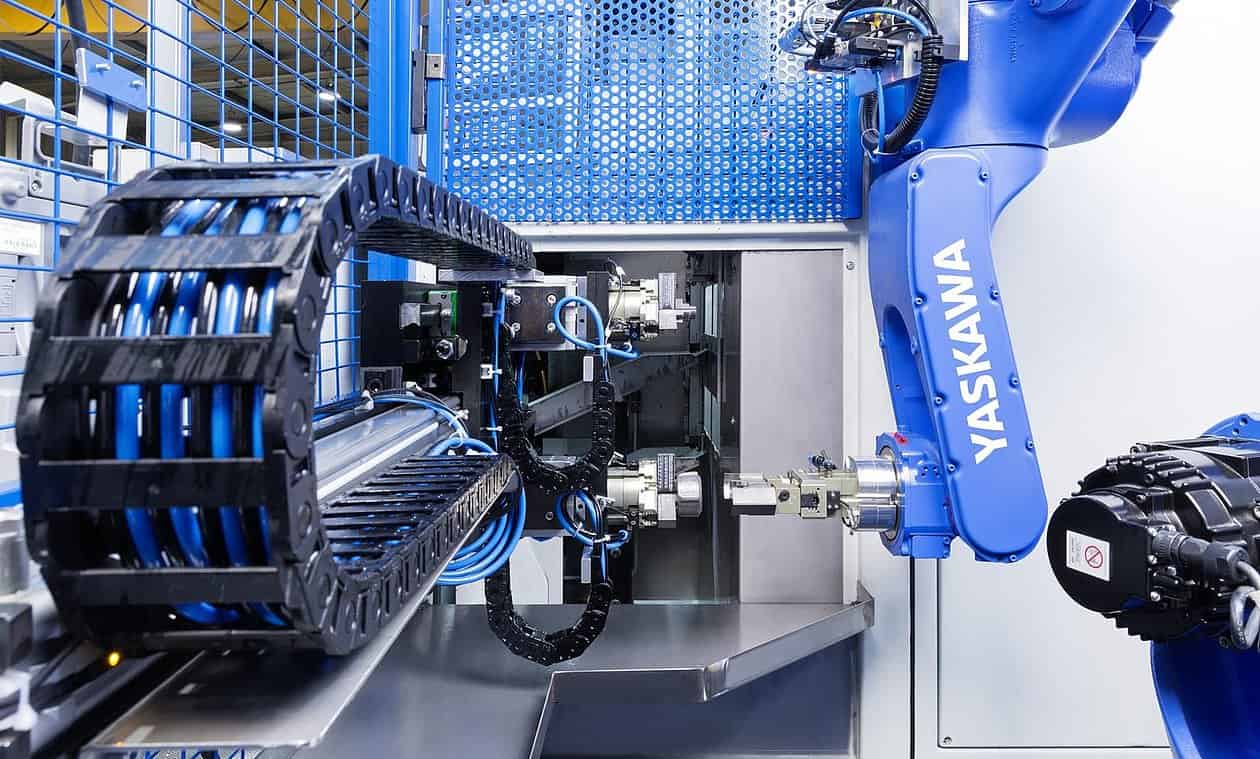
We staan er niet bij stil. Maar er komt wel wat bij kijken om deuren automatisch te laten opengaan. De meer dan 600 medewerkers van BEA Sensors doen dat gelukkig wel. En hoe. Het bedrijf met hoofdkwartier in Angleur (vlakbij Luik) mag zich pionier noemen in deze nichemarkt en blijft voortdurend inzetten op innovatie. Om de onberispelijke kwaliteit van zijn producten nog beter te garanderen, investeerde BEA onlangs in een nieuwe testopstelling. Het hart van deze cel is de Yaskawa HC20DTP cobot. “Hij gaf ons de flexibiliteit die we zochten”, vat Industrialization manager Sébastien Simonis samen.
Bij de oprichting van BEA, bureau d’electronique appliqué, in ’65 liet niks nog vermoeden tot wat voor wereldspeler het zou uitgroeien. “Toen lag de focus nog op algemene elektronica, maar het management voelde aan zijn theewater hoe detectie steeds belangrijker werd. Al in ’72 werd de eerste sensor voor beveiliging ontwikkeld, een wereldprimeur en het pad waarop we steeds verder gegaan zijn”, legt Sébastien uit. Sindsdien bouwt BEA aan een volledige lijn voor toegangscontrole, en veiligheids- en beveiligingssystemen voor de industrie, de beveiligingssector en transport. Tot op vandaag is innovatie het handelsmerk van het bedrijf. En hoewel BEA intussen wereldwijd actief is met productiesites in Pittsburgh en Peking, gebeurt het gros van de R&D nog steeds vanuit Angleur. “Ons hart ligt hier. Dat klinkt misschien niet als iets wat je van een technologiespeler mag verwachten, maar het zijn echt de mensen die het bedrijf maken”, aldus Sébastien.
Innovatie hand in hand met kwaliteit
Het heeft BEA een reputatie opgeleverd van pionier. Een reputatie die het met elke innovatie ook weer bevestigt. Een mooi voorbeeld daarvan is de ORASCAN die onlangs zijn vuurdoop kreeg op de BAU beurs. Sébastien: “Om een schuifdeur vlot, veilig en betrouwbaar te laten werken, had je drie aparte sensoren nodig, vaak een combinatie van infrarood- en radartechnologie. Met de introductie van de ORASCAN kan je voortaan de volledige deur controleren met één enkel apparaat. We zijn er immers in geslaagd om de lasertechnologie nog een pak nauwkeuriger te maken en te integreren met radartechniek.” Dat deze innovatie bijzonder hoge ogen gooide op de beurs, hoeft dus niet te verwonderen. “Van zodra de ORASCAN commercieel beschikbaar is, moet onze productie er klaar voor zijn. Maar dat geldt ook voor onze kwaliteitscontrole, want elk product wordt hier uitvoerig getest vooraleer het naar de klant vertrekt”, beklemtoont Sébastien.
Meer flexibiliteit in kalibratie en kwaliteitsinspectie
Het team Industrialization bedacht daarom een nieuwe testopstelling. Waar ze in het verleden steevast voor specifieke, op het product afgestemde, installaties kozen, wilden ze het deze keer over een andere boeg gooien en de eigen productie future proof maken. “Het idee was om te werken met een robotcel voor kalibratie en kwaliteitsinspectie, die zich flexibel kan aanpassen aan de andere vorm en afmetingen van nieuwe en bestaande producten en 24/7 autonoom kan doorwerken.” Het hart van de cel moest een zesassige cobot worden met voldoende payload om ook op dat vlak de nodige flexibiliteit in huis te halen. Een zoektocht die hen al snel naar Yaskawa op Brainport Industries Campus leidde, want met zijn Motoman HC reeks zet het wat dat betreft de standaard in de cobotmarkt. “Ze hebben de grootste”, vertelt Gilles Bauduin, technical support en designer Industrialization, met een knipoog. “Bovendien wist ik uit ervaring bij mijn vorige werkgever hoe betrouwbaar ze werken.”
Racks: standaardaansluiting, custom design
Ook voor BEA was dit nog grotendeels onontgonnen terrein, waar ze met heel het Industrialization team enthousiast de schouders onder zetten. Gilles: “De enige robot die hier al in de productie meedraait is een vierassige. Deze uitdaging was toch van een heel andere grootorde. We moesten de cel immers zodanig opbouwen dat de cobot elke grijppositie kon bereiken en op een vlotte, logische manier weer bij zijn startpunt raakte.” Gelukkig kon het team van Sébastien rekenen op heel wat ondersteuning van Yaskawa. De cobot werd al in 2020 geleverd en geïnstalleerd op zijn sokkel. “Door corona hebben we het project echter in de koelkast moeten steken. Een jaar geleden werd het weer opgepakt.” Eerst werd de rack ontworpen, gebouwd en ingepast in de cel. Samen met de cobot vormen de racks ten slotte de sleutel tot flexibiliteit. “De racks beschikken over een standaardaansluiting, zodat de cobot ze makkelijk kan grijpen. Maar daaronder kan het ontwerp aangepast worden in functie van het te testen product.” Met ruimte voor 10 sensoren per rack en 30 racks kunnen er zo 300 producten voor kwaliteitsinspectie ingeladen worden.
Eerste hulp bij programmeren
Volgend punt op de agenda: leren programmeren. “De eerste dagen kreeg ik er toch hoofdpijn van”, geeft Gilles met de glimlach toe. “De ondersteuning van Yaskawa was echter top. Ik vertelde wat ik wilde bereiken, zij toonden hoe dat op de meest efficiënte en snelste manier te realiseren was. Door hun ervaring wisten ze welke paden de cobot het beste kon volgen. Ik heb er heel veel van geleerd.” Hij kreeg overigens als enige de opleiding, maar toch kunnen ook andere leden van het team de cobot probleemloos bedienen. “Omdat hij functioneert als slave van de PLC in de TwinCAT omgeving van Beckhoff. Ze geven de opdracht welke bewegingen hij van A naar B en terug moet maken. Hoe hij die bewegingen moet uitvoeren, hebben we dan al geprogrammeerd.”
Vertrouwen getankt
Vandaag stelt het R&D-team de cobot al behoorlijk op de proef. “De ramp-up is begonnen en we hebben er alle vertrouwen in dat eenmaal de productie van onze ORASCAN onder stoom komt hij vlot zal kunnen volgen.” Ook op vlak van flexibiliteit heeft hij zich al bewezen. “Hij maakt het heel eenvoudig om het ontwerp van producten verder te finetunen en dan meteen aan de nodige kwaliteitsinspectie te onderwerpen. Zelfs als de afmetingen meer dan 10 mm verschillen, hoef ik enkel één regel in de programmatie aan te passen om de cobot betrouwbaar aan het werk te laten gaan.” Het beste bewijs van zijn kunnen is dat de cel intussen al een exacte kopie heeft gekregen en de testcapaciteit zo opgetrokken werd naar 600. Daarnaast kijken BEA en Yaskawa samen hoe ze een robot in de productie kunnen integreren om bij de productie van een andere nieuwigheid, de ARTEK sensoren, de lijm heel gecontroleerd kunnen neerleggen. “Er is met dit project een stevige basis van vertrouwen gelegd”, besluit Sébastien.