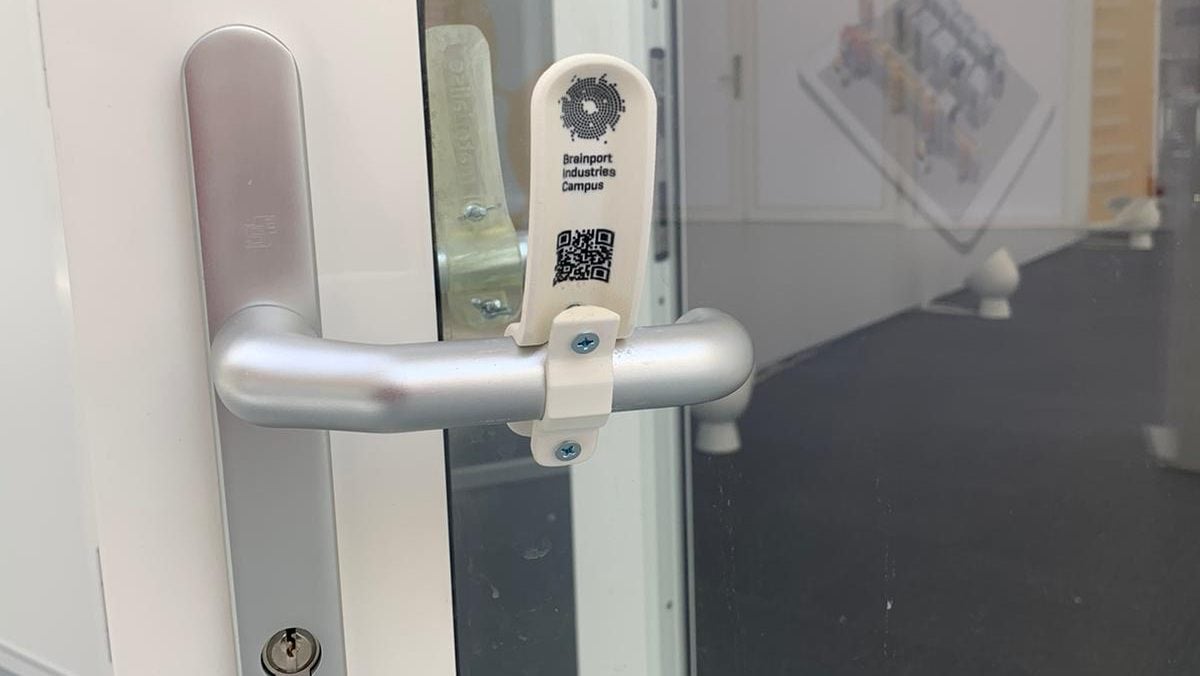
De kans dat je wordt besmet met het coronavirus via een deurklink is klein, maar niet onmogelijk (volgens het RIVM). Dat is ook wat Maarten van Dijk, founder van Additive Center en Maikel de Wit, director Marketiger, dachten toen ze een aangepaste deurklink ontwikkelden. Met deze 3D-geprinte klink kun je de deur openen met je onderarm en hoef je niets met je hand aan te raken.
Op Brainport Industries Campus (BIC) worden vandaag de eerste twintig deuren in de algemene ruimtes voorzien van de 3D-geprinte deuropener. Afhankelijk van nieuwe maatregelen en of bijvoorbeeld de scholen weer open mogen na 6 april, volgen meerdere deuren op de campus. “Het originele ontwerp is een open-source design van Materialise, wij hebben dit met onze kleuren 3D-printers naar een nieuw niveau getild. De anti-coronaklink wordt hier op BIC geproduceerd en voor het eerst uitgerold. Bedrijven willen toch het zekere voor het onzekere nemen. Ze vinden het ook belangrijk dat ze naar klanten uitstralen dat ze er alles aan doen om productie veilig te stellen”, laat Van Dijk telefonisch weten.
Ook campusdirecteur Erik Veurink ondersteunt het initiatief en geeft aan trots te zijn. “Wij hebben veiligheid en gezondheid hoog in het vaandel staan. En dat huurders in deze moeilijke periode hun steentje bij dragen juichen we alleen maar toe. Dus ook in deze hectische en ongewone situatie gaat innovatie op BIC “gewoon” door. Daarom hebben we vanuit campusmanagement opdracht gegeven om alle openbare ruimtes van deze klink te voorzien.”
Marketiger print de deurstukken in één stuk en kan variëren in kleur of personalisatie zoals bedrijfslogo’s. “Voor nu komt er een QR-code die linkt naar de site van het RIVM, zodat mensen die op de campus zijn altijd de laatste informatie kunnen checken. Maar je kunt er ook hele andere dingen op printen. Allerlei verschillende klinken worden met honderden tegelijk geproduceerd. Dat duurt telkens ongeveer een dag”, zegt Van Dijk.
Oplossingen voor lastige situatie
Net als in de rest van wereld is ook op de campus de activiteit beperkt tot een absoluut minimum. Maar dat wil niet zeggen dat de productie stilligt. Veurink: “Producerende bedrijven als KMWE en Anteryon zijn fysiek nog in bedrijf. Veel bedrijven hebben gehoor gegeven aan de oproep om maximaal vanuit huis te werken, waardoor het hier een stuk rustiger is.” Ook bij Additive Center merken ze dit en werken ze aan oplossingen.
Zo is Van Dijk bezig om het curriculum voor training in bijvoorbeeld 3D-metaalprinten online beschikbaar te maken. “Normaal gesproken zit je met engineers van verschillende bedrijven bij elkaar, maar dat mag niet meer. We werken er nu hard aan om lesmateriaal digitaal te krijgen, zodat engineers dit toch thuis kunnen maken en hun concepten via een conferencecall kunnen bespreken. Het is ook belangrijk dat ze daar feedback op krijgen.”
Tijd en rust, maar ook financiële druk
Volgens Van Dijk wordt het bedrijf nu toch wat vaker gebeld door bedrijven die een onderdeel niet geleverd krijgen. “Ze willen dan weten of wij het kunnen 3D-printen. Vaak gaat het om onderdelen die in serie een paar euro kosten. Maar als je dit gaat printen kost het vaak wat meer. Het ligt eraan hoe essentieel zo’n onderdeel is of het dan uiteindelijk geprint gaat worden. Want stilstaande machines kosten nu eenmaal veel geld.”
Zelf anticipeerde Van Dijk begin dit jaar al op de situatie. “We merkten dat bepaalde onderdelen toch lastiger te krijgen waren. Daar hebben we op ingespeeld en contact gelegd met onze toeleverancier of er nog voldoende reserve-onderdelen op voorraad waren bijvoorbeeld. Je wilt niet dat de boel stil komt te staan. Maar het blijft een bizarre situatie. Je moet creatief zijn en er het beste van maken. Aan de ene kant heb je daar de rust en tijd voor, maar je hebt wel de financiële druk. Die combinatie dwingt je om te ondernemen.”
Voor urgente onderdelen (medisch maar ook andere) is er een speciaal portal ingericht: www.additivecenter.com/hulplijn