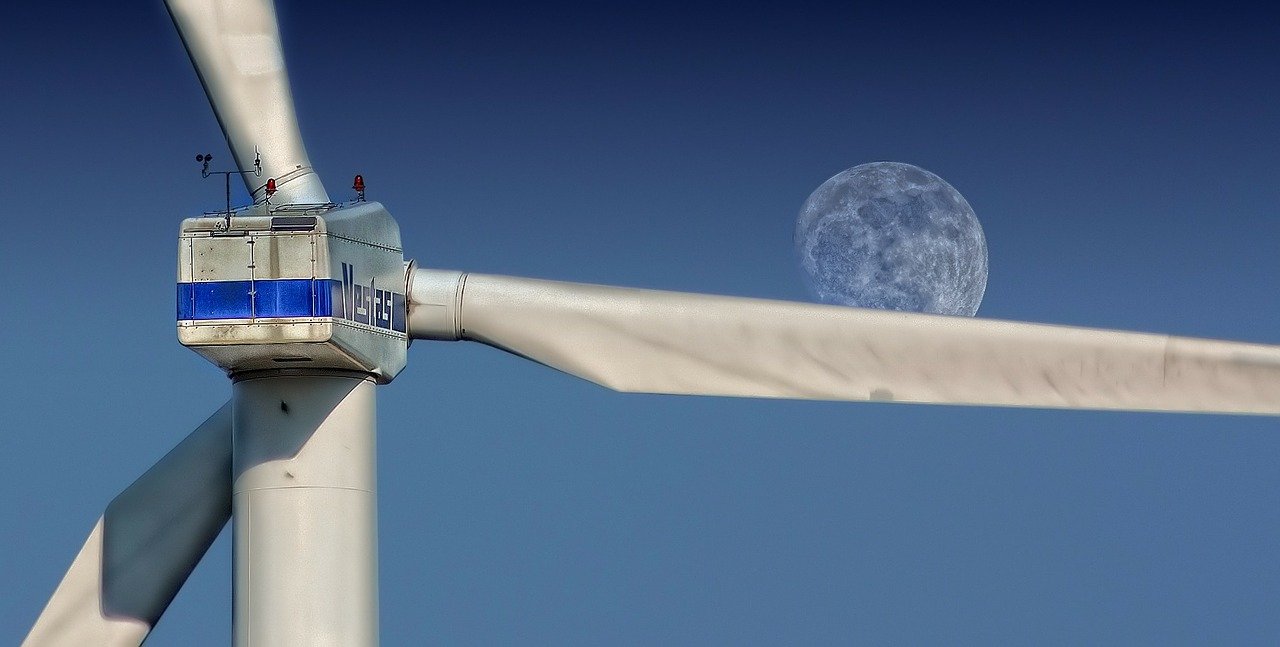
The Netherlands is increasingly focusing on green energy, and new wind turbines are being built at a rapid pace, both on land and at sea. But what should be done with the wind turbine blades when they are decommissioned? A circular recycling process has been set up in Eemshaven in Groningen, which covers everything from dismantling these rotor blades to reusing the raw materials. “You can use them in 3D printers and countless other applications,” says Maaike van Heeren, communications consultant at Chemport Europe, an incubator for green chemistry, which is involved in the project.
Anyone who thinks about wind turbines soon imagines a clean environment. Although wind energy is making an indispensable contribution to the energy transition, the actual recycling of the blades is far from sustainable. They usually end up in a landfill or in an incinerator and are still rarely reused for high-end applications. This is now about to change in Groningen. Various companies, organizations and educational institutions are joining forces to set up the Decom North consortium. The aim is to make recycling viable. This is quite a daunting task: the blades are made of composite, a material as strong as steel. Yet it can be done. Chemport Europe, Groningen Seaports and the Offshore Wind Innovation Centre, among others, all play an important role in the establishment of the consortium.
An entire chain
“Recycling composites is not new,” van Heeren points out. “But it is new that an entire chain is being set up. From dismantling, the logistics, the processing of the composites, to making new raw materials and doing research into high-end applications: it’s all happening here in Groningen.” The ultimate goal is clear. “Windmills for windmills,” says van Heeren. “However, that is not possible at the moment, because as soon as you cut into the blades, the strength goes out of the material, which is made of fiberglass and resin. Eventually, though, it should be possible. But until that time, countless other applications are possible. The great thing about this is that it is already happening – processing blades into new products. So, as a result, CO2 is being saved right now.”
Pilot plant
In a brand new pilot plant in Eemshaven, where the blades are chemically recycled, there is scope for researchers and students as part of the Knowledge-based High-value Applications Project. This project is looking for applications that are of the highest possible quality. Students from Windesheim University of Applied Sciences, Stenden and Hanze University of Applied Sciences, among others, are able to work on projects at the pilot plant. “I think it’s really cool that students from the region are involved and can contribute to the energy transition this way,” says Van Heeren. Students are able to work on different research questions. “What are all the materials that can be used? What properties does a certain raw material have? And how much CO2 can you actually save? I can see plenty of opportunities for the students.”
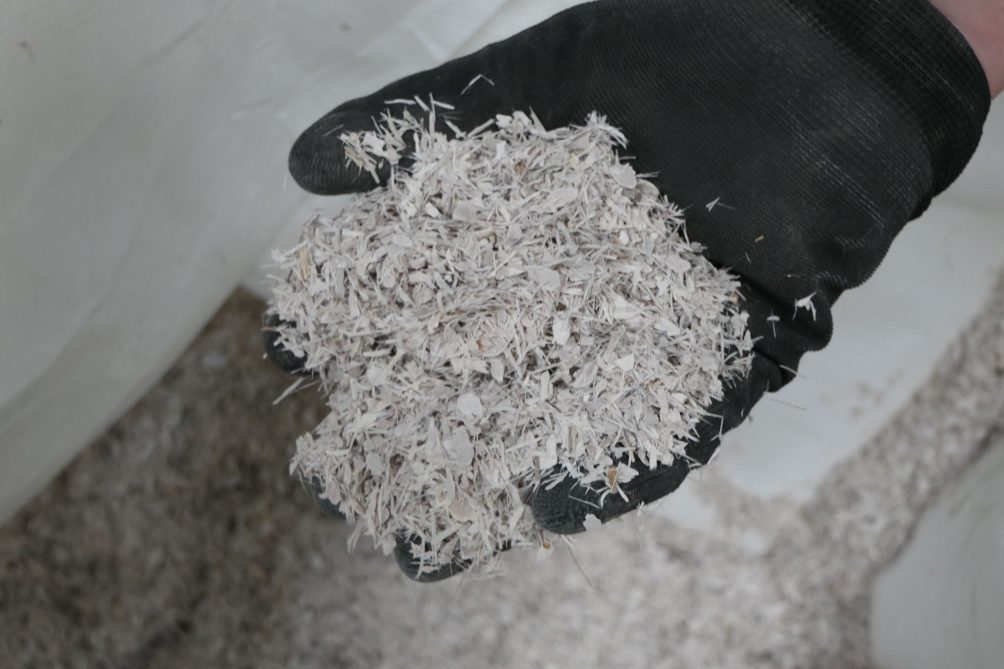
Shoring up shoreline banks and construction materials
Sylvia Oomen, managing director of Circular Recycling Company (CRC) is involved in the pilot plant that is coming to Eemshaven. “The aim of the plant is to make raw materials when recycling the blades and to cut down on CO2 in the process. Applications are possible in shoreline revetments (ed. a revetment serves as a protection for a shoreline bank, to protect against, among other things, wave motion). Often posts are installed there that are made of tropical hardwood. We can use raw materials from the pilot plant instead. In addition, a company like Nedcam from Heerenveen can use raw materials for printing objects in 3D. I am also excited about applications in the construction industry. The construction industry has traditionally not been particularly circular. We can use our raw materials to make more sustainable plates and posts.”
Also interesting: Quickly detect damage in wind turbine blades with Tarucca’s AI
Tests and challenges
Before any of these applications become a reality, tests and calculations must be done first. Until that happens, the consortium is turning to Neocomp in Bremen. That company processes the cut-out fiberglass and synthetic resin rotor blades into cement. Oomen: “We face major challenges. We have to be able to supply consistent, dependable materials to the construction and automotive industries, for instance. That calls for complex calculations. And we must, for example, look at tensile forces on the material by doing casting tests whereby we work with molds.
In part due to these challenges, it will take some time before the fully circular ‘windmill for windmill’ process will be in place. “There is an insane amount of force on the blades of wind turbines. If your material is not consistent, and a blade is 10 percent heavier, then you are already contending with an energy yield that is significantly less. Eventually, it should be possible to find applications for wind turbines, but until then, we already have some great products that we can make.”
Just the beginning
Oomen envisages that similar projects will be launched elsewhere in the country over the coming years. “The project is completely in line with the targets set by the Netherlands to go green. As a consumer, if you find out that your green electricity is generated by a wind turbine that is subsequently incinerated or dumped and buried, that doesn’t make you very cheerful. I am confident that as a country we are becoming increasingly aware and are taking better care of the earth.”
You can read other stories about Groningen via this link.