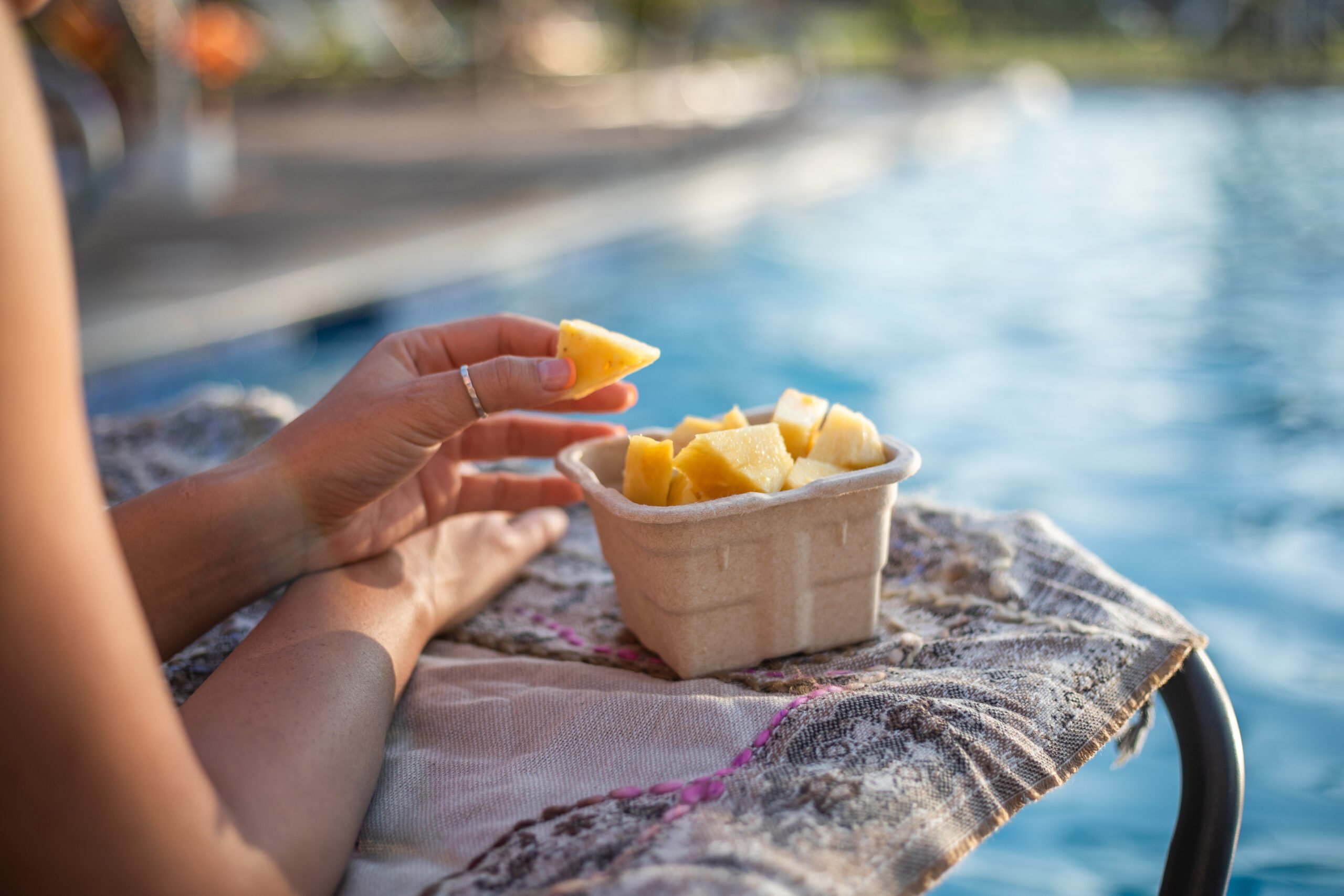
The globally operating company Footprint decided last year to set up its European headquarters at Brainport Industries Campus (BIC) in the city of Eindhoven, the Netherlands. The expansion across Europe, the Middle East and Africa (EMEA) will be led from this new location. โBy the end of 2022, the European Research and Development center at BIC will be up and running,โ says vice president of sales Joost Bakx.
Attracting new talent
On the choice for the BIC, Bakx says: โThe main reason is that we need to find technical talent to develop our plant-based packaging. This talent is in very high supply in the Eindhoven region.โ A second reason is the fact that Eindhoven is an important hub for innovative technology companies. โAt BIC, there is a wonderful interplay between many different companies that can strengthen each other. Whatโs more, several educational institutions are also located here. Itโs really interesting to collaborate with them and also attract talent that way,โ Bakx explains.
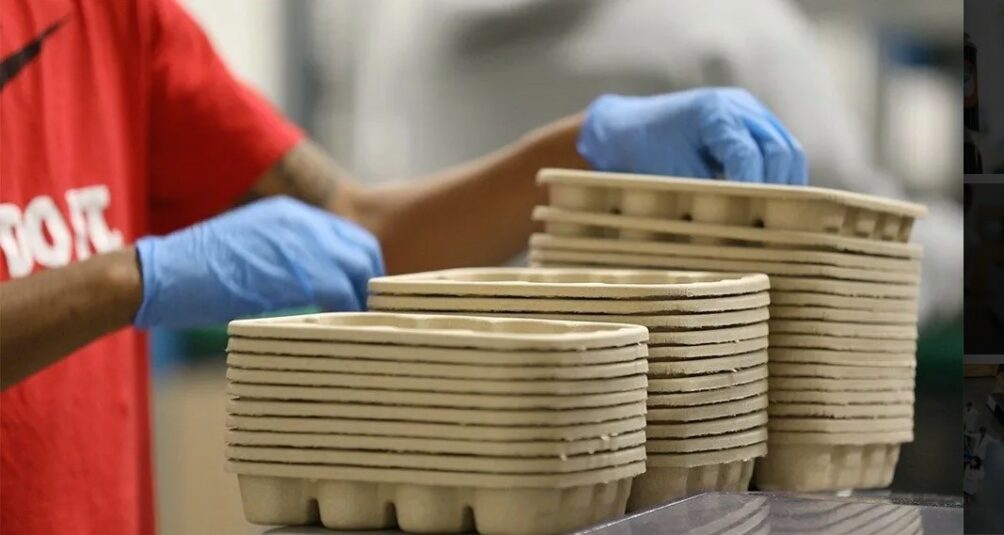
Circular material
Footprint has now more than 2,000 employees worldwide and is expanding rapidly. The company focuses on developing solutions for parties who want to make the transition from single-use plastic to circular materials. Plant-based products are used in this process. Bakx explains: โWe make our products based on wood fiber and wood pulp. It involves the whole trajectory. We design, develop and manufacture our own products.โ The wood fiber for the U.S. market is currently sourced from Canadian or US forestry. โThese are all managed forests,โ Bakx points out. โFor the European market, we are going to source the wood fibers from Scandinavian countries.โ
Natural barriers
Bakx makes a differentiation between technologically simpler products, such as plates and cutlery, and those products with more added value, such as coffee mugs and meal containers. โWith the latter category, a specific type of barrier is needed that is not naturally there. However, we can create that barrier with our technologies. This is how we are able to mimic the properties of plastic,โ Bakx notes. An example of how such a technology works is that it is capable of containing water or oil in a product so that it does not leak. Bakx: โA plant-based product has many openings by nature. If you magnify it, it looks like a birdโs nest. So we have to try and close those openings so that a barrier against water and/or oil is created.โ
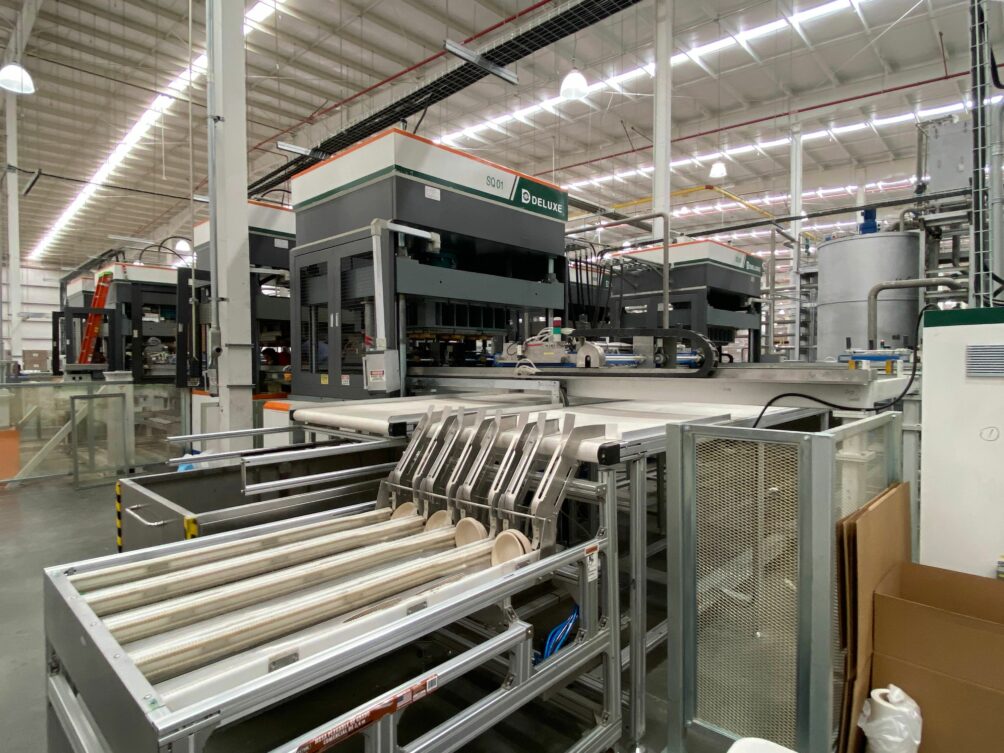
Interplay between fibers
Bakx details a few more things about the underlying technology: โItโs an interplay between different types of fibers. There are short and long fibers, straight and curled. That in itself already provides a certain strength. We use chemistry to bind the fibers and make them even stronger. In all cases, this is enough to create a water barrier.โ Yet thatโs not all. The way the parts are formed also plays a role. This involves thermoforming, also known as vacuum forming. Bakx: โThe parts are vacuum-sucked from a pulp slurry. Then they are pressed. They reach their final shape and protective properties under the influence of heat. This is a special part of the process that you have to master properly in order to be able to create those barriers.โ
Single use
On the lifespan of the products, he says, โOur goal is to help customers eliminate single-use plastics from their entire processes. As such, our products are intended for single use. But they are compostable and/or recyclable. Consequently, after use, no harm is done to the environment.โ In the event that the products do end up in the environment, they will decompose within sixty days.
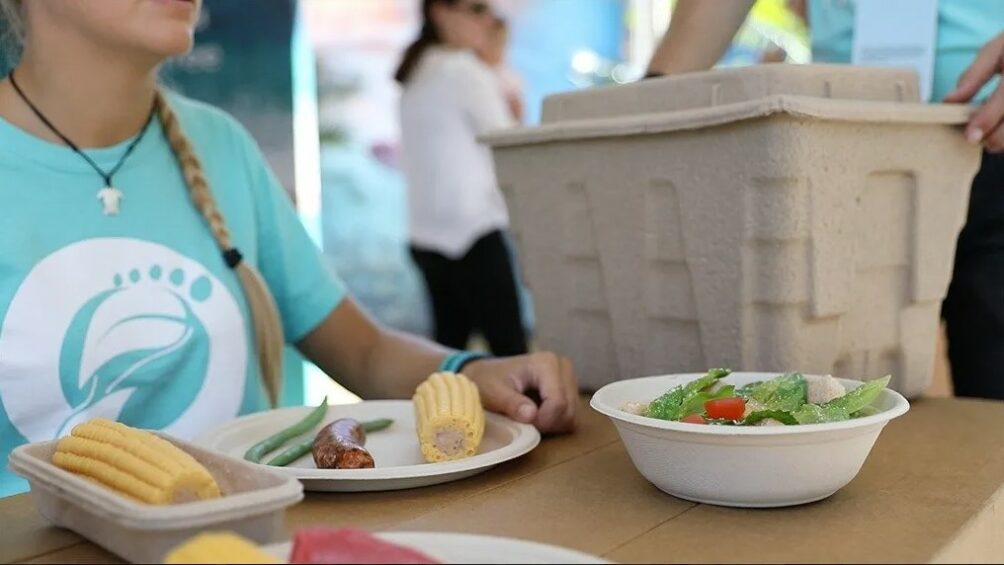
Dying turtle
Footprint is specifically focusing on the food industry. From 2024 onwards, this industry will have to comply with much stricter rules when it comes to the use of disposable plastic. Disposable products such as cutlery, meal containers or cups will no longer be allowed in offices, restaurants or festivals. All this is related to the Single-Use Plastics EU Directive. The first step was taken last year, with the banning of plastic straws and cotton buds, among other things. โYou no longer see these in the European market either,โ Bakx says. A subsequent step by the SUPD was to add a logo of a dying turtle to plastic coffee and drinking cups. This logo alerts consumers to the fact that the cups are detrimental to the environment.
Next year, companies that make products for food consumption will be required to start contributing to the recycling system for those products. โIt is still unknown what the cost of that will be. But in any event, the new rules make it clear that itโs prudent to consider alternatives like the ones provided by Footprint. For one thing, the companies then donโt have to pay those costs, and furthermore, they are contributing to protecting the environment.โ
Footprint sees increasing demand from the market
Although the European branch is not yet fully operational, Bakx is convinced that they are right on time for companies that want to make the switch. Plus, the headquarters in America has been running at full capacity since 2014. โWe see an increasing, very widespread demand around the world. Our factory in Poland is to a large extent already sold out. In addition, we are working on several follow-up projects to be able to meet the increasing demand from the market even more effectively. Companies are not only working on their own sustainable development goals, but are now also having to deal with stricter regulations. So yes, the sense of urgency is considerable.โ
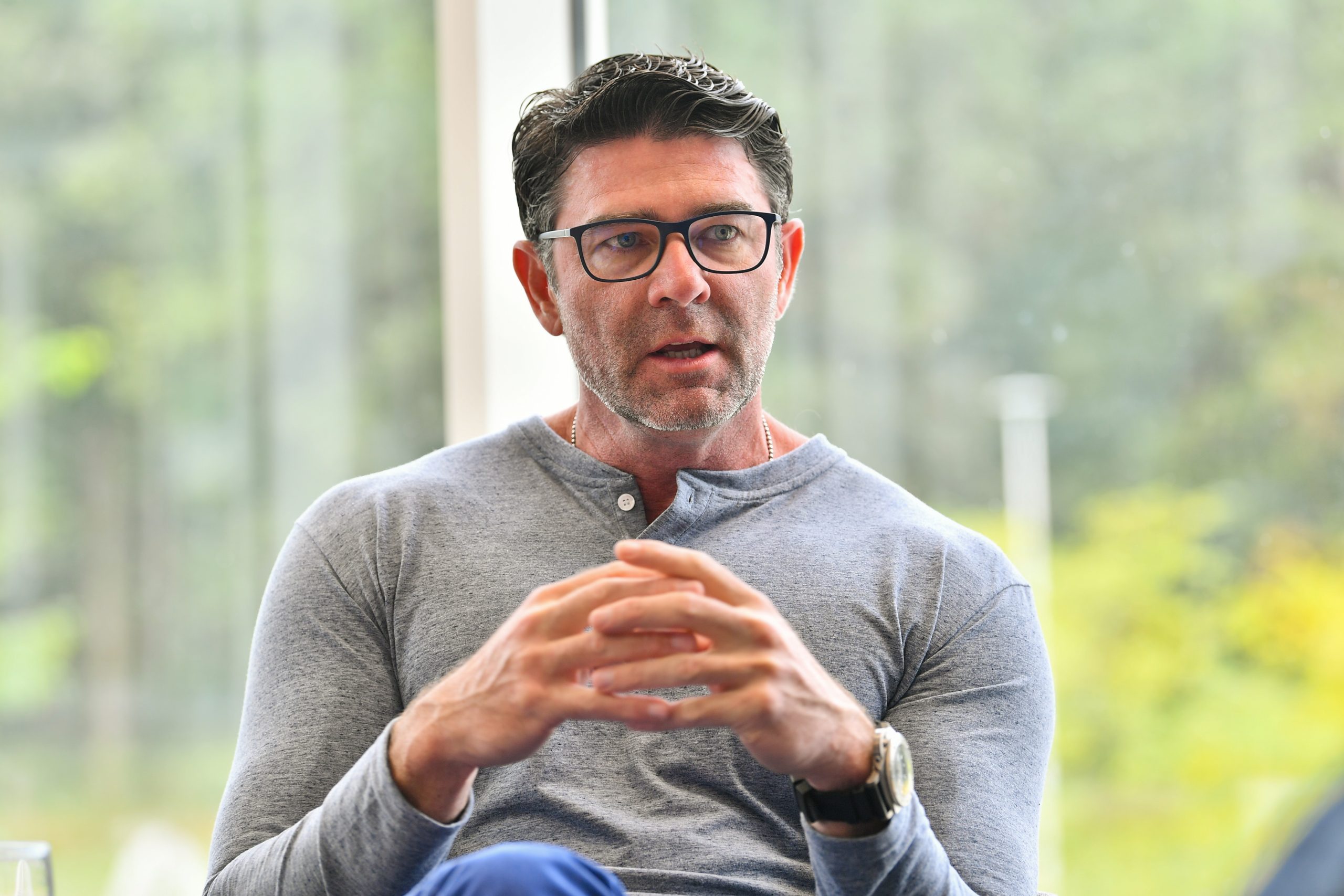