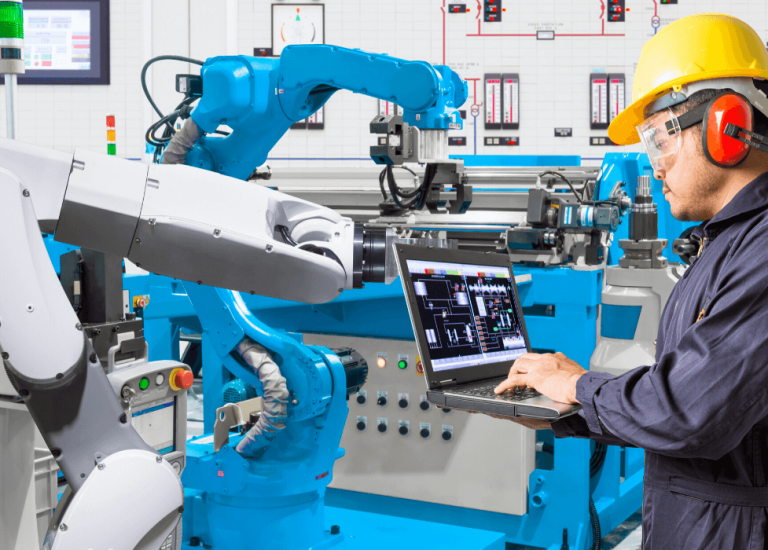
A world without plastics is unthinkable. Every day, millions of plastic products roll off the production lines around the world. For example, your Dopper bottle, the packaging for a parcel you ordered online, or a part of your car. The plastics industry, together with the rubber industry, accounts for 35,000 in the Netherlands. The sector has an annual turnover of around 8.8 billion euros and is mainly made up of small and medium-sized enterprises (SMEs).
The image that polymers has is not always a glowing one, as people invariably immediately think of plastic and plastic soup. Fortunately, the industry is increasingly proving otherwise. To connect all the different parties in the industry, Mikrocentrum is organizing the Kunststoffenbeurs (‘Plastics Trade Fair’) for the 22nd time this year. On 15 and 16 September, everyone who matters in the sector will gather under one roof in the Brabanthallen in the Dutch city of Den Bosch. The trade fair is organized by Mikrocentrum, an independent knowledge and networking organization for the high-tech manufacturing industry.
1. Sustainability
Plastics are mainly made from natural materials such as cellulose, carbon, natural gas, salt and especially crude oil. There is not much you can do about that. But there is something the sector can do about how residual products and recycling can be dealt with.
For example, the sector is using recyclate more and more and companies are working on optimizing their production process. The goal is that products of higher quality that are largely made of recycled materials leave the factory. In addition, companies are also looking at how they can make their own production process more energy efficient. The aim is to reuse as many residual streams from the production process as possible. For instance, some factories collect the heat released in production processes and reuse it.
That sustainability is important is also evident in products packaged in plastic and in packaging materials. At present, 39.5 percent of packaging is made from plastic. The Dutch Rubber and Plastic Industry Federation (NRK) has drawn up a sustainability plan. That plan contains a number of guidelines. Among other things, the packaging must become more efficient and lighter and be made of as much recycled material as possible.
2. Reshoring and automation
The pandemic has made it difficult for companies in the plastics industry to import all the parts that they need. Transportation and imports are becoming more costly. Logically, the question then arises: do the products really have to come from so far? So one trend is that the production of parts is steadily being brought back to Europe. In order to keep products interesting from a cost point of view, companies are placing more and more emphasis on automation. For example, parties that develop smart software to optimize production processes are emerging, and robotics is also making inroads into the industry. Robots can take over and accelerate parts of the production process and you will be seeing them at work in factories more and more often.
3. Scarcity
The plastics industry is facing a shortage of personnel and raw materials. This scarcity is a major challenge for the industry. A lot of companies have decreased production during the pandemic or even stopped operating altogether. When production resumed in full, raw materials were hard to come by. In the best case scenario, the scarcity also gives companies something to work with. I f production can become smarter by using less residual waste and fewer employees, the industry itself can cover part of the gap.
When it comes to personnel shortages, Mikrocentrum is also trying to bridge a part of that gap. The knowledge center is facilitating a wide range of training courses for employees who want to get started in the industry. From BBL Injection molding to a course in polymer chemistry.
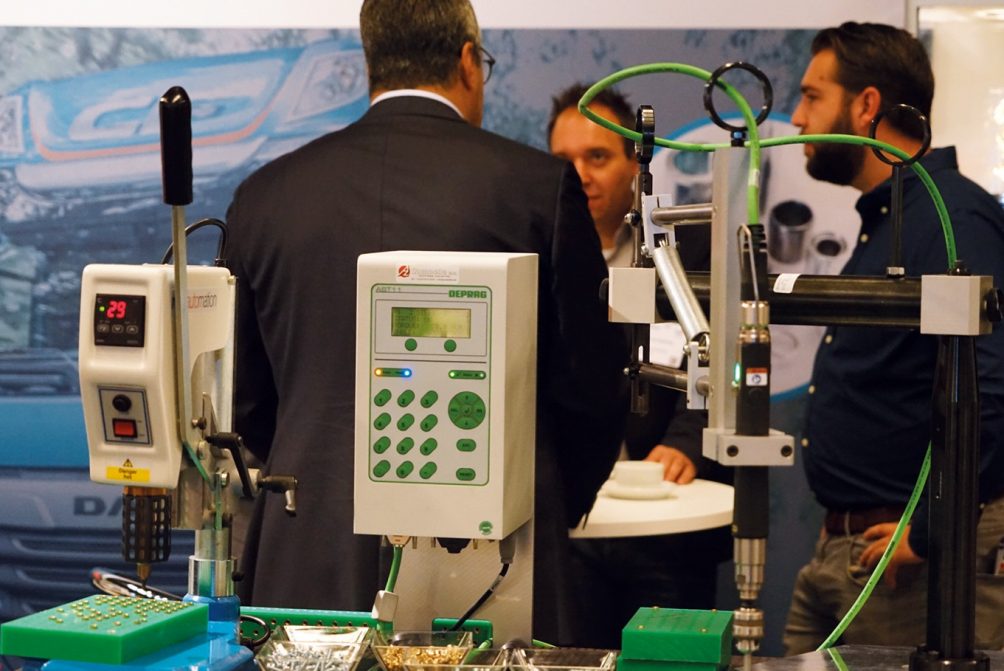
4. Circular economy and smart materials
A circular chain is an issue across all industries, but especially in the plastics industry where raw materials are becoming increasingly scarce. It revolves primarily around the reuse of products and materials without compromising on quality. One example of this is that the industry is starting to make more and more use of smart materials. Plastics are often very strong and last a long time. On the one hand, this is an advantage, because these products do not degrade very quickly, but it can also be a disadvantage. Companies within the industry are responding to this. Take garden plant pots as an example, which after a while simply degenerate into compost. That is plastic that dissolves very easily into nature.
5. 3D printing
3D printing is currently still losing out to the classic techniques such as injection molding, extrusion or vacuum casting, but it is set to take over an ever larger share of the market in the future. For example, you can easily have a prototype printed and you do not immediately need to have an expensive mold made. But it is also very interesting when it comes to producing complex materials. In addition, it is a circular technique: No more material is used than is needed and consequently there is no residual waste. Before this trend can be fully synchronized with the circular economy, recyclable or biobased materials should preferably also be used.
Would you like to know more about the developments in the plastics and rubber industry? Then visit the Plastics Trade Fair on September 15 and 16. Register (for free) via this link.