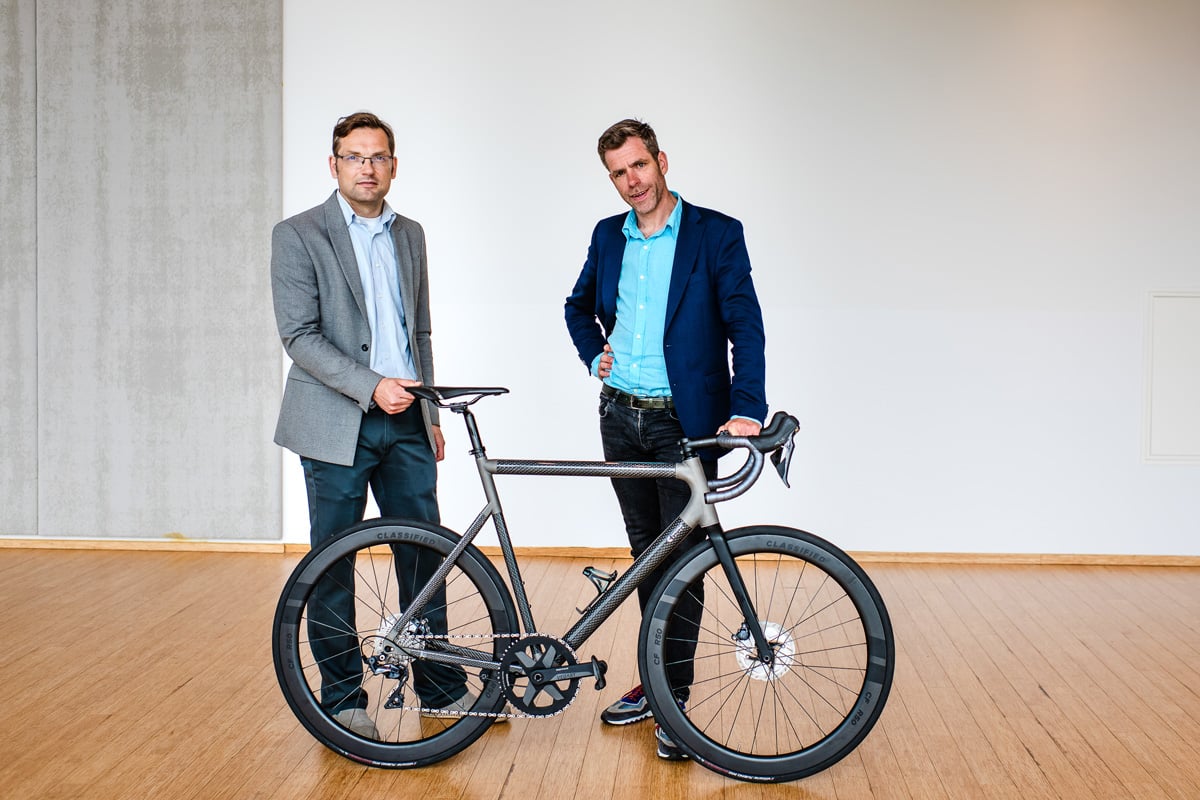
The first prototypes of the 100% Limburg Bike are ready. They can currently be seen at the Innovation Hub in Leuven, Belgium, where the World Cycling Championships are held from 23 to 26 September.
The 100% Limburg Bike was developed at Brightlands Chemelot Campus in Sittard-Geleen with a consortium of entrepreneurs, researchers, and students. In the coming months, the bike will be tested extensively by, among others, former professional cyclist Bram Tankink.
The 100% Limburg Bike is unique for several reasons, the inventors say in a press release. “First of all, the bike will be made exactly to size,” says Bram Tankink, a former professional cyclist and involved in the project as a business developer for the campus. “The angles and lengths of the frame tubes are variable so that you are “placed” perfectly on your bike. The bike is adjusted to your stature and length, so to speak. One was custom-made especially for me and I get to test it out.”
Tuning
Important, says Niels Boon, movement expert, and researcher at Bikefitting.com. “By building a fully customized bike, you can better tailor it to the cyclist’s needs and desires. This allows us to find an optimum between different variables such as ergonomics, steering behavior, and aesthetic aspects of the bike. This is a lot easier than with off-the-shelf frames.”
The bike incorporates several innovations developed on campus. The tubes and fork are made of interwoven carbon and super-strong Dyneema® fiber from DSM. The joints in the prototype are made of titanium and magnesium, printed with the specially built 3D printer on Brightlands Chemelot Campus. The combination yields a super-strong and feather-light frame, virtually unbreakable. 3D printing with carbon and built-in sensors that measure whether damage has occurred to the frame after a fall or heavy impact, for example, is in development.
The 100% Limburg Bike was developed by a consortium of regional companies including carbon specialists Eurocarbon and CeraCarbon, Belgian Cycling Factory, KEMBIT, and Mullens Sports & Health Innovations. Chemelot Innovation and Learning Labs (CHILL) and Brightlands Materials Center (BMC) signed on to print with magnesium, titanium, and carbon composite.
A step further
Pieter Potters, manager of R&D at Belgian Cycling Factory, producer of the successful bicycle brands Eddy Merckx and Ridley, certainly sees commercial opportunities for the 100% Limburg Bike. “It would be a nice addition to our bike range. With the Eddy Merckx brand, we also market customized bicycles, but the Limburg Bike goes one step further. Furthermore, we see opportunities in the innovative combinations of materials for new components such as stems and seat posts.”
In the coming months, the bikes will be extensively tested for riding experience and against applicable standards by Bram Tankink and others. Students from Zuyd University of Applied Sciences will be responsible for the quality tests on a test bench and set-up of their own in Heerlen. After the test phase, the 100% Limburg Bike must be made ready for the market. Then it will become clear who will produce the bicycle and what the consumer will pay for a personalized copy.
The Limburg Bike project involves over 1.8 million euros. Brightlands Chemelot Campus, the Province of Limburg and the participating companies are investing 1.2 million euros, the European EFRO OPZuid subsidy program is providing 600,000 euros.
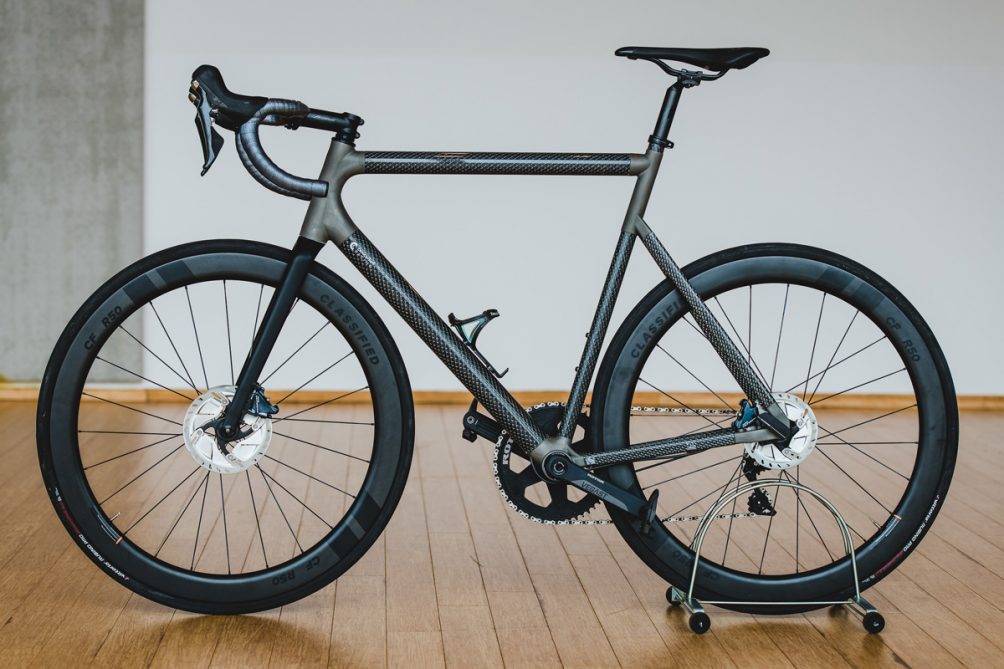
Selected for you!
Innovation Origins is the European platform for innovation news. In addition to the many reports from our own editors in 15 European countries, we select the most important press releases from reliable sources. This way you can stay up to date on what is happening in the world of innovation. Are you or do you know an organization that should not be missing from our list of selected sources? Then report to our editorial team.