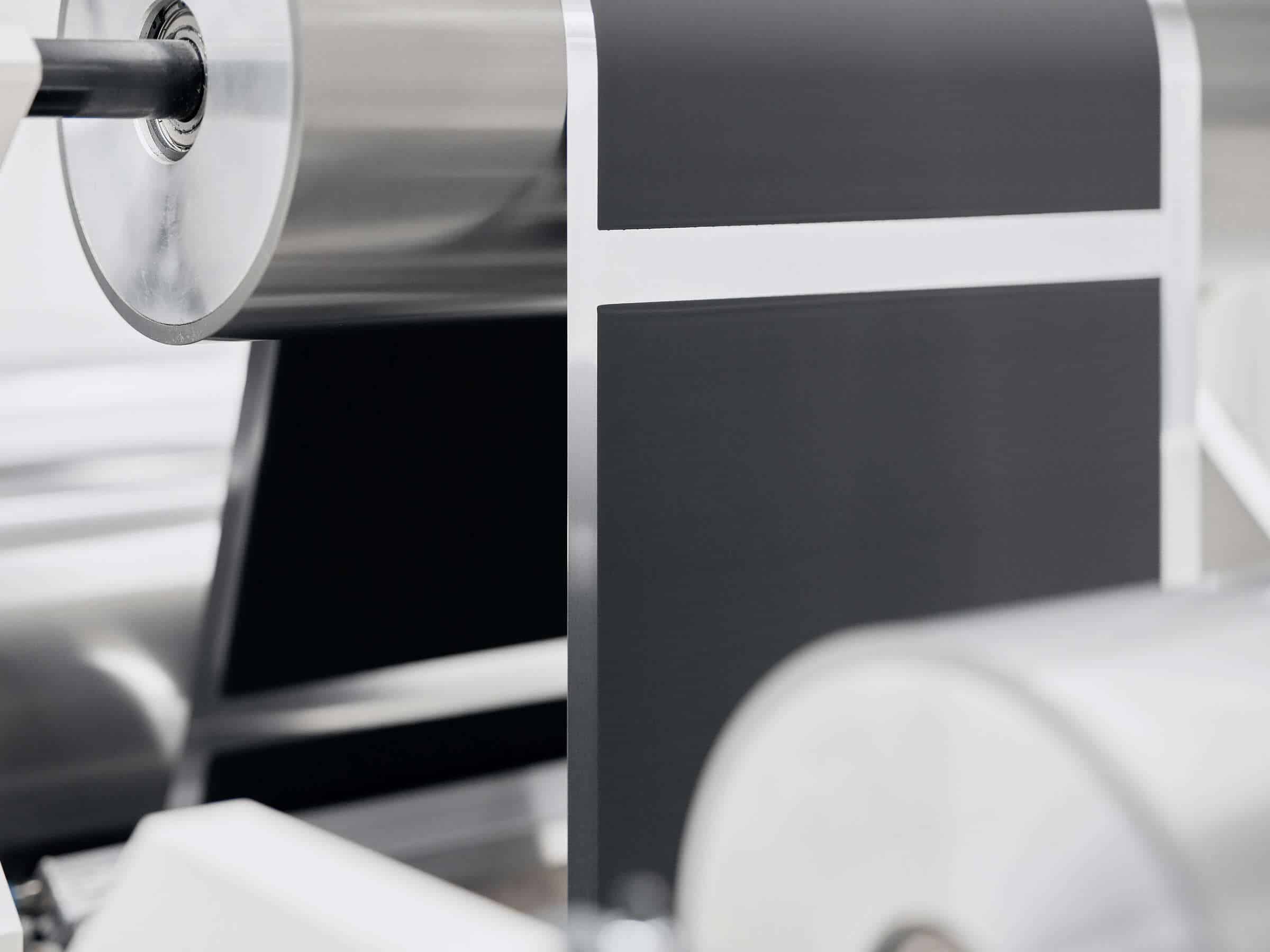
PowerCo, a Volkswagen subsidiary, is partnering with German printing machine specialist Koenig & Bauer to develop a groundbreaking Dry Coating technology for battery cell production. This innovative process is expected to reduce energy consumption by 30%, save floor space by 15%, and cut costs by hundreds of millions of Euros annually. The Dry Coating procedure applies powdery materials directly onto foils, creating a thin and even layer that enhances energy density, battery performance, and fast-charging capabilities. The technology also eliminates the need for energy-intensive drying furnaces, suction systems, and chemical solvents.
- Thin layers are essential in battery production.
- PowerCo and printing machine specialist Koenig & Bauer developed a new technology.
- With this technology battery production will become simpler and cheaper.
Collaboration for sustainable battery cell production
According to a recent cooperation agreement signed by Koenig & Bauer and Volkswagen subsidiary PowerCo SE, the two companies will collaborate in the field of sustainable battery cell production. Koenig & Bauer will develop a machine for the industrial powder coating (solvent-free dry coating) of electrodes, a sub-process of multi-stage battery cell production. This new method eliminates the costly and energy-intensive drying of wet-coated electrodes, increasing efficiency and sustainability in volume battery cell production. The development phase is scheduled to run until the end of 2024.
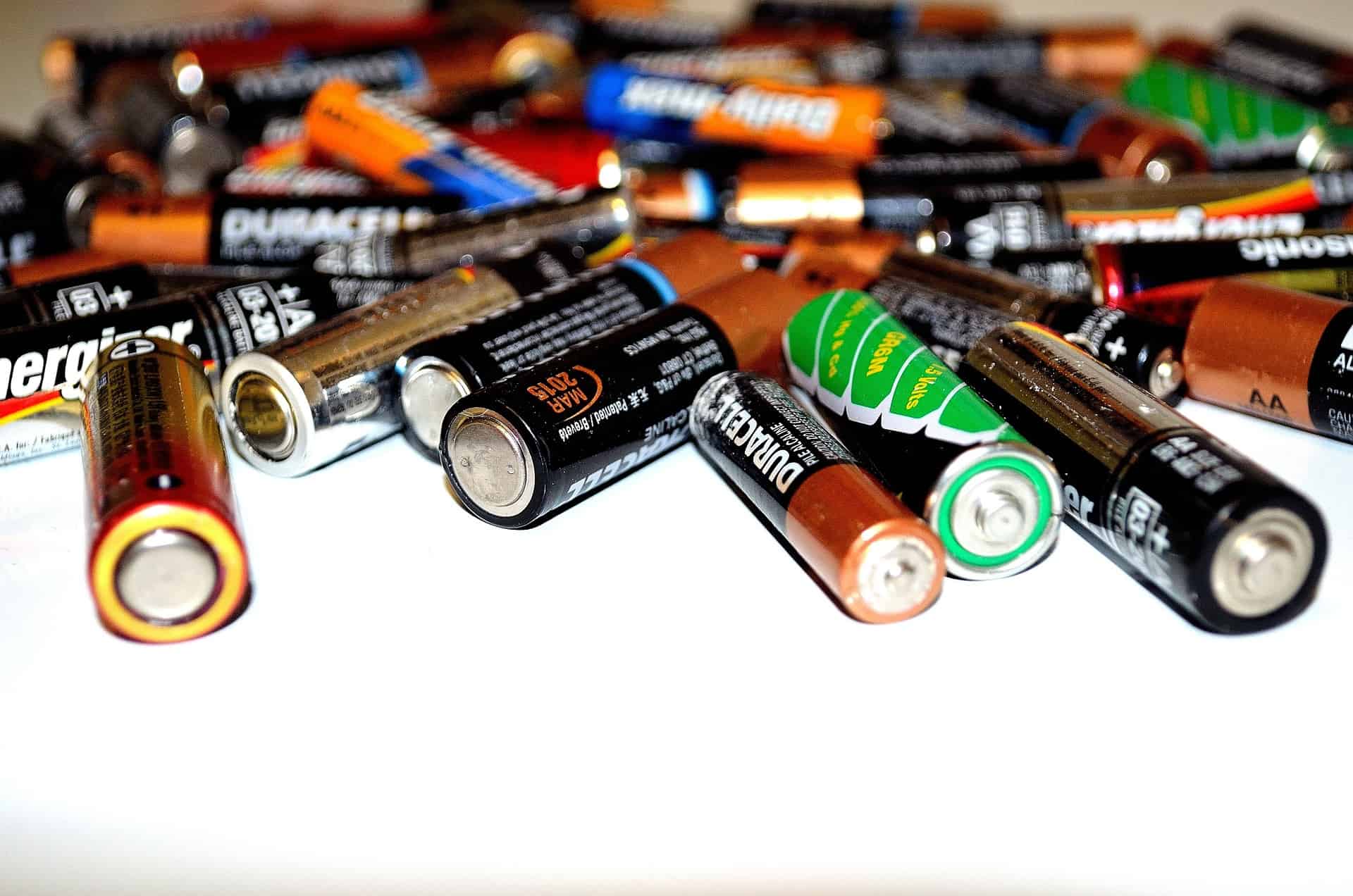
If the ambitious development goals are achieved, Volkswagen will have the exclusive right to use or sell the Koenig & Bauer equipment for a period of 7 years. A separate supply and distribution agreement will be concluded for this purpose. The collaboration with Koenig & Bauer allows PowerCo to adjust its plants to new processes quickly. The Dry Coating procedure is expected to be a game changer in battery cell production.
Tesla’s promise to produce 4680 batteries that are 50% cheaper has yet to materialize due to challenges with dry electrode coating production. However, Volkswagen may beat Tesla to the punch, with dry-coated cathodes developed through their partnership with Koenig & Bauer.
Impacts of Dry Coating technology
The Dry Coating procedure involves applying powdery basic materials directly onto foils, resulting in a thin and even layer that improves energy density, battery performance, and fast-charging ability. This new process eliminates the need for the most energy-intensive part of cell manufacturing and the use of chemical solvents. Internal tests have already proven successful, showing a decrease in energy consumption of about 30%.
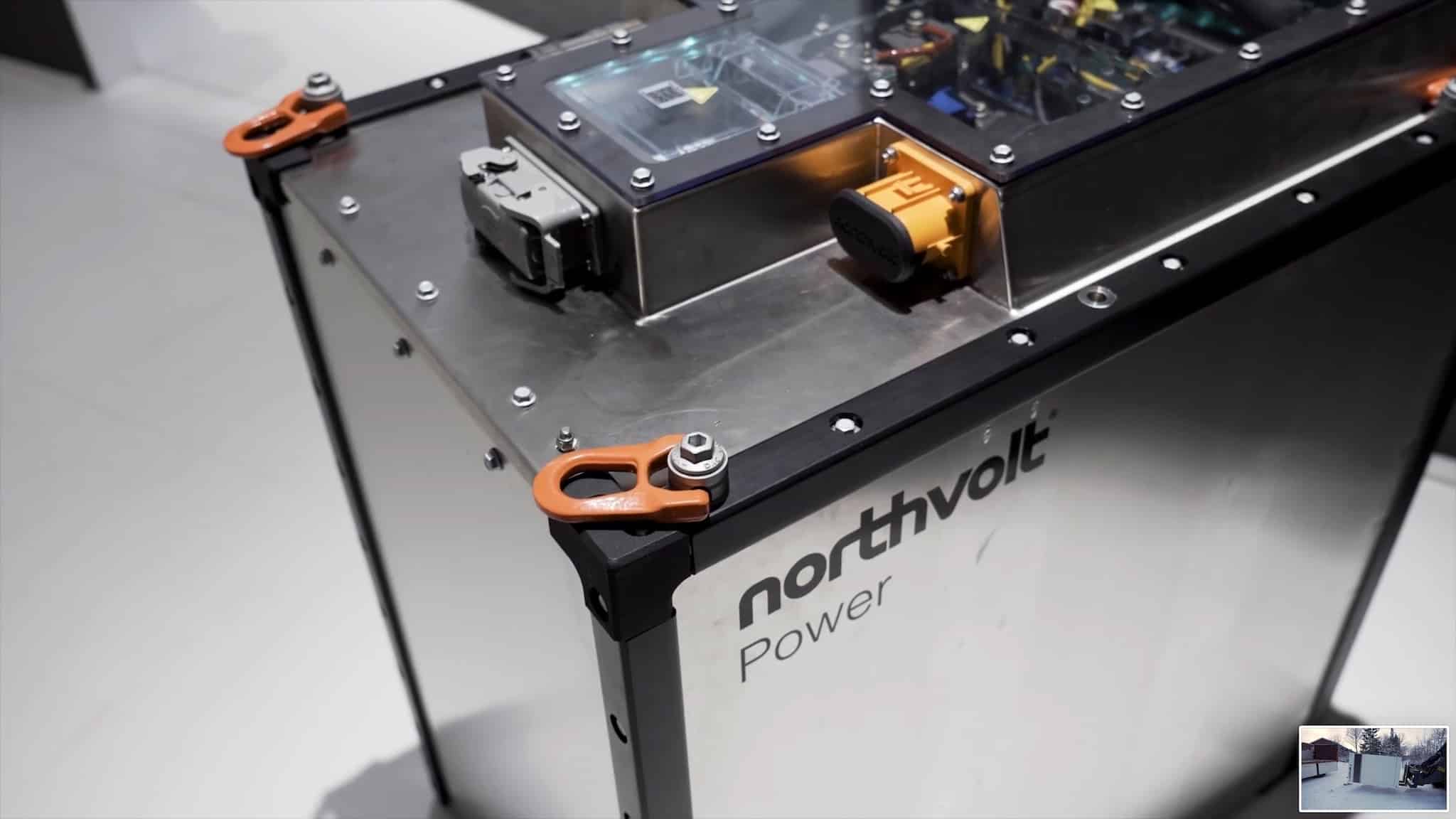
Furthermore, the technology reduces the required floor space by 15%, eliminates the need for energy-intensive drying furnaces and suction systems, and cuts costs by hundreds of millions of Euros annually. PowerCo and Koenig & Bauer aim to exit the development stage by the end of 2024 and start production in 2026/2027.