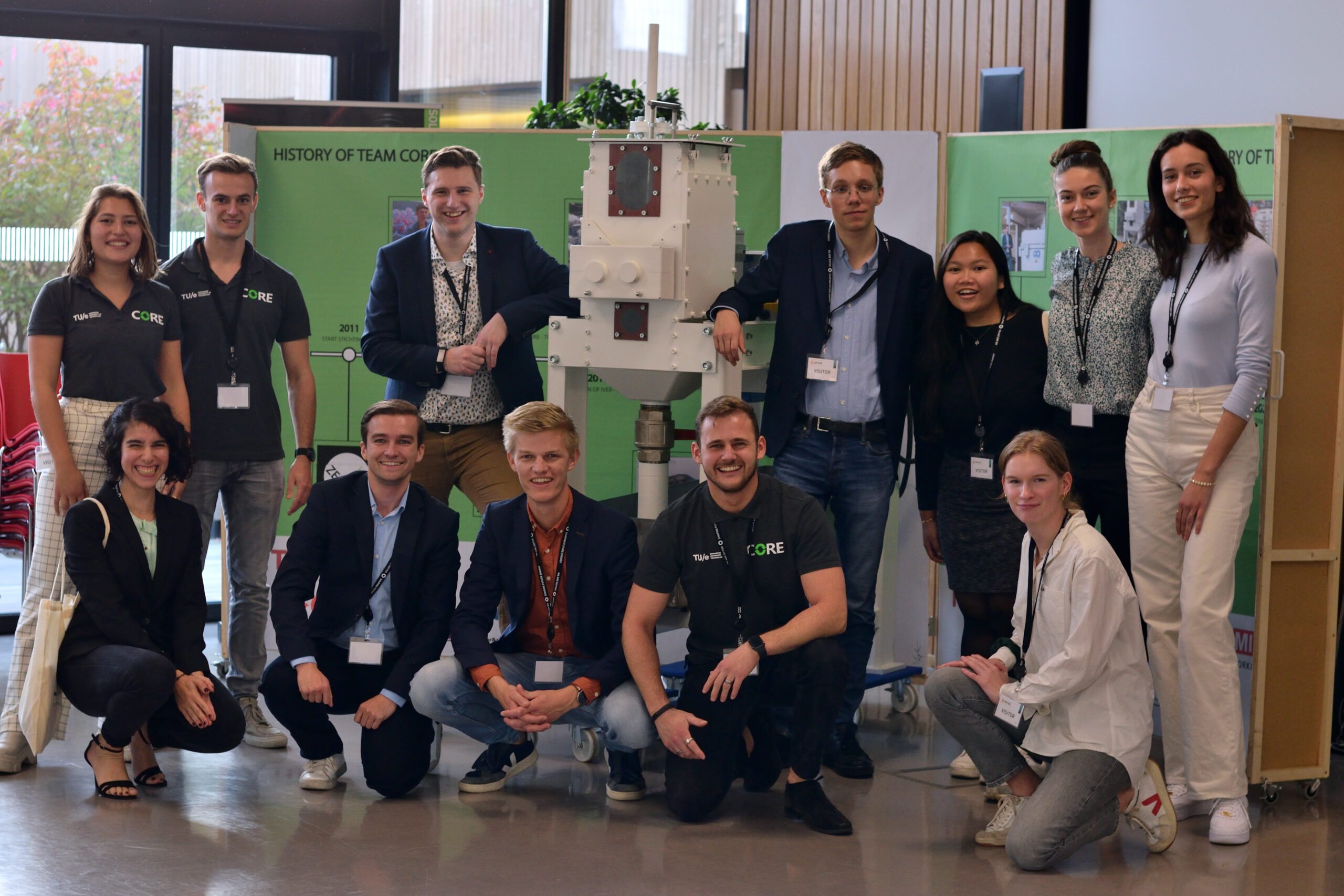
We are using batteries more and more. In our own home, we use an average of 113 per year. There is also a growing demand for electric cars and bicycles. Whatโs more, industry needs batteries in order to become electrified. There are two complicated aspects to this increasing demand, says Dirk van Meer, founder of CORE Chemistry, a spin-off of the Eindhoven student team CORE. โRecycling batteries is not something you do lightly. Battery fires pose a big risk.โ The students have now found a way around that.
Batteries are made up of flammable substances, Van Meer explains. โThose substances are unstable and can cause waste fires at high temperatures.โ The number of waste fires in Europe is increasing, according to research by the Dutch Ministry of Infrastructure and Water Management. In 49 of the 53 fires at European e-waste recycling plants, batteries are the cause. โThese fires can release hazardous substances, which local people could inhale.โ
The team has been working for a year and a half on a solution to battery fires. Last Monday, the students unveiled their invention. A fully functioning shredder, the CORE Titan. Filled with pride, students from both the old CORE team and the new one presented the system. The student team changes membership each year.
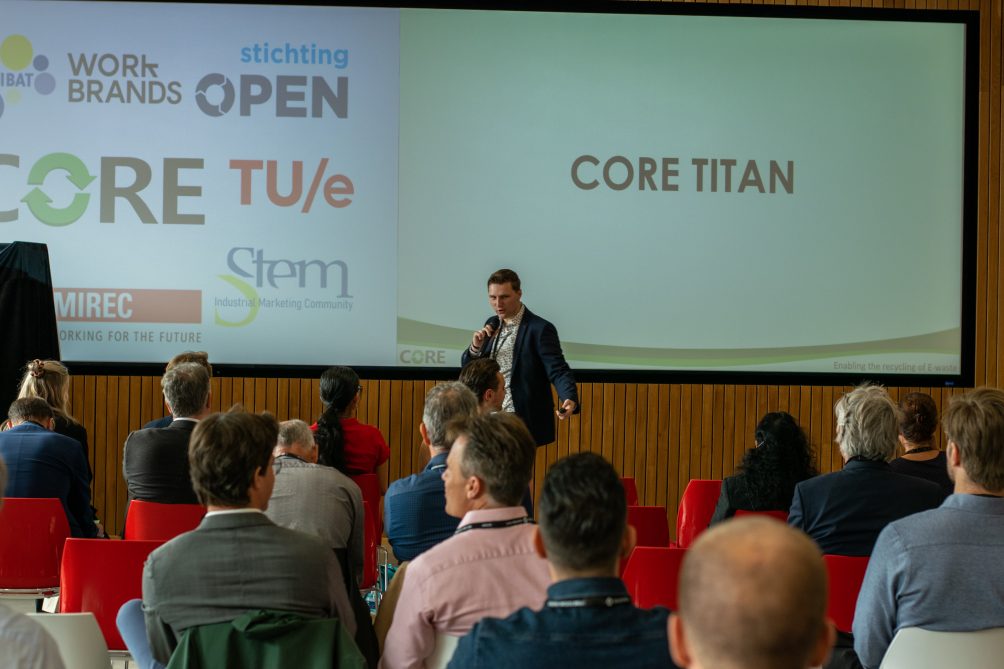
Separating
About 60 people showed up for the unveiling. Partners who had helped make it possible, fellow students from other programs, but also interested people from the waste industry. Like Hanneke Agterhuis, project manager business development at waste processor Renewi. โFor me, it is a great first step in solving a huge problem. I think itโs a topic that is important for many companies, but not important enough to put a dedicated team on it. Iโm glad these students took the first steps.โ
For Hugo Stijnen, business developer at Bluetron, it is also a familiar problem. โThe a flood of batteries is huge, but often it is not necessary to throw away power supplies at the end of their life cycle. Bluetron gives used industrial power supplies a new life. We do this for companies such as IBM, among others. It is cool to see how CORE has taken up recycling. I am looking forward to their next step.โ
New materials
This is a first step, because the shredding mill shows that it is safer if you shred the batteries in a tank of salt water. This means less risk of a waste fire. The students want to use what remains to make new materials. Whether they will succeed is another matter, Gabby van Meer confirms. He is the father of student Dirk, who founded the student team CORE in 2018. From a young age, son Dirk became intrigued by his fatherโs unbridled ambition to be able to recycle metals.
That ambition actually stemmed from 2002, Gabby van Meer explains. A medical mishap had him out of action for months. He went to the hospital to have his tonsils snipped and the doctor โdecided to cut my carotid artery.โ A year of rehabilitation followed, learning to talk again, getting back into shape. But not just that. โThe first four years after my rehab were a big party for me. It was all injury time. I might not have survived what had happened, so all that time was extra. There werenโt really any problems, because I knew it was not going to last.โ
Relevant
Van Meer quit his job at an American manufacturing company. โI had had enough, I wanted to do something socially relevant.โ He chose the public sector and worked for Prorail for 10 years and advised the province of North Brabant and Drenthe, among others, for 6 years.
In 2006, his quest for a way to reuse metal began to take shape. At Prorail he made sure, among other things, that the written-off sleepers of the rails could be disposed of properly. โIn Belgium they went into the ovens and in England they made garden furniture from them. As a public sector company, you donโt want to deal with your waste like that. That had to change.โ He learned about recycling through Autorecycling Nederland (ARN) and others. He also met precious metals chemicals director Leo Nevels who inspired Gabby van Meer to have a dream: A factory where metals could be reused using smelting technology based on the way the earth functions.
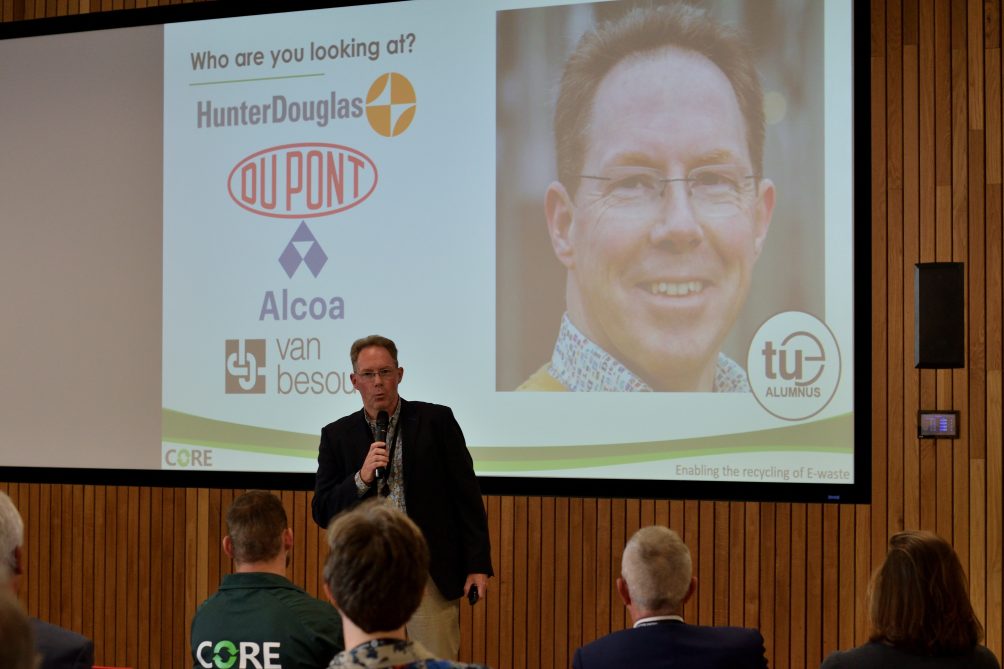
Nevels had figured out how the earth processes its difficult residual streams, Van Meer senior explains. โThose heavy metals find their way through contaminated silt to the bottom of the ocean. Through tectonic plates, they end up in the earthโs core where it is quiet, warm and low in oxygen. But that process takes centuries. I thought it should be possible to do it faster. Society is ready for that.โ It surprises Van Meer senior that we seem to be living in a world where we never break anything down. โAs if there are always enough building blocks.โ In 2011, Gabby van Meer founded the Institute for Elementary Retraction to make that factory a reality one day.
Read more about team CORE here.
Further steps
In spite of his relentless ambition, it seemed as if Gabby van Meer would have to give up on his dream. He did not have the money, the knowledge or the network to build a factory. Until son Dirk expressed interest: โHe said in no uncertain terms that the factory had to be built anyway.โ Dirk went to study technical chemistry, his father introduced him to his network. Some six years later, there was a lot of trial and error, pondering, experimenting and revelation. โWe come a step further every time,โ he says. About 100 students have been involved at some point; currently the team has 22 students.
Read more about the development of COREโs oven here.
Van Meer senior thinks itโs wonderful to see how the students work together and also have the energy to simply keep going. โLast Saturday, things went wrong at the last minute. So, at half past 10 that evening two students were still working really hard. Romanian hip-hop turned up loud. That took some getting used to, but it is a small price to pay when you see what they have built.โ
Dirk graduated last summer. Father and son are still closely involved with the student team. But they are also working on the factory within the spin-off CORE Chemistry, โwhich is going to be there one dayโ. Initially, Delfzijl was on the cards, but Gabby admits that the business case was flawed. โLimited capacity per year and an awkward location. Itโs quite difficult to let go of that, but if in theory you already have to add a few hundred thousand euros each year, then you know itโs not right.โ
Eye-opener
It marked an end for the Van Meers, but also a beginning. โWe learned a lot from the process. From the supply and discharge, and how to train people. But we also ran into the question of how we want to process unsorted batteries. What is needed in order to do that?
A shredder that works in salt water popped up, says Gabby van Meer. โA concept from Eastern Europe. We asked students if they wanted to do research on that. They came back saying itโs a good first step, but that smelting technology is not exactly a good next step.โ
That was an eye-opener for Gabby. โI was mostly working on a technical solution. As a mechanical engineer, I tend to go for the solution, not for the problem. Iโve learned not to put the technology first. Itโs all about accelerating the circular economy.โ
An โoptimist to the core,โ Gabby van Meer is certain that the factory will one day materialize. The plans have shifted from Delfzijl to Moerdijk. He is pleased to see that a physical step has been taken with the CORE Titan. That Dirk took over the baton from him at the time surprised him. โBut my youngest son even went a step further. He asked: โDo you know why the things you invent never seem to get off the ground? Itโs because you donโt take the user side into account. Itโs just the technology.โ He is now studying technical psychology. According to him, itโs better to develop technology that gets used, than to have ten genius ideas that never get off the ground.โ
Also interesting: Are lithium-ion batteries written off? 3 developments that prove otherwise