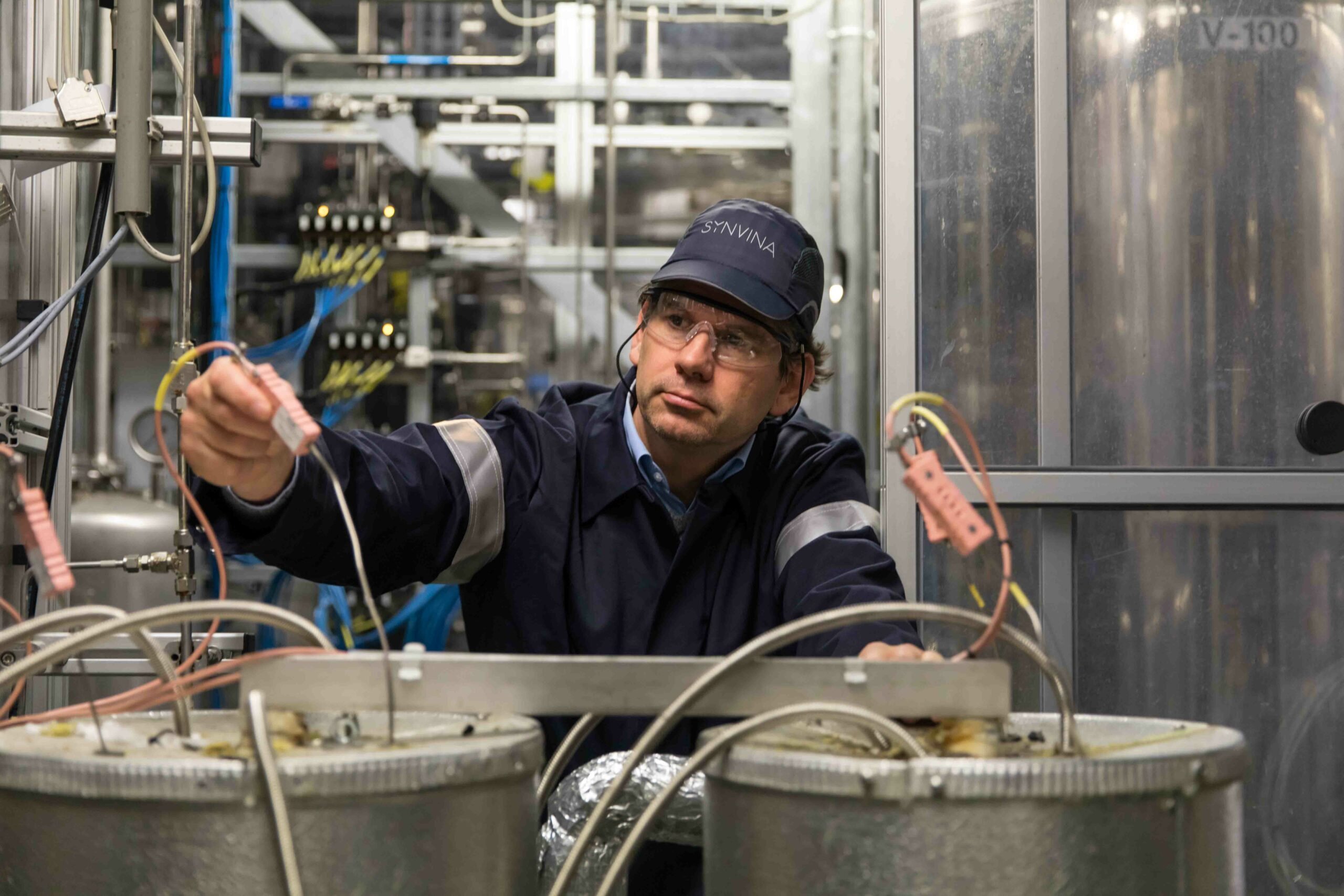
Avantium will be opening the world’s first commercial factory for the production of bioplastic PEF in the Dutch town of Delfzijl in 2024. The pilot plant is already fully operational at the Brightlands Chemelot Campus in Geleen. “We can still do a lot of good for generations to come.”
“We believe in a fossil-free world, let’s go!” – The statement on the website of the publicly listed company Avantium is crystal clear. “We make bioplastics from plant-based raw materials, so not from petroleum,” explains Patrick van den Berg, Plant Manager at Avantium. “And by doing that, we are striving for a world where chemical products are no longer made from fossil raw materials.”
The pilot plant on the Brightlands Chemelot Campus opened in 2011, a year before the arrival of Van den Berg. By his own account, van den Berg stepped into a fantastic adventure. Moreover, after DSM, he ended up at a young, flat organization where the lines are kept short. “The fact that you can set up something up from scratch seemed really wonderful to me,” he says.
Bioplastic
Sustainability was not really an issue at that time. “The sense of urgency was there but it wasn’t really felt across society in those days. The adventure back then was more about discovering the potential of an amazing and promising chemical building block FDCA (furanic acid) that is needed to make our bioplastic PEF (polyethylene furanoate). We are still in the process of discovering new, surprising properties. The applications for PEF are very interesting, so things are just bound to improve and become more fun.”
Avantium’s pilot plant was set up in Geleen in 2011. “Because we came here in a situation that was so well arranged and which enabled us to get started quickly. Just think of permits, facilities, the whole infrastructure, everything is properly taken care of. That’s important for a scale-up and an SME company like Avantium since basically that’s what we still are.”
The lines are short and Brightlands has developed itself even further, particularly for start-ups and scale-ups, according to Van den Berg. “It’s not like that we can take a close look behind the scenes of each other’s companies. We are all very innovative and therefore somewhat cautious about revealing innovative ideas and discoveries. We often keep our cards close to our chests on that front. But we help each other out when it comes to safety, personnel and certain services. Plus, we inspire each other and challenge each other.”
Brightlands
All of the technology is being used at the pilot plant on the Brightlands Chemelot Campus, and soon it will be rolled out at the commercial plant in Delfzijl. In Geleen, many tonnes of the raw material FDCA (furanic dicarboxylic acid) that is needed for the production of recyclable plastic PEF is already being produced. And once the commercial plant in Delfzijl is up and running, the pilot plant in Geleen will continue to run as an innovation center, where, for example, the technology for making FDCA and PEF will be improved even further.
Also read: ‘Making chemical industry more sustainable goes hand in hand with circular economy’
Superior properties
Large-scale production of PEF is soon set to start in Delfzijl. Van den Berg: “Our bioplastic PEF resembles the PET used in PET bottles but has a number of superior properties. In the process, we also discovered that PEF has a very important property for packaging. It provides a very good barrier layer to protect the product you want to package, especially in stopping oxygen from getting into the packaging, which can cause products to spoil. But even carbon dioxide from soft drinks or beer, for example, is better preserved in a bottle made out of PEF,” he explains.
“PET bottles – and this is something that a lot of people don’t realize at all – are not always just made out of PET. In some cases, an extra layer of nylon is added where a good barrier is needed. With PEF, no such extra layer is needed, our bioplastic already has those very good barrier properties contained in it. The extra layers that are now in some PET bottles are a challenge for recycling. However, a PEF bottle can be recycled very effectively. Mechanical recycling of PEF is very similar to the PET recycling process; trials have shown that the established recycling systems are compatible with PEF, so there is no need to develop new systems. Moreover, PEF can be easily distinguished from PET and other plastics using commonly-used infrared detection techniques. Moreover, we discovered relatively recently that PEF breaks down in nature if it unexpectedly ends up there.” This is what Patrick van den Berg calls an interesting side benefit.
Biorefinery
What does Van den Berg see when he looks into the future? “Of course, we are always trying to make great dreams come true. The sky is the limit. But when I look ahead, I mainly see an Avantium that is busy with new technologies that are going to conquer the market. We have also developed a technology to make plant-based MEG (mono ethylene glycol) and we have a biorefinery where we extract sugars from non-edible biomass, such as wood chips. That takes time. Hopefully in a few years we will all find PEF bottles and PEF in clothing to be perfectly normal. By then, hopefully, no one will remember how much time it took and what we had to overcome to get to that point.”
It will be a while before consumers find PEF material in stores. “The customer is probably going to first notice that certain packaging is already made of PEF or gets a somewhat greener stamp – more organic – because PEF has been used in it.” When the Delfzijl plant starts running in 2024, things could move very quickly. “Then we want to start selling technology licenses to companies around the world, which will enable these companies to build FDCA plants themselves.”
Climate-neutral
The Brightlands Chemelot Campus aims to be climate-neutral by 2050. That is in line with the ideals of a company like Avantium. Van den Berg thinks this is a fine ambition. “These kinds of ambitions have to be defined in order to reach them. If you don’t do that, they won’t work. Avantium and Chemelot need to set ambitious goals. This may occasionally be accompanied by delays and disappointment, but that is inherent to large ambitious plans. If we had not had ambitious plans back in 2011, we would not have been able to announce last week that the shareholders have agreed to the construction of a large plant in Delfzijl.”
Patrick van den Berg recently gave a talk at Vista College in the Dutch town of Sittard so as to have conversations with operators about sustainability issues. He initially sensed a mixture of bravado and trepidation. ” Ultimately, you do notice that people are concerned about the future and how the earth will fare in the future. I hope our story might have inspired them. Even though my generation did not do many things that were right for the climate, we can do a lot of good things for the next generations. We are working hard to make that change. As a matter of fact, we can’t go back either, the turning point has been reached.”