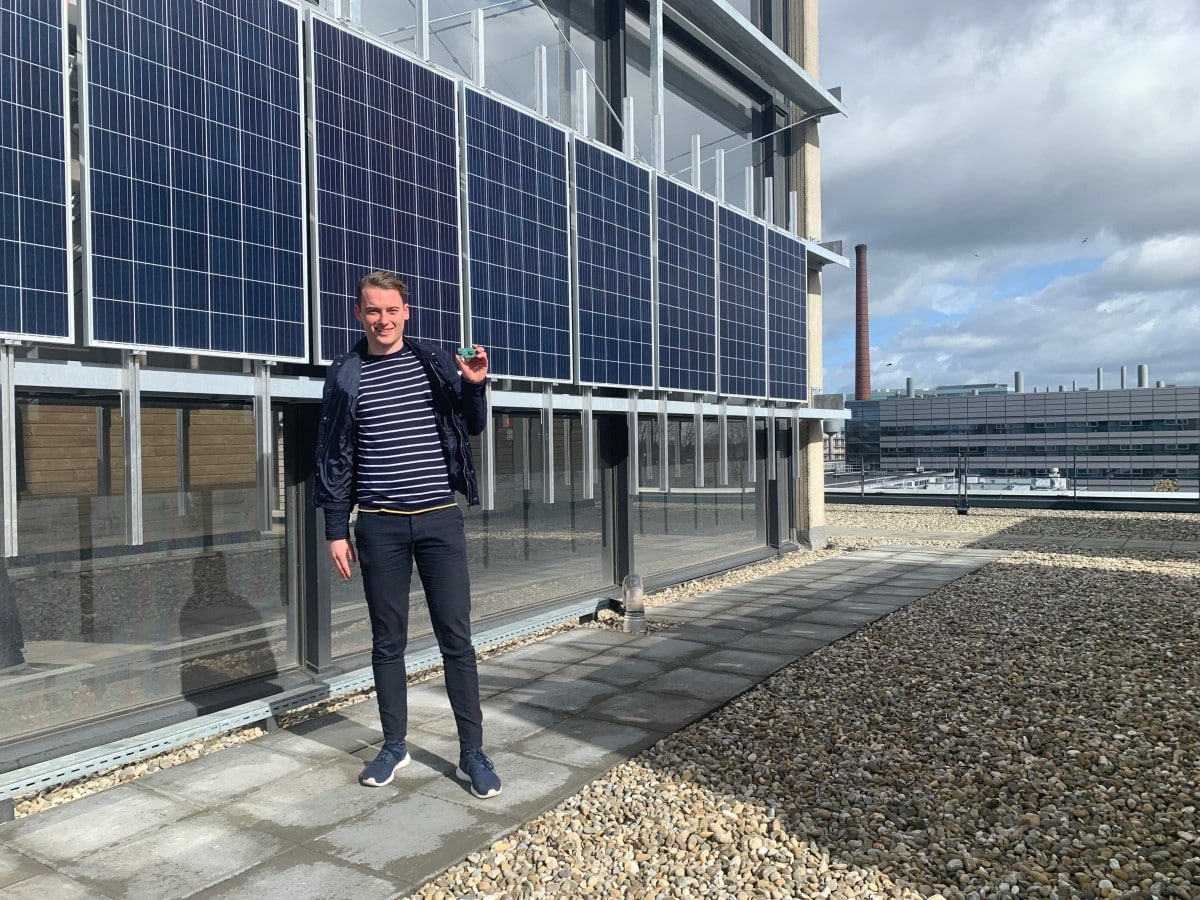
While some startups are making sexy products and love to be in the spotlights, others are working hard on techniques of which we will probably see very little. One of those is Taylor Technologies, a spin-off of the Technical University of Eindhoven which is working hard to make solar panels and cells more efficient and reliable.
Taylor has only existed for one and a half years and there are currently eleven people working on microelectronics for solar panels. Co-founder Michiel Roelofs summarizes the product the startup is making: “We are responsible for balancing solar cells. The inverter consists of ‘dumb’ power converters and a smart block, we provide the smart block.”
Between the solar panels on your roof and even between the cells in those panels, there can be differences when it comes to the yield. To make up for that difference, you need electronics that make sure each panel delivers the same amount. That’s exactly what Taylor can provide, microelectronics that, among other things, ensure that your panels have a higher yield and last longer. “If you have solar cells in a series circuit and one of them generates less energy, it obstructs the yield of the rest and becomes very hot, which reduces the life span of the panel.”
“If we have played our cards right, a consumer won’t know that we are in their solar panel”
“A good electrical engineering student can make the same as we do with an Arduino“, says Roelofs, but what makes it so special then? “The challenge in microelectronics is to make the same thing with as few components as possible, as cheaply as possible, and with the longest possible lifespan. What we actually do is put the functionality of dozens of standard components in a single chip in a half analogue way. Actually, it is a very elegant way of executing an algorithm on a few square millimetres.”
With Taylor’s electronics, you can make sure that there’s no longer a big difference between the cells. With this, you can win about 10% yield over the entire life span, according to Roelofs, but that isn’t even the biggest advantage: “Cabling also becomes easier, because thanks to us you can know exactly how much volts go through something. So we can save 30-40% on cabling and cabling time. This is even more important for larger systems than the fact that there is just a few per cent extra yields.” According to Roelofs, the electronics can also provide higher fire safety because they can switch off high voltages in the cells if something goes wrong. The lifespan of the panels should also be longer because the cells burn out less quickly. “The time it takes for someone to go up the roof to repair the solar panels is very expensive, but if the technician could see directly which panel should be replaced when something is broken, it would save a lot of time.”
From the very start of the company, Taylor has been looking for cooperation. “We took the technology to Solliance. They told us: ‘This is exactly what we’re looking for.’ That is how we ended up cooperating and started doing more and more projects together.” The company now cooperates in several projects, including in STAL and an Interreg-project around the integration of thin and flexible solar cells in roads and noise barriers. That kind of cooperation is also convenient when looking for clients abroad, according to Roelofs: “When you visit a module builder in China and say: ‘we work with TNO and imec’, they are immediately excited. There are simply not many knowledge institutions worldwide that are working at such a high level.”