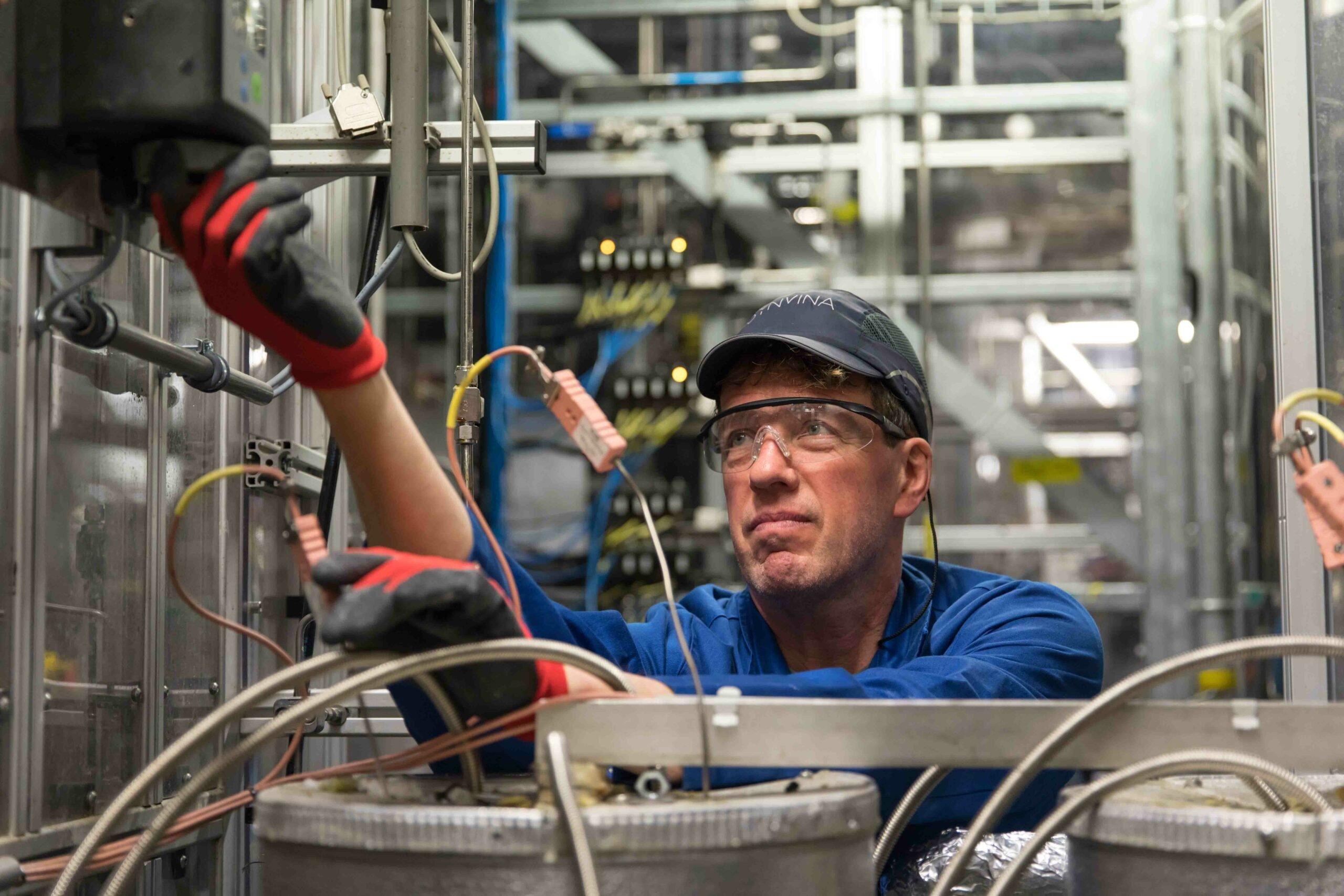
On 9 December last year, the tech company Avantium announced to the world that a positive decision had been reached regarding the construction of the world’s first commercial plant for the production of 5 kilotonnes of FDCA (furanic acid) per year, raw material for PEF (polyethylene furanoate). PEF is 100% plant-based and recyclable. The financing was arranged, in spite of a one-year delay. This was possible thanks to pledges by Invest-NL (a loan of €30 million) and loans from the four major banks ABN Amro, ASN Bank, ING, and Rabobank. Altogether good for another €60 million. Contracts have also been signed with clients including the Dutch company Refresco, bottler of soft drinks, and the Belgian company Resilux, supplier of rigid plastic packaging.
Tom van Aken, are you pleased?
“Yes – absolutely! The decision to start building our plant after a journey with so many ups and downs is enormously satisfying. People often think that the quality of plant-based plastics is inferior. But that is not the case with PEF at all. The advent of the factory is not only a culmination of the hard work of the past 15 years, of all the blood, sweat, and tears of our employees. But it is also important for our clients, who placed their trust in us; and also for new clients. And last but not least, it is good news for our shareholders and investors, who have put money into our company.
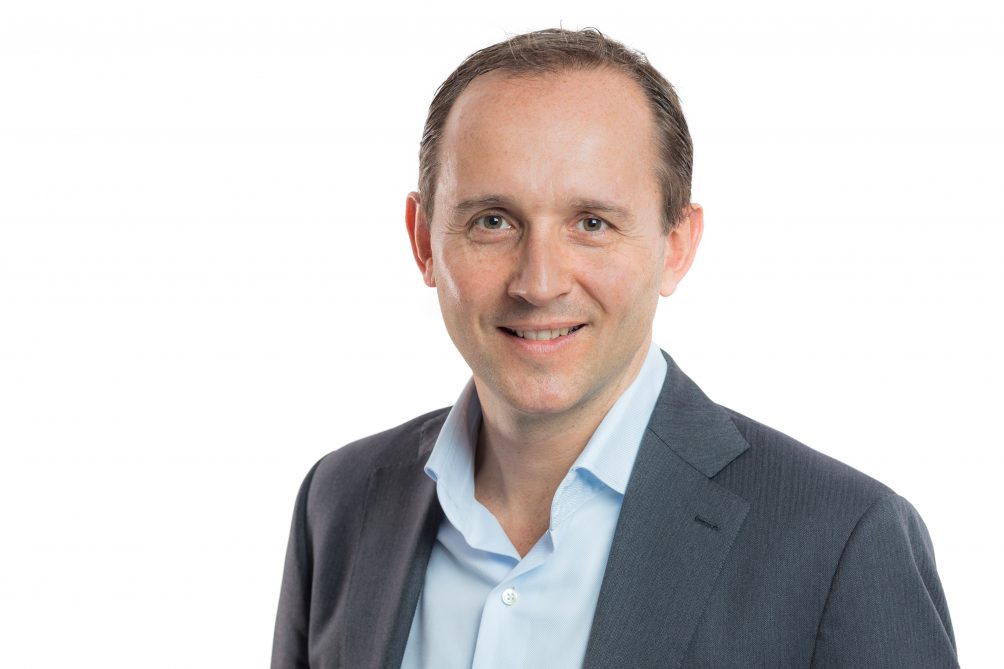
This “green light” for building a plant for PEF is definitely a historic milestone in the history of plastics. Do you know when the last time was that a new plastic was brought to the market? That was 20 years ago; with the manufacture of PLA (PolyLactic Acid); a biodegradable plastic made from lactic acid. You are probably familiar with it from those crinkly bags you put your vegetables in at the supermarket. PLA, however, does not have the right properties for packaging soft drinks, for example. However, PEF does.”
What made it so difficult to raise the money that was needed?
“It is more of a risk for banks to invest in disruptive, innovative technologies, such as those being developed by Avantium for the renewable and plant-based plastic PEF. After all, there hasn’t been any commercial experience with PEF yet. So such a transition takes time. The fact that our company has not been profitable in recent years has not helped, of course. That makes it all the more rewarding that we have managed to interest all kinds of parties in the realization of our factory.”
But in the end, it paid off. Is there any momentum in this respect? If you read the recent report by the WWF, for example, large companies do want to make their plastic use more sustainable, while large banks such as Rabobank have also recently expressed their intention to invest in circular manufacturing.
“It’s true. Large companies are also becoming aware that they have to join in the process of making plastics more sustainable. And that, if they wait any longer, it will only become more difficult to make the transition to plastic variants that are not only recyclable but also bio-based. However, the question they are wrestling with is how to go about it.
Moreover, public awareness of plastic pollution – not only in the ocean but also in other parts of the world – has grown considerably over the past few years. Plastic litter is a huge problem. For example, a few years ago National Geographics devoted an entire themed edition to global litter. I am a visual person: when you see all those photos combined, then you realize how bad things really are.
You can also read other IO articles on green chemistry via this link.
However, the proportion of plastics made from fossil raw materials – that is, petroleum – is also incredibly high: 98 percent. The raw materials transition, whereby we will no longer use fossil raw materials as a base and will instead manufacture materials from renewable raw materials, is lagging far behind compared to, for example, the transition to renewable energy sources. Significant steps have already been made in that regard. You are not going to change that overnight.”
So there is a market for alternatives to petroleum-based plastics?
“Yes, it also makes for a great business case. Our commitment is to have the plant ready by 2023 and operational by 2024. Apart from selling PEF from our factory in Delfzijl, we also want to sell technology licenses to companies around the world. With this kind of license, these companies can build their own larger factories for the production of FDCA and PEF. However, to do this you first need to have a commercial factory like the one we are going to set up in Delfzijl, which you can use to show the results to interested parties. With our renewable, plant-based plastic PEF, we think we can eventually appeal to an end market of US$200 billion a year. Not to mention the climate gains that can be made with PEF.”
So, how much would that amount to?
“We have independent scientific institutes calculate how much CO2 can be avoided with renewable and biobased plastics. The first analyses show that with the production of PEF, more than a 50% reduction in CO2 can be achieved. This is also what Avantium is striving for with its innovative technologies. We source raw material for bioplastics from plant-based sugars, from crops such as wheat, corn, and sugar beets. We do that for PEF but also for our other technologies.”
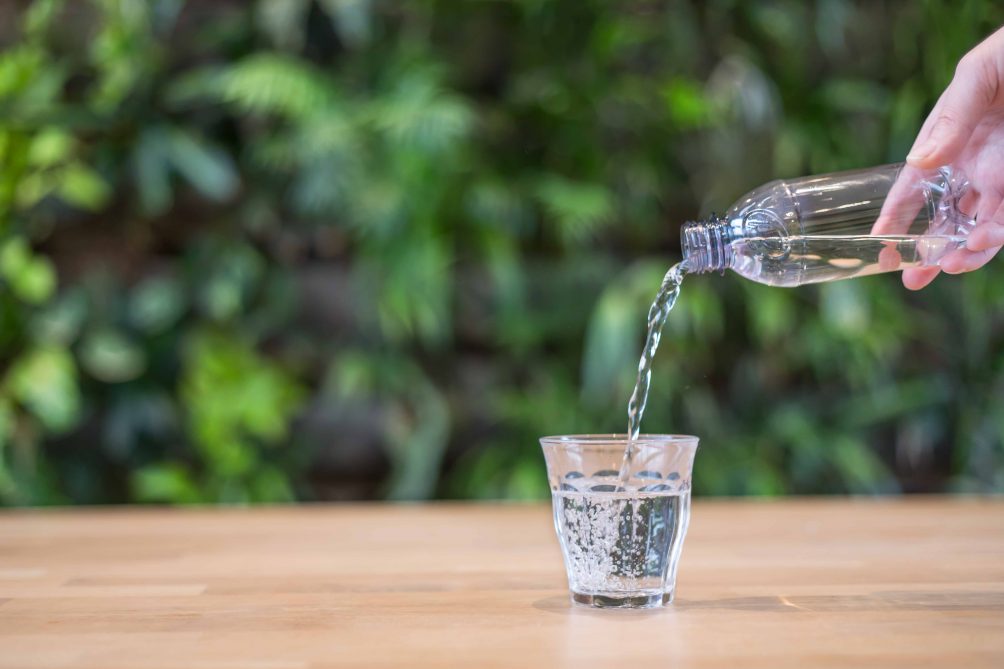
“By using Ray Technology, sugars from sugar beets, for instance, are converted by catalysis into plant-based mono-ethylene glycols: plantMEG. This is an essential ingredient for the production of polyesters that are used widely in textiles and packaging. The other technology is called Dawn Technology. This converts non-edible biomass, such as wood chips, into sugars and lignin, which can serve as raw materials for the chemical and plastics industries. For example, did you know that wood scraps have a sugar content of about 60 to 70%?”
This brings us to a thorny issue: edible crops versus non-edible crops.
“That’s right. But it’s also a matter of: you have got to start somewhere. And especially in the beginning, the production of PEF will not have any impact on the world food market. That’s why we’re also developing our Dawn Technology for converting non-edible raw materials into sugars. The transition from plastic to non-fossil raw materials is a massive and complex transition. That is exactly why we are able to tackle it as a scale-up. Such disruptive technological innovations are often not feasible for large companies. They are usually not agile enough for that kind of thing.”
You have been the director of Avantium since 2005, you were 35 when you were appointed. Back then, you already thought that Avantium – originally a Shell spin-off – should focus on innovative technologies for the production of bioplastics. Where did you pick up that idea?
“Well, it’s really not as if I had foreseen all the developments back then, or that I was at the forefront of the circular economy. At that time, we set out with Avantium to make 100% plant-based plastic from sugars. Later, in 2011, when we joined forces with Coca Cola, the idea arose to make everything 100% recyclable as well. Coca Cola was asking for that too. And later it turned out that PEF also breaks down if it accidentally ends up in nature. But when you see how enormous the plastic waste problem is, I don’t even want to talk about biodegradable plastic anymore! Because I don’t think plastic should end up in the environment at all.”
I see plastic packaging all over the place. I’m a chemist by trade. And whenever I see that, my hands start to itch: what else could we do with it?
Tom van Aken, CEO of Avantium
As Arnold Stokking recently emphasized as the chair of the ‘Green Chemistry, New Economy‘ coalition that Avantium is also a part of, plastic should no longer be considered waste, but as a raw material?
“Exactly! The fact that PEF, unlike plastics made from petroleum such as PET, degrades quickly is one more safety aspect. But recycling plastic is the answer. Both to reducing litter and reducing CO2 with respect to global warming.”
This is also the reason why last summer a refundable deposit was introduced for small PET bottles. From what I understand, PET takes about 500 years to degrade.
“It can take hundreds or even thousands of years for it to break down, depending on the type of plastic. Those 500 years, that’s just an estimate. After all, plastic hasn’t been around that long. So we have no way of measuring the exact environmental impact.”
So there is still a great deal of work to be done.
“Yes. When I walk through a supermarket, I see plastic packaging all over the place. I’m a chemist by trade. And whenever I see that my hands start to itch: what else could we do with that? I think it’s a great shame that sustainability and transitions are often just about what we will soon no longer be able to do. Whereas I think: what can we still do? What opportunities does it offer? Green chemistry has the future, I am absolutely convinced of that. I consider it a great privilege to work for a company like Avantium, surrounded by people who have the same of thinking.”
Also read: Dishwasher components made from recycled plastic