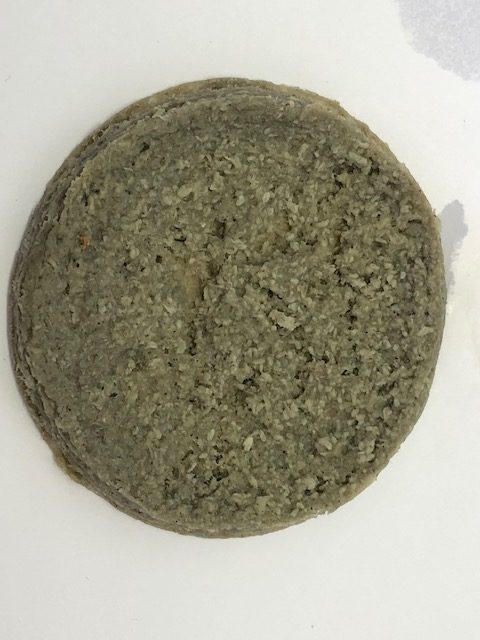
Kill two birds with one stone – to use a popular saying. That’s how the Rotterdam-based company Asbeter solves two problems at the same time. By tackling asbestos with the help of industrial waste acids. The asbestos is safely disposed of at an affordable price and in a circular fashion. And industrial waste streams used for this purpose cut down on CO2 emissions.
CEO Inez Postema outlines the remarkable process of the start-up that is about to break through with the world’s very first factory in this field.
How did the idea for Asbeter first come about?
Actually when we first met at a congress, my partner Pol Knops and I were not working on asbestos but on the use of CO2 as a raw material. Pol mentioned that asbestos also reacts with CO2. We looked into what was feasible. This turned out to be theoretically possible, but not in practice. That’s a shame, but then what was actually possible? Acids seemed to be more effective, but were an expensive solution. Then I asked: What if we use waste acids? That’s what started it all.
What does Asbeter do exactly?
In the process known in English as Asbetter Acids, asbestos inside a containment (a fully shielded space) is broken into small pieces under vacuum pressure in order to facilitate processing. This is done with specialized equipment. We use acids to separate the asbestos from the cement in, for example, roof panels or drinking water pipes.
Cement turns the acid alkaline. And the asbestos fibre changes its structure so that it eventually is no longer a fibre. You retain 20% of the cement in the form of silica powder. This can be used in construction. Asbetter Acids also makes CO2-free gypsum during one of its circular process steps. Normally, waste acid is neutralized and dumped, which releases considerably more CO2.
There are still a million tons of asbestos roof panels and thousands of kilometers of drinking water pipes containing asbestos in The Netherlands. So, plenty of work.
What distinguishes this company from other companies?
We are the only ones that break down asbestos. At present, asbestos is merely collected and dumped. But we don’t dump it. Since we remain within the range when it comes to waste disposal costs, from now on the government can require that asbestos is not dumped but offered to waste processors that incorporate the Asbetter Acids process. As this guarantees the complete and safe destruction of asbestos.

How has the response been so far?
People mainly wonder why someone hasn’t come up with the idea of processing asbestos with waste acids earlier so that you can solve two environmental problems. We are the first company to try it this way.
Up until now, what has been the biggest challenge?
Often I’ve wondered what we’ve gotten ourselves into. For example, when a particular technique or piece of equipment isn’t working the way it should work. It’s sometimes difficult to gauge because we don’t have a reference. Nobody else processes asbestos the way we do. You run into delays, while the costs mount up and we don’t have any revenue as yet. Fortunately, we do have partners like the Province of South Holland, the Municipality of Rotterdam or the Ministry of Economic Affairs.
Have there been any high points so far?
Winning the Rabo Duurzame Innovatieprijs 2019 (Rabo Sustainable Innovation Award) in the Circular Economy category was fantastic. Especially with former top executive Herman Wijffels who thinks our idea is brilliant because it solves two problems. Processing asbestos, which yields another 30% in renewable raw materials as well. And that with the help of waste acids that normally account for substantial CO2 emissions from conventional discharges at present.
The demonstration plant, which will be ready in about a year and a half’s time, is of course another high point. On an annual basis, it can process 35,000 tons of asbestos cement and 165,000 tons of waste acids. €35 million is invested in that factory.
What’s in store in the near future?
Construction of the first factory for our process is in full swing. If you think about things like securing permits and construction, it’s a lot of work. You have to think ahead two years in advance. We will continue to test other equipment in the pilot plant and conduct more research in order to optimize production. It’s a process that doesn’t exist yet, where we have to find out for ourselves which equipment will best do the job.
Where will Asbeter be in five years’ time?
By then, there will be several factories in Europe using our technology. Already there are international parties that are interested in us.