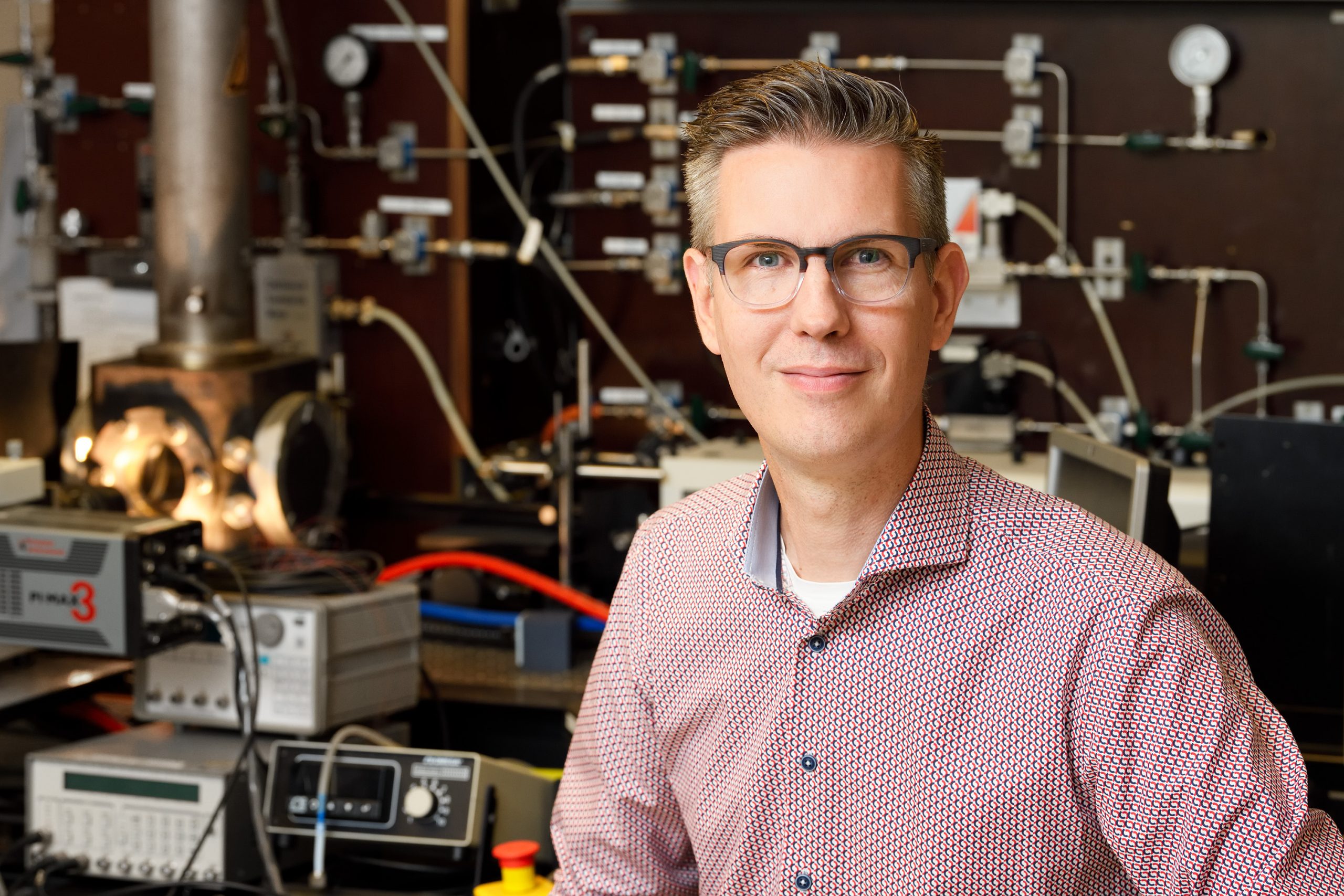
Iron as the new gold as far as energy sources go. Is that really feasible? In any event, this is the aim of Niels Deen, Professor of Power & Flow at the Faculty of Mechanical Engineering at the Eindhoven University of Technology (TU/e, the Netherlands). He is conducting research into this in collaboration with the recently established Eindhoven Institute for Renewable Energy Systems (EIRES).
It is already possible to extract CO2-free energy from iron granules as fine as powdered sugar by burning them. In this process, a cloud of iron powder is ignited by a flame at the bottom of a tube. A fan then blows the cloud up through the tube. The heat released during the combustion of the iron powder cloud rises like a whirlwind and flows through the end at the highest point of the tube to a heat conduit for industrial use. The burnt iron powder is driven by the whirlwind to the outside of the tube and is shunted through a hole to a (lower) conduit. It ends up there because the burnt powder is heavier than the hot air.
How do you fully remove the rust out of there?
The iron granules are oxidized during combustion which causes them to turn into grains of rust. As a result, they lose their capacity to oxidize or burn all over again. So, the trick is to make sure that the iron and the oxygen molecules are pulled apart from each other once more. This is also possible now. It is done by adding hydrogen to the rusty iron powder at a certain temperature. During that process, the oxygen molecules on the rust grains attach themselves to the hydrogen molecules, eventually creating a quantity of water and some iron.
The only problem now is that it is not entirely clear under what conditions and at what temperature the rust grains need to be purified 100 percent and separated from the oxygen, says Deen. “They are very small grains. They have a diameter of a mere 20 micrometers, practically invisible. It’s therefore not easy to see whether the rust has been removed down to the very core. What’s more, they melt at a certain temperature, so they are no longer grains then.”
The problem with grains that are not made entirely of iron is that they are less efficient. This means that their capacity to oxidize (or rust) is lower and they generate less heat than if they were made up of pure iron molecules. This is why it is very important to perfect this process.
Not a single grain should be wasted
A second prerequisite for energy generation where iron powder is used as an energy carrier is that all the iron powder burned in the process should also be captured by the system. Deen states that this has not yet been fully achieved. “Suppose that during the process you lose 1 percent of the iron powder because it ends up in the hot air shaft. Then after a hundred rounds of operation, you’ll have lost your entire starting stock of iron powder.”
The problem with that is not that the iron powder is expensive to make. Iron is one of the most common metals in the world. However, it does require a lot of energy to make it, Deen says. While the goal is to use energy sources more efficiently and to produce in a circular way.
If perfecting the process succeeds, it solves a huge problem. “Iron powder can then become the energy carrier in coal-fired power stations. The process is not quite the same. But there are plenty of similarities. Coal power stations also burn fine coal powder. Whole chunks of coal aren’t used in those plants either. However, an extra system will have to be added to make the plants compatible for burning iron powder.”
The principle of rocket fuel
It would provide a solution for owners of coal-fired power plants, such as Uniper, which is investing in the development of the technology by the TU/e.
The technology is still relatively young, Deen notes. “We have only been working on it for a year or two. The initiative came from Philip de Goey, a professor of combustion technology at TU/e with a track record of research that is known worldwide, Deen adds. He had read about research that is being done at McGill University in Canada into the use of metal powder as rocket fuel and thought it could be developed as an energy carrier for industry. He received a grant this year from the European Research Council amounting to 2.5 million euros.
There are no other universities or institutes in the world that are researching the use of iron powder as an energy carrier, according to Deen. This makes it a unique experiment, and in October, the first pilot plant was put into operation at the Bavaria brewery in Lieshout, near Eindhoven.
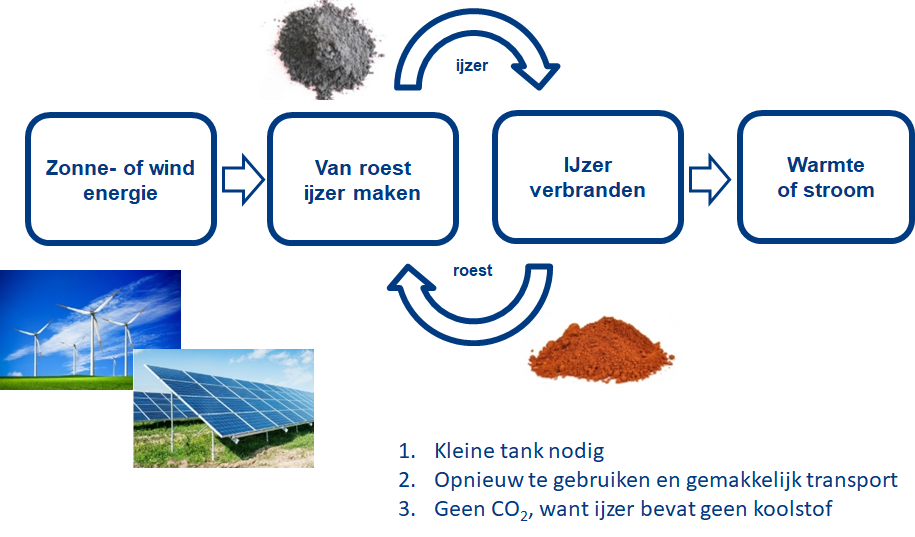
The development of metal fuels is one of the four iconic projects that the Eindhoven Institute for Renewable Energy Systems (EIRES) is focused on. EIRES was set up in 2020 by the TU/e. Other projects concern the further development of salt batteries to store sustainably generated heat and the development of affordable eletrolyzers. Digital models are also under development (digital twins) so that insight can be gained into the best choice for new technologies that have been developed during the energy transition. These choices must be made before 2050.