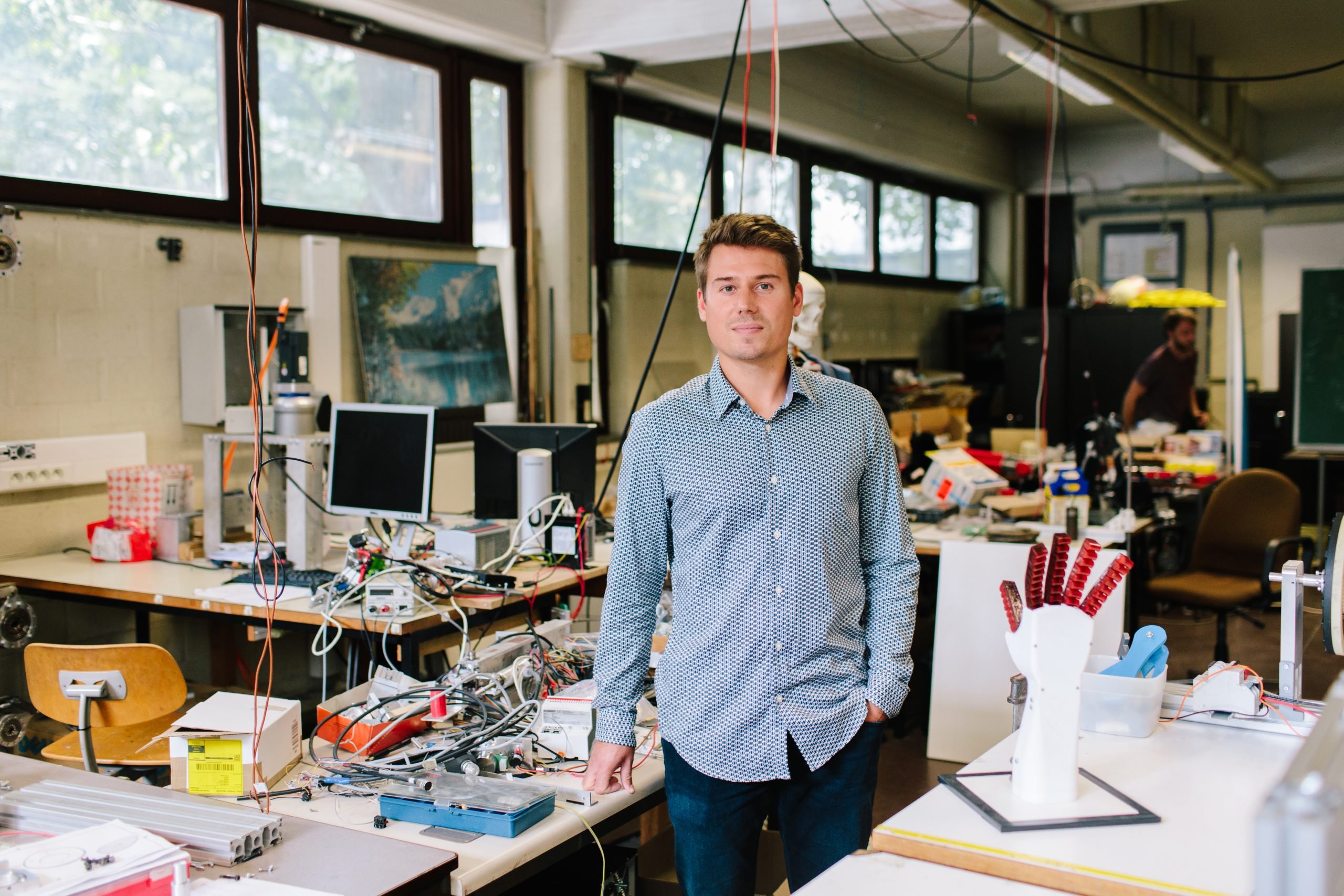
You cut a finger in half, put the two ends together, and after a while, it’s as good as new. It sounds like science fiction, but it’s absolute reality. If you are a robot at least.
In 10 years’ time, safe, soft robots will help us in our everyday lives. But because they are soft, they are also more vulnerable. Researcher Seppe Terryn at the Vrije Universiteit Brussel (VUB) in Belgium has found the solution in self-healing polymers.
Robots have long since ceased to be the stuff of the future. They are widely used in the production industry. Just think about the specialized tasks they perform in the automotive industry. These robots are large, heavy, and made of hard, metal parts. On the one hand to carry heavy loads, on the other so that they can protect themselves.
But an accident can easily happen with these robots. And because of their construction, the consequences may be serious. In other words, a dynamic, unpredictable environment, where people also work, is not the place for these kinds of robots. That is why researchers have developed soft robots. Robots that are based on the human body.
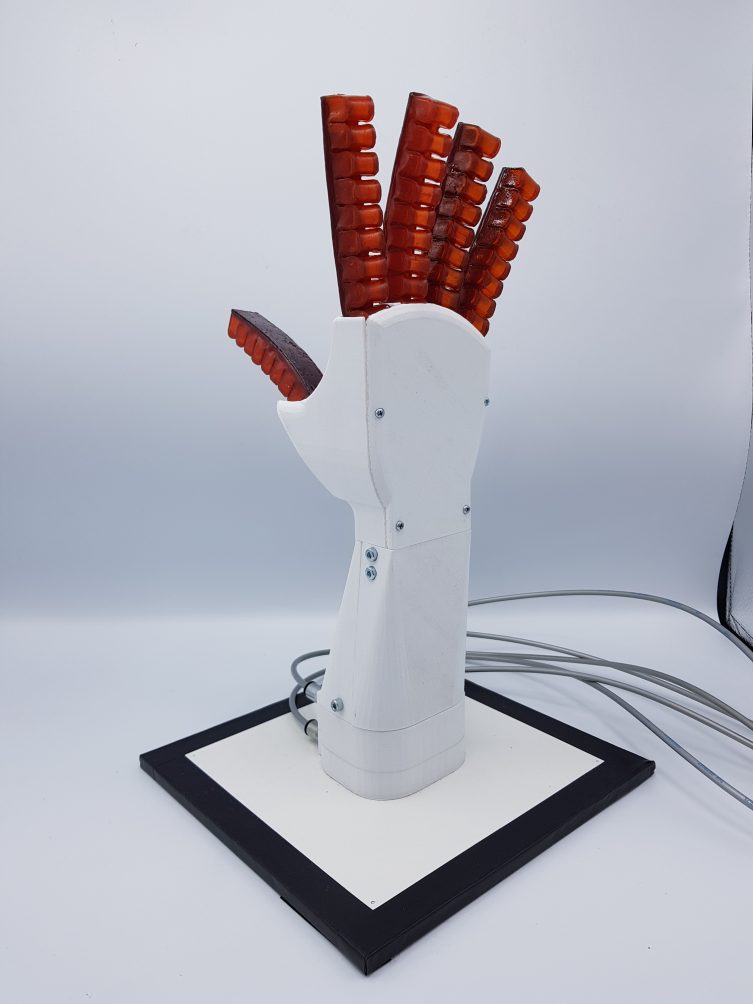
“Our body is flexible,’ Terryn explains. We have flexible muscles and flexible skin. If we bump into something, we partially absorb that collision. And this is how we also limit the damage. They’ve also started to apply this idea in robotics. We build robots out of elastic polymers. This way, we can make them flexible and give them passive intelligence. When you bump into these kinds of polymers, they tend to bend away slightly by themselves, without a sensor and a computer deciding that.”
Sensitive to damage
These types of robots can operate outside of an industrial setting. They can help us at home, in care centers, at school, act as service robots, or as part of an exoskeleton or a prosthesis. The problem is that these robots also get damaged more quickly. Just like the human body. “We, and soft robots too, are very sensitive to sharp objects,” Terryn says. “We sought a solution to this problem. The logical step is to make them bigger, stronger, and harder, but then you lose a lot of their interesting characteristics. Their flexibility disappears. We decided to let them heal instead.”
Two departments at the Vrije Universiteit Brussel joined forces: the Robotic & MultyBody Research Group and the Physical Chemistry and Polymer Science Group. “We were the first to combine these self-healing polymers with robotics. Before that, these were mainly used in the coating of expensive items, such as cars or cell phones. Scratches in those coatings were then able to heal quickly.”
Network polymer
Self-repairing materials are more expensive and therefore have so far found it difficult to enter the traditional industry, where cheap plastic materials are still holding sway. “But the components of a robot are more expensive at any rate,” Terryn adds. “If we can extend the lifespan of this kind of robot with self-healing materials, it will definitely be interesting for the market.”
With support from the SHERO project, Terryn and his colleagues succeeded in making large components from such polymers, while these were still capable of healing themselves. “For example, we made a robot hand out of self-healing material,’ he explains. “We cut one of the fingers in half and after a while, it grew back again.”
“To do this, we use network polymers. You can compare them with a spider’s web. Because all the chains are interconnected, they behave like a rubber band, which can stretch a lot but recoils every time you release it. The connection points in the network are made of reversible chemical bonds, namely the Diels-Alder bond. They can re-form after they have been broken.”
This Diels-Alder reaction is faster at higher temperatures. This also means that a robot heals faster if you heat the damaged area. Most repairs take anywhere between an hour and a day.
The only limitation in the repair process is that you need to have all the broken pieces. If you cut off a finger, it will not grow back by itself. You always have to connect it to the phalanx. It is also capable of resisting material fatigue. “In normal materials, fatigue occurs after a while. Because we work with a dynamic network, that will not happen. The bonds change all the time, even when at rest. Small cracks are also healed this way.”
Picking fruit
In order to test their research in practice, the VUB teamed up for the SMART project with Octinion, a Leuven-based company in Belgium that specializes in new technologies for the food industry. One of their robots picks strawberries.
“Strawberries are very fragile and come in a variety of shapes,” says Terryn. “You can then place a huge number of sensors and cameras on the robot’s gripper to calculate each time it needs to stop applying force. But that requires a lot of computational power. A soft robot is a more interesting solution here. But according to research, the lifespan of such a soft gripper is reduced by sharp branches or hard plastic that might damage the robot. That’s why Terryn’s research would be a great help in this respect.”
Recyclable
What’s more, the self-healing material they use has plenty of potential when it comes to being recyclable. We are able to convert a finger like that into another shape,’ explains Terryn. “This is not the case with similar materials, such as rubbers. Just think of the piles of car tires that remain untreated or are set on fire. Besides that, we have hired someone to look into how we can make the various components of the material more ecological.”
The researchers are constantly keeping an eye on the market throughout the further development of the material. This way, they want to be sure that there are plenty of applications for their product. Nevertheless, it is difficult to estimate how long it will take before these kinds of self-repairing robots reach the market. “A lot of tests still have to be done. For example, is it safe to eat a strawberry picked by our robot? First of all, a toxicity test is still needed for that. Safety is paramount. But that is precisely why I believe in this project.”
Photo: VUB researcher Seppe Terryn. (c) VUB
Read more IO articles about robots via this link.