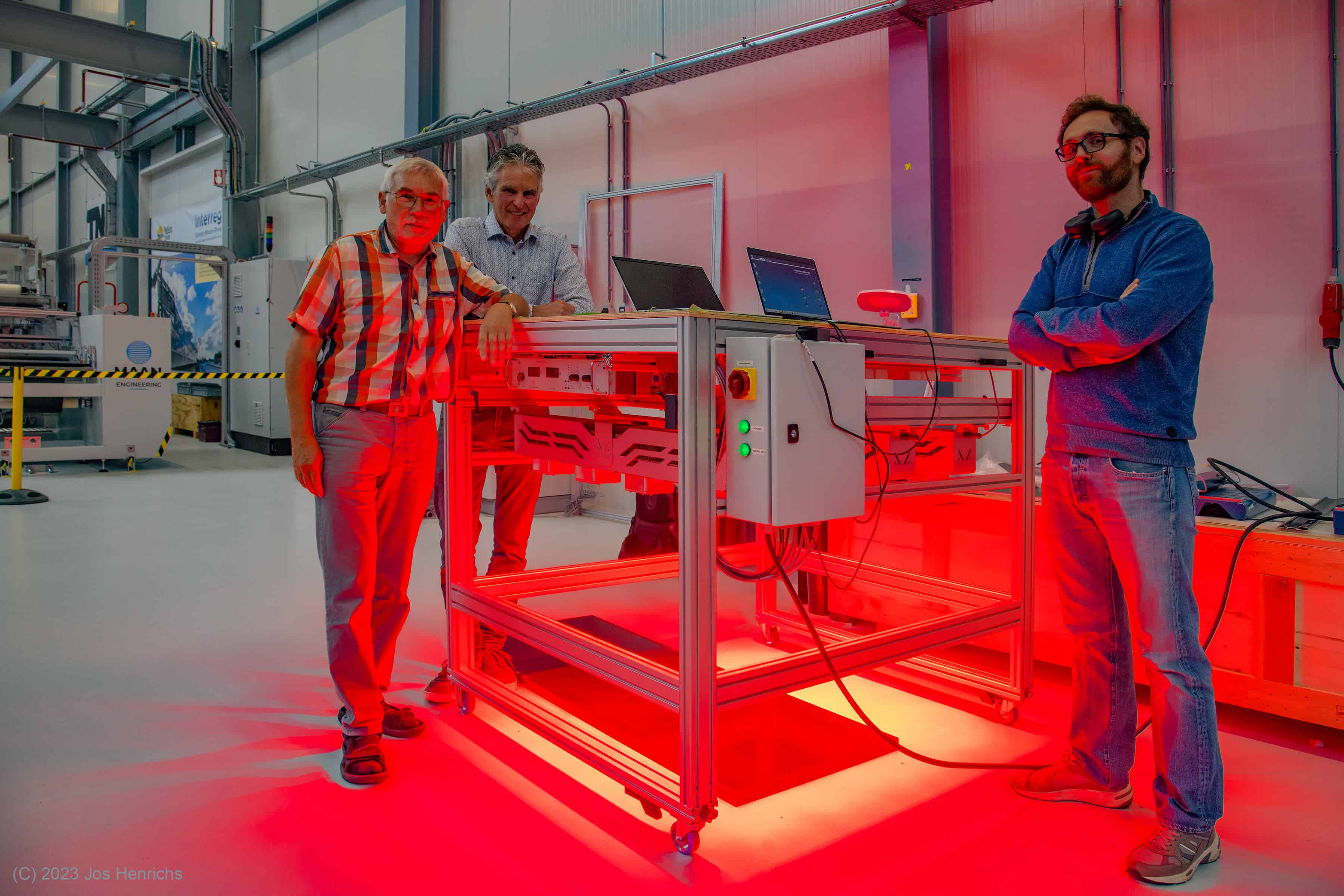
Some fifty organizations have already found a place in the Eindhoven Brainport Industries Campus. Most of them are high-tech manufacturing companies, as well as educational institutions such as Summa, Avans, and Fontys. But there is also plenty of room for research, like with TNO, a partner in Solliance, building efficient ways to produce flexible solar panels. In that process, the researchers encountered a challenge: How can you get a complete picture of imperfections in that manufacturing process? Electroluminescence was already a well-developed technique for characterizing solar panels, but a complementary method, photoluminescence, could reveal even more flaws in the modules, it was thought.
Until recently, the only way to do that was to cut such a panel or film apart and check it piece by piece. Not only was that far from flawless, it also meant that the checked modules were no longer usable afterward — a double waste, in other words. Moreover, better inspection methods were needed for the new CIGS solar panels developed by TNO. There must be a better way, thought Rémi Aninat of TNO. He put his problem to former colleague Jos Henrichs of Solland Solar, who in turn tipped off Hans Meeske of Holland Innovative. Meeske was immediately enthusiastic and turned it into an HI project. In addition to Henrichs and his colleague Paul Wijnands, Aubert Dupont of lighting specialist Stogger also became involved. Together, they looked for a solution. And found it.
Breakthrough
The result of their research – a machine that can detect defects in complete panels – is nothing short of a breakthrough. But it took two years of research, construction, and testing.
Together with the proud development team, we can now closely examine their masterpiece. On the BIC’s ground floor, behind an open fence that separates the TNO site from the other BIC tenants stands the oversized square bar table. At the top, a shelf keeps the sensitive equipment from becoming too fragile. Under the shelf, first a layer of electronics, and directly below it, the heart of the machine: 16 powerful lights and a camera in the middle of it. Together, they are capable of both electroluminescent and photoluminescent inspections.
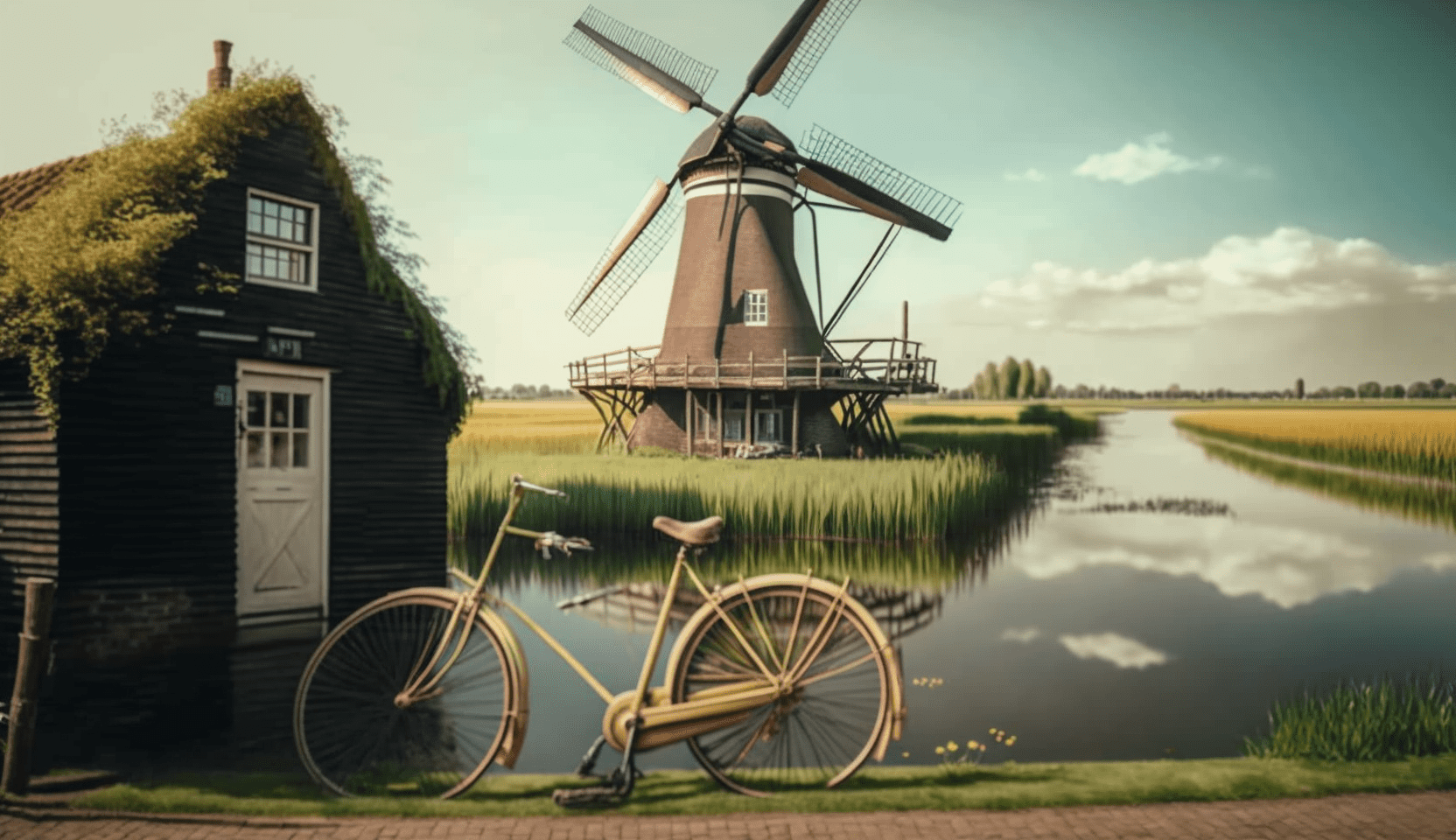
“In our lab, we could already do this kind of testing, but only on a small scale and therefore certainly not with complete panels,” says Aninat. “For TNO, working on an R&D scale is a requirement, so we knew we had to develop a solution. For all types of panels, the normal and the flexible ones.” And so Wijnands and Henrichs came into the picture. As the project manager and the system architect, they focused on solving the problem together with Stogger’s Aubert Dupont.
Prototype
Although the concept for that solution came into view fairly quickly, it still took some time before a working prototype could be delivered. This not only had to do with the design (initially, a closed cabinet was considered, but that turned out to be too inflexible and too expensive), but also with the system’s load capacity. Jos Henrichs: “This involves both the lamps and the camera. Quite a bit of current goes through the systems; if it all gets too hot, you run the risk of the material cracking or even breaking. That coordination is very sensitive.”
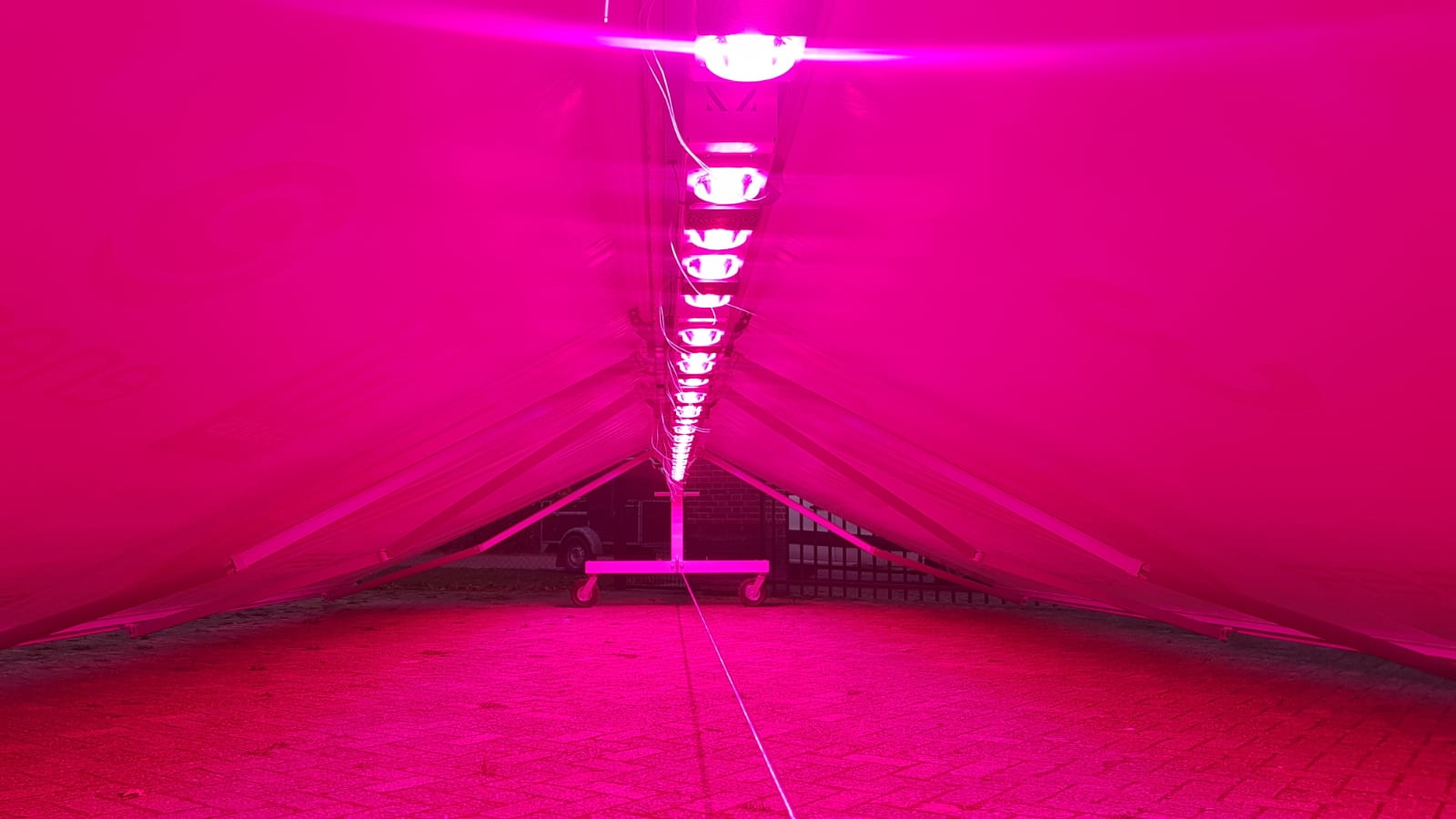
With 16 Mechatronix light engines of 500 watts each and special custom filters and lenses that ensure that only the feeble infrared luminescence light reaches the camera sensor, an ideal configuration seems to have been found. “It took us quite a bit of trial and error – and a lot of testing – but we are happy to have finally solved the puzzle,” Wijnands adds. The mechanical design, the electronics, and the timing of the lights have to be right, as do the signals given to the camera from the software.”
Custom pcb
Stogger and HI had previously worked together in greenhouse and sports field lighting. “So it was logical that they knocked on our door again,” says Aubert Dupont. But it wasn’t as if Stogger had these lamps on the shelf somewhere, either. “We have developed lamps before, but not that type. We did know that lamps with the desired frequency are also in greenhouses. It’s often a mixture of blue, red, and ‘far-red,’ but it had to be only red in this case. Once we found that light recipe, we could further develop and produce the setup.”
During the first tests, however, the filters placed in front of the lamps appeared to break after only two minutes due to the heat absorbed. Holland Innovative’s reliability experts solved this after setting up and performing the necessary lifetime tests. The result was an optimum exposure time in which the filters remained undamaged with certainty.

But that wasn’t all because to get reliable measurement results, the lamps had to be properly calibrated to obtain uniform illumination: the outer lamps had to get a different power than the inner ones. So, the control also had to be done separately. “A standard PLC won’t work then, but fortunately, I am used to self-building custom PCB.” And with that, the picture was complete for delivery of the light structure to Aninat and his team.
Roll-to-roll
Now that the machine is in place, it’s back to TNO to determine its functionality. Aninat: “I expect that we will use this new capability regularly. And always in the development phase of a project.” TNO is also considering tailoring this setup to specific applications, such as the long roll-to-roll laminated modules currently being developed at TNO. Could it also be something for other solar panel developers? “We can always determine that later. Let’s start optimizing everything for our own use first.”