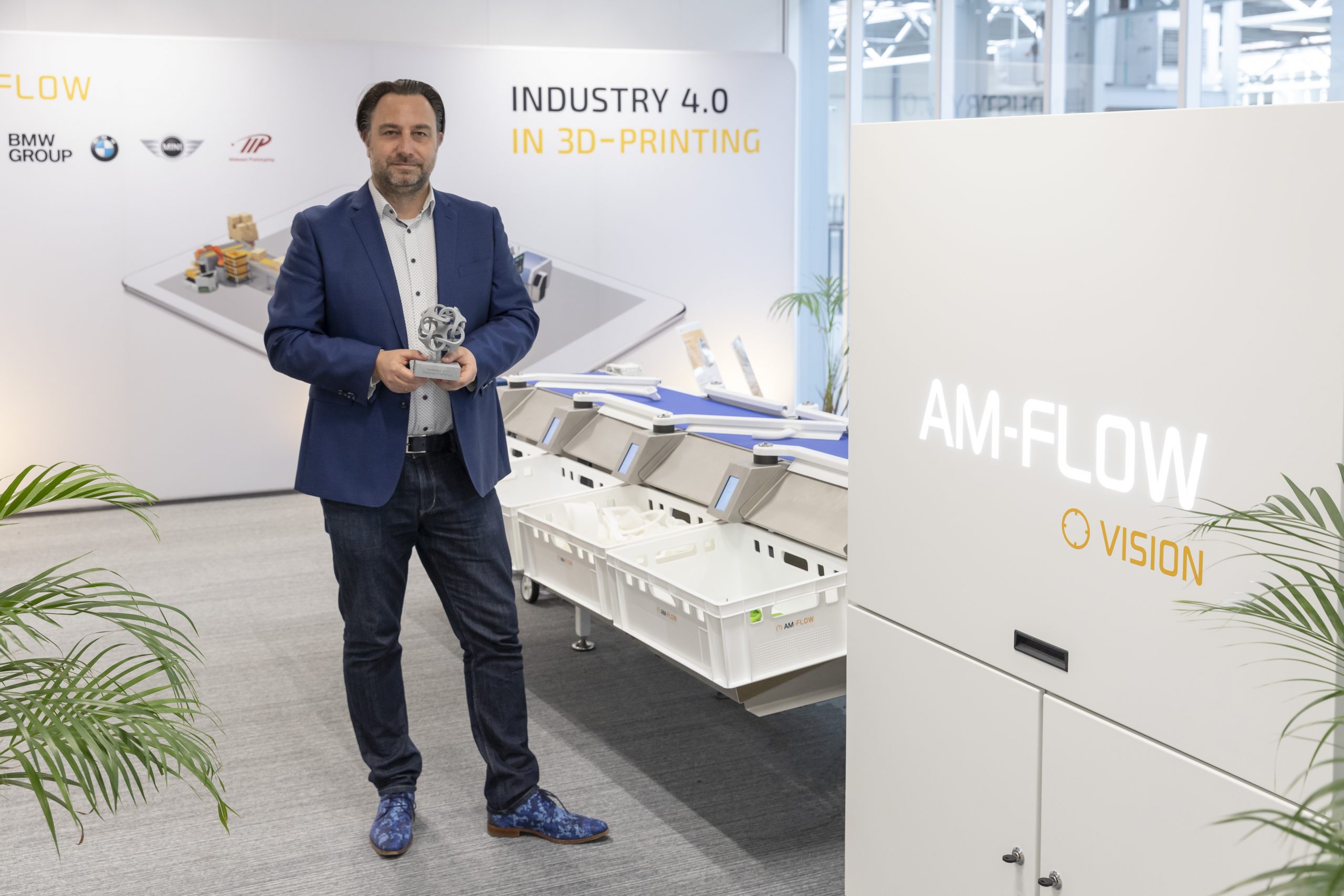
Fabrikanten maken steeds meer gebruik van 3D-printen als productiemethode. De Nederlandse markt voor industrieel 3D-printen groeit de komende jaren tot ruim 22 miljard euro in 2030, blijkt uit een rapport van PWC. Waar de techniek een aantal jaar geleden alleen nog werd gebruikt voor prototyping, is het inmiddels zo ver doorontwikkeld dat ook complete eindproducten uit commerciële printers rollen.
Maar hoe slim en digitaal 3D-printen aan de voorkant is, zo inefficiënt verloopt het proces als die producten eenmaal uit de printer komen. Bijna overal worden onderdelen nog handmatig geïdentificeerd, gesorteerd en nabewerkt. Best te doen voor een aantal prototypes, maar een repetitief en tijdrovend klusje als er ineens honderden producten per dag uit een printer komen. “Bovendien neemt de kans op fouten toe,” zegt Dennis Lieffering van AM-Flow. Het bedrijf werkt sinds 2018 aan de automatisering van dit proces. In Amsterdam ontwikkelen ze de software en in Eindhoven op Brainport Industries Campus alle mechanische toepassingen en robotics.
“Sommige onderdelen zijn bijna niet van elkaar te onderscheiden. Het gaat om hele kleine verschillen. Dat maakt het soms lastig om te zien welk 3D-model van welke klant is en wat ermee moet gebeuren. Of waar ze in de fabriek naartoe moeten.” Al dit handmatige werk noemt hij het ‘dirty secret’ van de additive manufacturing industrie. Lieffering: “Bedrijven laten terecht graag zien wat de voordelen van 3D-printen zijn. Maar de ‘achterkant’ – wat er gebeurt na het printen – blijft vaak buiten beeld. Nu is het nog zo dat naarmate de productie toeneemt, de kosten voor arbeid ook stijgen. Er komt niet alleen veel handwerk kijken bij het schoonmaken, identificeren en sorteren van de geprinte onderdelen, maar op heel de route door de fabriek. Tot de verpakking aan toe.”
Automatisch herkennen en sorteren binnen enkele seconden
Om dit op te lossen ontwikkelt AM-Flow machines op basis van data, sensoren en AI. Met deze machines verkorten ze niet alleen het productieproces, maar ze zorgen ook dat engineers, die dit handwerk nu nog voornamelijk doen, meer tijd over hebben voor andere dingen. Het ontwerpen van betere producten bijvoorbeeld. Dat werkt als volgt. Zodra een product uit de 3D-printer rolt, wordt dit eerst schoongemaakt. Daarna pakt een robotarm de 3D-geprinte objecten uit een bak en plaatst deze op een lopende band richting de AM-Vision. Deze module is voorzien van 10 camera’s die een product binnen enkele milliseconden herkent en doorstuurt naar het sorteersysteem. Vanuit hier worden de onderdelen met zelfrijdende karretjes naar de juiste afdeling gestuurd voor extra nabehandelingen. Verven of polijsten bijvoorbeeld. Als laatste worden onderdelen automatisch verpakt en gelabeld om naar de klant te sturen.
“Met onze technologie maken we ook de ‘achterkant’ van het 3D-printen digitaal. Hier komt geen mens meer aan te pas. We koppelen onze software aan de software van de fabrikant. Hierin staan 3D-modellen, productplanningen en wat er met geprinte onderdelen moet gebeuren. Krijgen ze nog een kleurtje? Moeten ze gepolijst worden? Op basis van dit 3D-model, een zelflerend algoritme en camera’s herkent de module producten razendsnel”, aldus Lieffering. Het unieke aan dit systeem is dat het niet uitmaakt hoe de geprinte delen op de lopende band belanden, van elke kant wordt het herkend. “Handmatig kan dit herkennen en sorteren soms wel een minuut duren, nu nog maar enkele seconden. Het zorgt ervoor dat de productiekosten per product omlaag kunnen.”
Gat in de markt
Volgens Lieffering is AM-Flow de enige partij die zich bezighoudt met de digitalisering en automatisering van postproductieprocessen bij 3D-printen. En dat is niet gek. De techniek is nog relatief nieuw, hierdoor zijn fabrikanten vooral bezig met de ontwikkeling van de 3D-printtechnologie en materialen. Enthousiast begint Lieffering over de geschiedenis te vertellen. “Het begon het in 1986. Chuck Hull printte toen het prototype voor een bekerhouder voor in een Saab op basis van stereolithografie. Hij gebruikte een laser om de benodigde kunsthars uit te harden met UV-licht. Sindsdien zijn er allerlei technieken bijgekomen en werd er door allerlei bedrijven geëxperimenteerd.”
SLS, bijvoorbeeld waarbij lasers kunststof- of metaalpoeder smelten. Of FDM, waarbij producten laag voor laag worden opgebouwd en de basistof een lange kunststof draad is. “Al deze technieken hebben weer allemaal hun eigen specificaties en eigenschappen. Ook komen er steeds weer nieuwe grondstoffen bij om mee te printen. Logisch dat het al die tijd om de ontwikkeling van het proces is gegaan”, legt Lieffering uit.
Met het vervallen van een aantal patenten rond 2005 werd 3D-printen ineens beschikbaar voor nieuwe fabrikanten. “Er kwamen allerlei nieuwe printers op de markt en de techniek werd steeds goedkoper, net als het printmateriaal overigens. Als deze materiaalkosten blijven dalen, wordt het steeds aantrekkelijker om eindproducten te printen.”
3D-printen heeft de toekomst
Lieffering gelooft dat 3D-printen alleen maar groter wordt de komende jaren. “Niet alleen de productieprijs gaat omlaag. Er zijn veel meer voordelen. Vergeleken met andere productietechnieken heb je minder materiaal nodig en kun je het ontwerp- en productieproces sneller aanpassen. Bovendien hoef je producten niet meer aan de andere kant van de wereld te produceren. Dat kan allemaal lokaal. Vergelijk het met de drukkerij op de hoek van de straat. Kijk wat Shapeways doet: een 3D-model uploaden en je bent klaar.”
Met verschillende klanten als BMW, Materialise en Midwest Prototyping werkt AM-Flow aan een nieuwe machine in het automatiseringsproces. “Het controleren van de kwaliteit van geprinte producten gebeurt nu in speciale meetkamers. Zeker in de automotive of luchtvaartindustrie is het belangrijk dat een product niet te veel afwijkt van het 3D-model. Maar ook fabrikanten die iets printen met elektronica erin willen controleren of dat aan de specificaties voldoet. De huidige manier van controleren duurt gemiddeld zo’n 15 minuten of zelfs langer. Dit willen we flink naar beneden krijgen. Met het digitale model hebben we in principe alle informatie om samen met de klant de kwaliteit te bepalen.”