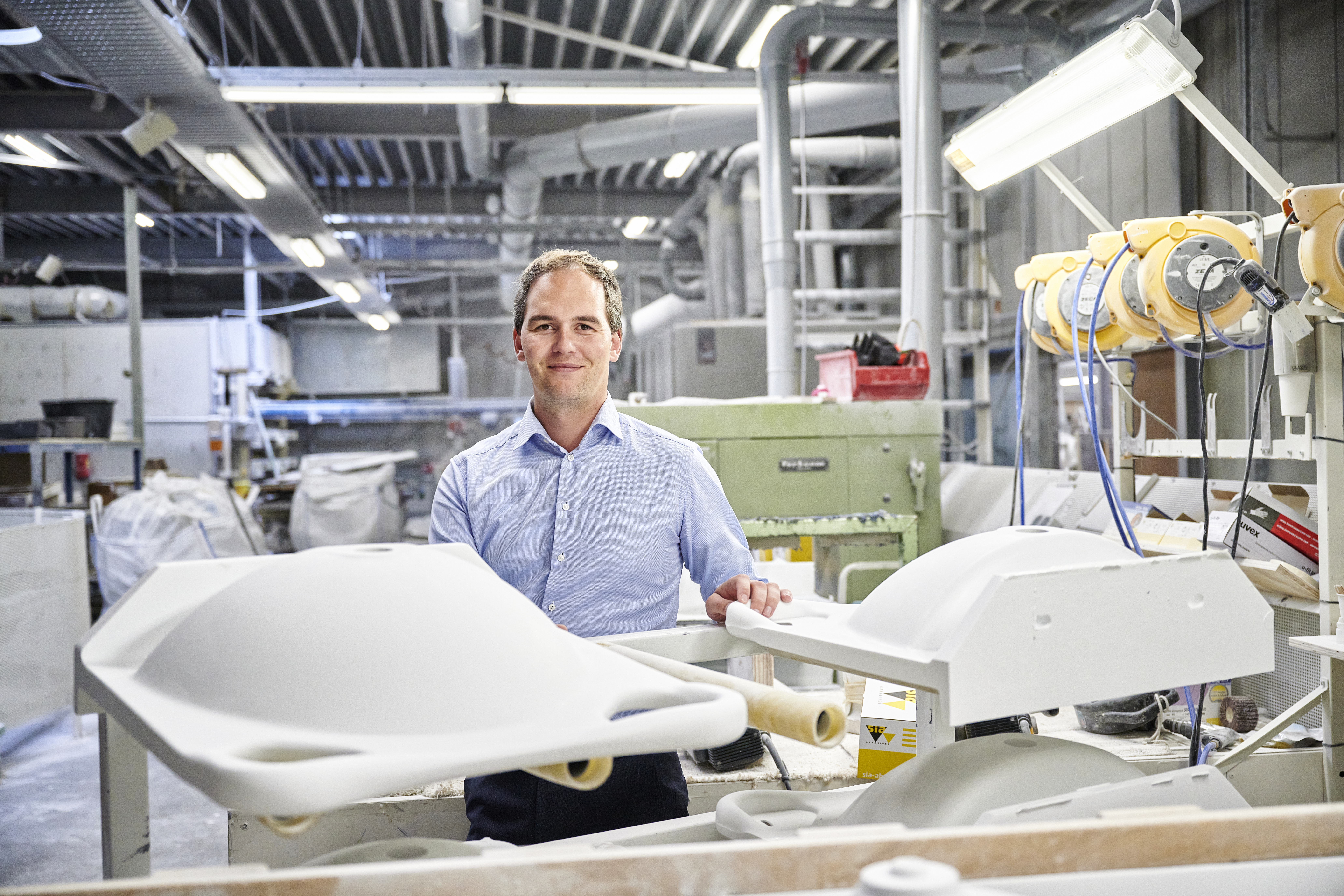
For the employees at Marlan, a Dutch company that supplies custom-made plates, molds and freestanding bathtubs, heavy, repetitive sanding work is a thing of the past. Starting next month, a cobot – a robot that works together with people – will take over several tasks from the employees. The manufacturer from the town of Leek was able to purchase the cobot partly due to support from the Province of Groningen: the Innovative and Sustainable SME Groningen subsidy scheme which innovative Groningen entrepreneurs can apply for.
This year, 11 companies have already been able to make use of the subsidy scheme, including Marlan. CEO of the company, Rik Heerema, is pleased with the arrival of the new machine. The company, which mainly makes washbasins and freestanding bathtubs, works with a product that has a stone-like appearance: a mineral (ATH) filled polyester resin, which has the advantage of being highly resistant to cleaning agents. “It’s a beautiful product but it involves a lot of manual work. It’s not appealing for employees to do sanding work all day. The new cobot takes over the boring tasks from the workers and can perform these tasks for an unlimited length of time. As a result, the employees are happier and, what’s more, productivity goes up.”
Also interesting: How are robots doing in greenhouse horticulture?
The company had already purchased a simpler version two years ago. “We used this old cobot as a kind of test subject to see what is possible. The newest one is a bigger, more advanced version of the previous one: it has a tool changer that lets you switch between tools. Plus, the cobot can work independently based on production drawings.” At the moment, there is no other comparable plastics company in Europe that works with a cobot. “It’s really quite special to be the first to make use of such an application.”
A third arm
The cobot operates on a specific piece of software (aka ‘hub’) that you can pair with various components made by different parties. By linking the cobot with different components, it can cut or sand, for instance. The hub was developed by the company Universal Robots.
The latest version of the cobot incorporates another unique feature. It can work simultaneously with workers on a finished product. “You have to think of it as a kind of third arm. The worker only needs to turn on the machine and change the sandpaper. Other than that, the two work synchronously, side by side, at the workstation.” This does not pose any problems in terms of safety. The cobot has the option to work with a laser scanner. If anything comes inside the red line, the robot shuts down automatically. In other words, it works within a virtually defined area.
“We are not using the laser scanner at the moment because the robot itself is already safe enough to work next to. Suppose we were to connect a milling machine to the cobot, then we would have an unsafe situation. In that case we would have to work with the laser scanner for safety reasons. We aren’t using that milling machine yet, but we want to do this in the future.”
Employees vs cobot
It took a while for the employees at Marlan to get used to the cobot. “Especially in the first year, I noticed that my employees saw the cobot as a threat. Some of them were even proud if the machine stopped working or made mistakes. To them, that was then proof that they were able to do the job better. It’s a kind of competitive behavior.”
Yet Marlan’s employees should not fear being completely replaced by cobots in the future. Heerema: “I don’t want to get rid of my employees at all. Cobots do not have the capacity to replace people in their entirety. People are much more flexible and can skip certain operations when necessary.” Besides, a cobot is also not faster at all. It is mainly about taking over the boring, repetitive tasks. “The cobot can work non-stop, no matter how tedious the task is. I think my employees should be happy with that in particular.”
One month wait
Within a month, Heerema expects to have the new cobot in house. It will take some time before the machine can run fully efficiently and is properly calibrated, but the wait is worth it. “I expect we will have recouped the costs for the machine within a year and a half. Eventually, we’ll be able to deliver a custom-made washbasin to customers within two weeks. That’s four times faster than what we are doing now. If we can deliver custom-made products so soon, it naturally becomes much more attractive to customers. So, partly thanks to the new cobot, we can grow quickly as a company as well.”
You can also read the other stories about Groningen via this link.