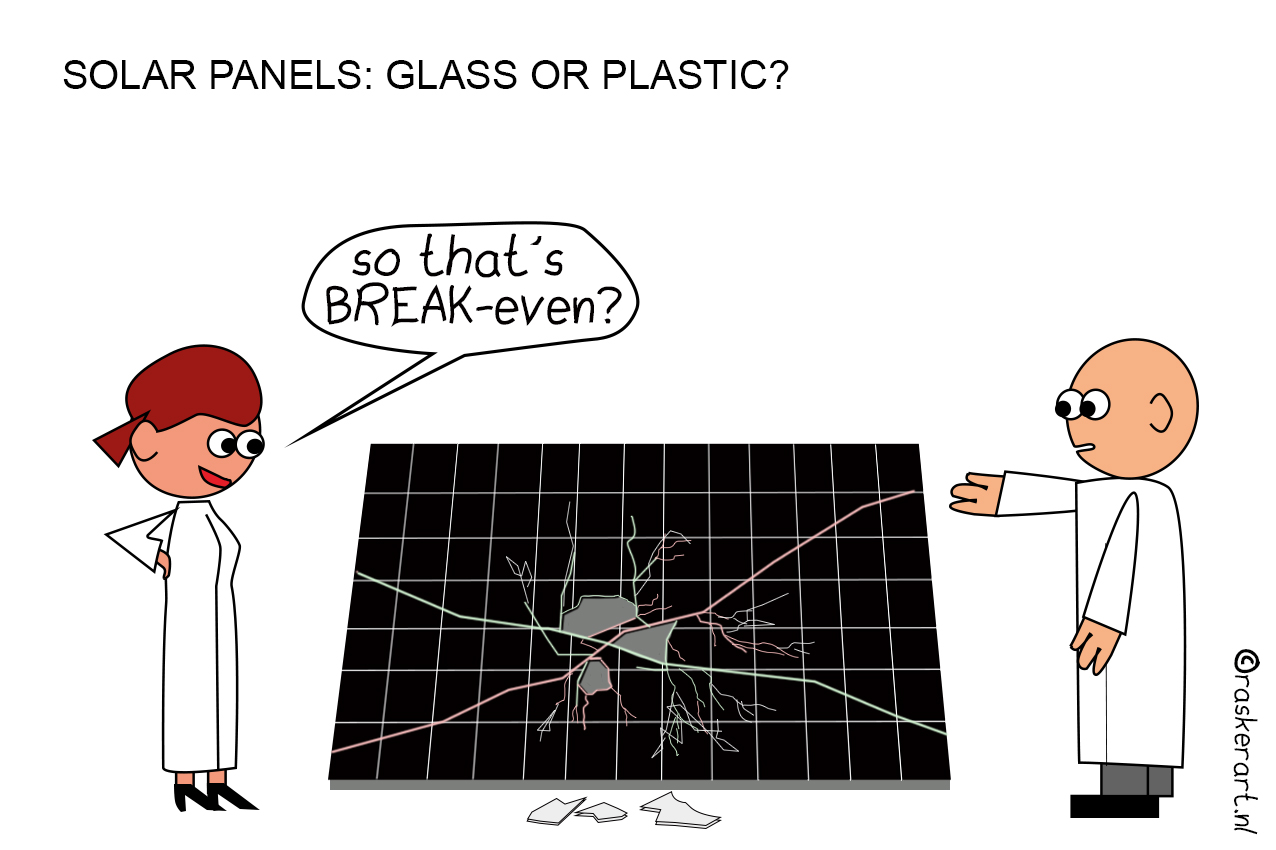
Only 12 percent of business premises that have a surface area larger than 1000 square meters have solar panels on their roofs. In The Netherlands, this amounts to more than 140,000 premises, which translates into approximately 38,000 hectares of roof area. Of all this roof surface area, not even 5,000 hectares is covered with solar panels, according to figures from the OverMorgen consultancy firm.
Even though plenty of entrepreneurs would like to install solar panels on their roofs, it is just not possible in some cases. For example, because their roof structure is not strong enough to support the weight of the panels. The Eindhoven-based start-up Solarge is one of the companies that has found a solution for this, which we wrote about last week.
The company makes solar panels that are half as light as traditional solar panels. How? By replacing glass with plastic, which also eliminates the need for an aluminum frame. To do this, the company combined the knowledge of SABIC (which developed a plastic that behaves in the same way as glass) with the expertise of Heijmans (which was able to apply the technique). The company plans to open a first factory for mass production in early 2022. It is expected that 500,000 square meters of solar panels should roll out of the factory each year.
Not impossible after all
It was long thought that replacing glass with plastic panels was impossible. According to Marc Koetse of the Netherlands Organisation for Applied Scientific Research (TNO), there are a number of reasons for this. Koetse works at TNO as part of the Solliance consortium on the integration of solar panels in products. Roof tiles, for instance. “Glass has a number of properties that are important for solar panels. First of all, it is fantastically transparent. Secondly, it is relatively inexpensive to produce and incredibly durable. You really have to do your best to break it over a period of 20 years.”
Another important property of glass is that it perfectly seals the solar cells from outdoor influences. “Take the most common solar panel. These are made of silicon solar cells which have metal contacts applied to them. If water and oxygen reach these contacts – especially when they are under a current – they will seriously corrode and your panel will break down. This is something you want to prevent. Glass blocks these influences and provides excellent protection for the solar cells. Plastic does not do this as well. It’s not for nothing that we eat tinned or glass-conserved vegetables,” explains Koetse.
According to Koetse, it therefore makes sense that glass is still the most widely used material in standard solar panels. “All those good properties of glass are hard to bring together in plastic. Historically – the first solar panels appeared about 50 years ago. We weren’t that far advanced with plastics back then.”
A little lecture on polymers
There has been a lot of experimentation with this over the years, Koetse knows. “There are quite a few industrial plastics that you are able to make just as transparent as glass. Those plastics you use to make bags or trays. But also acrylates, which you use to make Plexiglas. This is just not a particularly good candidate because it weakens in the sun. Heat makes it soft.”
Another problem with replacing glass with plastics, Koetse points out, is that they are flexible. Especially if they are thin plastic materials. “The sillicium solar cells in standard solar panels are rigid and fragile. You can’t bend them because they will then break. Solarge cleverly solves this by mounting a plate of stable composite plastic on the back.”
Glass is difficult to imitate
The main reason why glass is so difficult to replace, Koetse contends, is because the material’s various properties are difficult to imitate. ” It is possible, but you have to pull off all kinds of chemical tricks,” he says.
If you manage to do that, you can, in principle, achieve the same efficiency with a plastic sheet solar panel as you would with a ‘glass panel’. Koetse: “Temperature regulation only plays a very small role here, although there are materials on the market that are able to influence this positively. White backsheet, for example.”
Alternatives
In addition to Solarge’s ‘plastic solar panels’, there are other lightweight flexible alternatives available on the market. Good conversion efficiencies are currently being achieved with these. But Koetse explains that this market is not yet very extensive. At TNO, for example, they are working within the Solliance consortium on flexible solar panels, so-called solar films, and on ways to integrate these into products. “You can put solar panels on the roof, but what if they are integrated in a facade or in the roof tiles as well? Or in roads, bike lanes or acoustic barrier walls next to the highway? Because the price of these solar films is still relatively high, the demand is not very high either. As a consequence, they are not really breaking through. By using PV as a semi-finished product, we think we will be able to make a breakthrough.”
According to Koetse, this is because many of these solar panels are difficult to fabricate in an automated process. For example, current custom PV acoustic barriers that are currently being tested are all handcrafted. “The goal is to work towards semi-finished products that can be manufactured more intelligently and quickly.”
He sees opportunities in the EU for this smarter manufacturing process. “Integrating customized solar films into products such as building elements yields products that have a dual function. This is how you create extra added value. Europe is ideally placed to combine seemingly dissimilar production streams with each other by using smart manufacturing methods.”