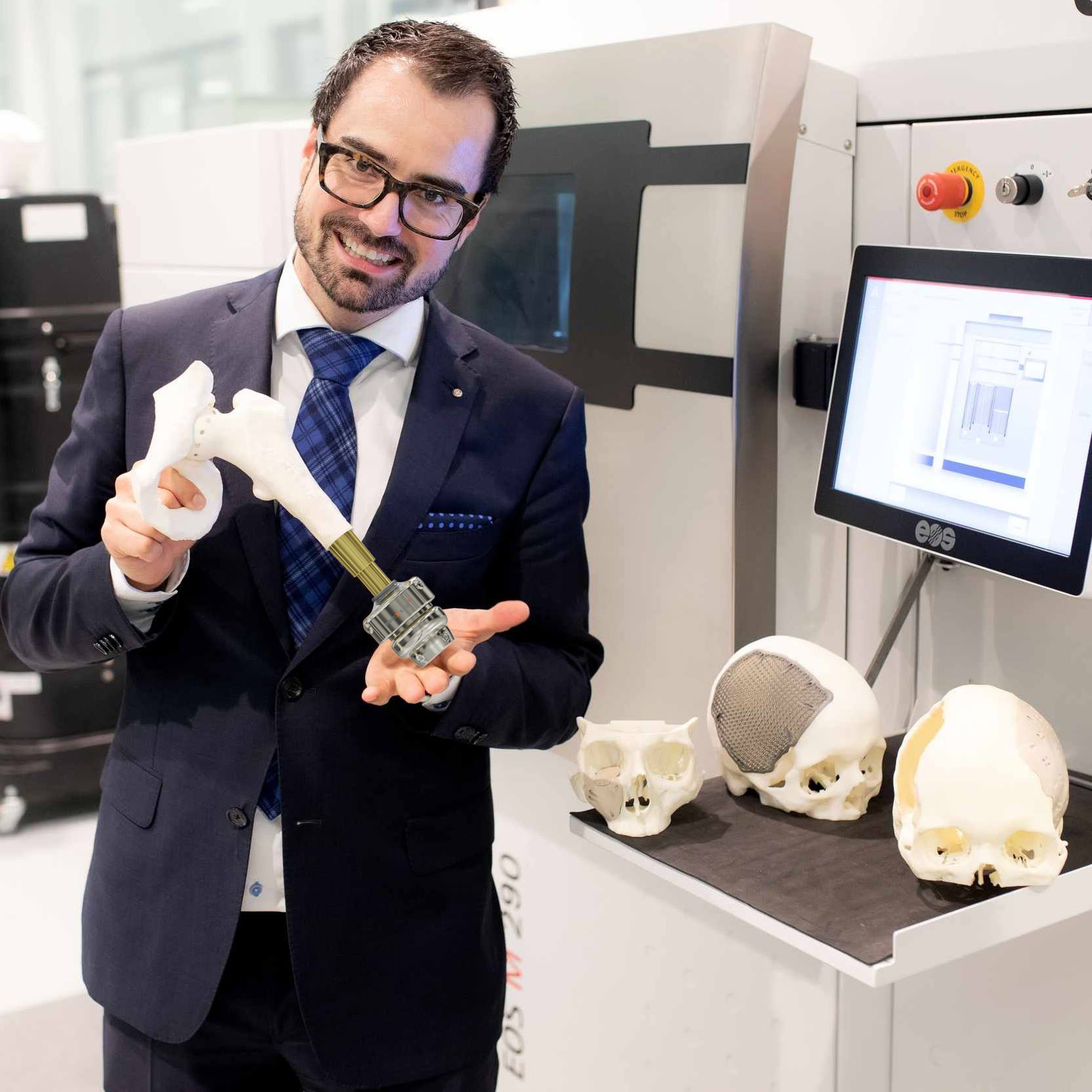
Some people have a hobby and work on it day and night. As far as Maikel Beerens is concerned, that’s his company Xilloc, which he started after graduating in biomedical technology.
It has been around for nine years now and now there is a manufacturing factory inside the building of a former DSM workplace on the Brightlands Chemelot Campus in Geleen, the Netherlands. The factory is comprised of a range of equipment, the most important of which is the 3D printer that he and his team, which now has 11 employees, use to make implants for human bodies.
Their first implant was completed nine years ago: A plate made of biocompatible plastic. This is material that living tissue responds well to and that can be implanted into the skull after part of the bone has been removed due to a tumor, for example.
Dent in your skull
Before the Xilloc implant came into existence, patients who had a tumor in their cranial bone were fitted with a clay implant, Beerens explains. This is a difficult thing to make. It often failed to fit properly, causing the patient to experience discomfort after surgery. In films that have been recorded with patients and are available on YouTube, you can see that they suffer from headaches and an odd-looking dent in their skulls.
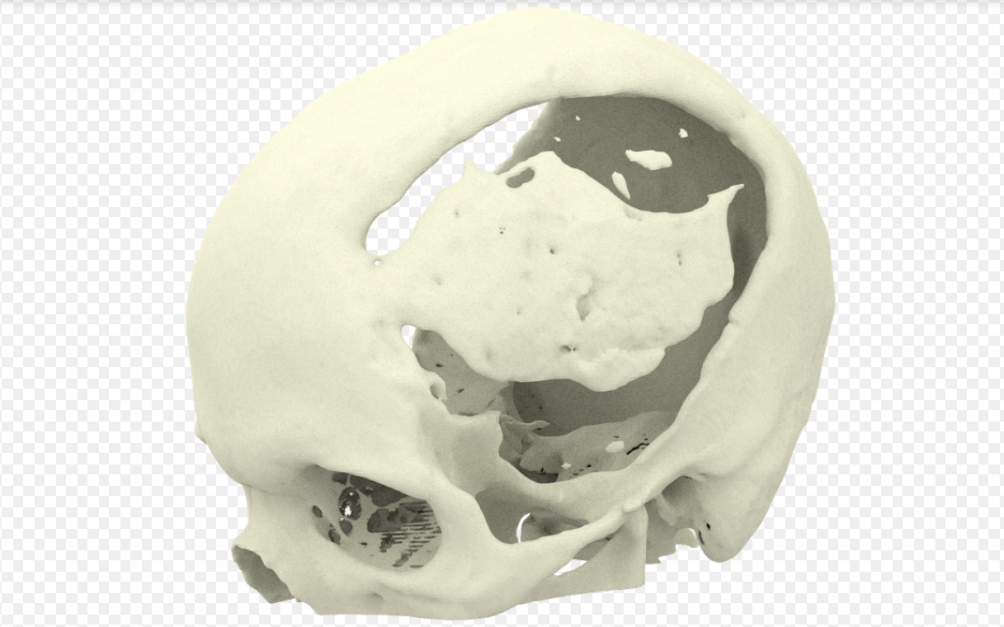
As a result of Xilloc’s work method, none of this is necessary anymore. The doctor sends the patient’s data digitally to Xilloc, including a CT scan of their skull. Xilloc then creates a design for the implant. Once the doctor approves it, Xilloc prints the implant using the 3D printer and finishes it off with the equipment that makes the product smoother and the printed structure stronger. “Recently, we delivered an implant 24 hours after it was ordered,” Beerens says.
Not only does Xilloc supply the implants needed to cover gaps in a skull after surgery. The start-up also makes a surgical guide that the surgeon uses to cut away the tumor. The surgeon screws it onto the skull and then cuts through it with a saw so that the cut bone is exactly the same shape as the implant. This is then immediately attached. In the past, the patient had to undergo surgery again for this, often two weeks later,” Beerens goes on to say. Therefore, with Xilloc’s product, the patient heals faster and much better from the operation.
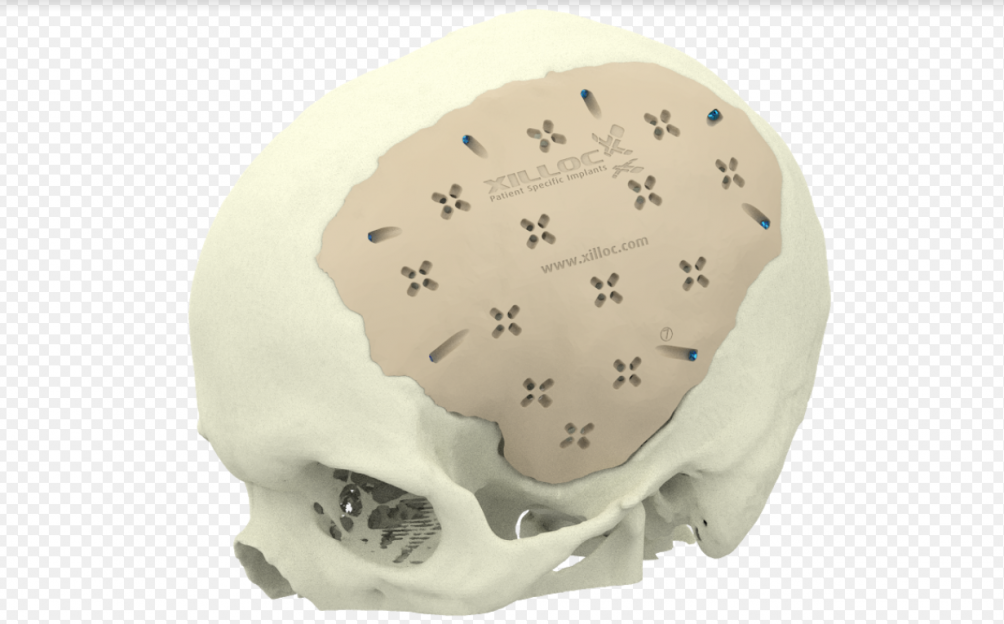
Biomedical cluster
But why is the manufacturing factory located specifically on the Brightlands Chemelot Campus in Geleen? “There is a biomedical cluster of companies here,” Beerens notes. This ties in with the activities of the original owner of the site, DSM, which has a large biomedical branch.
Without Chemelot’s investment in the pilot plant, Beerens would not have been able to develop his start-up into the company that Xilloc is today. “It took millions of Euros to buy the 3D printer and the other equipment in the factory. We could never have been able to afford that. Nor is it that easy to find investors for this kind of venture either. They want to see if it works in practice first. While you’re spending the first few years actually developing the product. Then it has to go through a clinical trial. You won’t make a lot of turnover with this kind of product during those periods.”
Beerens states that Xilloc is now becoming a scale-up. This means that production can be stepped up and that Xilloc is actively launching its products on the market.
3D-printed jaw
Not only does the company supply cranial implants and associated surgical guides for saws to surgeons. There are twelve product families, ranging from a titanium pin that can be inserted into a leg and which a prosthetic can be screwed onto, to a 3D-printed jaw joint. “We’ve worked on this for years, together with the (Dutch) University of Groningen. At a later stage, we tested them in studies set up for that purpose and conducted a clinical trial. We managed to deliver the first mandible back in April.”
Xilloc does not have much competition, Beerens adds. At least not in Europe. “We supply 81 hospitals across 15 different countries.”
If it hadn’t been for the investment from Brightlands, the Rabobank, the province of South Limburg, and two private investors who believed in his product, Beerens suspects that his business would never have gotten off the ground. “I’d spoken to a number of venture capitalists who said they wanted to wait. I think they might regret their decision now.”