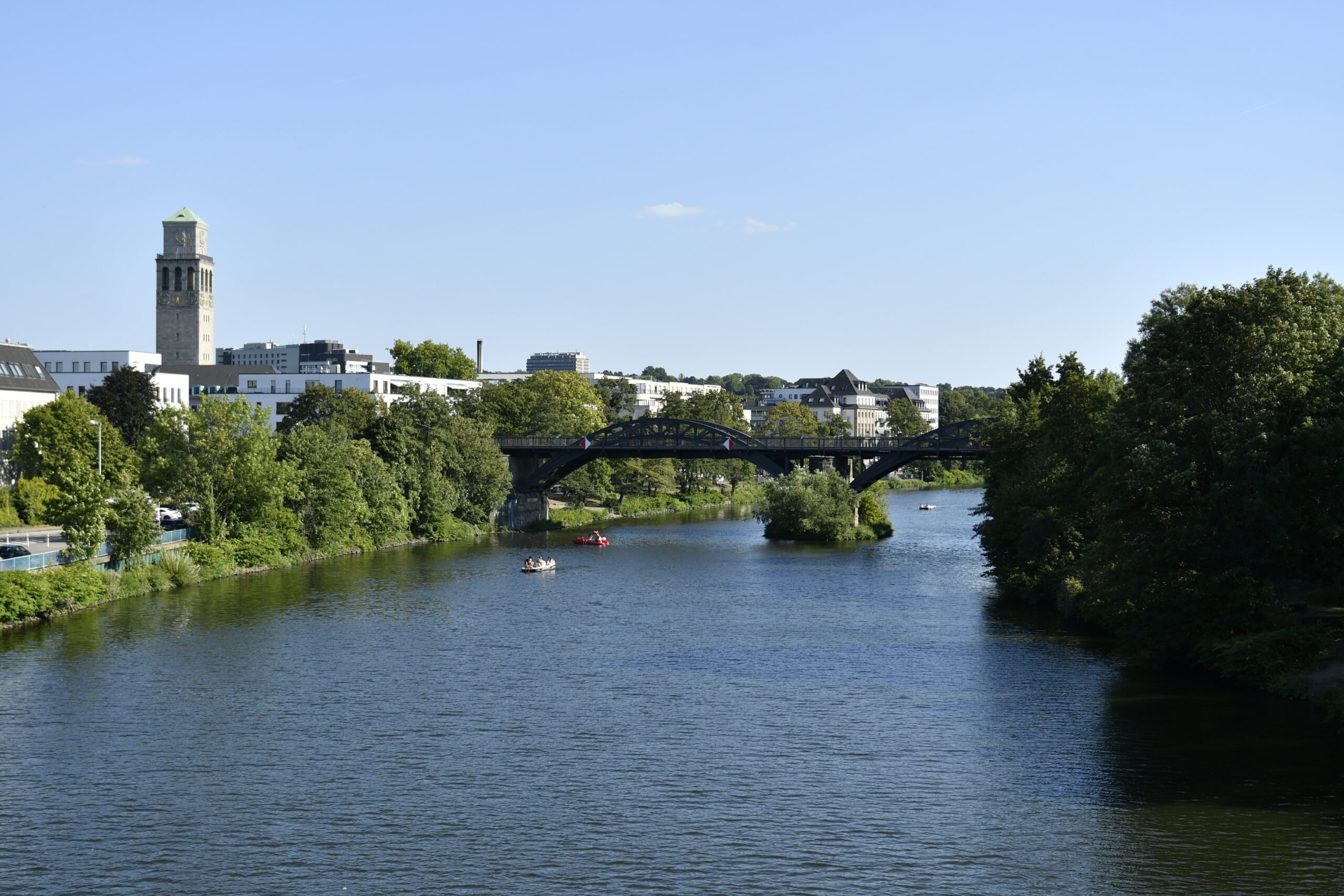
In Germany this summer, you can travel on regional public transport for 9 euros per month. Innovation Origins is seizing this opportunity to visit a number of future-proof projects. In this edition, we travel to Mülheim an der Ruhr.
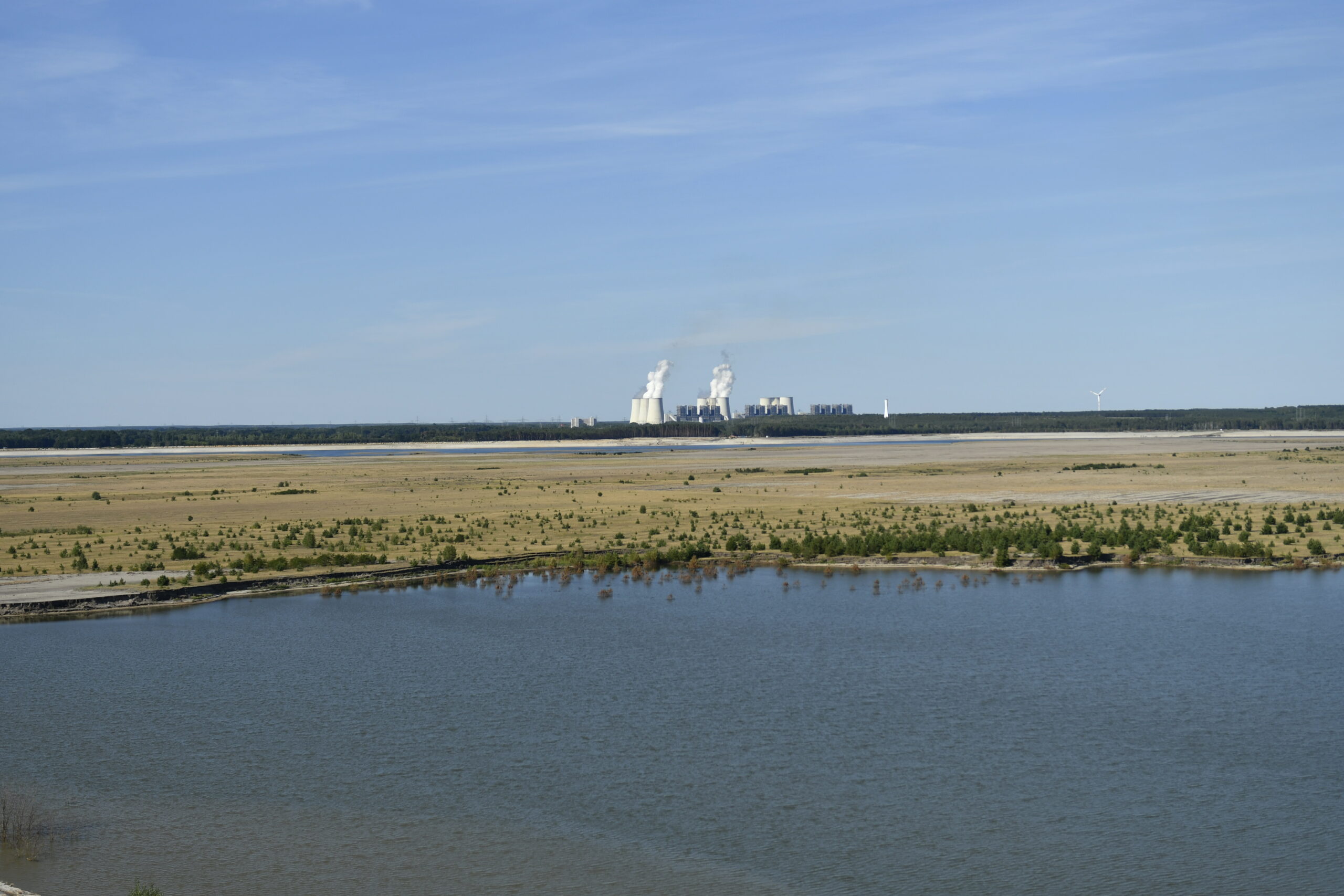
Mülheim an der Ruhr might not at first sound like a fun outing for the whole family. The city is located in the middle of the Ruhr region, which is made up of a lot of cities that have more or less grown into each other, such as Duisburg, Oberhausen, Essen, Bottrop, Bochum, Gelsenkirchen and Dortmund. They all have a long industrial heritage and have always burned a lot of fossil fuels.
When you think of the Ruhr, you tend to think of a rather dirty river with impoverished working-class neighborhoods along its banks. But you will not find much of that in Mülheim. It is actually really pleasant to stroll along the promenade, motorboats can be rented from the small harbor, people can fish and you can see plenty of paddle boarders and pedal boats out on the water.
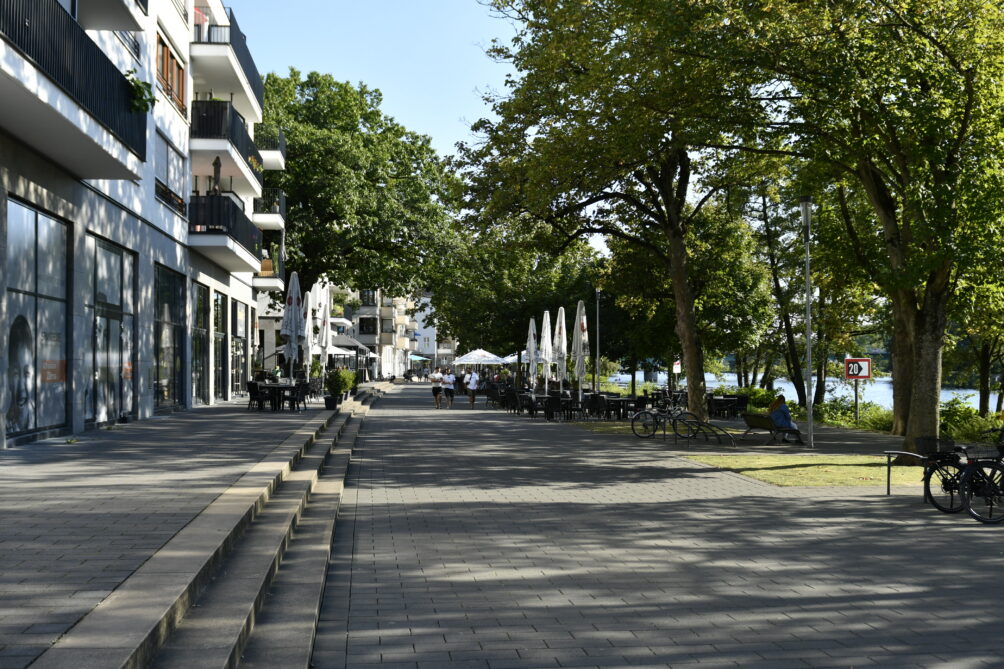
Siemens Energy
There is industry in the area, although it is relatively clean nowadays. For example, on the outskirts of the city – sandwiched between the two arms of the Ruhr – there is a large industrial park that houses, among other things, a Siemens Energy factory. Just earlier this month, Chancellor Scholz visited there to show the world that the gas turbine that is required to enable more Russian gas to flow through Nord Stream 1 is ready for use. The turbine has been in Mülheim for some time, but according to the Germans, the Russians are trying to slow down exports in order to increase fears of gas shortages.
The fact that there is comparatively low levels of pollution in Mülheim does not mean that environmental protection is not an important concern. This becomes very clear during a visit to the Max Planck Institute for Chemical Energy Conversion.
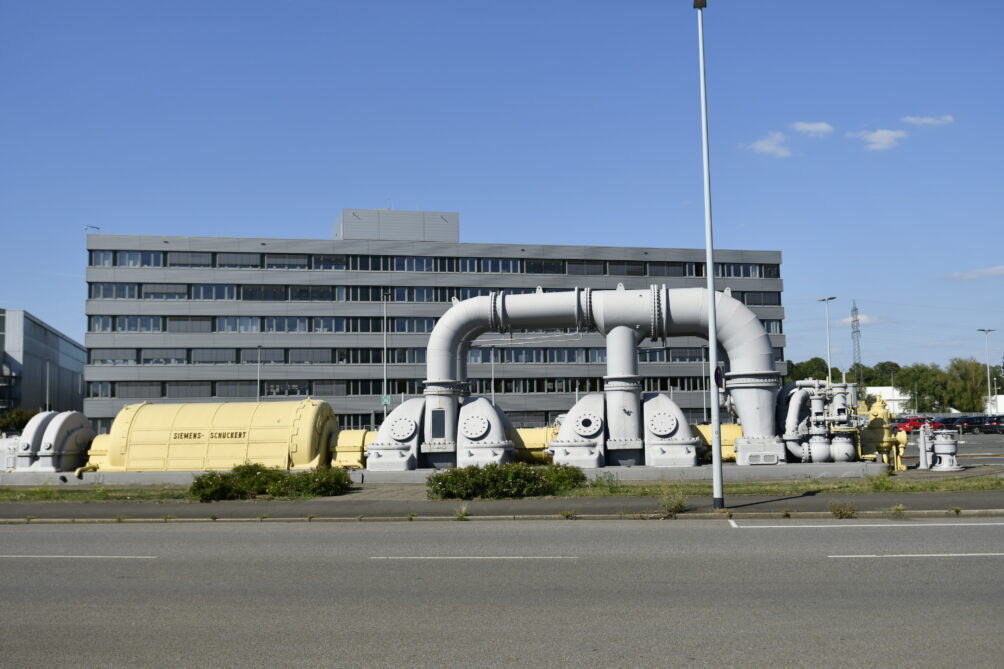
Brand new laboratories
Holger Ruland and Nikolas Kaeffer give a tour of the largely brand new complex. Ruland is head of “Catalytical Technologien” in the “Heterogeneous Reactions” department, Kaeffer is head of “Metallorganic Electrocatalysis” in the “Molecular Catalysis” department.
Some buildings are so new that the floors have yet to be laid and the equipment installed. In one of the laboratories, technicians are just installing and checking large hermetically sealed cabinets where experiments can be carried out on the gas coming out of the ceiling through the pipes.
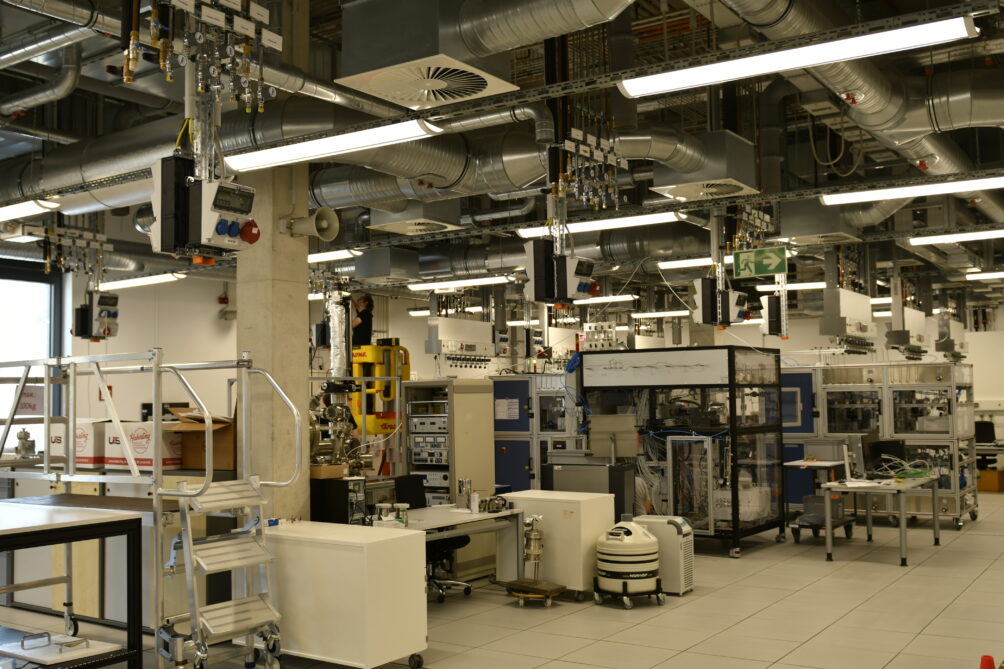
In another lab, tests are being conducted with a mixture of gases and solids. Numerous chemicals are stored along the walls for this purpose, obviously in compliance with all of the safety regulations.
A pair of rubber gloves stick out of one of the cabinets. Kaeffer explains that experiments are done there on a molecular level, whereby it is extremely important to keep the air as pure as possible. Among other things, Kaeffer is looking for ways to make chemical processes more energy-friendly.
Carbon2Chem
Among the most exciting pieces of research they are working on at this Max Planck Institute – there are more than 80 departments belonging to this research institute in Germany – is the so-called Carbon2Chem-Projekt. Many people will have heard of CCS. That stands for Carbon Capture and Storage, where carbon dioxide (CO2) emitted by, for example, steel mills, cement producers and waste incinerators is captured and stored underground. So far, not such a huge success.
At the Max Planck institute in Mülheim, they do work on CCU: Carbon Capture and Usage. The aim here is to harness CO2 to make something else out of it. More specifically, at Max Planck in Mülheim they are working on converting nitrogen and CO2 into usable products such as methanol and other fuels that can be used by aircraft, for one thing. For this, CO2 requires the carbon molecule (C) to be separated from the oxygen molecule (O2).
As a result, much less CO2 is released into the air. This greenhouse gas is recycled, in a manner of speaking. It is one of the ways to make the manufacture of steel CO2-neutral.
Ruland goes on to explain that converting CO2 is not a new concept. “What we are interested in is perfecting the process in such a way that it is economically viable.”
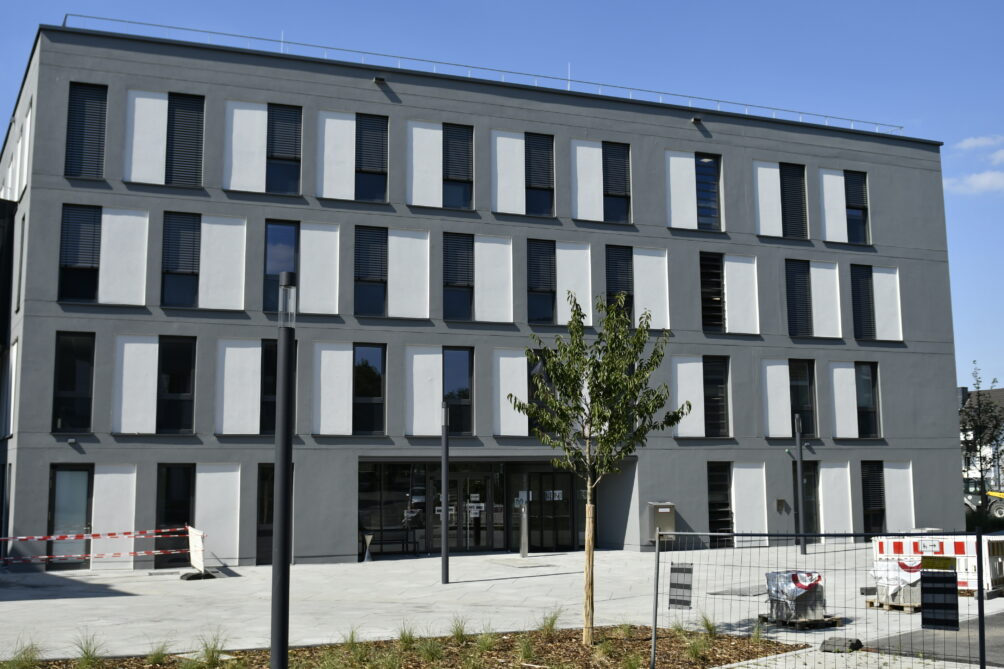
More than just CO2
The fact is that a lot of (scarce) energy is needed in the conversion process and smoke from a steel mill contains more substances than just CO2. The Max Planck Institute in Mülheim is working on solutions together with several other research institutes and industry partners, including the steel giant Thyssen Krupp.
Put very simplistically, it comes down to how Thyssen Krupp uses coal for its smelters. This produces smoke that, after being treated with a catalyser, leaves the factory via a chimney.
That smoke contains a lot of CO2 which with the help of energy can be converted into methanol (CH3OH). Other energy carriers and chemical products can then be made from methanol.
Hydrogen is in short supply
Sounds like the Egg of Columbus, although there are a few problems. Firstly, the smoke from the factory must be suitable or made so. Too much contamination with carbon monoxide is not good.
Secondly, the energy source that is used to extract the carbon must be renewable, otherwise it is of no use. The most suitable is hydrogen produced with green electricity from wind turbines or solar panels, for instance.
“Some of the research is being done in Mülheim, and a really large-scale trial is taking place at a Thyssen Krupp factory in Duisburg,” Ruland adds.
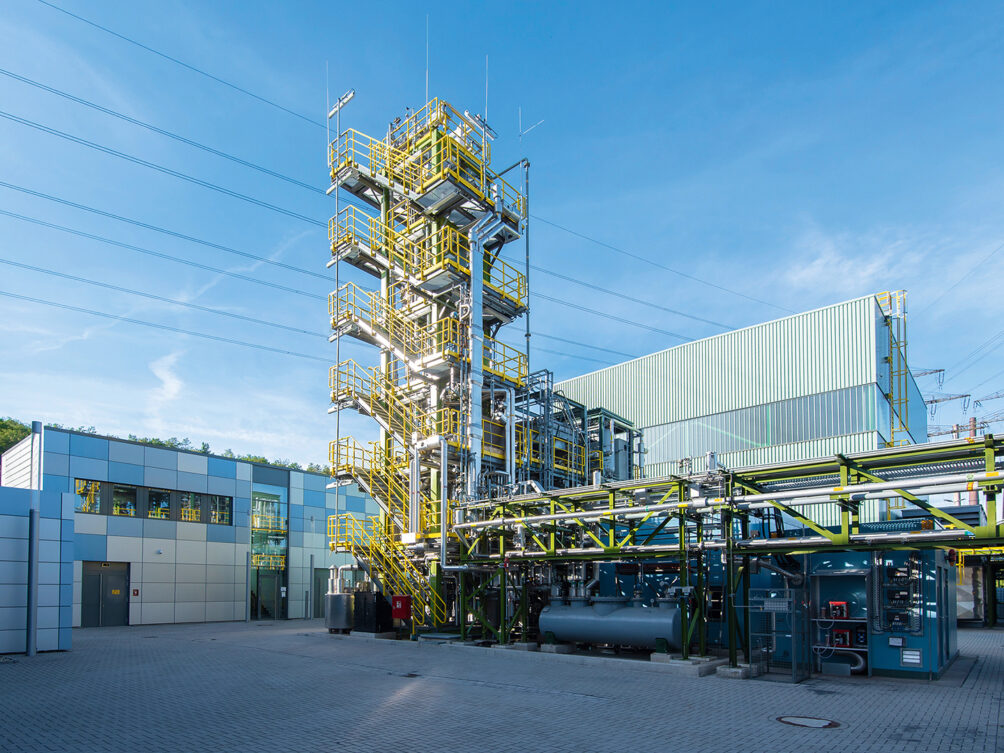
His job is primarily to analyze the gas as it comes out of the factory pipe and how it can be made suitable in the most efficient way possible for methanol conversion with a catalyser.
According to Ruland, the project is growing in terms of scale. Work is underway on a facility that can produce several thousand tonnes of methanol per year. It is being subsidized by the government to the tune of 145 million euros.
Other sources of CO2 will have to be considered in the future, according to Ruland. In addition to steel mills, other large emitters such as cement factories and waste incinerators spring immediately to mind. It is quite conceivable that CO2 will at some point become a scarce product that can be used for the production of a range of fuels and plastics.
But then there has to be a sufficient supply of green hydrogen and the production process has to become cheaper. Ruland: “What would also be a big help is if emitting CO2 becomes more expensive for companies. The more expensive CO2 emissions become, the more attractive it will become to capture CO2 and use it as a raw material for something else.”