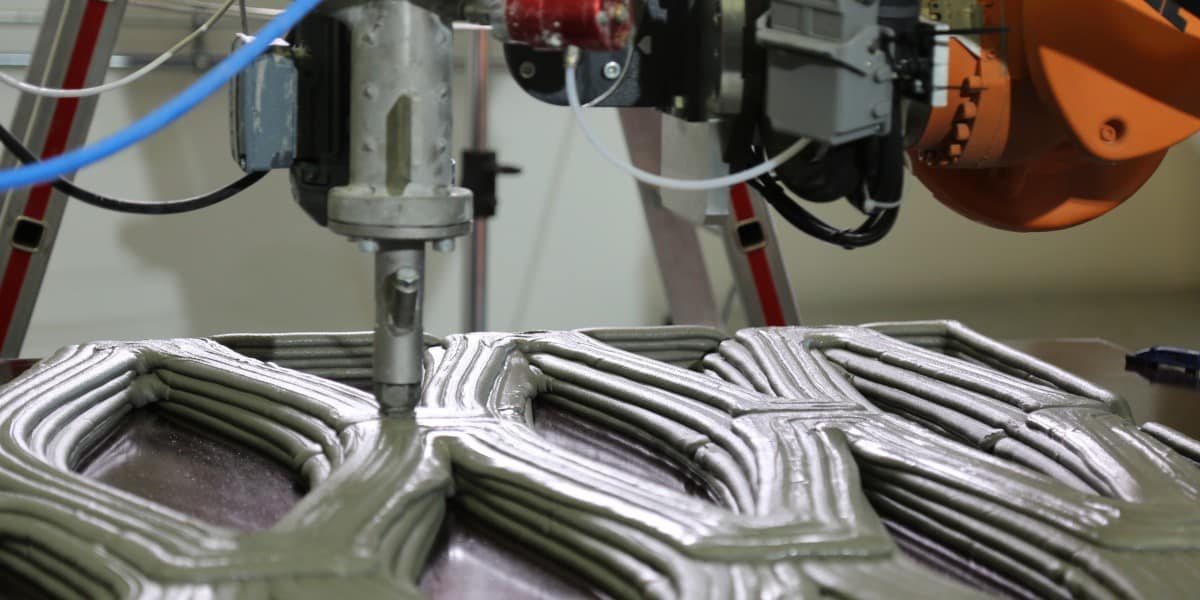
Huizen die rechtstreeks uit de 3D betonprinter komen zijn nog steeds in experimentele status, maar uiteindelijk zou dit fenomeen de bouwsector sterk kunnen vereenvoudigen. Aan de Technische Universiteit van Graz is zojuist een project afgerond waarin toekomstige toepassingsgebieden voor de technologie zijn getest. Het leidmotief was het grondstofbesparend gebruik van bouwmaterialen.
Veel onderzoeksteams zijn bezig met het 3D-printen van beton en hebben allemaal te maken met vergelijkbare problemen, zegt Stefan Peters, hoofd van het Instituut voor Structureel Ontwerp aan de TU Graz. De belangrijkste aandachtspunten zijn de samenstelling van het beton en het type machines dat gebruikt kan worden voor 3D printen. Als deze problemen worden opgelost, heeft de technologie het potentieel om de betonnen constructie te veranderen, dus de wetenschapper.
Efficiënt gebruik van middelen
Zelf doet hij onderzoek in een interdisciplinair team dat het volledige potentieel van 3D-betonprinting beter wil benutten. Beton is wereldwijd het meest gebruikte bouwmateriaal. Bij de productie van cement en staal worden grote hoeveelheden fossiele grondstoffen zoals kolen en olie verbruikt. “Volgens de huidige berekeningen kunnen de fossiele grondstoffen steenkool en olie in hun huidige vorm slechts voor een goede honderd jaar worden gebruikt. Daarnaast komen bij de productie van gangbare bouwmaterialen grote hoeveelheden CO2 vrij. Met een efficiënter gebruik van middelen kan veel worden bespaard”, legt Peters uit.
Inflexibele schil constructie
Conventioneel worden prefabbetondelen in de schilconstructie vervaardigd. Dit is een soort giettechniek: vloeibaar beton wordt in een vooraf gebouwde bekisting gevuld en stolt in de gewenste vorm. Het proces is eenvoudig, snel en betrouwbaar. De vervaardigde componenten zijn zeer robuust. Het probleem met het proces is een gebrek aan flexibiliteit, wat resulteert in een hoog verbruik van middelen en beperkte ontwerpmogelijkheden:
- Om het proces zuinig te houden, worden altijd dezelfde componenten uit één bekisting geproduceerd – ook al is het niet nodig om altijd dezelfde hoeveelheid materiaal te gebruiken.
- De productie van individuele of geometrisch veeleisende bekistingen is duur en vaak niet rendabel. Daarom zijn ze vaak uitgesloten tijdens het planningsproces.
Peters noemt een klassiek plafondelement dat in heel Europa voor miljoenen vierkante meters wordt gebruikt als voorbeeld van de schilconstructiemethode. Het heeft een dikte van ongeveer dertig centimeter, een overspanning van ongeveer acht meter en wordt ondersteund door dragende elementen.
Individueel planbaar
Dit plafondelement was een van de twee case studies in het onderzoeksproject. In 3D printen kunnen individueel geplande elementen op basis van een digitaal model worden geïmplementeerd. Peters en zijn team overwogen waar ze met minder beton af konden zonder dat dit ten koste ging van de prestaties.
In de tweede casestudy moest een sierlijk geveldeel dat niet in een bekistingssysteem kon worden geproduceerd, driedimensionaal worden geprint. De basis voor het onderzoeksproject was het wiskundig onderzoek van de twee elementen en het testen van een zuinig gebruik van grondstoffen. Vervolgens moesten de rijwegen van de printrobot nauwkeurig worden berekend. “Het is als het tekenen van een huis zonder de pen van het papier af te halen”, legt Peters uit.
In dit fundamenteel onderzoeksproject doet een interdisciplinair team van architecten, ingenieurs, werktuigbouwkundigen en materiaaltechnologen onderzoek. Er waren ook industriële partners bij betrokken, die samen het volledige productieproces van een prefabbetonelement vertegenwoordigen.
Machine- en betonmix
Er werd een printer gebouwd om de nieuwe constructietechnologie te testen. De geschikte printkop is ontwikkeld in samenwerking met een bedrijfspartner. Het betonmengsel werd droog in een grote zak gepositioneerd, verwerkt door een wormpomp en via een lange slang naar de printkop getransporteerd. De printkop spuit het beton in banen uit.
De uitdaging was het optimaliseren van de printbare betonmix en vooral het bereiken van een pompbare consistentie. “Het beton moet continu door de printverstuiver kunnen worden getransporteerd en mag niet blijven plakken, zelfs niet tijdens korte pauzes. Tegelijkertijd moet het zich bij aankomst op de plaats van bestemming verbinden met de eerder aangebrachte laag”, verklaart Andreas Trummer vom Institut für Tragwerksentwurf van de TU Graz. Inmiddels is er een mooi mengsel gevonden. De grofste delen hebben een maximale doorsnee van drie millimeter.
Ook de verbinding tussen de afzonderlijke betonplaten kon pas na meerdere pogingen tot stand komen.
Medio november waren alle problemen opgelost en was het team tevreden met de resultaten van de eerste compressietesten op het Instituut voor Bouwtechniek.
Samenwerking met commerciële ondernemingen
Het zal nog enige tijd duren voordat huizen standaard uit de betonprinter komen. “Wij als TU Graz staan voorop als het gaat om de toekomstige toepassingsgebieden van de nieuwe technologie, omdat hier tot nu toe weinig aandacht aan is besteed,” zegt Peters. Er zijn al vervolgprojecten gepland.
Een zeer fijne betonmix en een speciaal gebouwde robot maken ook 3D printen van gevelornamenten mogelijk. © Birgit Baustädter – Technische Universiteit Graz.