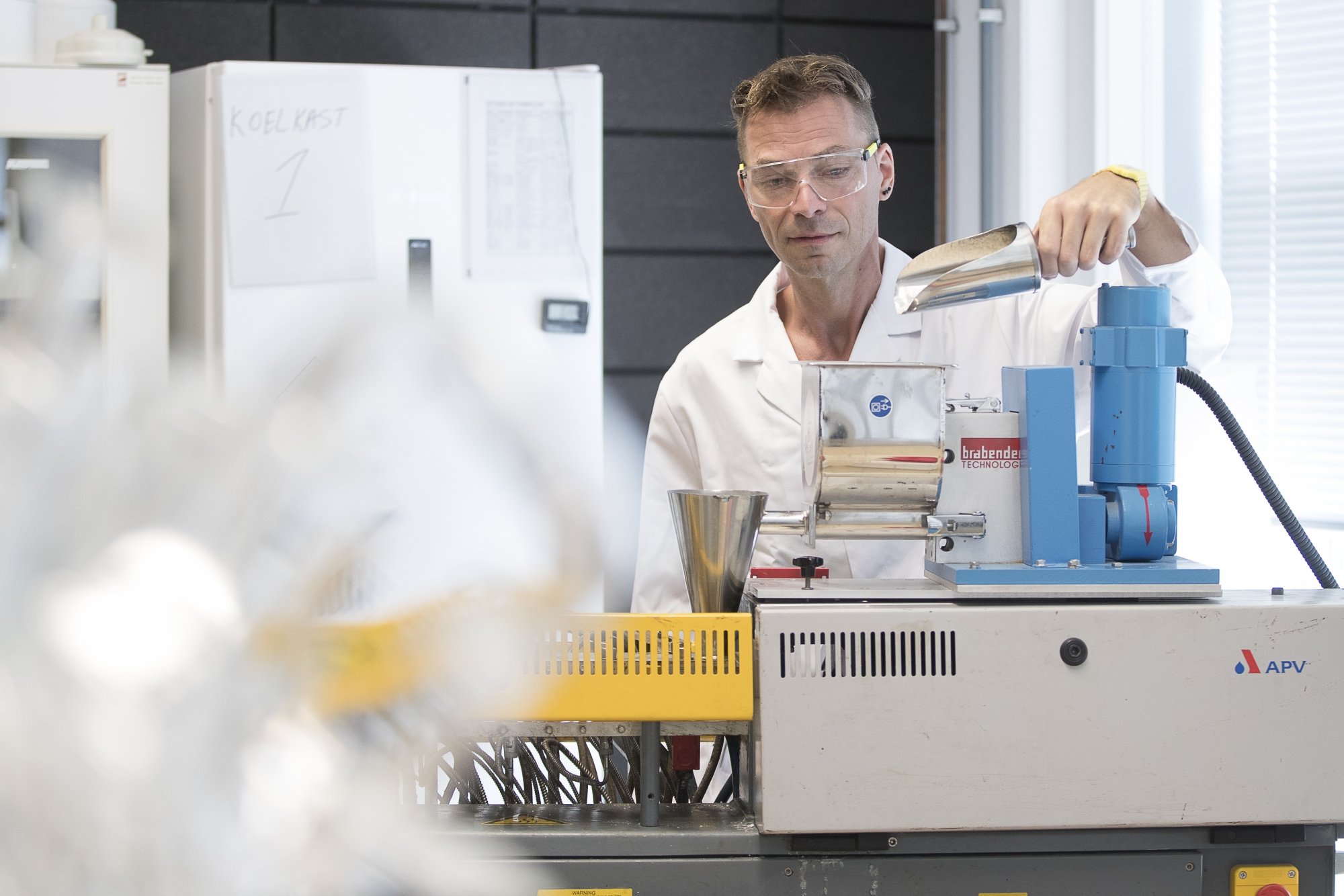
[et_pb_section bb_built=”1″][et_pb_row][et_pb_column type=”4_4″][et_pb_text _builder_version=”3.12.2″]
Chemische industrie en duurzaamheid gaan niet hand in hand als het gaat over duurzaamheid. Vaak het eerste dat mensen te binnen schiet bij chemische industrie zijn rokende schoorstenen of gevaarlijke stoffen. Dat kan toch niet duurzaam zijn?
Dit is het eerste deel van twee artikelen. Morgen het tweede deel.
[/et_pb_text][et_pb_text _builder_version=”3.12.2″]
Maar dat is precies waar het team bij Brightlands Materials Center, een initiatief van TNO en de Provincie Limburg, zich mee bezighoudt. In een oud gebouw op Brightlands Chemelot Campus in Geleen zoekt het R&D team naar manieren om toepassingen van plastic te veranderen. Het doel: verduurzamen van de plastics industrie. Marnix van Gurp is, samen met Peter Wolfs, directeur van dit ontwikkelingscentrum. Hij loopt door de verouderde gangen en laat zien wat er allemaal gebeurt om kunststof ‘opnieuw uit te vinden’. Binnenkort verhuist hij met zijn team naar een nieuw gebouw op de campus.
[/et_pb_text][et_pb_testimonial _builder_version=”3.12.2″ author=”Marnix van Gurp” job_title=”Managing director” company_name=”Brightlands Materials Center” quote_icon_background_color=”#f5f5f5″ text_orientation=”center” animation_style=”flip” animation_direction=”top” saved_tabs=”all”]
“We zitten straks echt met de gebakken peren als het gaat om recycleerbaarheid van al die verschillende materialen.
[/et_pb_testimonial][et_pb_text _builder_version=”3.12.2″]
Het is overal
Dat ‘opnieuw uitvinden’ is hard nodig meent hij, want zoals het nu gaat kan het niet langer. Van Gurp: “Het pallet aan verschillende kunststoffen is onvoorstelbaar breed. Er zijn tientallen soorten met additieven voor kleur, sterkte en andere gebruikseisen. Plastic voor binnen, voor buiten. Het mag niet in de fik vliegen of moet buigzaam zijn, voor iedere toepassing is er wel een plasticsoort te bedenken. Het is overal; in flessen, speelgoed, verpakkingen en kleren. Hierin zijn we als maatschappij echt doorgeslagen”, Van Gurp kan zich er zichtbaar aan ergeren. Druk gebarend vertelt hij verder: “Al jaren zoeken we – tot nu toe met beperkt succes – naar een oplossing voor het steeds groter wordende plasticsprobleem. We zitten straks echt met de gebakken peren als het gaat om recycleerbaarheid van al die verschillende materialen.”
[/et_pb_text][/et_pb_column][/et_pb_row][et_pb_row][et_pb_column type=”1_2″][et_pb_text _builder_version=”3.12.2″]
Proces kan altijd duurzamer
Niet alleen het recyclen van materialen heeft prioriteit meent van Gurp: “Nu komt veel van het plastic afval in de zee terecht of het gaat in een verbrandingsoven waarbij veel CO2 vrijkomt. Wij zoeken naar circulaire oplossingen waarbij materialen een zo laag mogelijke footprint op het milieu moeten hebben.”
Bij het Brightlands Materials Center proberen ze die footprint te verminderen door te werken aan lichtere materialen voor de auto-industrie. Van Gurp: “Elektrisch rijden is over een aantal jaren de norm. Het zware gewicht van auto’s maakt dat ze minder zuinig zijn, door de materialen die in auto’s verwerkt zijn, lichter te maken verminder je automatisch de impact op het milieu. Het materiaal moet natuurlijk net zo sterk, of steviger zijn. Maar daarin kijken we ook naar het proces. Duurzaamheid gaat ook over lokaal produceren en het verminderen van afval. Of afvalstromen verwerken tot nieuwe producten.”
[/et_pb_text][/et_pb_column][et_pb_column type=”1_2″][et_pb_text _builder_version=”3.12.2″ border_color_all=”#b7b7b7″ animation_style=”fold” background_color=”#f5f5f5″ custom_padding_last_edited=”on|” saved_tabs=”all” custom_css_main_element=”padding:3%;”]
Lightweight Automotive
Brightlands Materials Center richt zich op materialen en oplossingen voor drie verschillende thema’s en industriën. Additive manufacturing, Lightweight Automotive en Sustainable Buildings. Hiervoor werken ze samen met universiteiten, kennisinstellingen en bedrijven aan verschillende projecten. In het Lightweight Automotive programma gaat het om ontwikkelen van lichtere materialen die ervoor zorgen dat voertuigen zuiniger rijden. Maar ook om betere productiemethoden waarbij minder afval vrijkomt en om materialen die zo zijn ontworpen dat ze gemakkelijk hergebruikt kunnen worden. In 2019 komt in het nieuwe gebouw een showcase waar nieuwe technieken en materialen te zien zijn.
[/et_pb_text][/et_pb_column][/et_pb_row][et_pb_row][et_pb_column type=”4_4″][et_pb_image _builder_version=”3.12.2″ src=”https://media.innovationorigins.com/2018/12/photostique-brightlands-morres-076.jpg” /][et_pb_text _builder_version=”3.12.2″]
Nu gebruikt de auto-industrie nog veel materialen die moeilijk te recyclen zijn. In de proeftuin Thermoplastics Composites werkt Brightlands Materials Center samen met bedrijven uit het zuiden van Nederland aan materialen die beter geschikt zijn voor hergebruik. Het project wordt gefinancierd door Op-Zuid, provincie Limburg en de deelnemende bedrijven. Van Gurp: “Veel composieten zijn erg slecht te recyclen, niet alleen in de auto-industrie. Dat geldt ook voor boten van glasvezel, gehard met kunststofhars en de wieken van windmolens. In tegenstelling tot composieten smelten thermoplastics na verhitting, hierdoor kun je ze beter hergebruiken. Het doel van het project is om metaal te vervangen in de auto-industrie, maar ook om vanuit restmateriaal hoogwaardige materialen te ontwikkelen.”
Tekst gaat door onder de video.
[/et_pb_text][et_pb_text _builder_version=”3.12.2″]
Carbon laten praten
Van Gurp zet een veiligheidsbril op en loopt een testruimte binnen: “Hier zoeken we uit hoe we carbon – eigenlijk een composiet gemaakt van koolstofvezels en kunststof – kunnen gebruiken in een 3D-printer. Wat is er voor nodig om dit materiaal sterk en licht te maken?” In de ruimte is een student van de Technische Universiteit Eindhoven bezig met 3D-geprinte vezels. Van Gurp: “Racefietsen van carbon zijn vaak luxe producten waar mensen veel geld voor betalen. Het materiaal is ontzettend sterk in de zin dat het veel kracht kan hebben, maar wanneer je valt met zo’n fiets breekt het gemakkelijk of ontstaan scheuren in het carbon.”
[/et_pb_text][et_pb_testimonial _builder_version=”3.12.2″ author=”Marnix van Gurp” job_title=”Managing director” company_name=”Brightlands Materials Center” quote_icon_background_color=”#f5f5f5″ text_orientation=”center” animation_style=”flip” animation_direction=”top” saved_tabs=”all”]
“Nu staat een vliegtuig na een hagelstorm zo’n twee maanden aan de grond voor controle. Het zou ideaal zijn als het materiaal via sensoring zelf aangeeft waar het probleem zit.”
[/et_pb_testimonial][et_pb_text _builder_version=”3.12.2″]
Samen met een aantal studenten van de TU/e en eigen onderzoekers wordt er gezocht naar een manier om carbon composieten te laten ‘praten’. Van Gurp: “Niet alle schade is meteen zichtbaar na een val, uit voorzorg gooien mensen een fiets dan weg. Zonde. Door sensoren in een composiet te verwerken is het materiaal in staat aan te geven hoeveel kracht erop staat. Hierdoor kun je een waarschuwing instellen dat het tijd wordt om je fiets na te laten kijken.”
Op dit moment is zo’n toepassing in consumentenproducten veel te duur, maar in andere toepassingen ziet Van Gurp op korte termijn meer mogelijkheden: vliegtuigen. “Nu staat een vliegtuig 2 tot 3 maanden aan de grond als er een hagelstorm geweest is. Omdat je de schade niet altijd kunt zien wordt alles nauwkeurig nagelopen. Dat kost veel tijd en geld. Het zou ideaal zijn als het materiaal via sensoring ‘aangeeft’ waar het probleem zit.”
[/et_pb_text][et_pb_image _builder_version=”3.12.2″ src=”https://media.innovationorigins.com/2018/12/brightlands074.jpg” /][/et_pb_column][/et_pb_row][/et_pb_section]