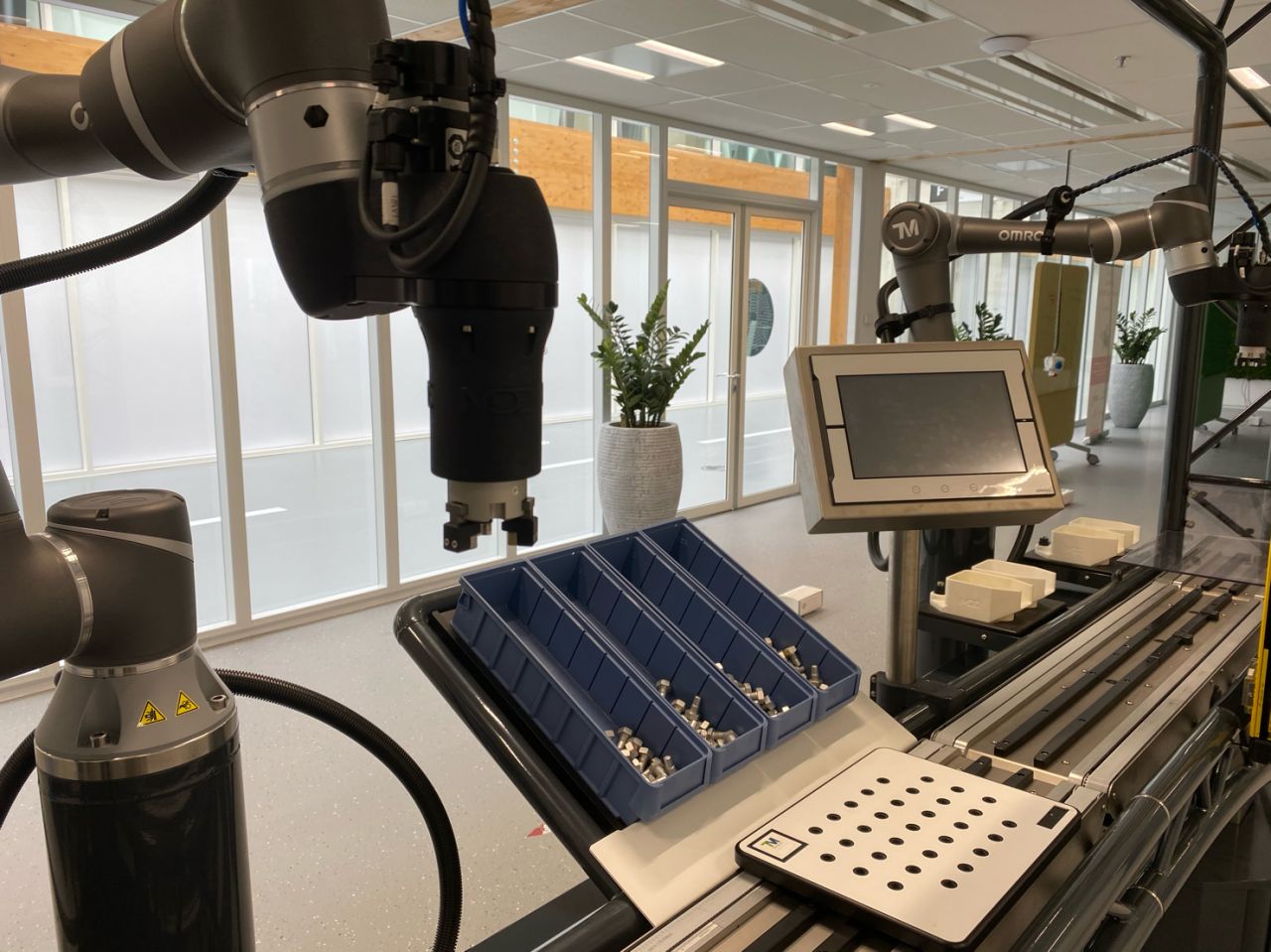
Better cooperation between humans and machines in manufacturing processes. This is exactly what Omron’s self-learning assembly line is trying to achieve. Omron is one of the world’s largest players in the field of industrial automation. Since recently, this demo is located in the Flexible Manufacturing field lab on the Brainport Industries Campus in the Netherlands.
The idea is based on the company’s table tennis robot Forpheus. This robot learns from the movements of human players and becomes better at the game that way. But instead of completely crushing a human opponent, the robot adjusts its level to that of the opponent and provides feedback so that the opponent can improve their game.
“This principle of learning from experts is now being applied to a factory,” explains Mariya Yurchenko, Omron’s data expert. “You have experts in some factories who have more than twenty years of experience. They know exactly what settings they need to adjust in a machine when, for example, the material changes. It’s like an extension of their body, so to speak. They can teach the machine that knowledge so that it ”knows” itself what the best way is to assemble a product.”
Showcasing the possibilities of machine learning
According to John Blankendaal, director of Brainport Industries, knowledge will be collected ‘at a very high level’. “Both parties participating in the flexible manufacturing field lab and graduates of the Eindhoven University of Technology (TU/e) are going to work on this. We also want to use this demo to showcase what is possible with machine learning. Companies that are wondering whether they can use this and what the next step is can visit the campus,” Blankendaal states.
In the field lab demo, the ‘product’ is made up of combinations of four different colors of screws. The machine analyzes the operators’ hand movements. Based on this, the robot puts together the perfect combination. “The machine takes everything into account. Does an operator use two hands? What’s the timing between the different steps? What mistakes do they make? The machine also looks at age, experience, and whether someone has already been working a long shift, for instance.”
Read more about the various field labs on the Brainport Industries Campus here.
You can deduce all kinds of things from all this data, Yurchenko notes. “If there is a lot of time in between various steps, someone might hesitate. Or does someone make more mistakes when on a night shift? We try to check whether all these assumptions are valid and we have developed a model for this. This is where all the data comes together. This is how the machine determines a ‘best practice’ in order to assemble a product as optimally as possible.”
Quest for the best way for machines and people to work together
This ‘best practice’, as Yurchenko describes it, is again used by the machine to support operators who have less experience. “Especially in the manufacturing industry where many product variations are involved, this can help prevent errors. Via the machine, the knowledge gained from experienced operators ends up with their colleagues who don’t know that much yet. Because of this cooperation between human and machine, the new operators learn much faster and they continue to be closely involved in their work.”
It is as yet not known when this self-learning assembly line can be put into practice. The preliminary research results are in, but there is still plenty to test and analyze. “The pandemic has slowed things down considerably. In order to test whether the model works, we need data and input from various experts, which has now become a bit more difficult.”
Nevertheless, Yurchenko is confident that things will work out: “The environment in which we work is a kind of playground where we figure out how robots and people can best work together. At the same time, we are working on real problems, engineers are constantly brainstorming along with us. They have ten other suggestions for each idea. That motivates us.”