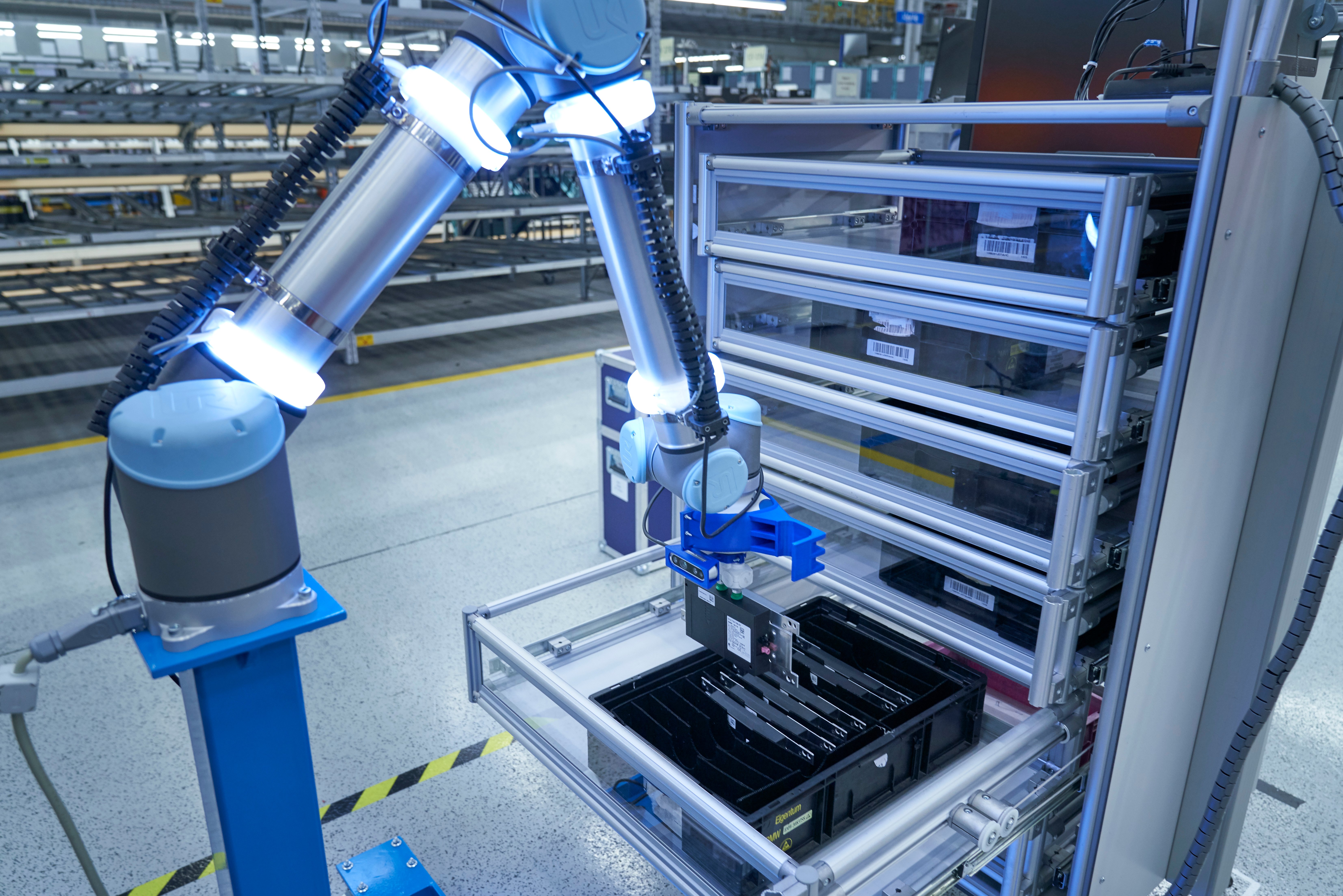
In a world where automation increasingly transforms work environments, factories are no exception. Some manufacturers are turning to “dark” production, where full to near-total automation allows robots to take over, even running overnight. A prime example is UK-based Wootzano, using robot-powered packing lines and aiming for complete automation. However, replacing human workers isn’t straightforward, as robots lack in creative thinking and problem-solving skills. In 2018 Tesla CEO, Elon Musk, admitted “excessive automation was a mistake” and replacing some robots with human workers. Has AI brought us any closer to a full dark factory?
- Automation transformed manufacturing, with robots taking over heavy tasks and moving towards lights-out factories.
- AI enhanced automation, with robots learning and adapting to their environment for increased efficiency.
- Full automation remains a challenge, but smart factories are becoming more prevalent, offering significant benefits.
The dawn of automation
Factories have long been the epicentre of human labour, filled with the grunts and groans of workers and machinery alike. The rise of automation has created a shift in the manufacturing industry. Robots now shoulder a substantial portion of heavy lifting and assembly tasks that were once exclusively human.
Consider Wootzano, a UK-based fruit packer, which has taken significant strides towards a future of ‘dark’ production. At Wootzano, robots prepare and pack fruit with little to no supervision, aiming for a factory floor devoid of human presence. The goal of such companies is not simply to replace human workers with machines, but rather to create an environment where machines can work continuously without human intervention. The potential cost savings are substantial; Wootzano predicts that, eventually, they will be able to operate with 80% fewer people than they currently employ.
The human factor in automation
But the march to full automation is not without its hurdles. As Helge Wundermann, a professor of robotics at University College London, explains to CNBC, robots are not particularly good at creative thinking or problem-solving. In the event of an error or unexpected situation, human expertise is often crucial to pinpoint and solve the problem. In fact, in some cases, the rush towards automation has proven premature.
Elon Musk, CEO of Tesla, famously admitted that his decision to heavily automate the Model 3 factory was a mistake. After experiencing production delays and quality issues, Musk replaced some parts of the automated assembly process with human workers. The move proved successful, with production rates improving significantly.
The emergence of intelligent robots
However, with the advent of Artificial Intelligence (AI), the balance is beginning to tip. AI offers a new dimension to automation, with robots capable of learning and adapting to their environment.
Ford is already harnessing the power of AI in its Livonia plant in Michigan. Here, technology provided by Symbio Robotics analyses previous attempts to determine the most efficient assembly approaches and motions. The result? A 15% faster assembly line – a significant improvement in the automotive manufacturing industry.
Similarly, the concept of ‘lights-out’ manufacturing, where the need for human activity is minimal, is gaining traction. In these factories, production can continue uninterrupted, even in the dark. The benefits of ‘lights-out’ manufacturing are manifold, from increased productivity to reduced upkeep costs.
Autonomous factories: A reality?
While full automation remains a challenge, some factories are making significant strides towards this goal. VDL Cropteq Robotics, for example, has developed an autonomous leaf-cutting robot for cucumber plants. The robot’s AI system uses a vision system, neural network, and plant model to recognise objects and adjust its movements accordingly.
Seizing the opportunities presented today by lights-out processes, forward-looking manufacturers are implementing these processes within their conventional and smart factories, making for a “lights-sparse” facility or production line. This deployment provides realistic value to manufacturers, bringing about continuous improvement, reduced production costs, and improved quality.