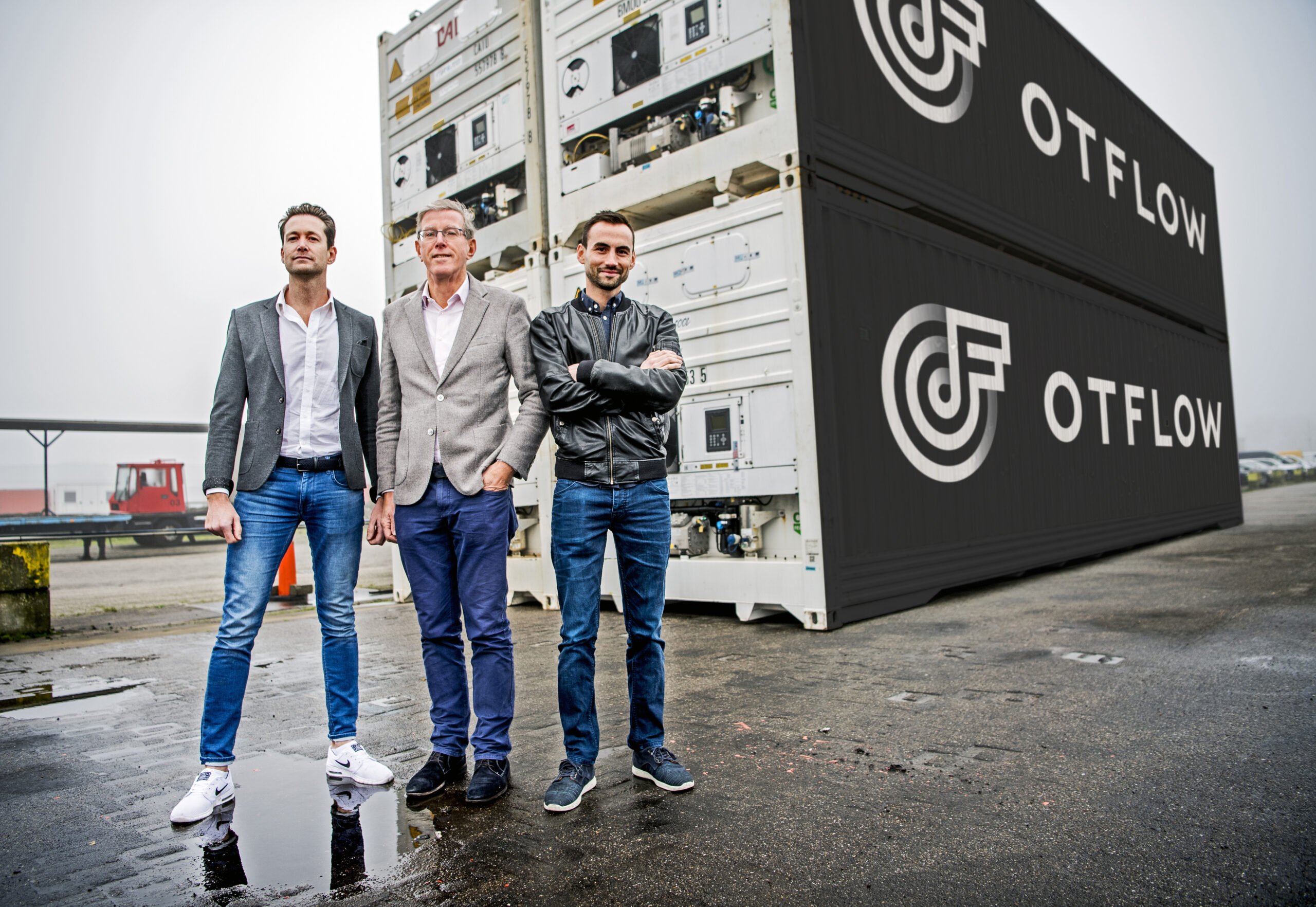
About Otflow
- Founders: Otto de Groot and Ronald Hagenman
- Founded in: 2016
- Employees: 9
- Money raised: no external capital
- Ultimate goal: Contribute to a better world by cutting down on food waste on a global scale in a sustainable and environmentally friendly way.
The Danish company Maersk, the largest shipping container company in the world, was faced with a problem: after transport by sea – which can take up to three weeks – all too often, fruit was not fresh on arrival. Maersk called in the help of Wageningen University in the Netherlands. Who then in turn approached Otto de Groot, an expert in the fruit industry. De Groot came up with a mat that improved air circulation in the container. And so, in 2016, Otflow was born. The start-up’s mission is to curb food waste. “Initially, by manufacturing these air distribution mats. But in the long run, by becoming a knowledge institute in the field of maritime transport,” says co-founder and CEO Ronald Hagenstein
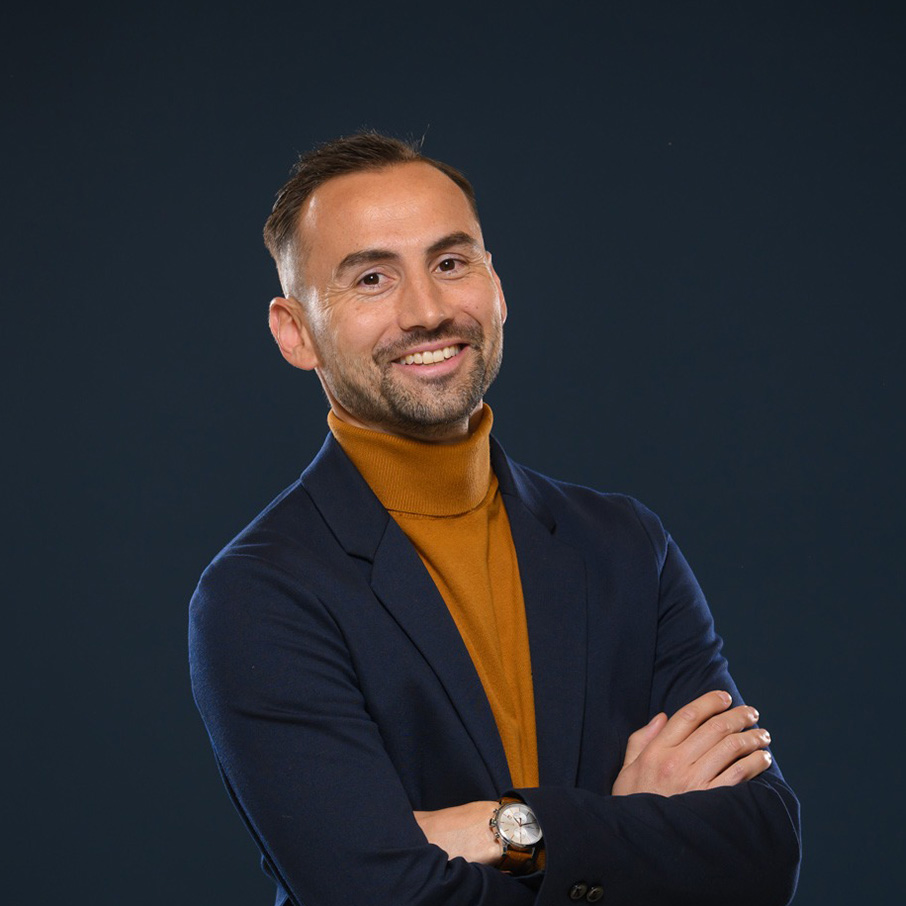
What problem does Otflow solve?
“It is very difficult for exporters to keep produce fresh for three weeks while it is being shipped from South Africa to the Netherlands, for example. The containers in which the fruit is transported are like tunnels that are twelve meters in length and three meters wide. The floor has a grid which cold air is blown through by a refrigeration unit. That air is lazy and just wants to go up. This was not a problem in the past when the boxes of fruit were placed directly on the floor. This prevented the cold air from rising, and it would reach a larger part of the container. Nowadays, the boxes of fruit are on pallets. That means the cold air is able to rise and less cold air reaches the other side of the container.”
And it’s not an option to just put the boxes of fruit back on the floor?
“No, in terms of logistics, the pallets are a must for fast loading and unloading.”
So Otflow makes mats that improve air circulation. Tell us about it!
“Our mats actually have the same effect as the boxes of fruit that were on the floor: they keep the cold air from going straight up. We cut the mats into a shape that tapers and which provides the most optimal level of air distribution. This reduces the difference between the temperatures close to the cooling unit and on the other side by up to 75 percent.”
What material are the mats made out of?
“From recycled material such as milk cartons or cardboard boxes for oranges that we source from the food industry. The mats are single-use and can be recycled again at the destination.”
Isn’t it more sustainable to manufacture mats that last a year, rather than a single time?
“No, they aren’t in the end. We supply thirty clients who in turn export to 180 countries. We have no idea where an Otflow ends up. And retrieving all those mats again is really impossible logistically speaking. Moreover, that would create a huge carbon footprint.”
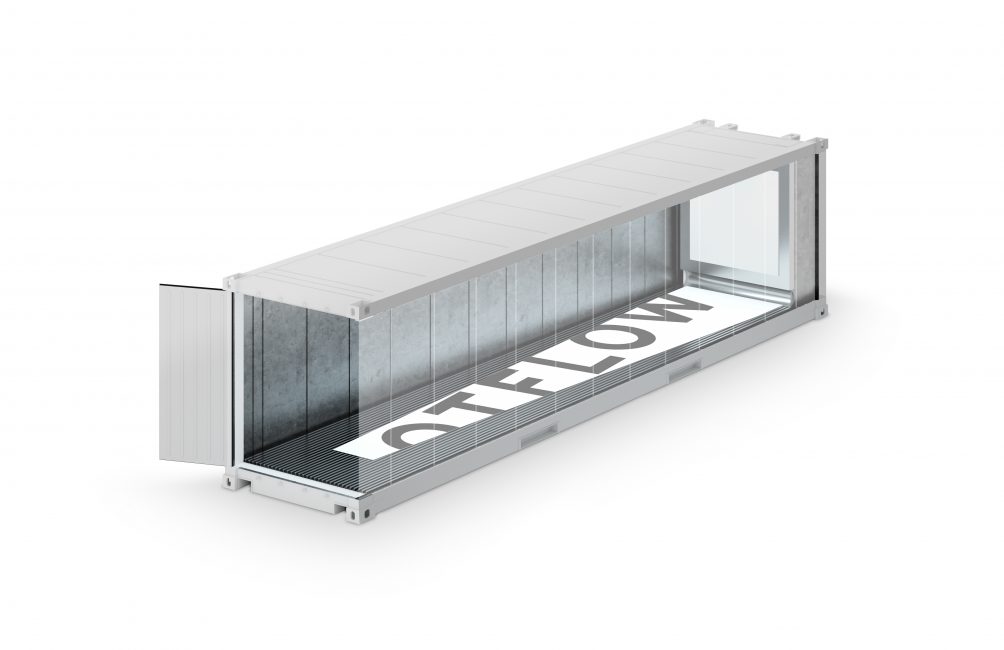
Which phase is Otflow in now?
“We have passed that prototype stage when we were cutting mats ourselves in a stable, haha. We’ve also built a manufacturing factory which has a high-tech machine that’s eight meters in length and a robotic arm that makes the mats. We entered the market in 2018 and are now at a stage where we are preparing to scale up to manufacturing 12,000 mats per year.”
Still, scaling up production is not your only ambition, right?
“True. In the future, we want to make Otflow primarily a knowledge institute in the field of maritime transport. That’s why we have been working with Sioux Technologies in Eindhoven for over a year on a 3D simulation of a refrigerated container. With everything on board: the fruit, the fruit boxes, pallets, insulation properties, air flows, air, loadability, and so on. That way, we don’t have to knock on the door of a university for every problem, and we can simulate cases from customers ourselves and advise them on the most efficient way to transport goods.”
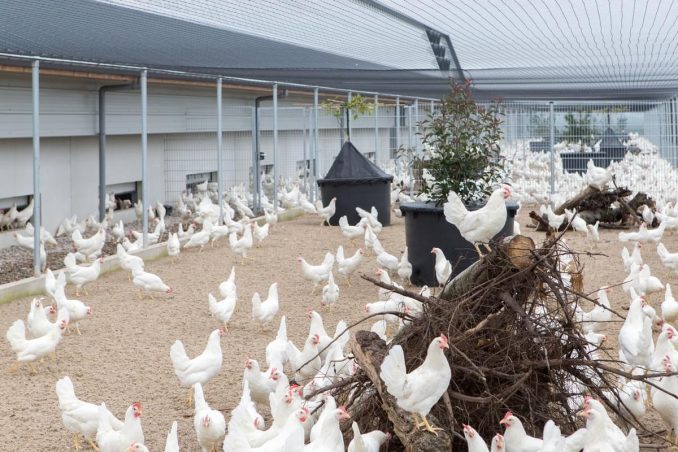