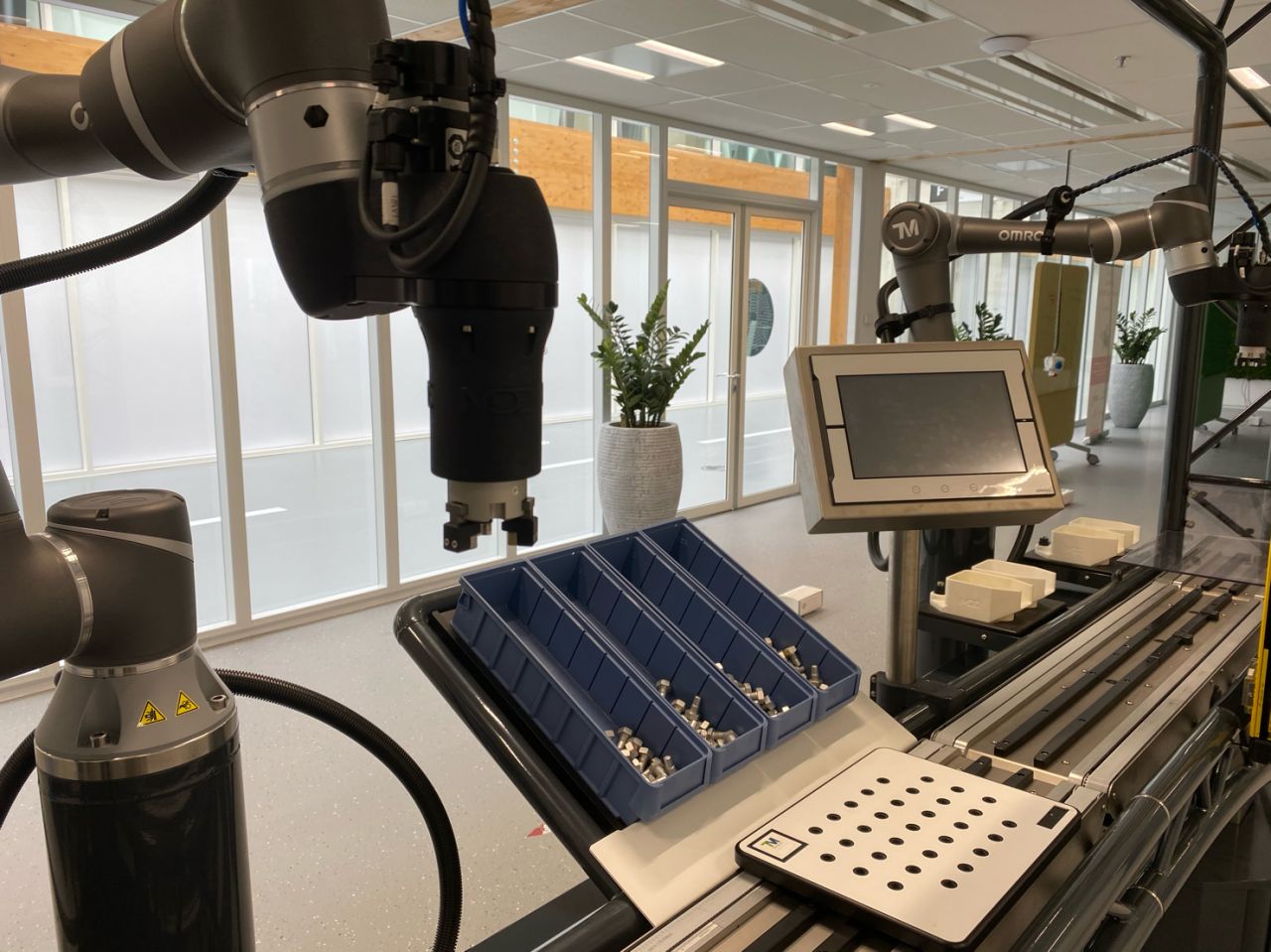
Een betere samenwerking tussen mens en machine in een fabricageproces. Dat is precies wat de zelflerende assemblagelijn van Omron – een van ‘s werelds grootste spelers op het gebied van industriële automatisering – voor elkaar probeert te krijgen. Sinds kort staat deze demo in het fieldlab Flexible Manufacturing op de Brainport Industries Campus.
Het idee is gebaseerd op de tafeltennisrobot Forpheus van het bedrijf. Deze robot leert van de bewegingen van menselijke spelers en wordt hierdoor beter in het spel. Maar in plaats van de menselijke tegenstander compleet inmaken, past de robot zijn niveau aan aan dat van de tegenstander en geeft feedback zodat de tegenstander beter wordt.
“Dit principe, het leren van experts, vertalen we nu naar een fabriek”, legt Mariya Yurchenko, data-expert bij Omron uit. “Je hebt in sommige fabrieken experts rondlopen die meer dan twintig jaar ervaring hebben. Zij weten precies welke instellingen ze in een machine aan moeten passen als bijvoorbeeld het materiaal verandert. Het is als het ware een verlengstuk van hun lichaam. Die kennis kunnen ze de machine leren zodat die zelf ‘weet’ wat de beste manier is om een product in elkaar te zetten.”
Mogelijkheden van machine learning laten zien
Volgens John Blankendaal, directeur van Brainport Industries gaat er ‘op hoog niveau’ kennis verzameld worden. “Zowel partijen die deelnemen aan het flexible manufacturing-fieldlab, als afstudeerders van de TU/e gaan hiermee aan de slag. Ook willen we met deze demo laten zien wat er allemaal mogelijk is met machine learning. Bedrijven die zich afvragen of ze dit kunnen gebruiken en wat hierin de volgende stap is, kunnen op de campus terecht”, zegt Blankendaal.
In de demo in het fieldlab bestaat het ‘product’ uit combinaties van vier verschillende kleuren schroeven. De machine analyseert de handbewegingen van operators. Op basis hiervan stelt de robot een ideale combinatie samen. “De machine houdt met van alles rekening. Gebruikt een operator twee handen? Hoe is de timing tussen verschillende stappen? Welke fouten maken ze? Ook kijkt de machine naar leeftijd, ervaring en of iemand er al een lange dienst op heeft zitten bijvoorbeeld.”
Lees hier meer over de verschillende fieldlabs op de Brainport Industries Campus
Uit al deze data kun je allerlei dingen afleiden, legt Yurchenko uit. “Als er veel tijd tussen verschillende stappen zit, kan iemand twijfelen. Of maakt iemand meer fouten als hij nachtdienst heeft? We proberen al deze aannames te toetsen met de werkelijkheid en hebben hiervoor een model ontwikkeld. Hier komen alle gegevens bij elkaar. Zo komt de machine tot een ‘best practice’ om een product zo goed mogelijk in elkaar te zetten.”
Zoektocht naar hoe machines en mensen het beste samenwerken
Deze ‘best practice’ zoals Yurchenko het noemt, wordt door de machine weer gebruikt om operators met minder ervaring te ondersteunen. “Zeker in de maakindustrie waar het gaat om veel variaties binnen producten, kan dit helpen om fouten te voorkomen. Via de machine komt de kennis van ervaren operators terecht bij hun collega’s die nog niet zoveel weten. Door deze samenwerking tussen mens en machine leren de nieuwe operators veel sneller en blijven ze betrokken bij hun werk.”
Wanneer deze zelflerende assemblagelijn in de praktijk gebruikt kan worden is nog niet bekend. De eerste onderzoeksresultaten zijn binnen, maar er is nog genoeg te testen en analyseren. “De pandemie heeft de boel flink vertraagd. Om te testen of het model werkt hebben we data en input van verschillende experts nodig, dat gaat nu allemaal wat moeizamer.”
Maar toch heeft Yurchenko er alle vertrouwen in dat het gaat lukken: “De omgeving waarin we werken is een soort speeltuin waar we uitvinden hoe robots en mensen het beste kunnen samenwerken. Tegelijkertijd werken we aan echte problemen, engineers denken constant mee. Voor ieder idee hebben ze weer tien andere suggesties. Dat werkt motiverend.”