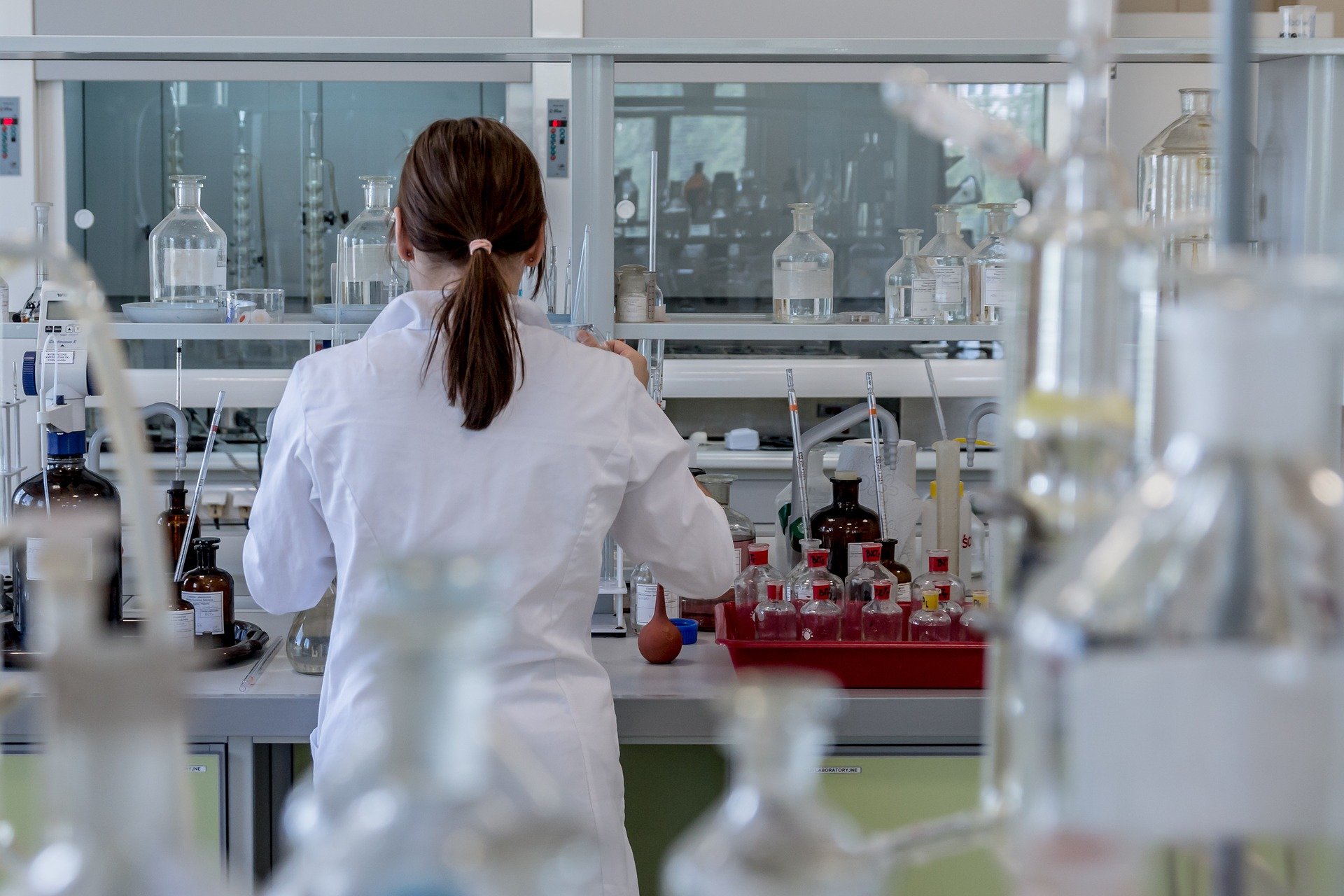
Nowadays, many of the molecules that are needed in Europeas ‘active ingredients’for the production of medicines, cosmetics and plastics are not made in Europe but in Southeast Asia. That these lengthy supply chains can cause problems was highlighted by the corona pandemic last year. Yet this geographical dependence is not the only problem that the chemical industry faces.
“We source active ingredients in the form of a vat of white powder or liquid from China. This is not given a second thought anymore, it is something that’s just taken for granted. Large companies in Europe have significantly reduced their R&D processes that was focused on these import molecules. The production process is geared towards importing things from China,” Rinus Broxterman explains. Broxterman was trained as an organic chemist and worked for thirty years for the chemical giant DSM in various research and development roles. He is currently CTO at InnoSyn on the Brightlands Chemelot Campus in Geleen, the Netherlands. At InnoSyn he is involved in helping companies to innovate in the area of chemical processes.
Less reliance on imported chemicals
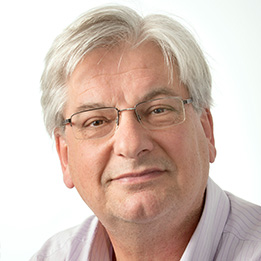
According to Broxterman, it is a mistake to take the production of straightforward chemistry for granted. “Bringing production back to Europe not only ensures that there is less dependence on countries such as China, but he believes it can also contribute to innovations and improvements in production processes. For example, you would not only solve the problem of medicine production stagnating because of shortages. But manufacturers themselves will be able to work towards making their processes much more sustainable.”
“Can you make do with fewer raw materials to produce the same results? How can you cut down on chemical waste? And can you use less energy during the process? These are all questions that have been relegated to the back burner because Europe has been so heavily dependent on the import of chemicals from abroad.”
Unwanted side effects must have a price tag
Moreover, by bringing production back to Europe, Broxterman believes you can also better control and, where necessary, improve things that society deems unacceptable. “Some products we import are made in ways that are completely unacceptable in terms of their environmental impact. We should no longer want medicines that involve dumping waste in a river somewhere. Charge a price per kilogram of waste produced and have it reflected in the cost price. By charging for by-products such as waste, CO2 emissions or other matters that society regards as unwelcome, you can qualify process problems more effectively. By doing this, it forms a manageable challenge for companies to improve themselves.”
The same goes when it comes to a carbon tax. In his view, this forces companies to emit less and think about how things can be done differently. “Sustainability is becoming increasingly important. Some of the raw materials will be reusable or will have to be biobased. Even electricity is going to be green in the future. A price on CO2 emissions will force companies to look for alternatives.”
Classic image of chemist is outdated
Broxterman has to laugh: “On average, process innovation in chemistry doesn’t have a sexy image. The classic image: an experienced chemist stirring in a 3 neck lab flask and performing a different test every day. It is a slow process and success depends on the ideas of the individual chemist. This was indeed the case in my time in the lab, although it is already changing quite a bit.”
For instance, they can take semi-automated measurements in labs nowadays. Technology makes it possible to capture and use data in a structural way. With machine learning, an algorithm makes connections that a chemist might overlook. And chemistry itself is not standing still either. For instance, more and more manufacturing and process innovation is being done today on the basis of flow chemistry rather than batch chemistry.
Batch vs flow chemistry
The difference? Broxterman explains it like this:: “In batch chemistry, you mix precursor substances in a scaled up flask (reactor) and let them react with each other. In a number of cases, this releases a great deal of heat reaction. This can lead to dangerous situations. Also, the conditions in the large reactor container are not the same everywhere. It creates fewer or unwanted reactions depending on the location in the reactor. In flow chemistry, you let the substances pass and react through long, fairly thin conduits. So the reactor is actually a thin pipe now.”
“You can determine and control conditions, such as temperature and retention time, much more precisely. The conditions are the same for all molecules in the reaction conduit. This makes it safer and more sustainable because you can remove heat reaction much more easily, among other things. But it also offers a lot of opportunities for research into processes.”
Would you like to know more about flow chemistry and how it can accelerate innovation? Watch the Brightlands Science Lecture here.
A chemist can simply adjust the temperature of the pipes and experiment with the outcome on the fly. “In my time in the lab, this required me to do a new experiment each time. By the end of the week, I was happy with a small list of results. Flow chemistry works much more efficiently. Instead of one experiment or one data point per day, you end up doing, say, 20 experiments and data points per hour. So, this allows you to try out new process variations much faster and achieve much more within a short period of time.”
Broxterman believes that this trend in continuous flow chemistry is unstoppable. “It is more efficient, more sustainable and helps speed up research. More and more companies that still produce in batches are now knocking on our door to switch to flow chemistry.”
It’s not rocket science
But it also requires an investment, both in terms of resources and people. “In addition to the hardware that is needed – you also need different types of pumps, flow reactors, and other technical components such as sensors, among other things – a chemist in flow chemistry also has to have knowledge of all those components. It requires a chemist who doesn’t just wield a spatula to weigh out precursor substances. But they also need to be able to handle a baco and understand how to set up their first flow chemistry unit. That still poses an implementation barrier sometimes.”
Broxterman does think that it is feasible for the chemical industry to bring both the production of basic molecules, and molecules for drugs, back to Europe. “It’s not rocket science and essentially all the fundamental concepts are known. Setting up highly innovated process R&D will cost a bit more, but with the latest technologies it doesn’t have to be extremely expensive. Medicines, for example, will be slightly more expensive, but you can be sure that no more waste is being dumped into rivers. Production processes will become more efficient, cleaner and more sustainable.”