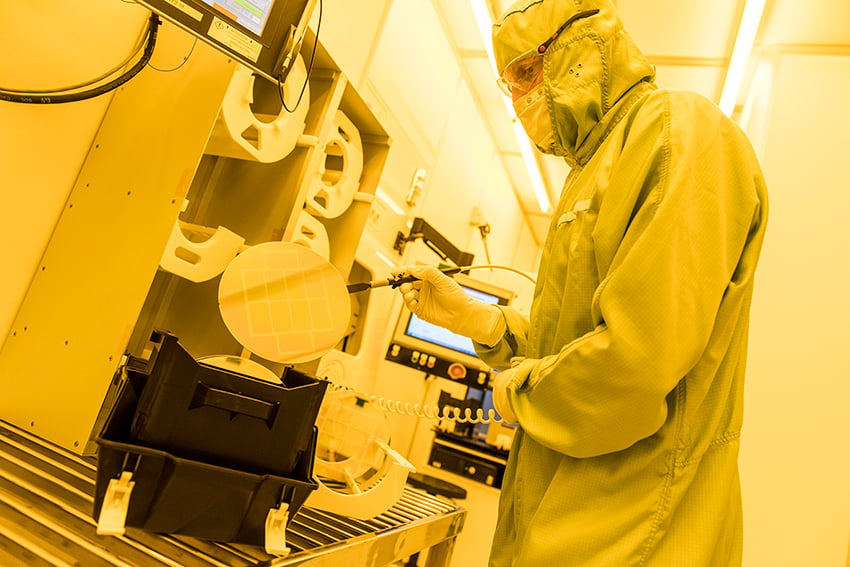
“Precision work down to the nanometer” is how Robbert van der Waal describes the work that Philips MEMS Foundry does. As part of Philips Engineering Solutions (PES), the company mainly makes a lot of components for customers outside of Philips. “Our technology is too good to keep to ourselves,” he says.
For example, Philips MEMS Foundry makes ultrasound transducers for catheters that allow you to look inside a heart, Van der Waal explains. Another example are the infrared sensors used to measure people’s temperature for Covid-19. Or the very thin membranes that the MEMS foundry makes for the EUV lithography machines of the ASML chip machine manufacturer. These membranes are about 200 millimeters in diameter and 50 nanometers thick. They are used to capture unwanted particles.”
Van der Waal is responsible for sales and business development at the MEMS foundry, which is located on the High Tech Campus Eindhoven (HTCE), “that big, low-rise building across from the Strip. We help our customers to make their components a reality. Once you have designed them, you don’t actually have them in your hands yet. We develop the fabrication process and then make the components.”
New medication
Customer requests range widely. “That keeps us sharp and competitive. It forces us to develop new knowledge. That’s good for Philips and that’s good for the outside world.” A lot of technology is always involved, says van der Waal. “A fabrication process can be ready for production within a year, but it can also take as long as three years.” One of the ‘older’ customers of the MEMS foundry is the Emultech company. That company started in 2009 as a spin-off from the Eindhoven University of Technology (TU/e). Today it is the world leader in microfluidic emulsion particle production. The company is also located on the HTCE, next to the MEMS foundry.
Emultech focuses on microfluidic emulsion particle production, offering applications in the field of pharmaceutical drug delivery and, for example, the closure of a blood vessel (embolization). “With our technology platform, we can improve existing medication or even develop new medications, says René Hansen, CEO at Emultech since last July.
A fortune
“Like blood thinners, for instance, which people now have to take twice a day. Thanks to our microspheres (cell-like structures with dimensions from 1 to 1000 µm, ed.) that deliver the blood thinner in a controlled way, a patient receives the medication over several weeks. A patient takes a dose once a month. Our microspheres deliver the amount that is needed daily. This greatly improves both adherence to the treatment and the ease of use for the patient.”
Van der Waal: “Emultech started in the clean room with us at the time when we also let third parties use our machines, whom we referred to as ‘hotel guests’. In 2012 we changed our business model and became a foundry for medical components, among other things. This required stricter control over the use of our machines. From then on, the hotel guests were also supported by us. So, Emultech as well.” Meanwhile, Emultech and the MEMS foundry have jointly developed a prototype that Emultech is demonstrating to other parties and which has already led to sales. “The foundry model has worked well for them, because a clean room of their own would have cost a fortune.”
“Strictly speaking, we have no understanding of emulsions and the so-called droplet generators that Emultech makes,” Van der Waal states. “But we do know how to make really tiny channels, tracks and holes with wafers made of silicon and glass and then how to put together a droplet generator chip.”
Nanometer
Emultech makes microspheres from miniscule particles that are perfectly equal in size, measured in micrometers or microns (one millionth of a meter) and even right down to nanometers. Hansen: “We are able to completely control the properties of those particles.” Such as their size, consistency, construction and shape, but also the percentages of medication and how quickly or slowly the drug is released from the particle. “In the last 5 years, we have made a breakthrough by being able to make 100 identical channels work stably and in parallel on a single unique chip. This allows these chips to continuously form consistent emulsion droplets in a fully controlled, predictable and scalable manner. MEMS Foundry manufactures these precision chips to our exact specifications.”
Sometimes it is particularly convenient that both companies are neighbors. During the development phase, there are often last-minute changes, Van der Waal points out. “Then an engineer calls us to say they still have some old material lying around – If we can do an extra sample run. That flexibility helps Emultech in their development.”
Hansen: “A lot of time and energy has been invested in order to get where we are today. Our technology is mature, robust and we understand it thoroughly. Now we need to make sure we can determine the right applications to roll it out on a larger scale.” Hansen sees those applications not only in improving existing medications, but also in creating new ones.
Van der Waal: “That’s the really special thing about my work. On the one hand, it’s super high tech. It’s something new and different each and every time. But it is also super relevant. We make the heart of the Emultech machine that enables you to make better medications.”