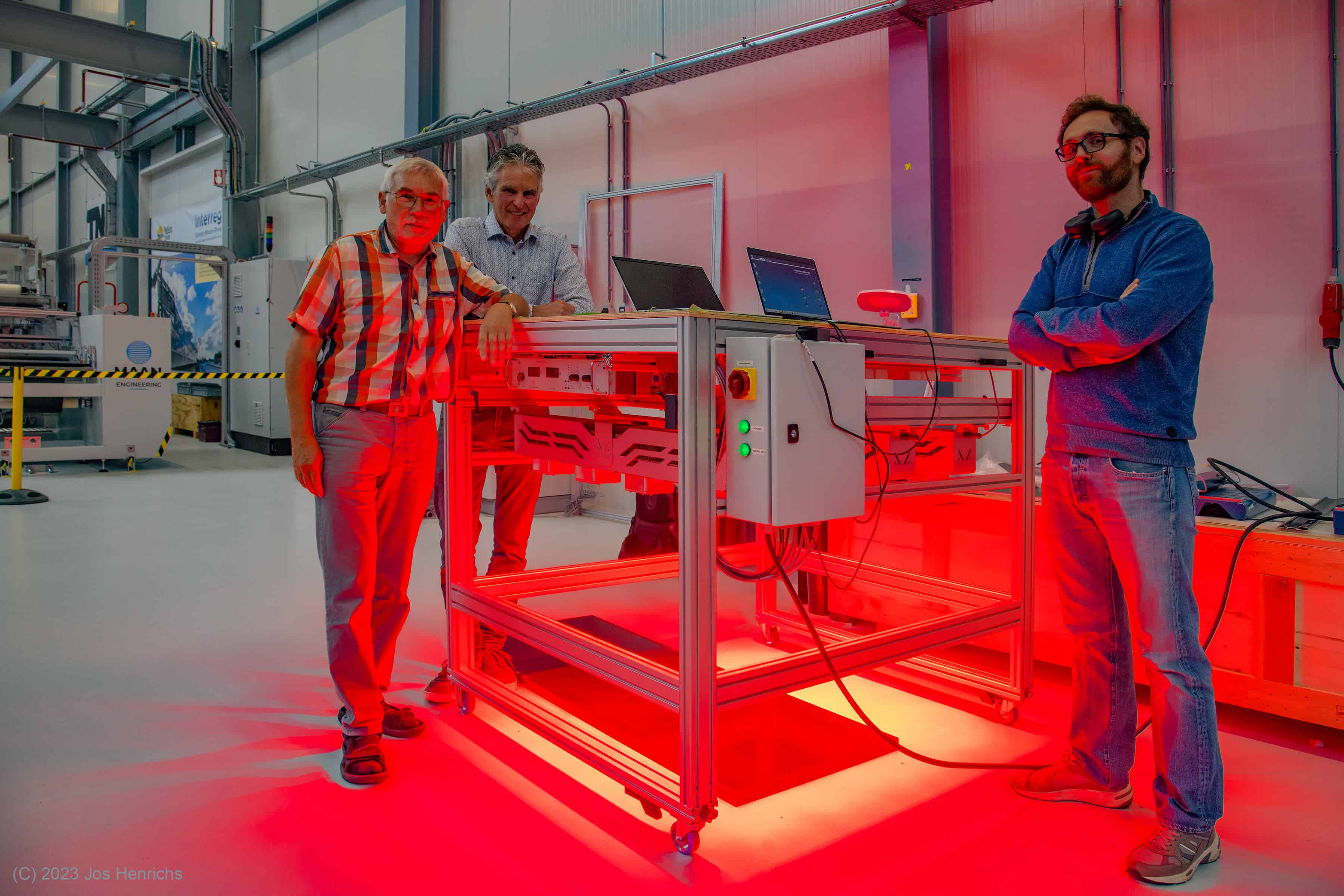
Vijftig organisaties hebben inmiddels een plek gevonden in de Brainport Industries Campus. Veelal high-tech maakbedrijven, en daarnaast ook onderwijsinstellingen zoals Summa, Avans en Fontys. Maar er is ook volop ruimte voor onderzoek, zoals bij TNO, partner in Solliance, dat bouwt aan efficiënte manieren om flexibele zonnepanelen te produceren. In dat proces stuitten de onderzoekers op een uitdaging: hoe kun je in dat maakproces een vollediger beeld van onvolkomenheden krijgen? Elektroluminescentie was al een goed ontwikkelde techniek voor het karakteriseren van zonnepanelen, maar een complementaire methode, fotoluminescentie, zou nog meer fouten in de modules aan het licht kunnen brengen, zo was de gedachte.
Tot voor kort was de enige manier om dat te doen door zo’n paneel of folie kapot te snijden en per stukje te controleren. Niet alleen was dat verre van foutloos, het betekende ook dat de gecontroleerde modules daarna niet meer bruikbaar waren. Dubbel zonde dus. Bovendien waren er betere inspectiemethoden nodig voor de nieuwe CIGS-zonnepanelen die TNO ontwikkelde. Dat moet beter kunnen, dacht Rémi Aninat van TNO. Hij legde zijn probleem neer bij oud-collega Jos Henrichs van Solland Solar, die op zijn beurt Hans Meeske van Holland Innovative tipte. Meeske was direct enthousiast en maakte er een HI-project van. Naast Henrichs en zijn collega Paul Wijnands werd ook Aubert Dupont van lichtspecialist Stogger er direct bij betrokken. Samen zochten ze naar een oplossing. En vonden die ook.
Doorbraak
Het resultaat van hun speurwerk – een machine die defecten in complete panelen kan opsporen – is niet minder dan een doorbraak. Maar daar waren wel twee jaar van research, bouwen en testen voor nodig.
Samen met het trotse ontwikkelteam kijken we naar hun meesterwerkje. Op de begane grond van de BIC, achter een open hekwerk dat het TNO-terrein scheidt van de andere BIC-huurders, staat de groot uitgevallen vierkante statafel. Aan de bovenkant zorgt een plank ervoor dat de gevoelige apparatuur niet te kwetsbaar wordt. Onder de plank eerst een laag met elektronica maar direct daaronder het hart van de machine: 16 sterke lampen en daar midden tussenin een camera. Samen zijn ze in staat zowel elektroluminescente als fotoluminescente inspecties uit te voeren.
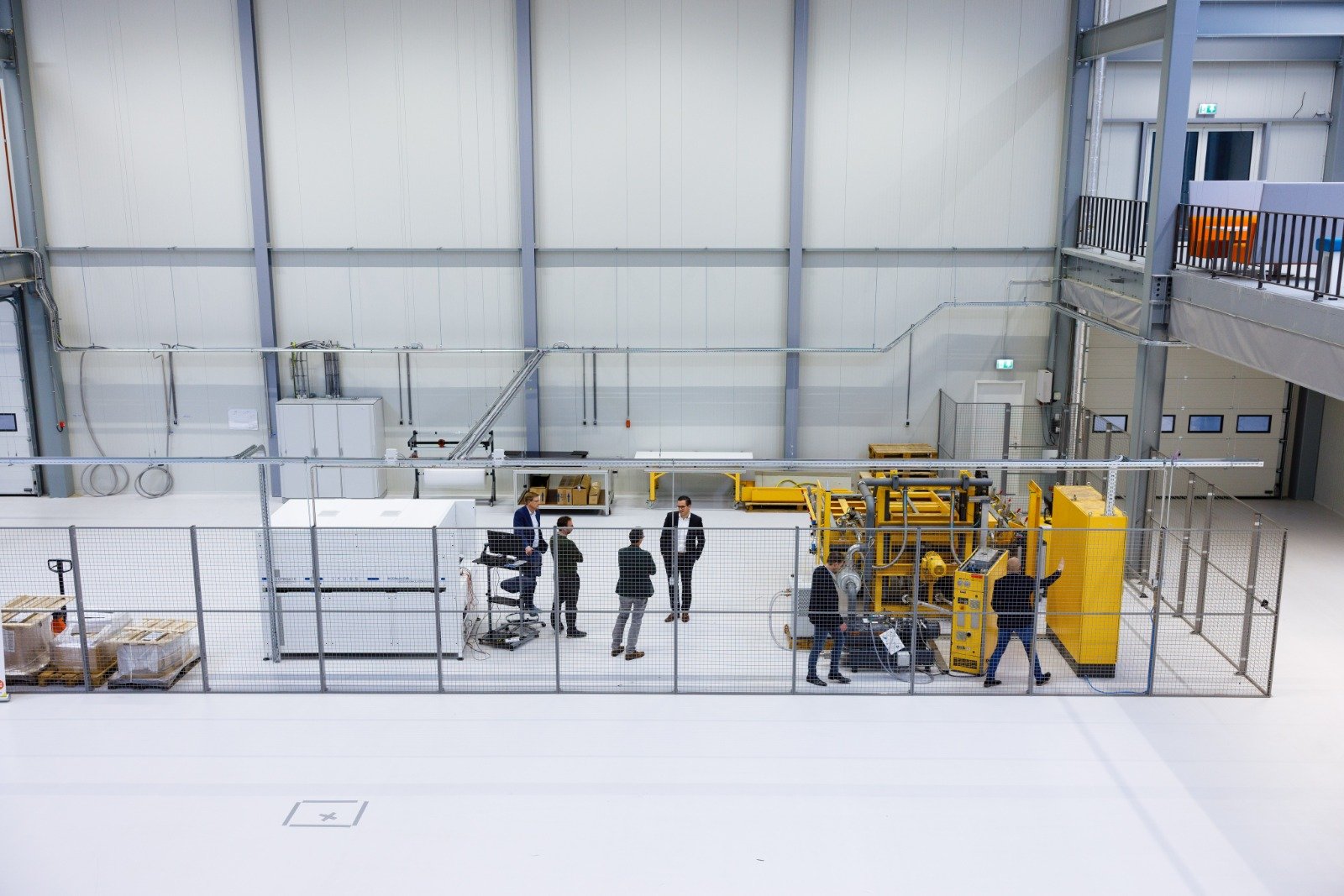
“In ons lab konden we dit soort testen al doen, maar alleen op kleine schaal en dus zeker niet met complete panelen”, zegt Aninat. “Voor TNO is werken op een R&D schaal een vereiste, dus we wisten dat we een oplossing moesten bedenken. Voor alle soorten panelen, de normale en de flexibele.” En dus kwamen Wijnands en Henrichs in beeld. Als projectleider en systeemarchitect hebben zich vervolgens samen met Aubert Dupont van Stogger gericht op een oplossing van het probleem.
Prototype
Hoewel het concept voor die oplossing al vrij snel in beeld kwam, duurde het toch nog wel enige tijd voordat er een werkend prototype kon worden geleverd. Dat had niet alleen te maken met het design (aanvankelijk werd gedacht aan een gesloten kast, maar dat bleek toch wat te inflexibel en te kostbaar), maar ook met de belastbaarheid van het systeem zelf. Jos Henrichs: “Daarbij gaat het zowel om de lampen als om de camera. Er gaat nogal wat stroom door de systemen; als het allemaal te warm wordt loop je het risico dat het materiaal gaat scheuren of zelfs breken. Die afstemming ligt heel gevoelig.”
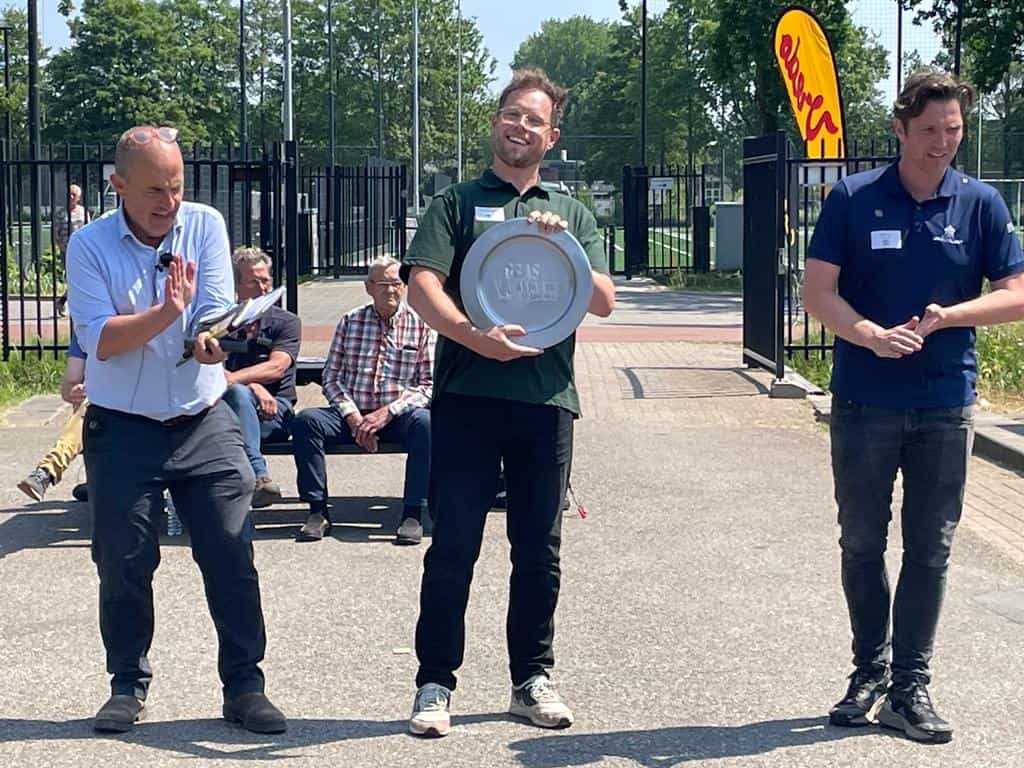
Met 16 Mechatronix light engines van 500 watt elk, speciale custom filters en lenzen die ervoor zorgen dat alleen het zeer zwakke infrarood luminescentielicht de camerasensor bereikt, lijkt een ideale configuratie gevonden. “Het kostte ons behoorlijk wat vallen en opstaan – en heel veel testen – maar we zijn blij dat we uiteindelijk de puzzel hebben opgelost”, vult Wijnands aan. Het mechanische design, de elektronica, de timing van de lichten moet kloppen, net als de signalen die vanuit de software aan de camera worden gegeven. Het luistert allemaal ontzettend nauw.”
Custom pcb
Stogger en HI hadden eerder al samengewerkt in kas- en sportveldverlichting. “Logisch dus dat ze ook nu weer bij ons aanklopten”, zegt Aubert Dupont. Maar het was ook niet zo dat Stogger ze ergens op de plank had liggen. “We hebben wel vaker lampen ontwikkeld, maar dat type niet. Wat we wel wisten is dat lampen met de gewenste frequentie ook in kassen zitten. Het is vaak een mengsel van blauw, rood en ‘far-red’, maar in dit geval moest het alleen rood zijn. Toen we dat lichtrecept hadden gevonden, konden we de opstelling doorontwikkelen en produceren.”
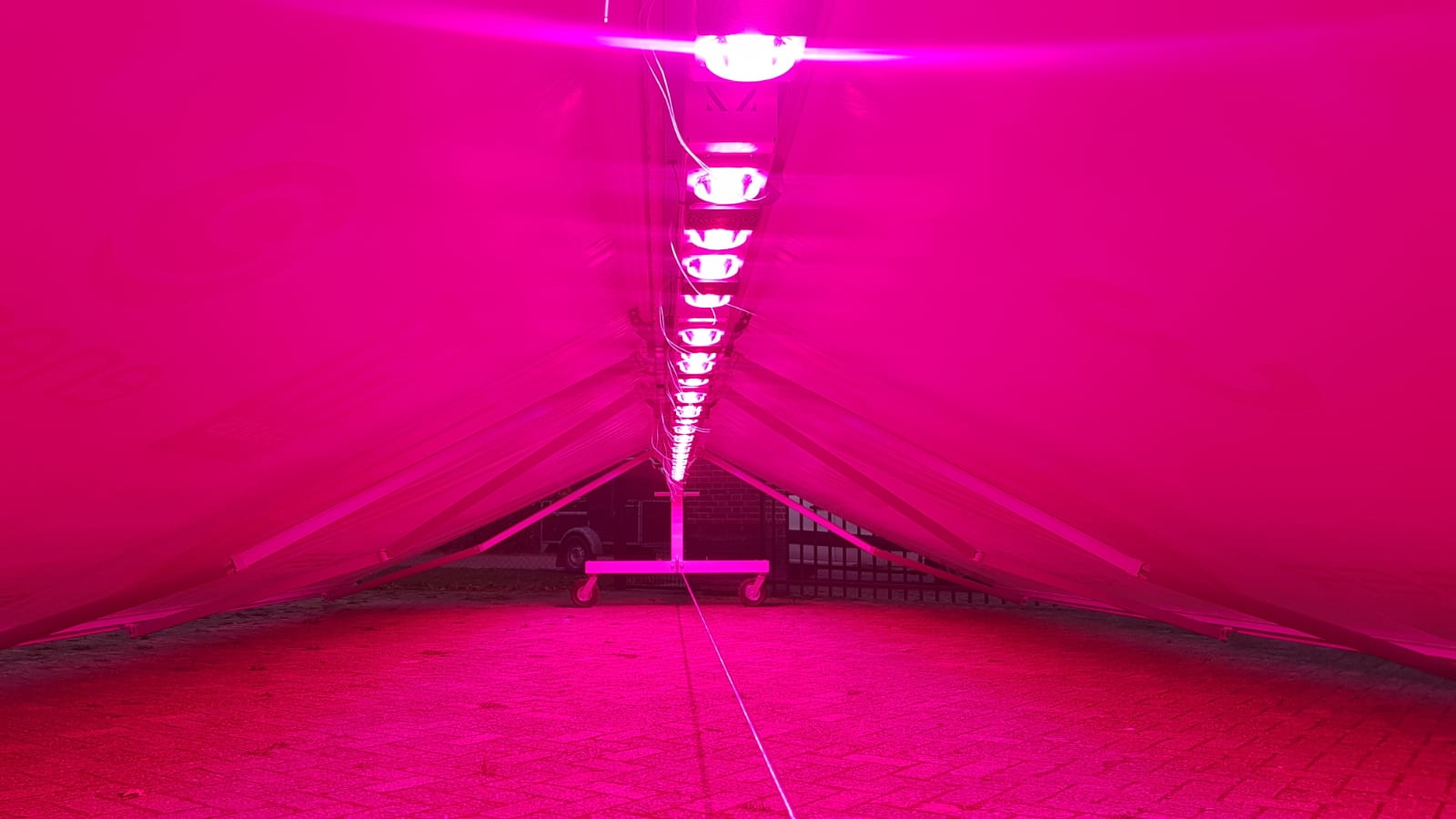
Bij de eerste testen bleken de filters die voor de lampen geplaatst waren echter al na twee minuten te breken door de opgenomen warmte. De reliability experts van Holland Innovative hebben dat opgelost na het opzetten en uitvoeren van de nodige levensduurtesten. Het resultaat was een optimum belichtingstijd waarbij de filters met zekerheid heel blijven.
Maar daarmee was het nog niet af, want om betrouwbare meetresultaten te krijgen moesten de lampen goed gekallibreerd worden om een gelijkmatige verlichting te verkrijgen: de buitenste lampen in een andere sterkte dan de binnenste. De aansturing moest dus ook apart gebeuren. “Een standaard PLC werkt dan niet, maar gelukkig draai ik mijn hand niet om voor een zelfgebouwde custom pcb.” En daarmee was het plaatje compleet voor de oplevering aan Aninat en zijn team.
Roll-to-roll
Nu de machine staat, is het weer aan TNO om de functionaliteit te bepalen. Aninat: “Ik verwacht dat we regelmatig gebruik gaan maken van deze nieuwe mogelijkheid. En altijd in de fase van ontwikkeling.” Ook denkt TNO al na over het afstemmen van deze opstelling op specifieke toepassingen, zoals de lange roll-to-roll gelamineerde modules, die momenteel bij TNO worden ontwikkeld. Zou het ook wat kunnen zijn voor andere ontwikkelaars van zonnepanelen? “Dat kunnen we altijd later nog bepalen. Laten we alles eerst maar eens voor eigen gebruik gaan optimaliseren.”