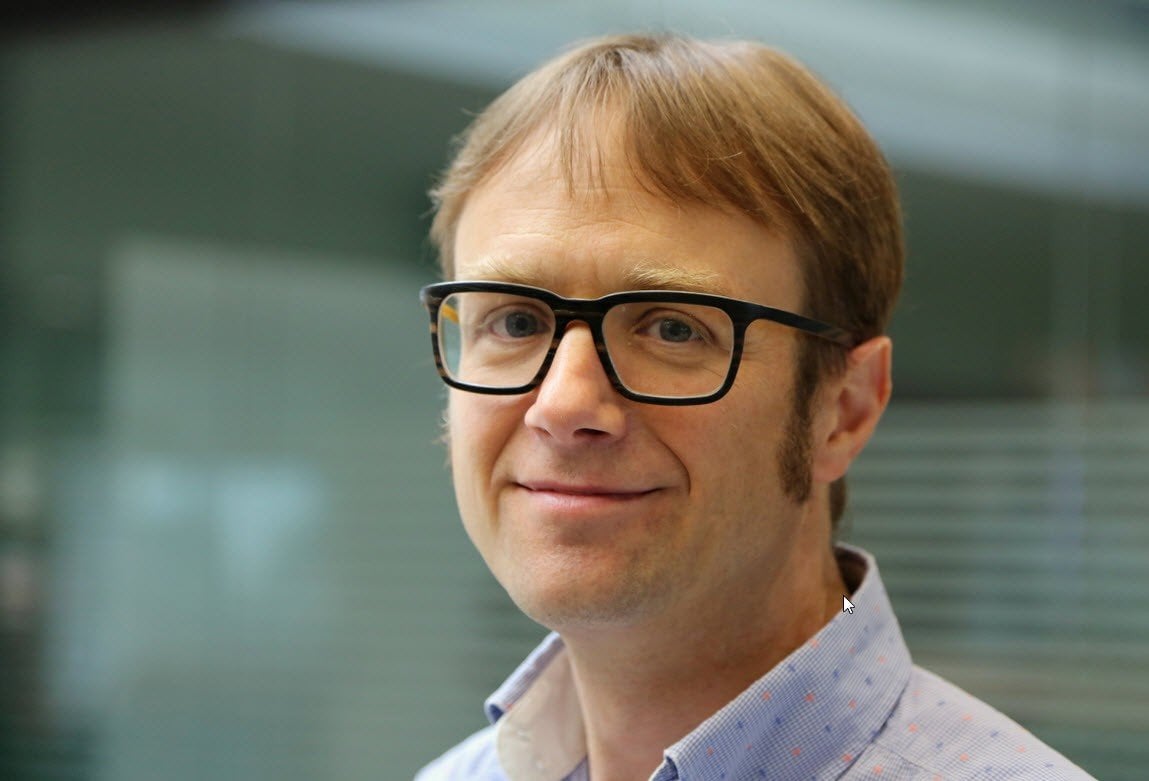
Two important European projects to take photonics to a next level have just started, both being led by the Eindhoven University of Technology. InPulse is one of them, JePPIX is the other. Professor Kevin Williams is Chair of the Photonic Integration research group. On the eve of Photonics West in San Francisco, he explained to Jonathan Marks the thinking behind the two projects, why they are needed now and how they fit in with other initiatives across the European Photonics Ecosystem.
More IO-reporting on the important developments in photonics here
What is the purpose of InPulse, โ it sounds like a โJePPIX 2.0โ?
Thatโs a nice way of thinking about it. It starts by taking what the Joint European Platform for Photonic Integration of Components and Circuits (JePPIX) has today โ which is a chip prototyping service. That means we have an ability to design and make a photonics chip, and then check whether it does what you expect it to do. InPulse enables the next step. It takes the chip from concept into something manufacturable.
This step from concept to manufacturable component requires robust, predictable performance and gets you to a stage where businesses can start assembling modules and shipping them to their customers. Business partners in InPulse like Technobis in Alkmaar can then confidently expect what their supply chain can provide them with. They can more accurately predict what that performance levels and yields are going to be. That allows them to build a business and enter into new markets.
InPulse enables the next step. It takes the chip from concept into something manufacturable.

Now, this starts as a four-year Horizon 2020 research project. But it sounds like it is the start of a much broader industry development programme.
Yes, absolutely. We have known for some time that Indium Phosphide Photonic ICs (PICS) have possibilities in many market segments. But so far, they have only broken through in high-performance communication. There are already Photonic Integrated Chips in mass production for that sort of environment.
But we see growing opportunities in Sensing, Imaging, Quantum and Terahertz applications. But the challenge has been that innovators in this space have not had access to high-reliability, high-performance technologies. They havenโt had the skills or the resources to work efficiently towards product releases.
Drastically reducing development time
In InPulse, our goal is to accelerate that process. Weโre currently experiencing timelines of the order of years to go from concept to the first prototypes and in-situ testing with customers. That clearly is too long, with product life cycles shrinking all the time. We think we can drastically reduce that development process to around two years by accelerating the fabrication process, and by making the design tools tightly coupled to the volume manufacturing process.
That means building on existing software tools for chip designers, so they can better predict the spread you might have in performance and get a feel quite early on of what this means for yield and the achievable specifications of their circuits. Also, weโre connecting that design process directly through to the testing and the packaging. And because theyโre so tightly coupled, youโre able to effectively see what your system level performance is going to look like before youโve even made the prototype chip and committed to fabrication.
This presumably will improve the ultimate reliability of the photonics modules.
Thatโs not a primary goal for this programme. Thatโs considered to be too close to the market for a subsidy program like InPulse. But there will be several benefits emerging from our work. Remember weโre creating the tools so that end users (companies) can work out in advance how yield and performance match their business environment. They can better understand where the fundamental challenges in achieving their targets could lie.
If they can more accurately predict the spread in performance, they can make better judgment calls based on the business case i.e. the number of chips they need to be getting through their process at a certain price point. So, in that sense, weโre creating the tools for businesses to evaluate yield and performance even though weโre not specifically solving that in this pilot-line programme.
If you talk to people in the semiconductor business, they tend to assume that the chip manufacturing and assembly process has already been built and perfected. So, much of the tooling for photonic integration must be already available. What is the current status?
There have been great strides in fundamental research and prototyping with Multi-Project wafers. But because of the relatively low volumes needed at this early stage, there hasnโt been very much equipment level innovation to benefit the Indium Phosphide community for the last two decades. We have tended to make do with what was established in the past. And whatever we can get hold of from the electronics world.
The electronics world works on a different scale. They handle much larger wafers. They handle larger batch sizes. And benefit from high levels of automation. They are good at making many millions of chips a month, which is what is demanded by consumer electronics companies mass producing smartphones.
But this scale advantage is also a scale problem. Because of the maturity of the semiconductor industry, the business models only work when you have a massive market. Yet the trend is towards making dedicated systems on a chip for specific applications, like a stress sensor system monitoring the performance of an aircraftโs landing gear.
Closely Matched to Market Size?
In Indium Photonics, the nice thing about the technology we work with today is that weโre quite closely matched to the current market size. So we can scale organically. But clearly, as market demand grows, we will need to scale reliable production of the chips. Currently, the chips being manufactured in the Indium Phosphide PIC fabs are 3-inches in size. By moving to 4-inch wafers we can double the capacity of the chip โreal estateโ. Weโll be increasing batch sizes as well, thatโs the number of wafers that we process at any one time. By reducing the time spent in the fab, we will get more wafers through the fab as well. This approach means we can scale quite considerably and effectively and yet still align to market needs. In this way, we stay cost-effective and sustainable.
So, will you be able to deliver hundreds of thousands of chips per year?
InPulse does not directly target high volume but focusses on perfecting and accelerating the methods that will scale. We have set ourselves a target of a million millimetre squared (wafer area), within the 4-year project.
For a pilot line, I think thatโs a very reasonable target but weโre not about manufacturing in this project. Now thatโs a commercial activity with a very high technical readiness level (TRL-8). But in combination with the other programme putting together the methods, metrology, automation and the new equipment, the end result is that weโre in a better position to build the next generation of fabs. These will have a high capacity to meet the demands of new market segments.
So, this sounds like a kind of high TRL level that youโre talking about. Is this something thatโs new for Eindhoven University?
It is relatively new. Weโve made a conscious decision within the last few years to address the gap between university research where we get up to about TRL 3 or 4 with academic demonstrations, and the expectations of the industry. Many businesses are only able to take on technology once as matured to the TRL 6 or 7 level with industry-ready prototypes. That gap has persisted, so the European Commission has consciously funded activities between TRL 4-7. We feel that weโre particularly well suited to coordinating activities to bridge that gap. We have a history in the Eindhoven University of Technology of cooperating with industry, in photonic integration research and also with our role with the joint European platform Photonic Integration in Europe.
How is PhotonDelta helping to accelerate what youโre doing?
PhotonDelta has already helped in many ways. The Photonic Integration ecosystem has been a key strength for us. Itโs also joining up the dots between the various stakeholders in the photonics community in the Netherlands and beyond.
Also, itโs making a very clear path towards a digital innovation hub which is a really important end goal for pilot-line initiatives. There are multiple pilot lines. And what weโre really trying to achieve at the European level is critical mass in photonics manufacturing. Organizations such as PhotonDelta play a key role in creating visibility, connecting stakeholders, creating momentum. The new investments that theyโre able to mobilize will enable further developments in these technologies.
Is there a link between inPulse and another pilot which was also awarded to the Eindhoven University of Technology, namely the Open Innovation Photonics Pilot for North West Europe?
Yes, they are highly complementary. InPulse is focused on consolidating the PIC foundry technologies which are available now, and building business and value chains.
The second pilot line programme OIPNWE was awarded in November 2018. That has the aim of creating the next generation fabrication tools which speaks to the point you hinted at earlier. What are we doing about yield? In the industry, we all know where the yield challenges come from. Weโve talked with equipment suppliers. We understand the challenges and equipment developers have an appetite to innovate with us. Theyโre ready to develop the tooling specific to the needs of high-yield, high-performance InP photonic integrated circuits. We are confident challenges can be addressed with a new generation of equipment. Once thatโs been made, tested and released to a second pilot line, Iโm sure we will be able to exploit that capability in the InPulse programme.
Is there any connection with other pilot-line initiatives?
This is a rapidly evolving space. InPulse is a standalone project in its own right. But clearly, weโre expecting to generate considerable business that will not just require Photonic Integrated Circuits. To properly realize the value of that, you need the packaging knowledge and the Chip Integration Technology Centre in Nijmegen will have a core competence in that space. Phix Photonics Assembly in Enschede and Technobis in Alkmaar both have a very compelling offer. There are several other parties that we will be able to link to as the technology matures, notably the PIXAPP Pilot Line in Ireland for photonic integrated circuit packaging.
What to expect from European Photonics in 2019?
Photos by (c) Jonathan Marks