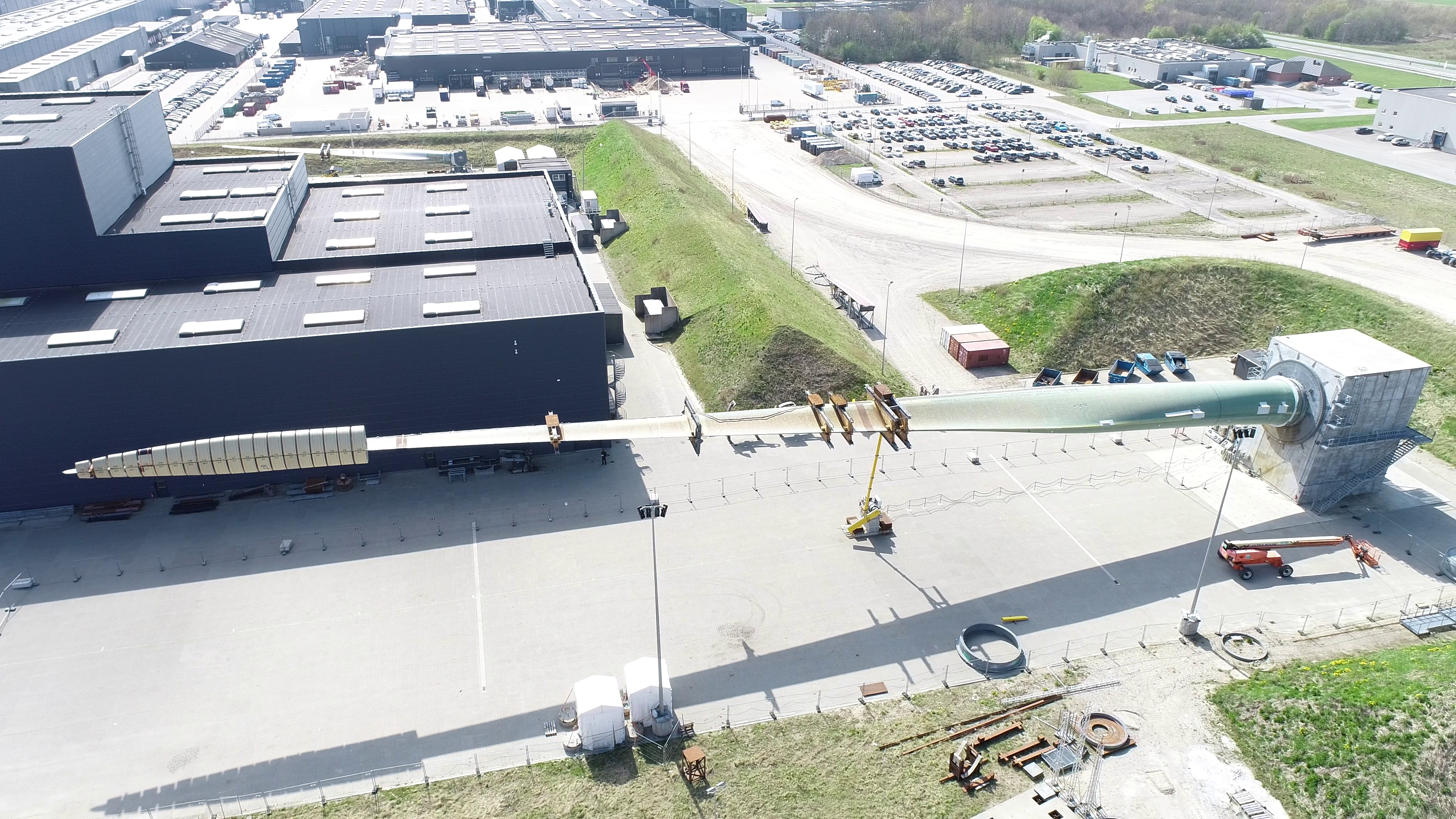
De landen van Noord-Europa hebben niet dezelfde hoeveelheid zon als de landen aan de Middellandse Zee, maar wind is er altijd genoeg. Offshore-windmolenparken zijn daardoor van cruciaal belang om hun aandeel van hernieuwbare energiebronnen te vergroten. Duitsland, België, Denemarken en Nederland hebben zich er onlangs toe verbonden een windmolenpark van 150 GW te bouwen in de Noordzee. Onderzoek gaat door en op de oevers van die zee worden de turbines van morgen ontworpen.
Enkele van de grootste windbladen ter wereld worden geproduceerd en getest in Aalborg, Denemarken. Geslagen door de wind en gestresst door barre wintertemperaturen ontwerpt Siemens Gamesa de offshore krachtcentrales van morgen.
Ingenieurs zijn voortdurend bezig met het perfectioneren van wieken om ze zo efficiënt mogelijk te maken. Tegelijk streven ze ernaar de hoeveelheid energie die ze kunnen opwekken, te vergroten. Op een van de testplatforms in Aalborg staat een 108 meter lang windblad, dat inmiddels alle geplande tests heeft doorstaan. Er is ook een exemplaar van 115 meter onderweg.
Een paar meter meer lijkt misschien niet zo’n groot verschil, maar het maakt wel degelijk veel uit. “Elke keer dat we een nieuw offshore blad testen, is dat een vrij grote stap voorwaarts. Slechts een paar meter meer maken het verschil in de belasting die het blad moet doorstaan. In dit geval zal de belasting met ongeveer 12 procent toenemen,” zegt Flemming Grün-Møller, testingenieur bij Siemens Gamesa.
Hoe langer het blad, hoe hoger de belasting die het moet weerstaan. Er komen heel wat tests, berekeningen en proeven kijken bij het maken van zulke lange wieken en bij het beheersen van de krachten die ze opwekken. Wat is er nodig om een windblad van meer dan honderd meter lang te ontwikkelen en te bouwen?
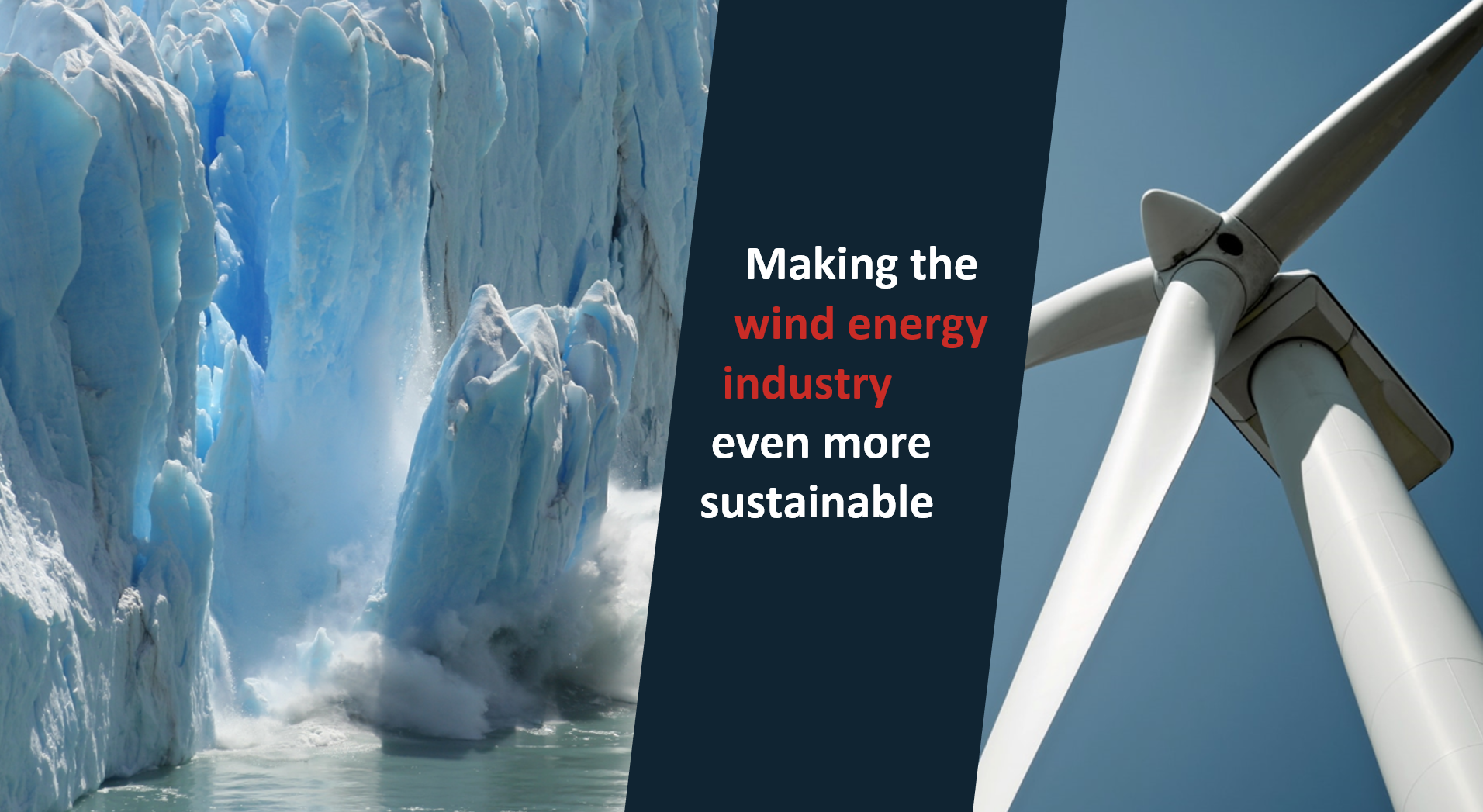
Stabiele en wintervaste infrastructuur
Ten eerste moet er een stabiele infrastructuur zijn om de impulsen die door meer dan honderd meter lange oscillerende wieken worden opgewekt, onder controle te houden. Stevige testopstellingen, met op de grond gestorte betonblokken, dienen als solide werkblad. “Daarmee is het eenvoudig om verschillende wieken te plaatsen en te verwijderen. Omdat we steeds grotere bladen ontwikkelen, wordt er op onze locatie een nieuwe testopstelling gebouwd, met staal om het betonblok te versterken”, legt Grün-Møller uit.
De testlocatie van Aalborg telt acht opstellingen. Sommige daarvan staan binnen, andere buiten het terrein. Bladen buiten testen betekent dat ze de barre omstandigheden van de Deense winters moeten doorstaan. Volgens de ingenieur is dat niet noodzakelijk een slechte zaak.
Grün-Møller: “Onze klanten vragen ons naar onze test en we kunnen zeggen dat de wieken ook onder zware weersomstandigheden buiten blijven – bij harde wind of bij -10° C. Ik vind dat een waardevol aspect. Het betekent dat de turbines niet alleen in mooie weersomstandigheden werken, maar dat ze ook meer uitdagende weersomstandigheden kunnen doorstaan.”
Voorbereiding op de tests
Voordat een nieuw blad bij de testopstelling arriveert, moeten er verschillende passages worden doorlopen. “Het begint allemaal met het ontwerpen en voorbereiden van alle onderdelen die we tijdens de tests nodig hebben. Vervolgens worden op maat gemaakte klemmen – om het blad te bewegen en te trekken – geïnstalleerd, evenals alle sensoren voor de metingen,” legt Grün-Møller uit.
Al deze stappen nemen maanden in beslag en zijn het resultaat van de coördinatie tussen tientallen ingenieurs en arbeiders – zowel in de testfaciliteit als in het productiecentrum. Ook de wiekenfabriek van Siemens Gamesa staat in Aalborg en maakt het – ondanks de tijd die met de ontwikkeling van een blad gemoeid is – gemakkelijker om alle noodzakelijke activiteiten te plannen.
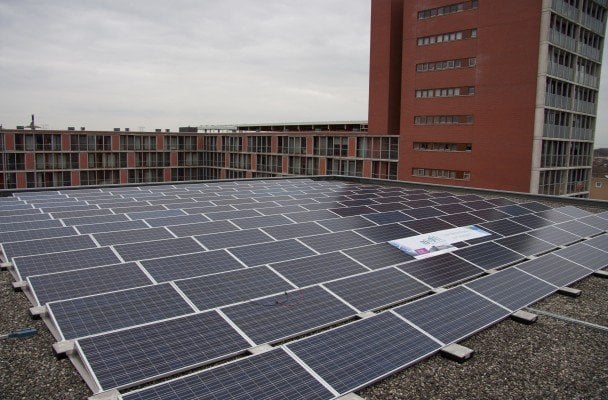
Trekken, duwen en verdraaien van wieken
Er worden statische en dynamische tests uitgevoerd op een blad. Met de eerstgenoemde testen bewijzen de ingenieurs de volledige integriteit van de bladstructuur in zware windsituaties. “De afdeling bladontwerp levert ons de doelstellingen voor de vermoeiingsbelasting, na de simulaties die zij uitvoeren met een computermodel. Wat wij doen is die berekeningen herhalen in de praktijk, om te proberen de doelstellingen te halen die de simulatie eerder heeft vastgesteld,” illustreert Grün-Møller.
Tijdens de statische test wordt de belasting in alle vier de richtingen uitgeoefend. Daarna vindt een vermoeiingstest plaats. Hierbij wordt de volledige levensduurschade gesimuleerd. Een machine, exciter genaamd, oefent krachten uit die het blad in vlakke richtingen doen bewegen. Een aanvullende statische test controleert de constructie na de gesimuleerde levensduur van 25 jaar.
“Torsiestijfheid en buigeigenschappen worden gemeten in kleine tests, die de analyse van het bliksembeveiligingssysteem omvatten,” voegt Grün-Møller toe. Alle procedures voldoen aan de internationale normen voor wieken. Het kan tot 12 maanden duren om ze allemaal uit te voeren.
Grotere wieken worden de nieuwe norm
De ontwikkeling van de 108 meter lange schoep gaat door, inmiddels zijn meer dan de helft van de cycli die nodig zijn om te testen, voltooid. Volgens de ingenieur zijn de fouten in het proces eerder leermomenten dan hindernissen.
“Het is onderdeel van het proces en helpt ons de kwaliteit te verbeteren. Bij de volgende test, waar ik aan ga werken, hoop ik niet op dezelfde problemen te stuiten als bij de vorige. We hebben veel geleerd van de tests in het verleden en bij Siemens Gamesa testen we de wieken verder dan de goedkeuring van buitenaf van ons eist. Het loont in termen van de waarde van het product,” benadrukt Grün-Møller.
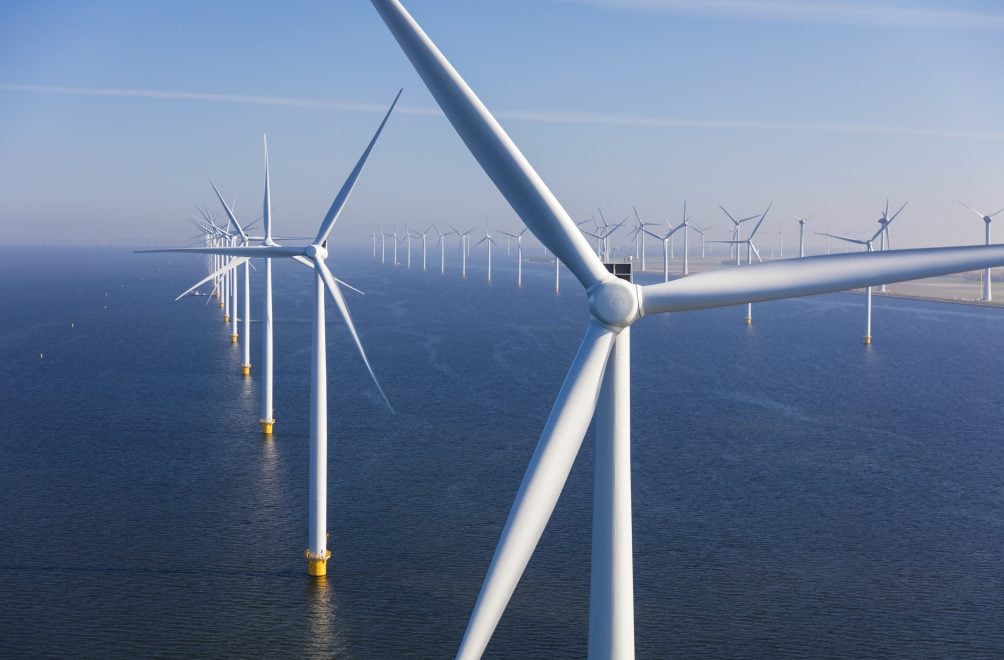
Er zullen dus grotere bladen en turbines in zee worden geïnstalleerd. “Veel mensen dachten dat we niet verder konden gaan. Tegenwoordig zijn de windturbines drie tot vier keer zo groot als 10 jaar geleden. Soms denk ik dat we ons te snel ontwikkelen, maar we boeken nog steeds successen, ook al zou het misschien verstandig zijn om ons meer op massaproductie te richten.”