will be analyzed.
Following initial successes in spin dyeing with black pigments, the project will be extended to textile production. The long-term goal is to integrate these technologies into the value chain on a commercial scale.
Also interesting: Vienna Textile Lab dyes fabrics with bacteria