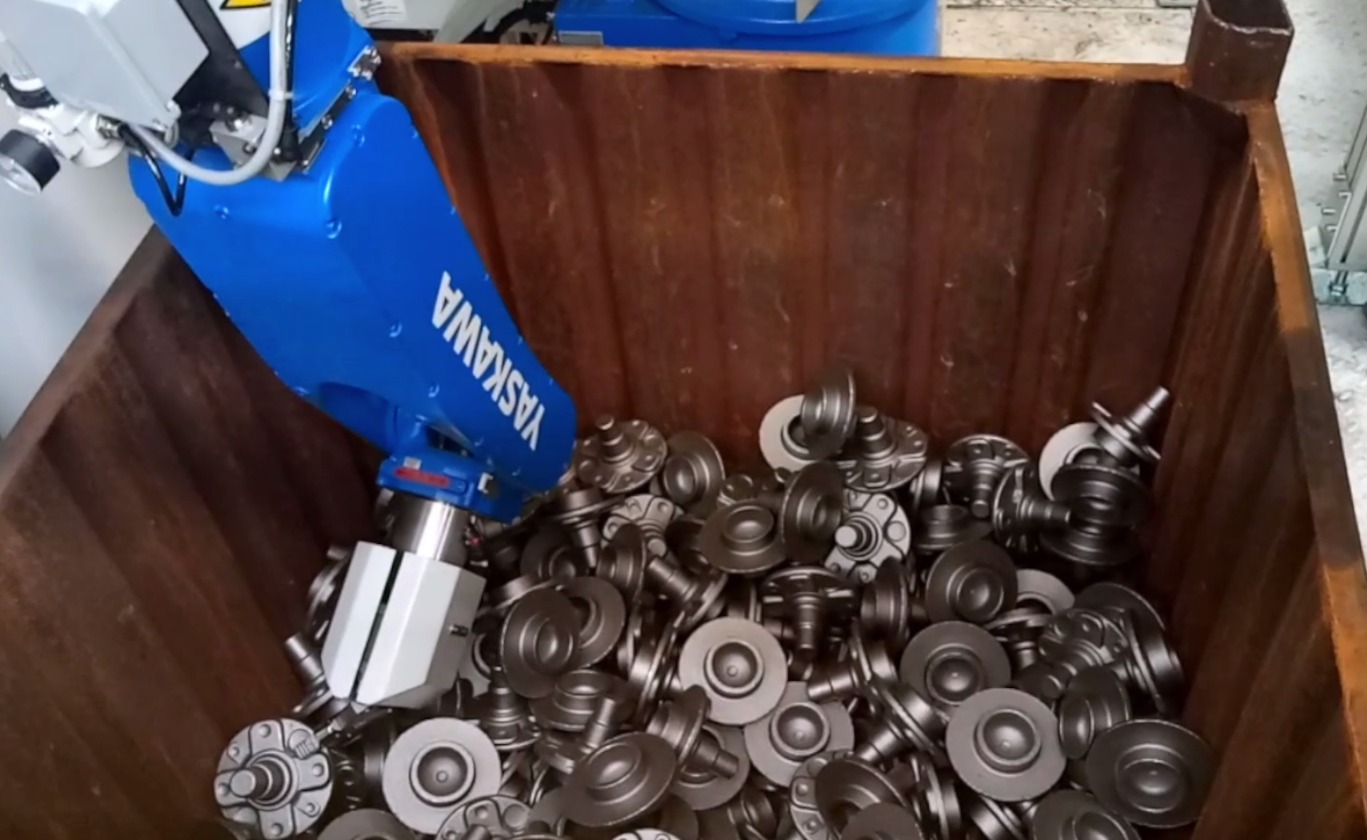
A robot arm that has to take parts from large containers in a factory cannot (yet) do it as well as a human being. Whether the product is upside down or twisted, humans do not have to think about it, whereas most robot systems have difficulties. Several companies and knowledge institutions at Brainport Industries Campus (BIC) are trying to find a solution for this.
Affix Engineering, a company that programs industrial robots and has a lot of experience with machine vision, is working together with Yaskawa, a Japanese robot manufacturer with a branch on the campus. This month, the first tests with the system will start in the Flexible Manufacturing field lab. Fonty students at BIC (the university houses three programs on the campus) are conducting various experiments and simulations. They seek to find out what doesn’t work, but especially what does.
Read more about the Factory of the Future innovation program, of which this field lab is a part, here.
Edwin van der Weele, project manager of the field lab, has already reserved a good spot for the robot arm in the room on the campus. He outlines the problem they are working on as follows. “All those parts often fall directly from the assembly line into a large bin. There is no fixed pattern for this and everything is jumbled up. People don’t have any trouble with this, but robots do. Sometimes they don’t recognize parts. Another time, the arm can’t go far enough into the bin. We are working on a system that is able to handle these issues.”
No need to reinvent the wheel
But according to Van Der Weele, much more is already possible with this technology than manufacturers often know. “With this set-up in the field lab, we want to show that a lot is already possible. Reinventing the wheel is not necessary at all.”
Danny de Greef, founder of Affix Engineering, concurs. “There are quite a few systems on the market that have already come a long way,” says de Greef. The tricky part, he says, is that a lot of things have to come together. For example, a robotic arm must be able to recognize a part, regardless of how it lies in the bin. “Parts never fall the same way in the bin. So the vision system must be able to recognize the product from any angle,” he explains.
Once the robot recognizes the part, it must then be able to take it out of the bin and put it away again in the right way. De Greef holds up his coffee cup. “This is how a robot squeezes it. If the gripper grabs the cup at the bottom, it falls over. A system must be able to take this into account. It’s important to the rest of the production process how such a product is put down.”
Testing with parts from practice
De Greef puts his coffee back on the table. There is more. The shape or material of the parts that a robotic arm has to grasp also has an impact on how the system works. “Take reflective parts. They interfere with the vision application,” says van der Weelen. He compares it to a motorist who can’t see anything because of the glint on his car window when the sun is low. “Because of the reflection of the laser, the same thing happens to the robot.”
To solve this, companies working with reflective parts can use an additional laser. “With this, you partially solve the problem,” De Greef knows. To test this further, Fontys students are going to work with different parts that come from companies. De Greef says: “The students help companies with testing overall, not just with reflective steel parts. But what happens to the system if, for example, there is oil on the products? Because of these accessible and inexpensive tests, manufacturing companies can implement robotization faster and cheaper.”
Converting knowledge for other manufacturers that come knocking
Mark Stappers explains that ‘his’ students gain practical experience in the field lab as early as during their studies. An ideal opportunity. Stappers is a lecturer and researcher with the Fontys research group High Tech Systems and Materials. “In the field lab, they get to work with various use cases and challenges that come directly from companies. At the same time, they gain knowledge that in turn is of value to other manufacturing companies facing similar problems.”
So how does that knowledge get to other manufacturing companies? Stappers: “The industry is still very much engaged in robotization and digitalization. These themes are also reflected here in the field lab. We try to make the link with the business world in various use cases. Cooperation is essential here. We also take a broader view. We try to gather general knowledge that can be converted when other companies knock on the door.”
A faster work process system thanks to simulation
The production environment can also play a big role in the success of so-called bin picking. “You want to prevent people from being bothered by the robotic arm. It is therefore important that everyone can continue to do their work. But at the same time, you also want all products to be picked from the bin,” explains De Greef.
In the field lab, companies can not only test this physically but also digitally with simulation software and a digital copy of the setup. “You can digitally optimize the entire system even before you have to purchase anything. Within a few hours of simulation, you already know whether it makes sense to place another gripper on the robot arm. That saves companies a lot of time and money,” he says.
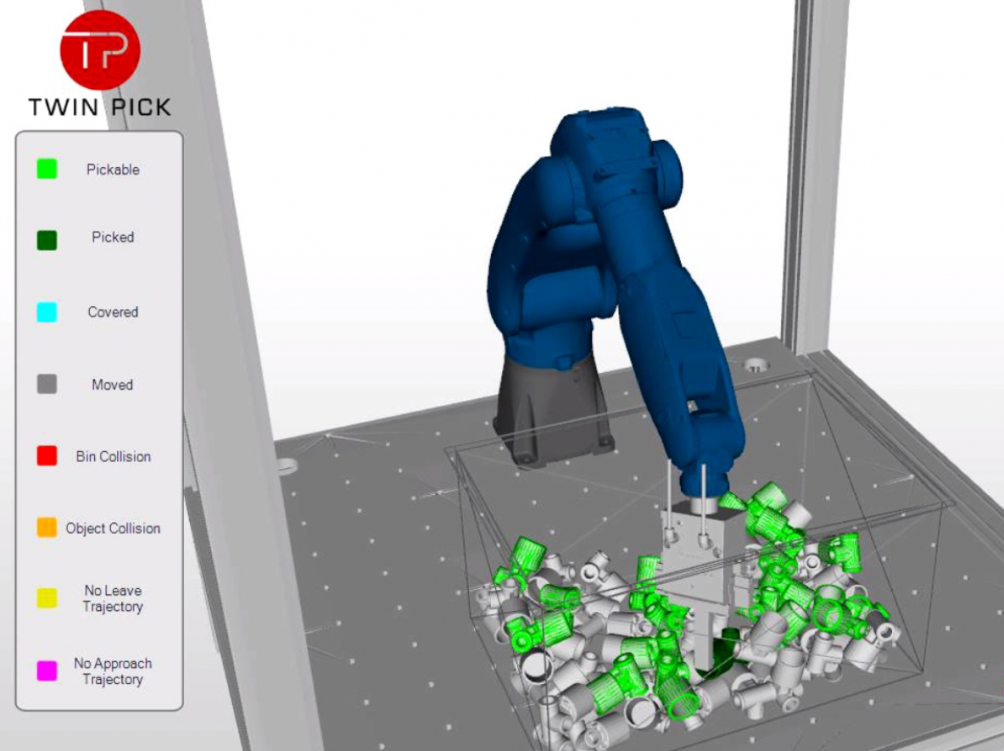
Meanwhile, De Greef shows a simulation where products end up in the bin randomly, just like in real life. “Now you see that most products are green, which means that the robot picks them without any problems. But the arm might not pick up parts or crash into the bin. You want to prevent such a collision to the extent possible. In the software, you can adjust things like the gripper, the settings of the arm, the bin and much more. Until it works.”