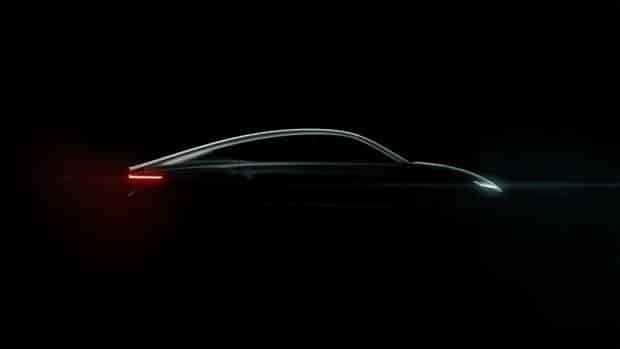
5 maanden geleden besloten we de bouw van het prototype te vervroegen. Geen gemakkelijke beslissing maar wel noodzakelijk om sommige van de concepten die we op papier hadden staan al vroegtijdig te toetsen met de realiteit. Het betekende financieel risico, het betekende een compleet andere focus, het was het startsein van 5 maanden met pieken en dalen maar ook een team dat er sterker uit is gekomen.
Het was de eerste echte test voor de 130 mensen die in de loop van 1.5 jaar bij Lightyear zijn begonnen. De lakmoesproef, kunnen we het voor elkaar krijgen met deze club? De werkdruk gaat als een golf door het bedrijf heen: eerst de architecten die, elk verantwoordelijk voor hun eigen stuk van het voertuig, in een korte periode alle koppelingen met andere systemen moeten doornemen: Exterieur met interieur, chassis met de aandrijving, software met alle elektra in de auto en nog honderden van deze koppelingen. Welke productiemethoden passen hierbij, rekening houdend met vibraties, temperaturen, volgorde van assemblage, sterkte, ga zo maar door.
Volgende fase detailontwerp, samen met de leveranciers. Zonder input van de leveranciers ontwerp je iets wat niet gemaakt kan worden. Het detailniveau is groot. Tot op welke twee panelen verbonden worden met welk schroefje en welke curve er voor zorgt dat exterieur en interieur tot op minder dan een millimeter precies bij elkaar komen. Hoe zorgen we ervoor dat de stoffen van het interieur netjes worden gestikt en de randen niet zichtbaar zijn. Hoe zorgen we ervoor dat alle elektronica wordt voorzien van zowel stroom als van de juiste signalen. Tot op de interieurlampjes in de achterbak.
Niet veel later: orders plaatsen. Het prototype bestaat uit duizenden onderdelen, die vaak los van elkaar bij verschillende leveranciers besteld moeten worden. De telefoons draaien overuren en het kersverse inkoopteam, waarvan velen er pas een paar maanden zitten bestellen in hoog tempo de onderdelen die nog geen dag geleden van de tekentafel gekomen zijn.
Van over de hele wereld komen onderdelen binnen. Veelal Europa, maar ook vanuit de VS en China komen onderdelen met een aantal weken levertijd naar onze productiefaciliteit in Helmond. Daar beginnen de eerste assemblagewerkzaamheden. Eerst het chassis, de ruggengraat van de auto. De contactpunten met exterieur, interieur, aandrijflijn en thermisch systeem worden tot op de millimeter toe nagemeten en aangepast waar nodig. Vervolgens exterieur. Zouden de panelen van de leverancier precies passen op het chassis? Is het onderdeel precies goed getekend? Krijgen we de kieren tussen de panelen tot slechts een paar millimeter?
Dan de laatste fase, nadat de auto terug is van de spuiter. First things first: Iedereen plakt alle scherpe accessoires en stukjes van kledingstukken af. Spijkerbroeken vol met plakband, horloges af, en ja, zelfs ringen af. Kilometers aan bekabeling gaan de auto in, vantevoren allemaal al getest. Motoren worden in de auto verenigd met batterij en zonnepaneel. Eerder al in het lab getest, maar nu ook echt in de auto: zouden de motoren hun eerste rondjes in de auto kunnen maken?
130 mensen, duizenden anekdotes, lange dagen, wallen onder de ogen, partners die tot het gaatje gaan om te assisteren, naarmate de weken verstrijken komt er steeds vaker applaus. Dit is het verhaal van een team met één doel. En een gezonde hoeveelheid passie om de wereld beter te maken.
We zijn trots om onze bloed zweet en tranen dinsdag aan jullie te laten zien.
Over deze column:
In een wekelijkse column, afwisselend geschreven door Maarten Steinbuch, Mary Fiers, Carlo van de Weijer, Eveline van Zeeland, Lucien Engelen, Tessie Hartjes, Jan Wouters, Katleen Gabriels, Peter de Kock en Auke Hoekstra, probeert Innovation Origins uit te vinden hoe de toekomst eruit zal zien. Deze columnisten, af en toe aangevuld met gastbloggers, zijn allemaal op hun eigen manier bezig met oplossingen voor de problemen van onze tijd. Zodat Morgen Beter wordt. Hier alle eerdere afleveringen.