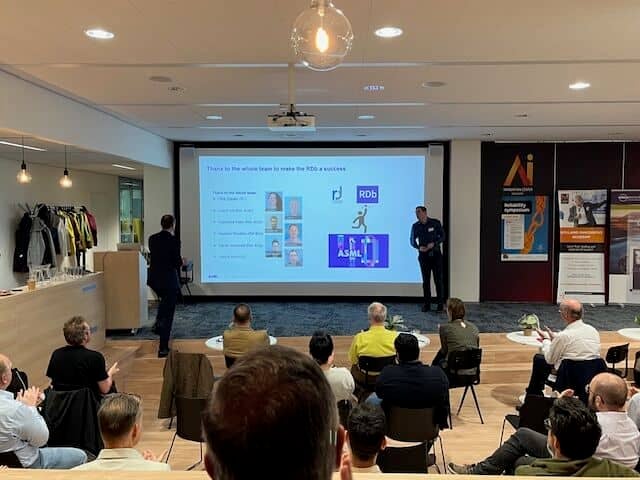
A deeply rooted drive for innovation and performance perfection is inherently present in all processes that ASML has installed within its organization. But so is its strive for reliability. In his talk at the Reliability Symposium recently hosted by Holland Innovative in Eindhoven, ASML’s Bas Dielissen shed light on the importance of reliability as a cornerstone of ASML’s ambitions. He connected the topic to the indispensable role of chips in modern technology.
Dielissen showed how ASML’s groundbreaking systems are pushing the boundaries of semiconductor manufacturing. With over 42,000 employees worldwide, ASML has evolved to a global leader in the tech industry, driven by its relentless commitment to innovation and reliability.
Reliability
Reliability is at the core of ASML’s mission. By integrating advanced reliability methods and tools into every stage of the design and manufacturing process, ASML ensures that it meets its customers expectation on high performance and reliable systems. This commitment supports the company’s growth and enables its customers to innovate and excel in a rapidly evolving technological landscape.
The importance of chips
“First of all, I cannot think of a world without chips anymore,” Dielissen began, emphasizing the ubiquity of chips in various technological applications. From artificial intelligence (AI) to energy transition and healthcare, chips are integral to solving some of the world’s most pressing challenges. The high demand for advanced computing capabilities underscores the critical need for reliable and efficient semiconductor technology.
Complexity and reliability of ASML’s systems
ASML’s systems are renowned for their complexity and precision. For instance, developing the latest EUV systems took over 20 years. These systems utilize tiny tin particles and a powerful CO₂ laser to generate EUV light, which is crucial for creating the fine patterns required in modern chips. Given the high stakes, the reliability of these systems is paramount. Dielissen explained that any failure, even of a single component among the system’s 100,000 parts, can lead to significant downtime and financial losses.
Minimizing downtime
To maintain the reliability of its systems, ASML employs a robust reliability department with around 200 engineers. This team is involved in every design process stage, ensuring reliability is built into each component and system. Dielissen introduced a comprehensive approach that integrates reliability considerations into the entire lifecycle of ASML’s products.
A critical tool in ASML’s reliability arsenal is the Reliability Database (RDB), which monitors the performance of parts and systems over time. This database has evolved from a list of numbers to an interactive dashboard accessible to all ASML engineers. The dashboard provides detailed insights into part performance, helping engineers quickly identify and address reliability issues.
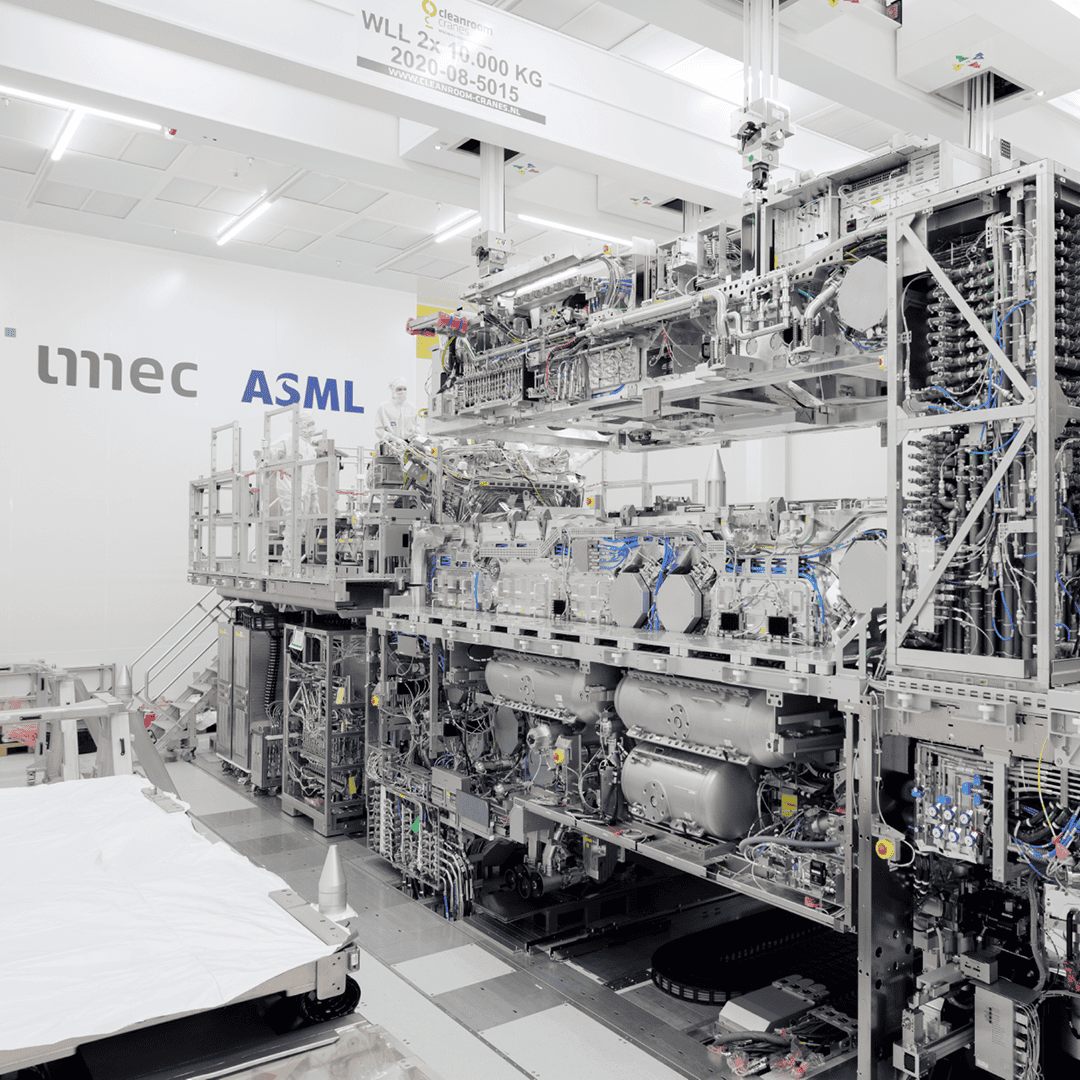
Innovative tools
Dielissen showcased several advanced tools used by ASML to analyze and improve system reliability. The “Lifeline plot”, for example, visually represents system performance over time, highlighting failure patterns and guiding engineers in their root cause analysis. Control charts further enhance ASML’s ability to monitor part performance and identify trends that could indicate emerging reliability issues.
Balancing reliability and cost
In addition to technical analysis, ASML also considers the economic impact of reliability improvements. By combining data on part usage rates, costs, and CO₂ impact, ASML prioritizes efforts to address the most critical issues. This holistic approach ensures that resources are allocated efficiently, maximizing the reliability of ASML’s systems while minimizing the total cost of ownership for customers.