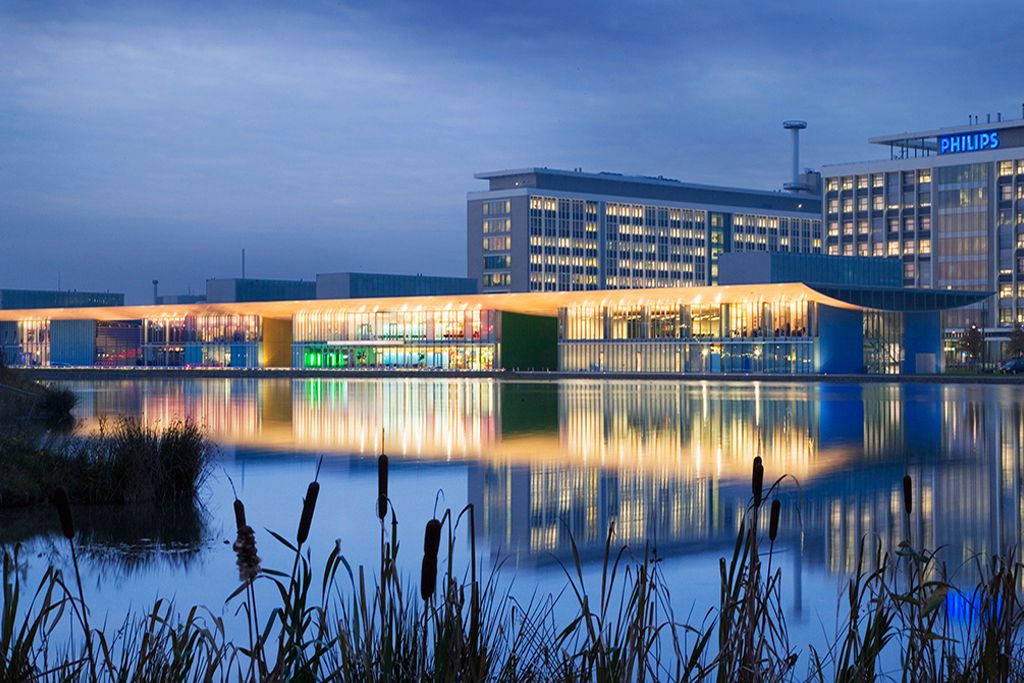
A lights out factory, where machines autonomously produce the right type of chip for the right customer, where production carries on after the lights have been switched off. That’s the dream of Jan Driessen, smart manufacturing architect at Nexperia. Driessen is working on a smart factory together with the AI-enabled Manufacturing and Maintance-lab (AIMM) at Eindhoven University of Technology (TU/e).
They also work with PhD students, who are doing their research inside the factory and at the university. Like Jelle Adan, who completed his doctoral research last month. He developed smart algorithms that automatically translate customer orders into scheduling.
Nexperia makes semiconductors and components for electronic products such as an electric car, laptops and smartphones. Annually, the company ships more than 90 billion integrated circuits (ICs) around the world. The head office is in the Dutch city of Nijmegen, the chips are produced in factories in Europe and Asia. For example, at the High Tech Campus in Eindhoven.
Transistors and diodes
These tiny products are most likely in your smartphone. Driessen: “If you touched your phone with your hand and our components were not in it, the static electricity that is on your hand could blow up the chips. Our transistors and diodes have the ability to capture that static.”
PhD student Jelle Adan looked at part of the ‘creation process’, as he calls it. How does a customer order come in? And how does the translation to a work order take place? That work order dictates which machines are needed to make the chip that has been ordered. Jelle Adan: “A lot is now being done by hand. A team of planners uses Excel to plan. The process relies heavily on the expertise and experience of those planners.”
It costs a lot of money to run a machine, Jelle Adan continues. ” In order to manufacture more, we can’t just add a new machine,” Driessen adds. “Nexperia has an output of about a thousand different types of chips. These all have separate formulas with different processing techniques. Every customer wants something slightly different.”
Chaos
Driessen wants to be able to manage ‘that huge chaos of customer orders.’ “How do you make sure that you deliver everything on time? That’s going to be an ever-increasing challenge. We’re already under enormous pressure with the rising demand for chips for electric vehicles.”
Artificial Intellingence can, according to Driessen, provide 1 or 1.5 percent in extra profit margins. “On a manufacturing process with more than 90 billion products per year, or about 3 thousand per second, that’s a tremendous gain.”
Ivo Adan, professor of Manufacturing at TU/e: “What we are aiming for is to get more capacity out of the factory. Not by making the factory bigger, but by managing the production process more intelligently. By using the data in a smart way, and by creating an autonomous factory. Jelle has made strides in this area. What was previously done manually has been automated and with that data we can improve the process even further.”
Packaging
These various process steps and criteria and the available capacity of the machines must be matched as rigorously as possible, Jelle Adan adds. “For each step, there are a lot of production-specific choices. Among other things, you need lithography machines and etching machines to be able to fabricate a wafer. Depending on the end product, for example, 100 thousand diodes can be placed on it. Before you can sell it to a customer, it’s got to be packaged first. So these steps involve cutting, gluing, attaching wires and encasing it in some kind of plastic. I managed to optimize those steps.”
Working with algorithms also generates real-time feedback. Ivo Adan: “We can use the data coming from the machines to immediately see what we need to do and how we need to go about it. If there is a deviation, there may be a good reason for it, but we do need to know that then.”
Will there eventually be no need for people at all? According to Driessen: “Perhaps in the most ideal situation. But you have to be able to interpret the numbers that come out of those algorithms. For instance, when a machine starts. In one, that’s when it’s charged and in another, when the first processing operation occurs. Which could be the same for an algorithm, so that nuance is key. You can stick your foot in it otherwise and make the wrong decision. That’s why we will still need people who are able to properly translate and manage the data flow back and forth between the work floor and the IT systems.”
Moving train
According to Driessen, an additional challenge is that you are not building a new factory, but trying to further automate an existing one that has already been running for 20 years. “People who have been working the same way for years are reluctant to make those kinds of changes. You’re trying to make modifications on a moving train.”
The corona pandemic prevented Jelle Adan from visiting the factories in Asia. Time differences and online sessions made it all the more difficult to make adjustments to that ‘thundering train’, Driessen points out.
Conducting research in the factory makes a PhD student like Jelle Adan understand real-world practices more thoroughly. He can see on site what is really needed. “Scientific research usually focuses on staged problems. Because I work at Nexperia and go to university, I am forced to look for what we can really use. To make those tweaks that are needed for it to be usable.”
Ivo Adan: “It is when you actually take a good look at the industry that this leads to some really fine fundamental research. It’s really not the case that we are just solving industry’s mundane problems. We look ahead together with industry. We jointly formulate sound scientific questions that are also relevant to industry. That’s what we have to work on over the next four years.”
Far away
Jelle Adan’s PhD research has now come to an end. He aims to implement the results of his research within Nexperia in the near future. The next PhD student is already ready and waiting. They are set to continue on with the maintenance of the machines. Driessen: “Just like your car needs to go to the garage for maintenance. Parts of the machines must also be replaced so that they can keep running. We want to make maintenance predictable. Sometimes machines are down because something breaks that we didn’t see coming.” Driessen wants to prevent that and link maintenance to the times when the right people are there to do the right kind of work.
Although the idea is that Jelle will stay with Nexperia for the time being, Driessen says. “We’ve taken some fine steps, but in fact, it never finishes. That speck on the horizon, a lights out factory, where production continues when the people have gone home, is still a long way off.”