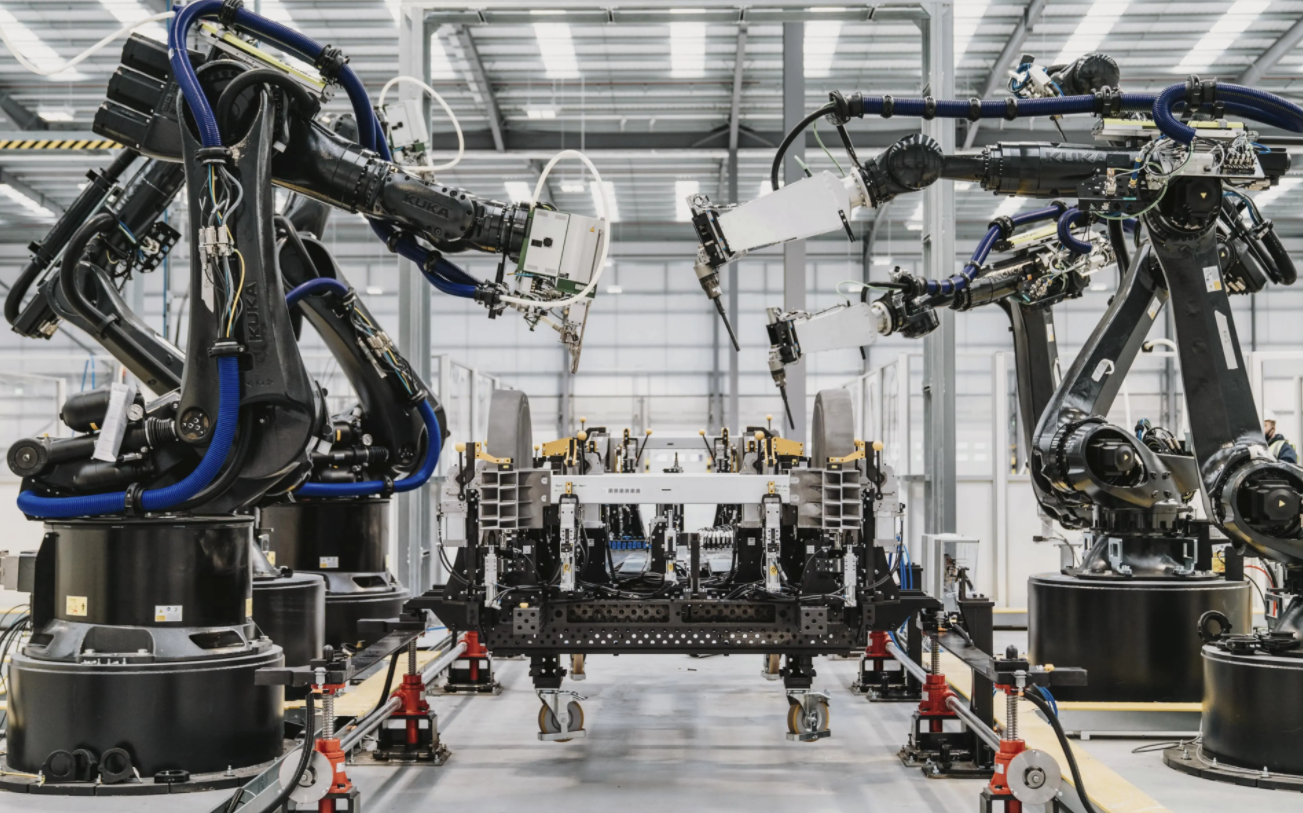
With the introduction of the Van, the young company Arrival is taking on the competition against existing manufacturers of commercial vehicles. Last week the Beta Van – an electric van – made its first appearance in Europe. Over the next few months, the van will be touring fifteen European cities in order to be introduced to the general public. The goal is to become the biggest player on the market.
The Beta Van is boxy in shape with rounded corners and a large, curved front section. The van looks gray and simple, even inside it has dispensed with every unnecessary knick knack. Arrival is a British-American start-up that manufactures electric, lightweight commercial vehicles. The prototype was built in collaboration with a number of logistics companies, including UPS. That company already placed an order for 10,000 vans, with an option for another 10,000.
Meanwhile, companies have already ordered around 60,000 vehicles, even before any of the vans have been driven on the road. In addition to the smaller Van, there are plans for three more vehicles: a passenger car, a larger van and a bus for passenger transport.
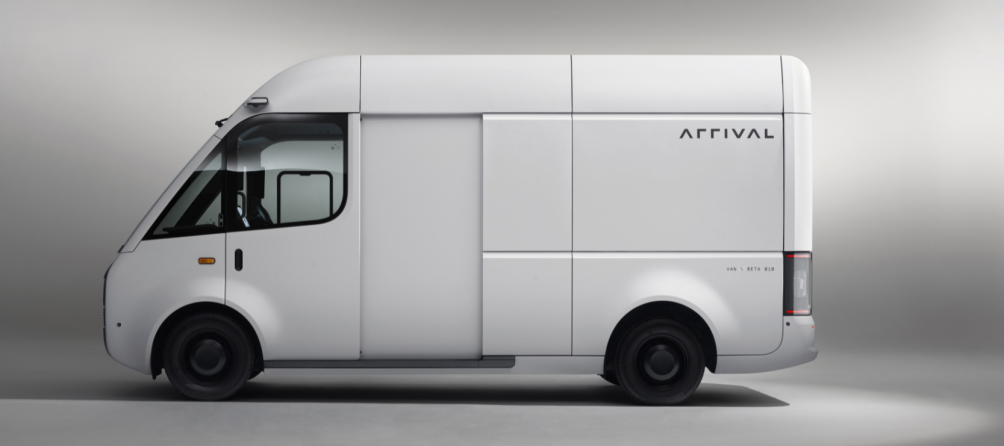
Cleaner air in larger cities
The company was founded six years ago by Bulgarian Denis Sverdlov with a clear mission: cleaner air, especially in larger cities. That’s why Arrival’s primary focus is on commercial vans and buses. “Customers around the world would like to drive electrically, but the fact is that they don’t know where to buy electric vans at a reasonable price, says David Ghione, Vice President of Sales at Arrival.
To be able to compete with fossil fuel vehicles, Arrival is taking a completely new approach, Ghione goes on to explain: “We do call our vehicles ‘bus’ and ‘van,’ but everything else is different. The manufacture, the technology and the material.”
A new manufacturing approach: micro-factories
One of the ways Arrival differs from other automobile manufacturers is in their approach to production. The company is introducing microfactories. These are built in places where demand for the vehicles is high. This helps keep the eco-footprint low, as well as the investment sum.
The factories are automated, but the real difference lies here: the machines are all connected and the entire factory uses AI to constantly react and adapt to ensure optimal productivity. “Arrival factories use autonomous, mobile robots that we developed ourselves. Whereas the bodywork of a car normally involves a thousand robot, the manufacture of a complete Arrival Van requires only seventy,” Ghione points out.
A microfactory can be housed in existing factory halls measuring 20,000 m2 – that’s about 24 times smaller than regular car factories. Small manufacturing hubs are installed in these spaces. One production hub can manufacture an entire vehicle. So, no more lengthy production lines or tight deadlines, just a set of components assembled by robots and humans. There are currently four of these types of factories here. By 2024, 31 should be operational, and by 2026 the plan is to scale up to 1,000 microfactories worldwide.
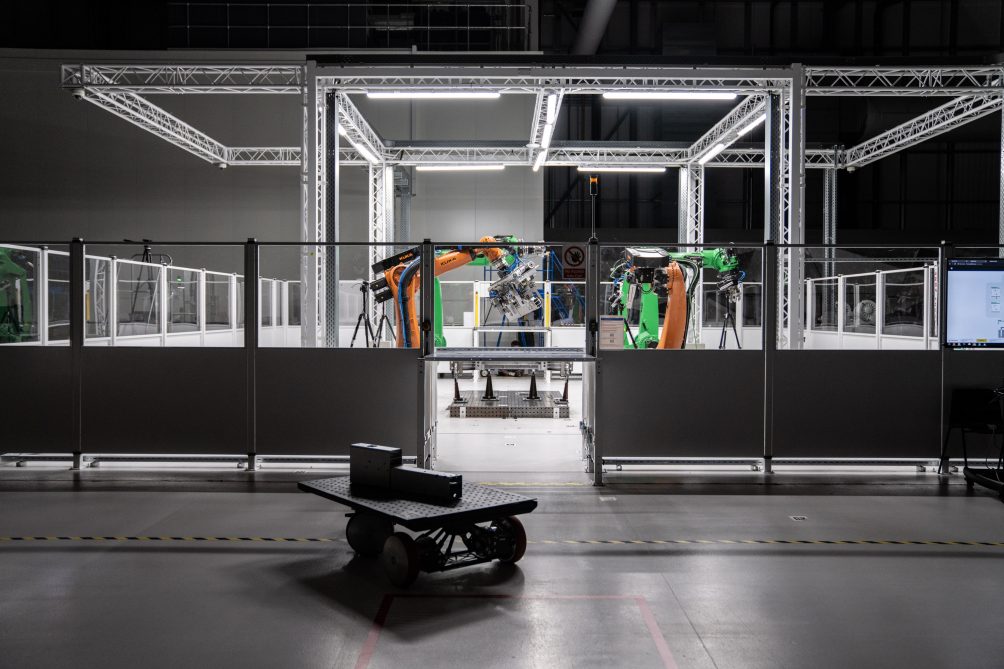
Flexibility
This manufacturing approach means that Arrival can respond easily to demand. Ghione: “This approach allows us to scale up very quickly. Moreover, we have developed modular components that are based on a network system. We use those components for all vehicles, so our manufacturing hubs are able to easily switch between different vehicles.
“Microfactories make our distribution and manufacturing cheaper, simpler and more sustainable. They are designed to last, and combined with Arrivals in-house hardware and software, we can keep the prices low and compete with fossil-fueled commercial vehicles,” Ghione adds.
Skateboard platform
Arrival builds the vans and bus on what the company calls a “skateboard platform” – a completely flat chassis on wheels that houses the battery and the engine. This enables the start-up to conveniently develop and produce new bodies for the platform base, as opposed to the years-long processes that traditional automobile manufacturers need to design different models.
Composite Materials
In addition, Arrival uses composite materials that are cheap, strong and lightweight. “The material is half as light as steel, yet durable and resistant to damage,” Ghione explains. A thick, structural adhesive joins the vehicle parts together, making labor-intensive and time-consuming welding processes a thing of the past. As to which reinforcement material is used, Ghione keeps his lips firmly sealed. “The driving force was to design a material that we can work with under low pressure. It is fully recyclable, we are trying to build a circular economy for our manufacturing processes.”
Would you like to read more about electric driving? Take a look here.