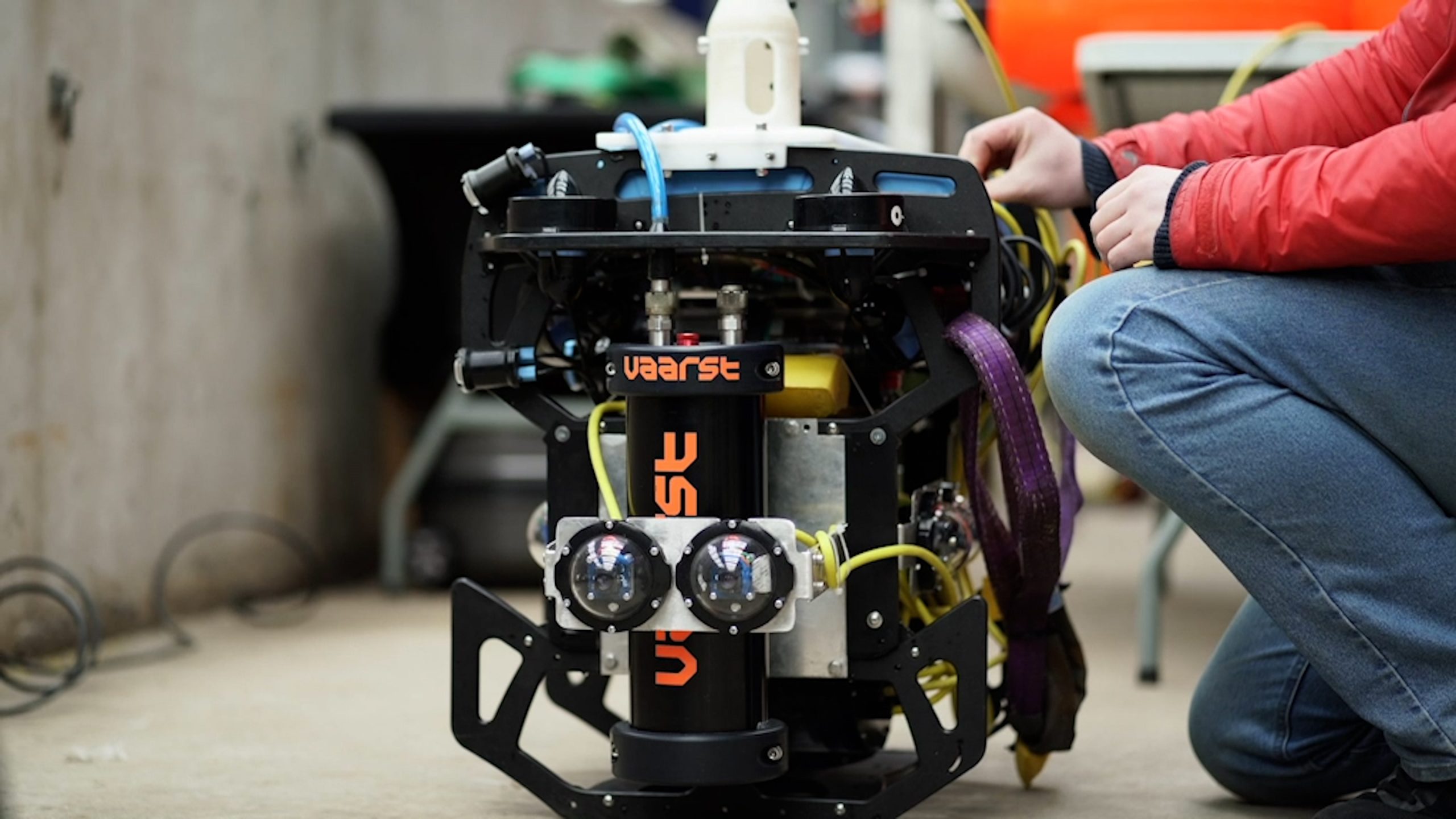
Cleaning up hazardous environments, such as underwater nuclear plants, can be a dangerous activity for the people involved. A project led by Rovco is providing a new way to take that work away from direct human contact with the development of an autonomous submarine robot.
The robot, known as Autonomous Aquatic Inspection and Intervention (A2I2), was showcased for its capabilities in hazardous environments in a live demonstration this week.
The A2I2 is a joint R&D project that also involves Forth Engineering, D-RisQ, the National Oceanography Centre (NOC), Thales UK and The University of Manchester.
One of the main purposes of the A2I2 is to remove direct human involvement in cleaning of nuclear waste in spent fuel ponds used for holding fuel assemblies that have been removed from nuclear reactors. It was therefore tested in Forthโs Deep Recovery Facility in Cumbria โ a 1.2 million litre tank of water โ to demonstrate the different technology that can assist in underwater nuclear decommissioning projects.
Remote control and sonar equipped
The top priority of this project is to remove direct human contact from dangerous environments. To that end, the A2I2 is able to be controlled remotely and is outfitted with sonar sensors to avoid collision with hazardous materials.
โIt means that you donโt have to have a prior knowledge of the environment,โ says Joe Tidball, Innovations Manager at Rovco. โThis is fantastic in a decommissioning sense when you donโt necessarily know what is down there in the water.โ
Machine Learning and 3D Imaging
Using a system known as SubSlam, the A2I2 is able to live-stream 3D images of matter within a spent fuel pond which enable onshore pilots to make quick decisions on what to do with the substances. This is especially useful in situations where the, often, nuclear materials are in danger of colliding with one another. Using a Last Response Engine (LRE), the A2I2 can intervene in these cases.
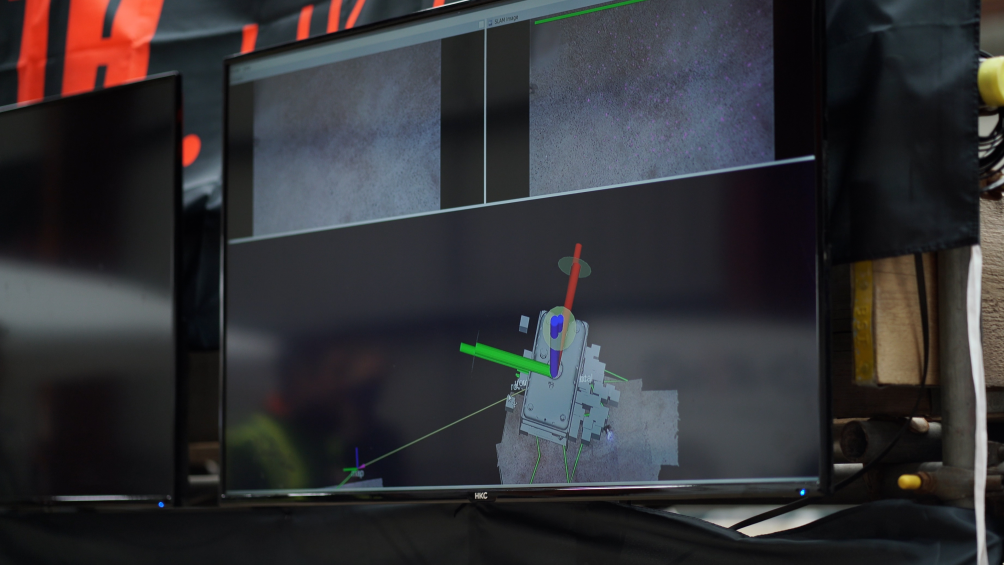
It can also take a survey of all potentially hazardous materials prior to decommissioning and compare it to a subsequent survey to ensure that the materials have all been removed. It does this autonomously with machine learning (ML) which help to remove human error in the surveying.
Autonomous decisions and wireless capabilities
D-RisQ has developed software for the A2I2 that help with its autonomous decision making. These act as both a support and safeguard to human control and are being further developed for more accurate autonomous decision making by the robot.
โWeโve demonstrated that we can alter the capability of the last response engine,โ says Nick Tudor, CEO of D-RisQ. โWeโve shown that we can be flexible in changing the way in which that behaves very quickly and be able to take in new sensors and new information and make a proper sound decision on that.โ
Currently, the A2I2 is tethered to a floating system aptly named Lilypad, which acts as its launch and charge point, as well as communications conduit. However, the University of Manchester are developing wireless underwater communications which will eliminate the need for a tether and allow the A2I2 to roam more freely.
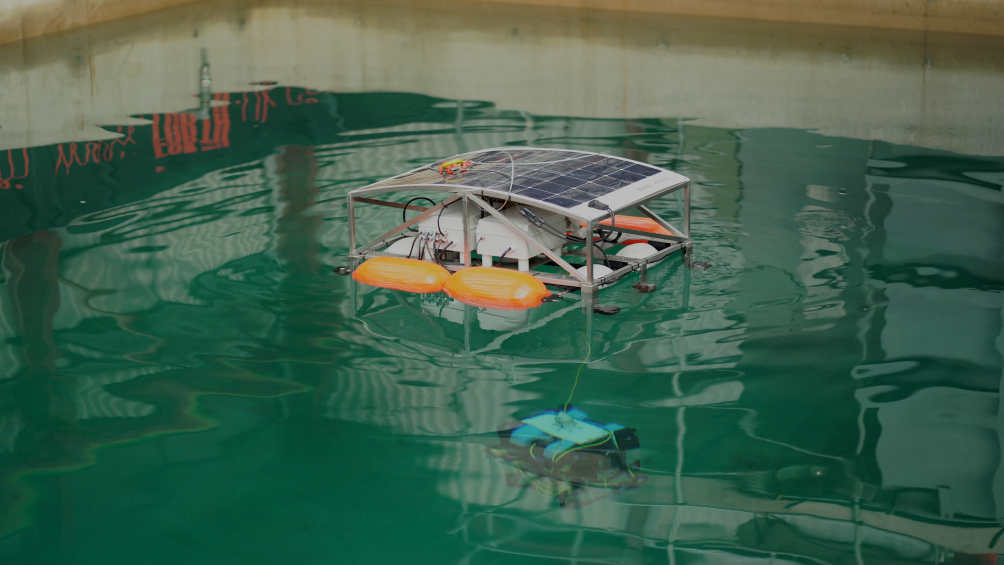
The next step is for a demonstration in a real spent fuel pod and the target is in one at the Sellafield nuclear site.
โWe see that happening within the next couple of months,โ says Tudor.
Read about another autonomous robot that kills weeds with laser vision