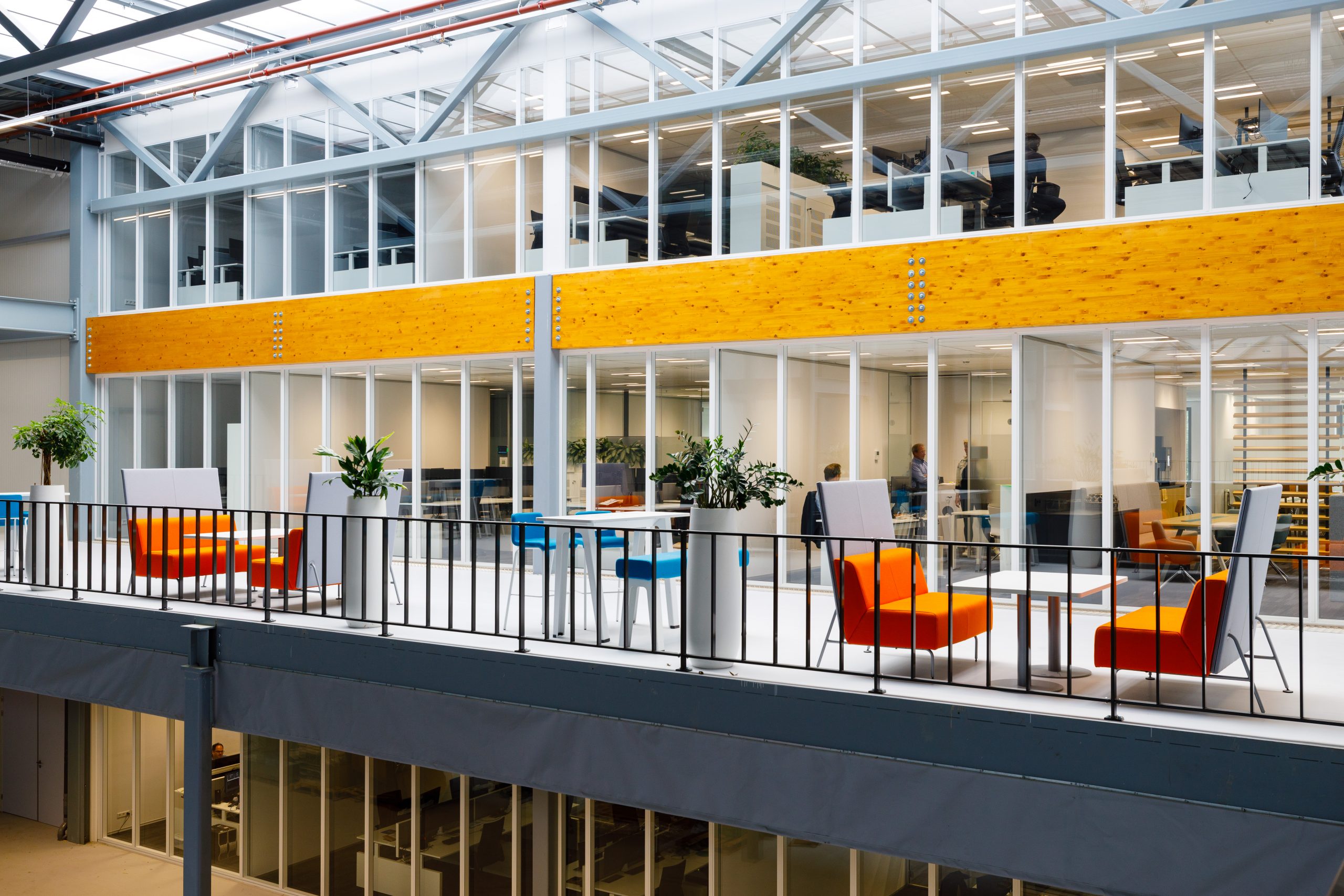
Robots that provide a specific part at the right time, AR glasses that support complex assembly needs, or near-automatic assembly lines where man and robot work together. These are just a few examples of developments within the field lab Flexible Manufacturing at the Brainport Industries Campus (BIC) in Eindhoven.
In the four hundred square metres of space on the campus, companies, educational and knowledge institutions work, for example, on self-learning assembly lines that can assemble complex products almost automatically. Or demonstrate innovations that are ready for the market. This autumn, Total Productivity, a company that helps other companies improve their productivity, will integrate in the fieldlab a software package in collaboration with TNO. A ‘Visual Factory’ supports operators with digital and interactive work instructions that can be customized according to the customer’s wishes.
But according to Peter-Jan Zwart, one of the founders and financial director of Total Productivity, the differentiating part of this software package lies elsewhere. “The special thing is that the software can be linked to ERP systems – where, among other things, orders come in. This allows the work instruction to be adapted to each different order. So you go from generic instructions to specific instructions. This makes flexible production possible.”
Quality of production
As well as giving work instructions to operators, the system also monitors the quality of the entire production process. “This is based on the LEAN idea of producing more efficiently and more cheaply. So the system not only has an instructive function. But also makes sure, for example, that as little material as possible is lost,” says Zwart.
Here more about the software package
In the incubator at BIC, companies work together with knowledge and educational institutions on innovations that help the Dutch manufacturing industry. The lab is part of the innovation program ‘Factory of the Future’ where eight overlapping projects are working on robotization, automation, and more efficient production processes. It is part of the nationwide network Smart Industry, with almost 40 field labs throughout the country.
TNO is engaged within Flexible Manufacturing to develop and demonstrate operator supporting technology, such as robot collaboration or projection techniques to teach employees in a faster way. TNO is supported by Interreg project FOKUS. Knowledge institutes like Sirris, Flanders Make, KU Leuven, and Open Manufacturing Campus are also involved. From the industry, FME, Agoria, HighTech NL, and Brainport Industries are connected.
By combining knowledge and infrastructure, both FOKUS and the field lab try to stimulate companies to come up with solutions for flexible production.